Somewhere near Ithaca, NY.
DMLS Site Visits
Last week, I had the pleasure of visiting two excellent resources in the world of additive manufacturing. What follows is all in relation to my titanium 3D printed bike seatmast topper project.
Within Lab
On Wednesday I sat down in the Brooklyn Navy Yard with Kaveh and Siavash of Within Lab. Within's software takes solid models as input and allows the engineer to convert them to 3D lattice structures in order to reduce mass and build time - and maintain structural integrity. Their software is no joke; it's clear that for engineered mechanical products, Within Enhance is going to be key to making 3D printing a viable manufacturing method.
There were a few key takeaways:
- The base portion of my topper is a thin walled sleeve. I suspect it could be latticed (instead of having a consistent wall), but I don't believe Within's software will generate curved lattice segments. The demos they ran all assumed a thin skin on the ID of the cylinder, but I suspect there's a better way - which would likely require a curved lattice.
- It's possible that many of the theoretical benefits of Within's process will be somewhat tempered by the nature of my relationship (as a designer) with the job shops that will eventually produce the parts. Optimally, the job shop has an intimate understanding of the design intent of the part - both its function *and* the assumed build characteristics. In other words, I would hate to optimize my part for a vertical build orientation, and then find later that my supplier was building horizontally. Big things like that should be easy to avoid, but it'll require a bunch of management and communication on my part.
- I'm unsure whether Within Enhance will be able to find an elegant design for the pinch bolt on the front of the Topper. I'd prefer to eliminate the bolt altogether, but I'm trying to redesign as little of the wheel as possible here. This isn't a criticism of the software itself - just an anomaly of my particular design (and the design of bike parts in general).
- Within's software deals entirely with STLs, which are limited in their portability. I don't think this will be a serious issue, but I was a bit surprised about it.
It's also worth noting that I really need to redesign the saddle clamp if I'm going to take full advantage of the manufacturing process. Again, though, I'll probably hold off for now and just focus on getting one of these made - and on a bike - ASAP.
Incodema
On Thursday, I got a facility tour of Incodema (warning: autoplaying audio on their site!), a job shop in Ithaca NY with DMLS, CNC, stamping, wire EDM, and welding capabilities. I also got a chance to talk in depth with Scott about their DMLS capabilities and the idiosyncrasies of my project.
A few interesting things that I learned here:
- Incodema uses wire EDM extensively for post processing. I had just assumed that part cleanup was either manual or machining, but EDM makes a lot more sense for lots of parts. Incodema keeps a bank of EDM machines, as uses them both for DMLS cleanup and for toolmaking for their stamping shop.
- Incodema is developing a proprietary surface finishing treatment for DMLS parts. I'm aware that this is a hot topic (another supplier bragged of their ultra secretive process), and grumblings continue in the traditional manufacturing world re: DMLS's low (Ra ~400) surface finish. It's unclear where Incodema is with their process, but the first articles I saw were quite pretty.
- After hearing Within's off-the-cuff recommendations about build orientation, Scott and I spent a little while setting up a build platform and support structures for my part. It appears that we could build 20 parts per build with the part oriented roughly upside-down, and we were able to reduce support structures a bit too. We did, however, increase build height significantly, and it's unclear what effect that'll have on the per-part price. (I should have more info on this soon.)
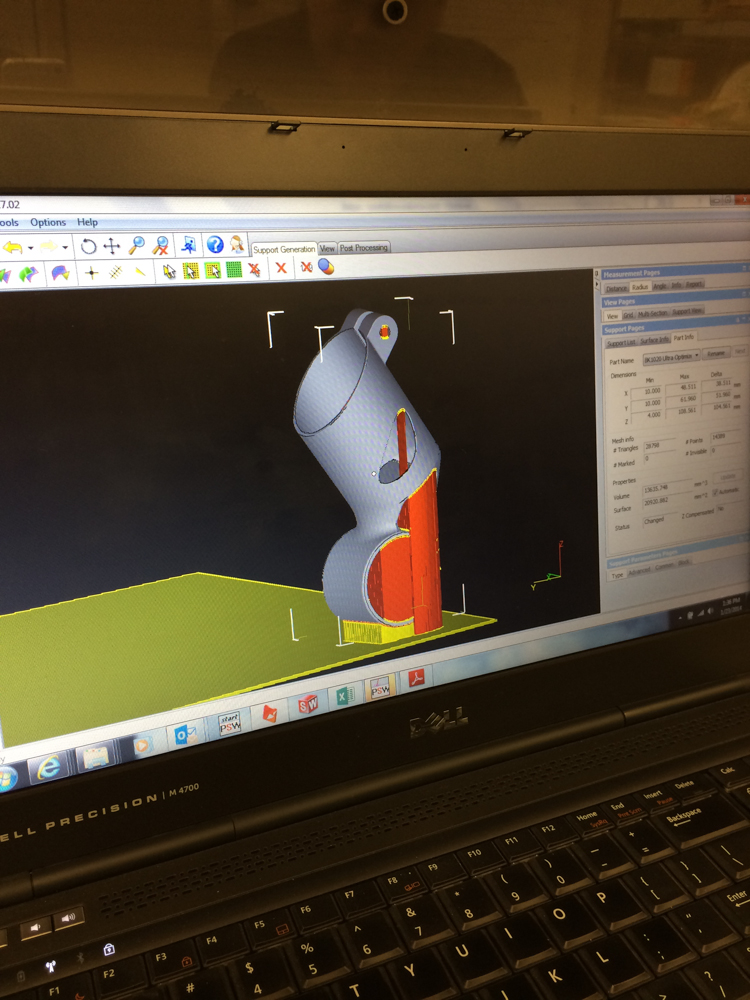
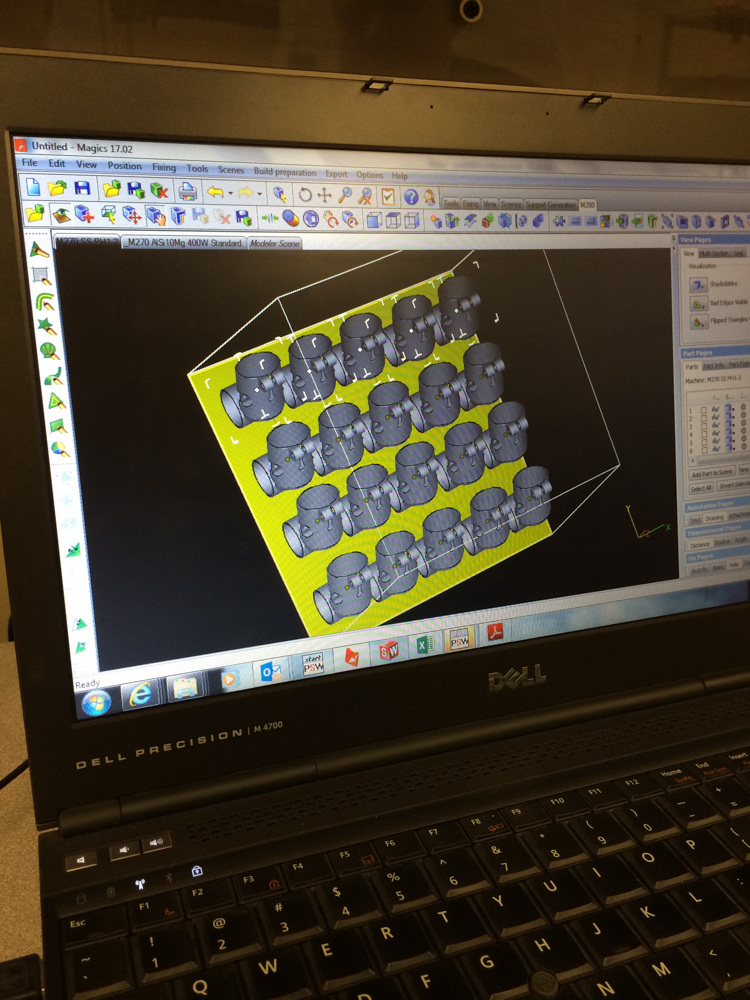
I also got a chance to see a bunch of other DMLS parts in their shop. Most were NDA and couldn't be photographed, but this demo knife blade was pretty cool :)
It's a little hard to see, but almost everything on the top left side of this image is support structures (the part is built with the blade edge up), which can be snapped off manually. Support structures on parts like this are built with perforations in a couple different dimensions, including along the part edge, so removal isn't too hard. The resulting blank still needs to be post processed pretty heavily, though - this knife will require polishing, probably some tapping, and the blade will need to be sharpened as well. My part had an estimated 1 hour of post processing, which seems really reasonable to me.
Next Up
I need to spend some time reconfiguring my design. It's likely that I strip away a few more features, and possibly redesign the bolt boss as well. I then need to think a bit on how I can prep for support structures, and whether I can remove areas of the part (especially around the saddle clamp tube) in order to reduce build time and mass. It's possible that I'll reduce the offset of the topper as well, as it both increases mass and also requires a lot more support in order to build the part.
I'll be putting a bit more time into this project over the coming week; expect updates.
My Realster
In 2010 I built a short production run of singlespeed bikes, dubbed The Realster. They were intended to be a practical take on the urban fixed gear. From the original product copy:
I believe in minimizing the degree to which my customers need to reorganize their lives in order to ride their bikes. On this project - a short production run of five framesets - I wanted to design a fixed gear bike that would be easy to use on a daily basis. The bike needed fenders, a rack, a comfortable riding position and a bell. It also needed good brakes, generous tire clearance and a reasonable pricetag. It should reward, not punish, you for riding it.
Enter the Realster. It's an upright, practical fixed gear for urban use. The stock version, shown below, sports swept-back handlebars, natural contact points (cork grips and a leather saddle) and a custom made porteur rack with salvaged cross-sawn hard maple slats.
I was in my old shop the other day and snapped a few quick photos of the stock Realster, which I kept for myself. The build is really casual, which is rare for me - but I really like it. I'm particularly fond of its rack, which was an early project that used my rack ends.
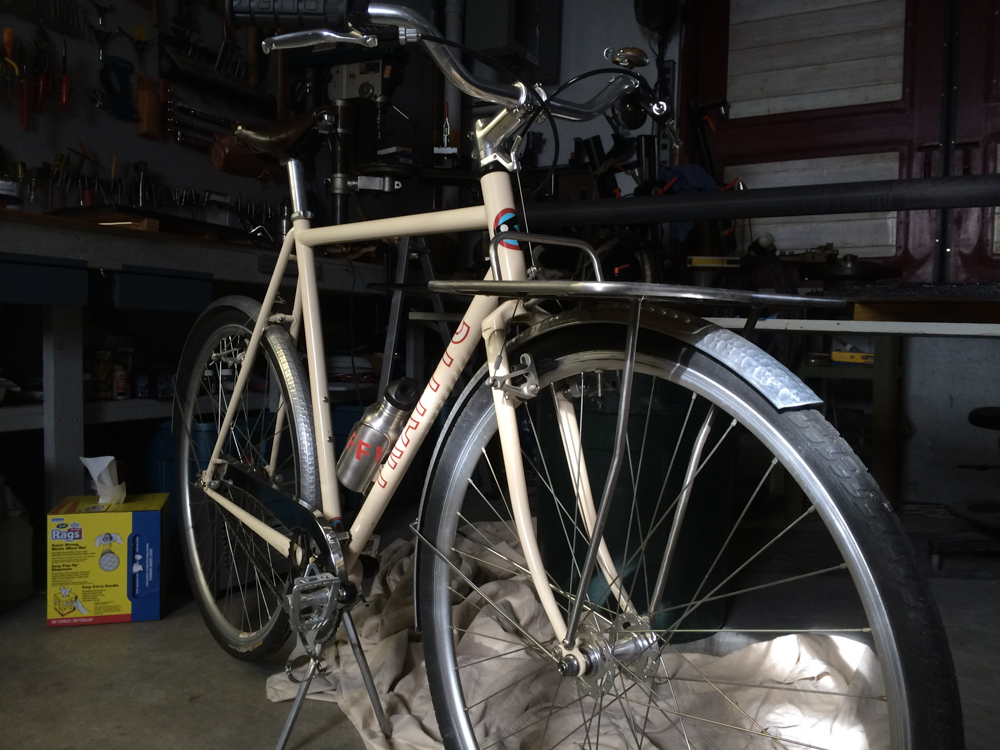
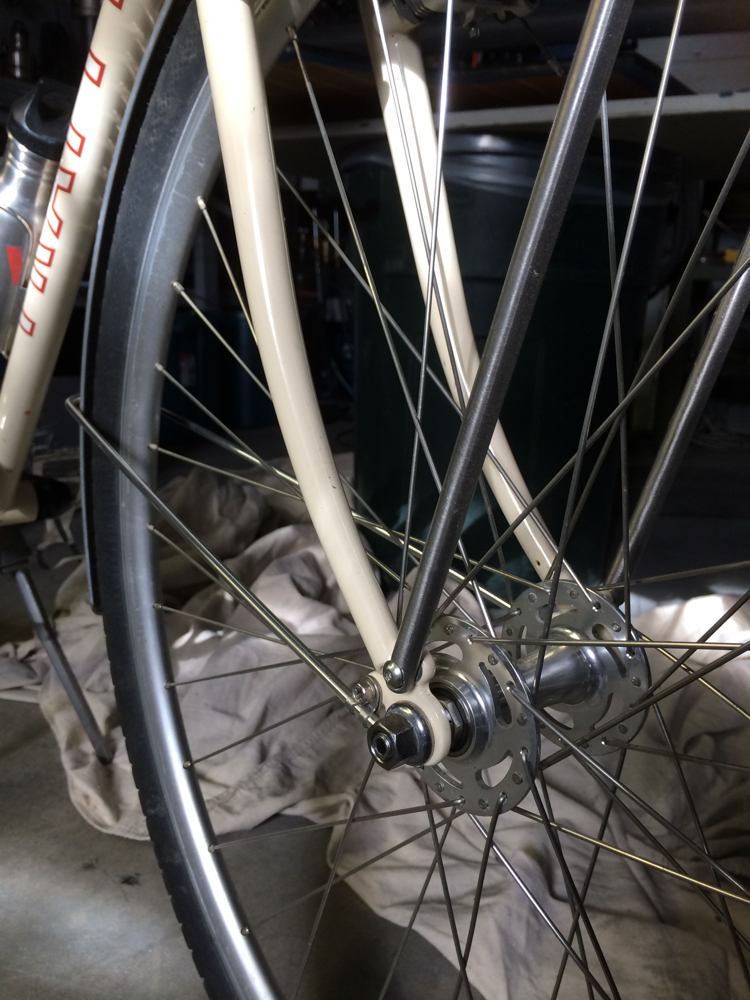
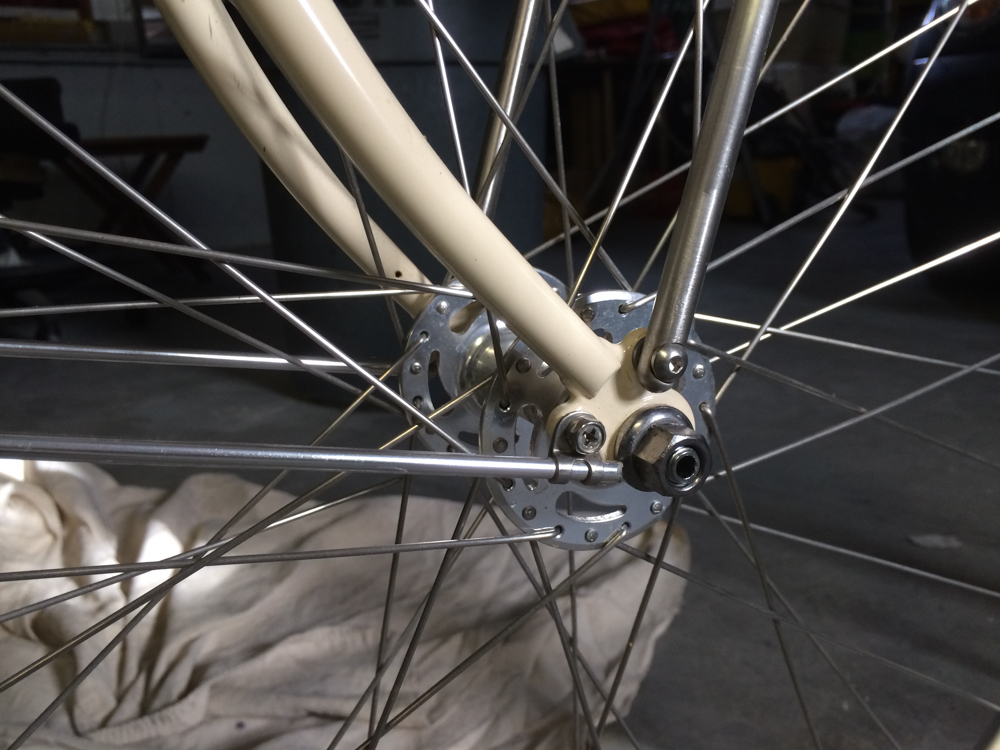
There's one of these framesets that never got built up; I recently put it on Etsy.
Stainless steel bike
This is from a while ago - late summer 2010. At the time, it was one of my proudest pieces of physical output, but somehow I never got around to properly sharing it on the internet. I never photographed it properly either, so these iPhone shots will have to do for now :/
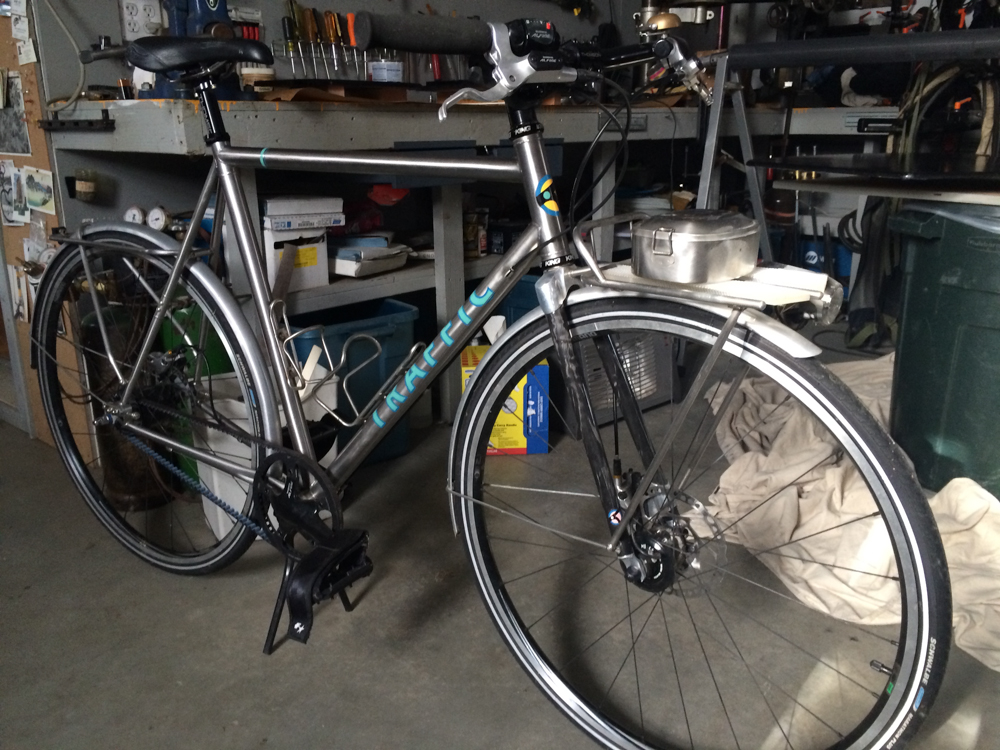
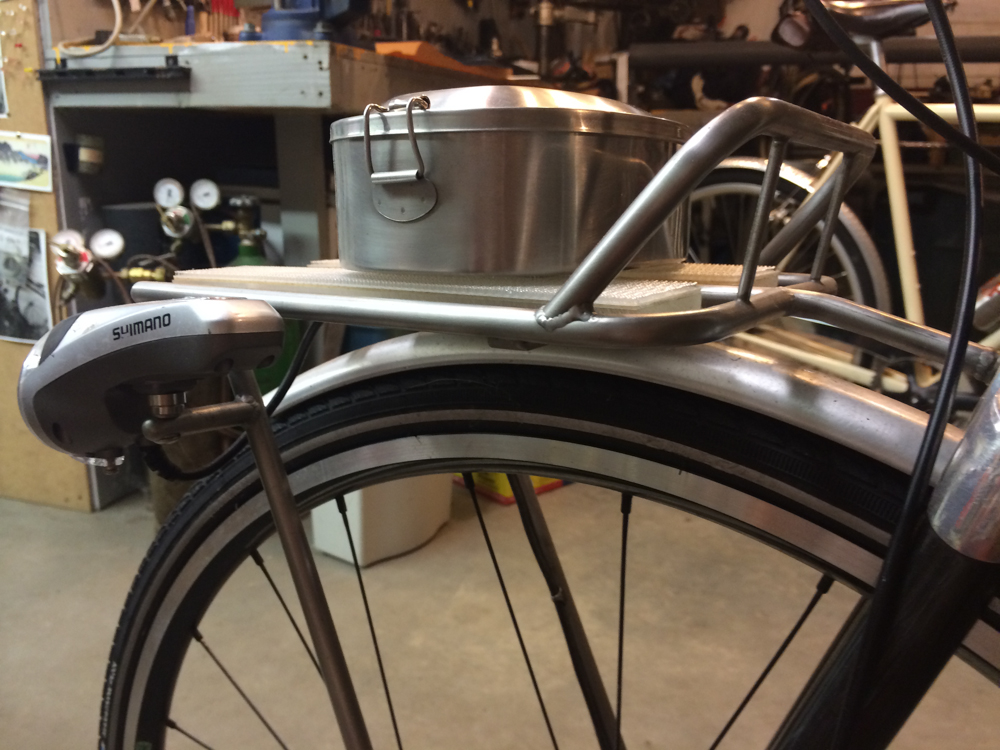
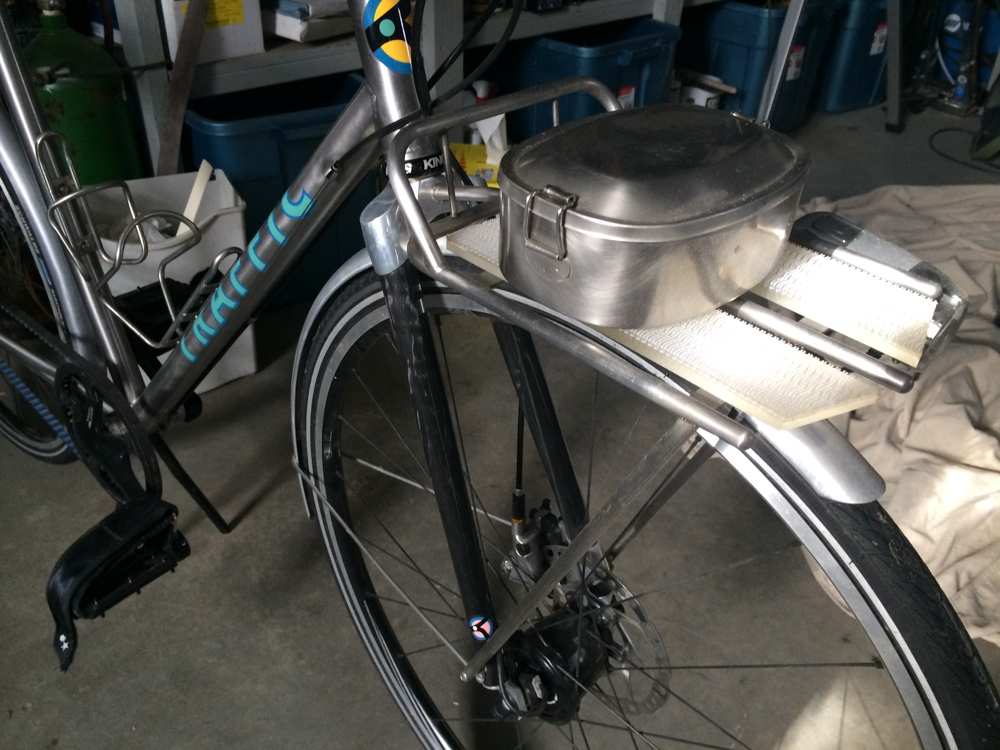
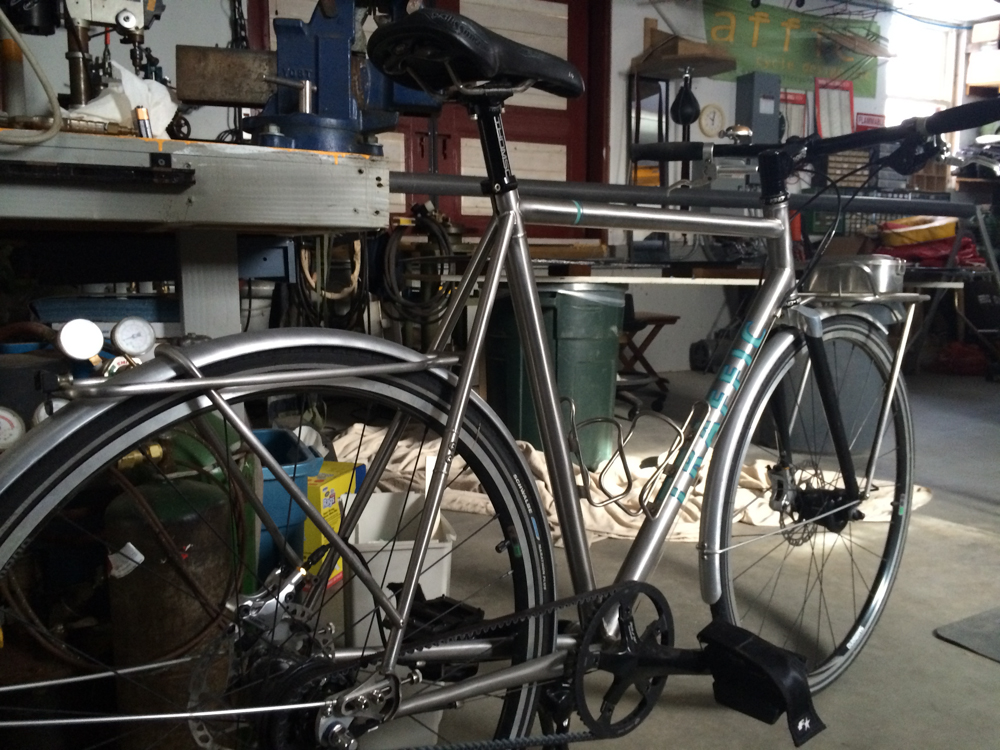
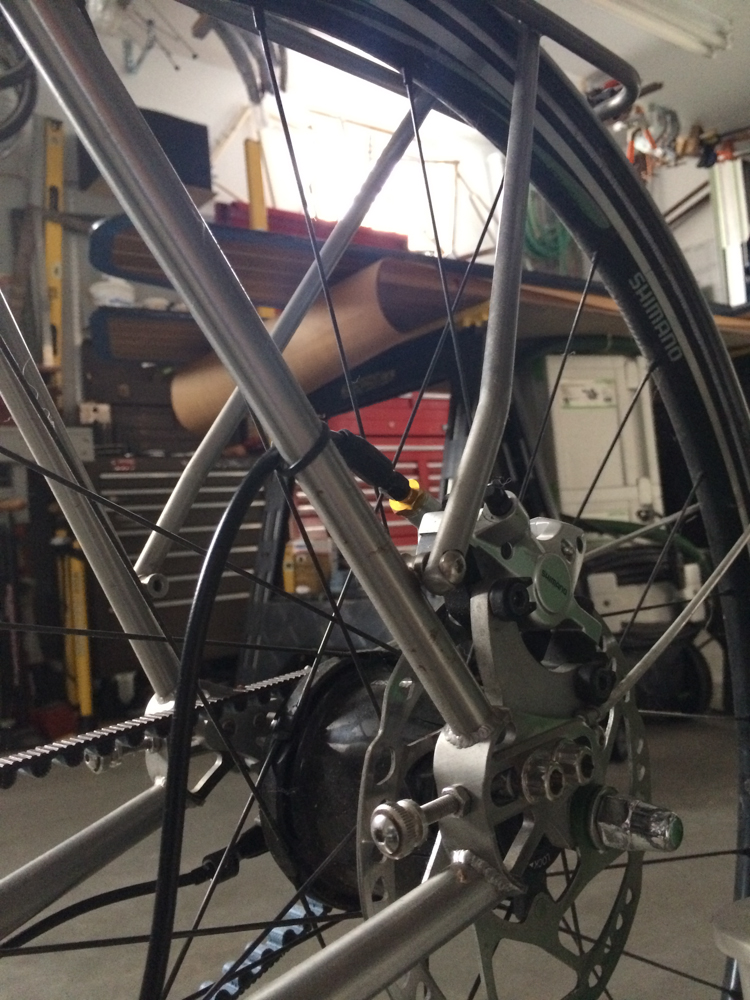
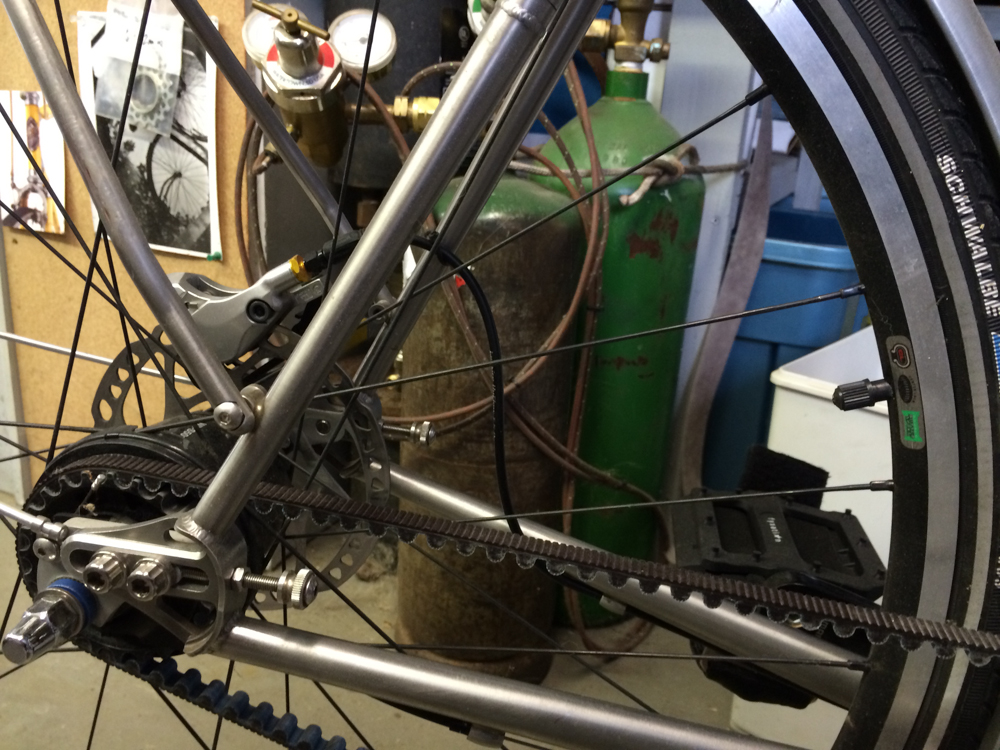
I love the belt drive, but am now quite a bit less enamored of the Alfine setup. The frame is pretty awesome, though (it's all Reynolds 953 mar-aging stainless steel), and I'm *really* proud of the racks.
This bike was the real impetus for me to make my own rack ends. I also made a few other little bits on the bike, including a pretty cool seatstay bridge with hidden fasteners for the rear rack.
Incidentally, the mushroom-head velcro on the front rack is a pretty slick way to attach commonly used things to a rack surface.
Powder
An old photo, taken during a day of boots-on-the-ground research on clearcoatable decals with powder coating.
This process was a PITA but the result is pretty cool. The decals are basically baked right into the frame. The guy I had doing my powder at the time didn't understand the process fully, so I spent the better part of a day there with him, working through it.
Scheming on Hario shit
Last week, with Jace.
An early idea of mine was to replace the whole drive bolt on the Mini Slim (there's no reason it couldn't be a hexagonal drive) but ultimately that'd be costlier and would require a lot more disassembly/reassembly by the user.
If you've struggled with your Hario grinder in the past, hit me up!
Plate rack ends
As described here, my 4-A rack ends grew out of a much simpler design that I had watercut out of stainless steel plate in 2010.
As it happens, I've got about 40 of these little guys left, and I'm glad to offer them as "cherry on top" rewards for anyone who backs my Indiegogo campaign. If you're a backer, I'll offer you a 50% match on these parts. In other words: you buy 16 of my 4-A rack ends, and I'll give you 8 of these plate ends. Just shoot me an email and tell me how many 4-A ends you've pledged for, and I'll add these to your order for no additional charge. I've only got a limited quantity of these, so give me a holler soon!
These are actually pretty great rack ends, and I'm sure that plenty of builders would get good use out of them!
Seatpost collar
After doing even more research on DMLS pricing (update soon), I played around a bit today with designing a seatpost collar.
The design here is pretty straightforward. I'm using fairly standard barrel nuts and a M5 bolt (I'll steal these from a Thomson collar I have laying around), and the part profile isn't trying to be innovative either.
I'm getting this printed in alumide (a mixture of nylon and aluminum) for an aesthetic/basic form/function mockup, and will look into pricing on the part too. I suspect that it could be relieved in a bunch of places still (to reduce build time & cost) but for now I don't care too much - I just want to get a functional stainless or titanium part on a bike ASAP.
Updates when Shapeways ships, probably before Valentine's day.
This was published in the New York Times Today.
Hario Skerton Mods
NOTE: The Hario/Porlex compatible drill adapter shown below is available for sale! You can find it on Shapeways, here.
I got a Hario Skerton manual coffee grinder a few years back, but quickly grew tired of the hand cranking (+ the jumps & catches & spills I frequently had with it). So I retrofitted mine with a nut instead of a thumbscrew, and have happily been using a drill with a nutdriver to grind my coffee.
A friend has the Hario MSS-1B Mini Slim grinder, and he has it even worse: The shaft has a pentagon stud, which has a loose fit with the stamped handle and is difficult to adapt to a drill. We were talking about his situation this week, and I decided to model a pentagon driver that could be 3D printed and would allow the user to use a drill to grind their coffee easily & quickly.
I realize that this is a pretty small market - people who are okay with having a drill in their kitchen - but I'm curious whether anyone else out there would be interested in something like this. I'll be testing a prototype of the part over the next few weeks; if you're interested, give a holler!
UPDATE: This part worked! And you can buy one for yourself here.
On Location w/ The Lady's Harp
Last night I went to the opening of The Tinnitus Suites at Nothing Space and saw The Lady's Harp in all its splendor.
The experience is a bit beyond words, but I can verify that the instrument is pretty cool. Daniel manipulates the mixing boards, but the Lady's Harp really plays itself.
Photos below. Daniel says he'll be posting the recordings on Soundcloud... eventually :)
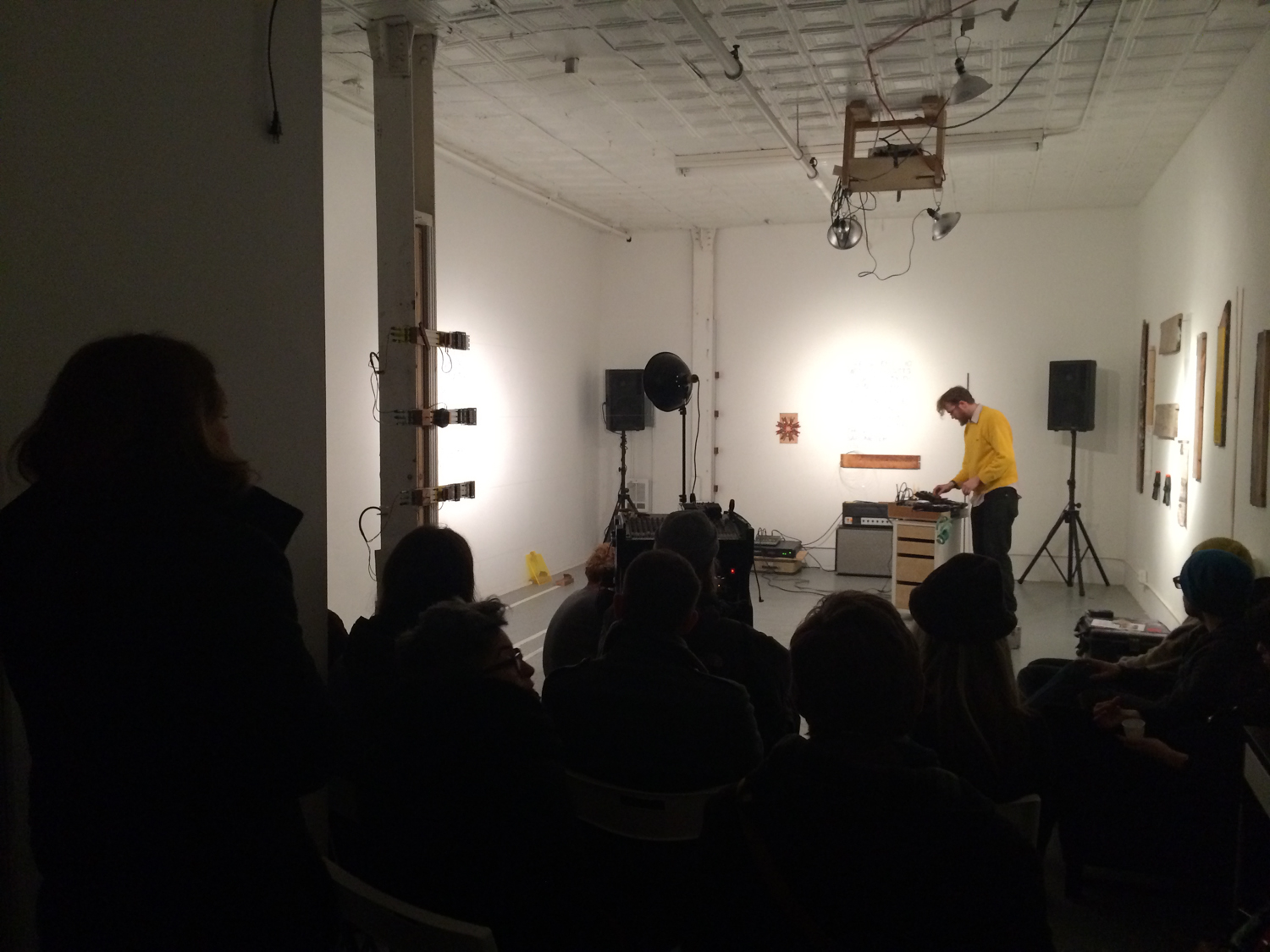
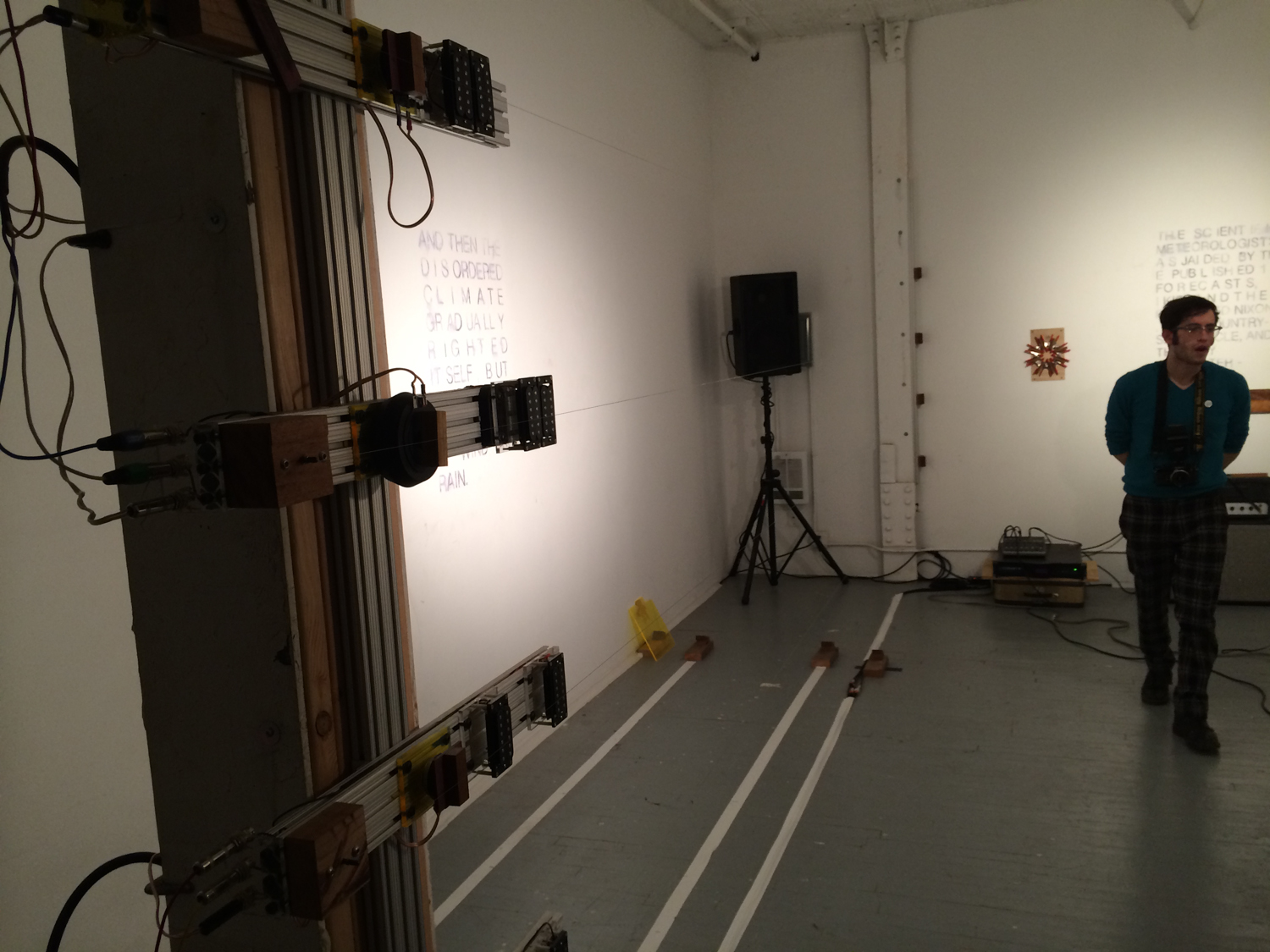
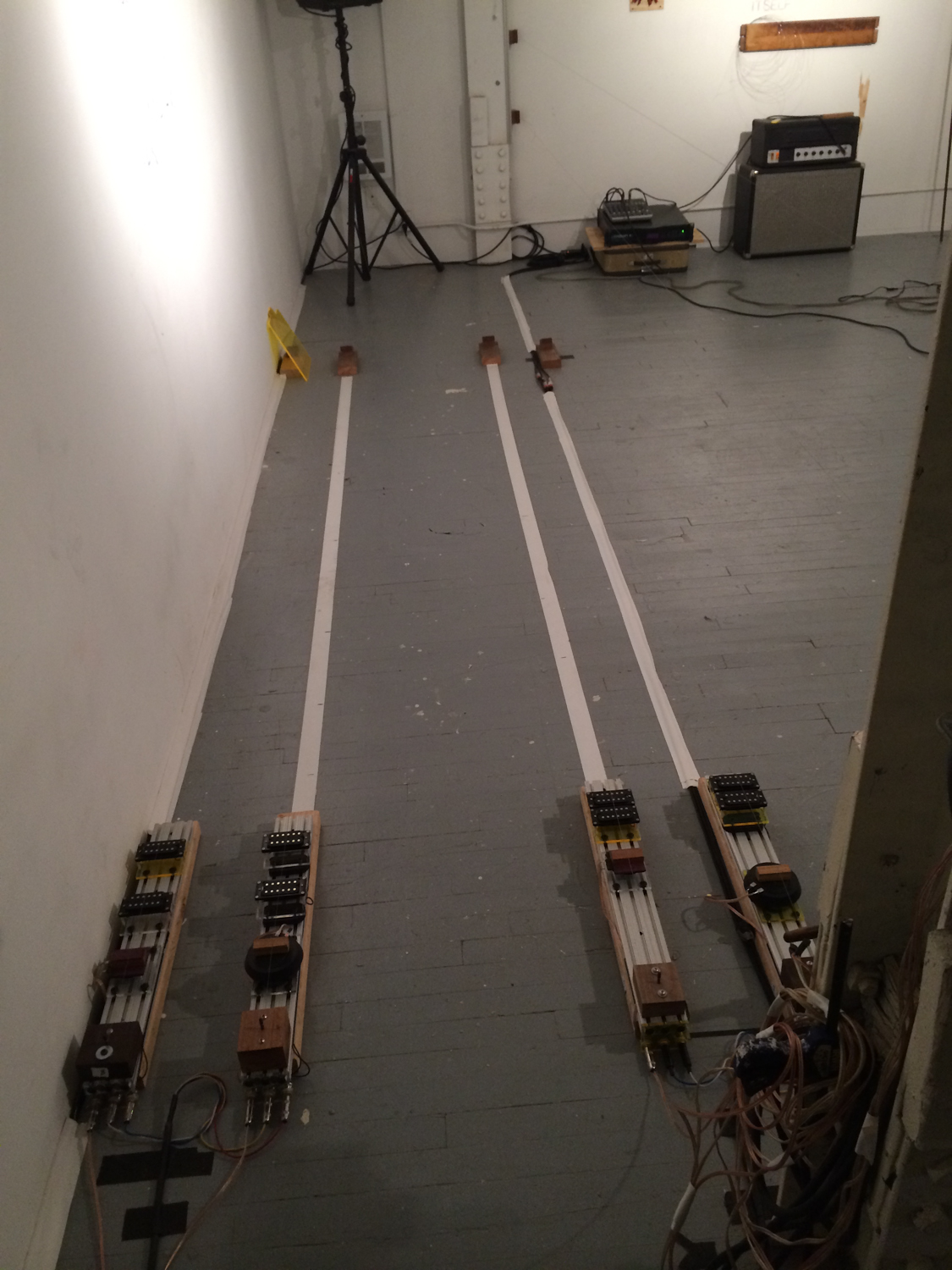
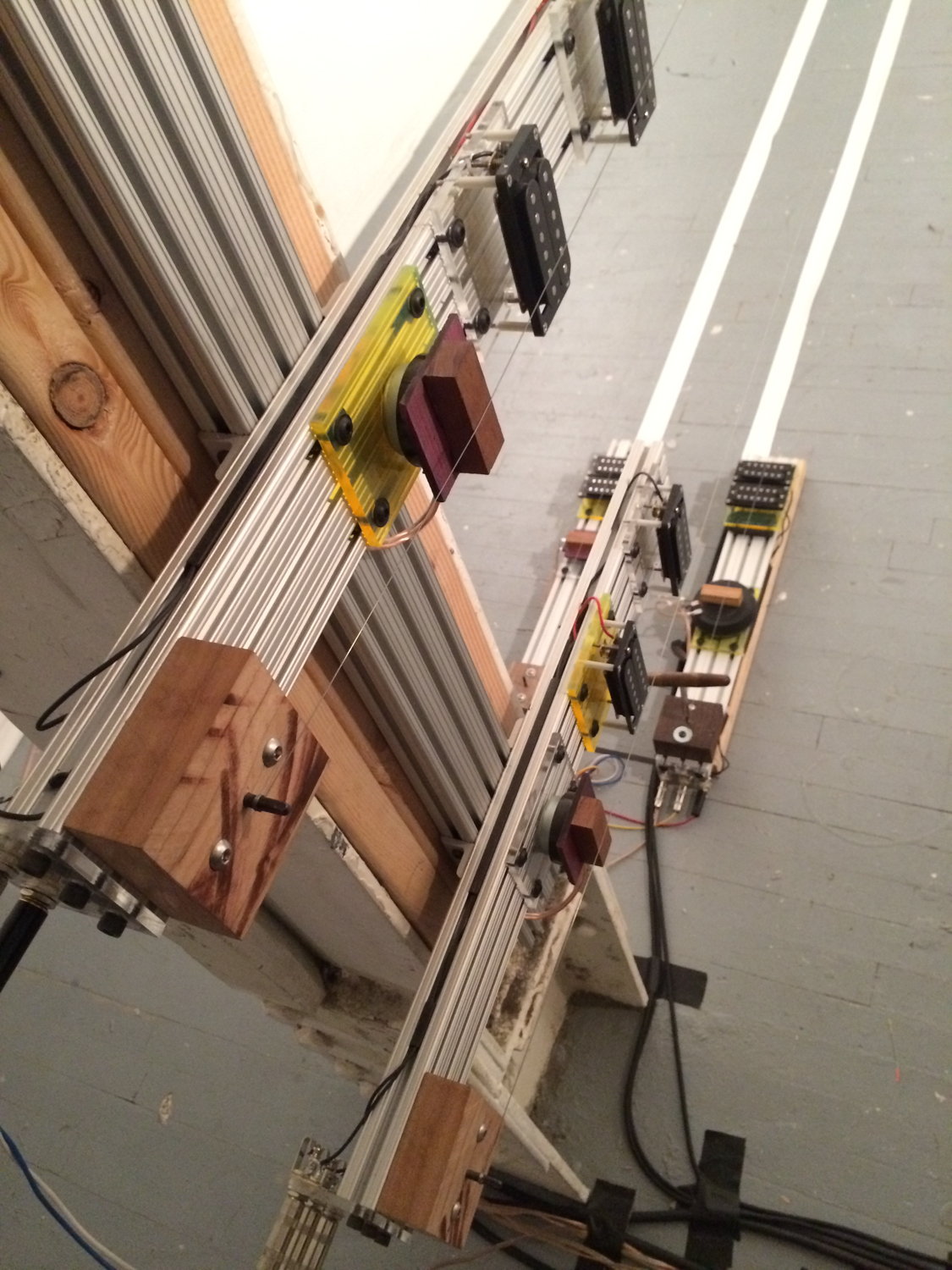
Shack
Somewhere near Ithaca, the other day.
Authorship
Shia Labeouf (!) writing in The New Inquiry about the future of creative writing:
Careers and canons won’t be established in traditional ways. I’m not so sure that we’ll still have careers in the same way we used to. Literary works might function the same way that memes do today on the Web, spreading like wildfire for a short period, often unsigned and unauthored, only to be supplanted by the next ripple. While the author won’t die, we might begin to view authorship in a more conceptual way: perhaps the best authors of the future will be ones who can write the best programs with which to manipulate, parse and distribute language-based practices.
I found this essay's discussion of the difference between literature and art/music to be really compelling.
Tinnitus Suites Tomorrow!
The Lady's Harp is fully assembled, and will be showing at Nothing Space over the next week. Come check it out!
The Public Radio on GitHub
The Public Radio is now contained on three repositories on GitHub. They're all within the same "organization," which is an improvement over the previous implementation. You can find it all here, and I encourage anyone and everyone to check it out and log issue requests/make whatever contributions they can!
The goal with The Public Radio is to maintain it as an open source project. Currently we've got embedded systems hardware data (BRD and SCH files from EagleCad), Arduino sketches, and C++ libraries all in their own repositories. I'm not certain this is the best way to organize everything, but it's a start. When I look at the physical hardware again (probably not until next week), I'll create a new repository for that and put STEP files there. I'm not sure that DXFs or STLs will make the cut, though I suppose they ought to. We'll see how the hierarchy works out.
We will, of course, sell The Public Radio as a fully assembled product, but we'll also maintain the GitHub repositories and try to support anyone who'd prefer to assemble/hack/repurpose the designs instead. We're also intending to sell a barebones kit - assembled PCB only, I think - and allow users to use their own speaker, UI, and enclosure.
GitHub isn't integrated into my workflow, and maintaining the repos will take a bit of elbow grease on my part - but I'm confident it'll be worth it.
Please check the repository out and give your feedback!
Test Protocols
From EN 14766:2005: Mountain Bicycles - Safety requirements and test methods, published by the European Committee for Standardization. Reference courtesy Marcus Schroeder (of EFBe, a bicycle testing firm in Germany) via LinkedIn.
The tests described here are roughly what my Topper would need to pass. (I've excerpted here for clarity.)
Note that 4.14.4 applies only to the saddle itself, so the current design wouldn't need to go through that step... but I've got schemes which might change that.
4.14.4 Saddle/seat pillar - security test
4.14.4.1.2 Test Method
With the saddle and seat-pillar correctly assembled to the bicycle frame, and the clamps tightened to the torque recommended by the bicycle manufacturer, apply a force of 650N vertically downwards at a point 25mm from either the front or the rear of the saddle, whichever produces the greater torque on the saddle-clamp. Remove this force and apply a lateral force of 250N horizontally at a point 25mm from either the front or rear of the saddle, whichever produces the greater torque on the clamp (see Figure 48).
4.14.5 Saddle - static strength test
4.14.5.2 Test method
With the saddle clamped to a suitable fixture representation of a seat-pillar and the clamps tightened to the torque recommended by the bicycle manufacturer, apply forces of 400N in turn under the rear and nose of the saddle cover, as shown in Figure 49, ensuring that the force is not applied to any part of the chassis of the saddle.
4.14.6 Saddle and seat-pillar clamp - fatigue test
4.14.6.3 Test method
Insert the seat-pillar to its minimum insertion depth in a rigid mount representative of that on the bicycle and with its axis at 73* to the horizontal. Mount the saddle on the seat-pillar, adjust the saddle to have its upper surface in a horizontal plane and to be at its maximum rearward position in the clamp, and tighten the clamp to the torque recommended by the bicycle manufacturer. Apply a repeated, vertically-downward force of 1000N for 200,000 cycles, in the position shown in Figure 50 by means of a suitable pad to prevent localised damage of the saddle cover.
The test frequency shall not exceed 4Hz.
My current feelings on topper
What follows is cross-posted from a discussion on linkedin re: my DMLS seatmast topper. Some of this is specific to a comment I received there, which basically boiled down to "the pricing structure and logistical/engineering benefits of DMLS are poorly suited for bike parts generally, and seatmast toppers specifically."
I've done a bit of pricing research and the numbers aren't totally crazy. Sure, the current cost is 2-3x what I'd want it to be, but between redesigning the part, and buying by the build platform (6-10 parts per order), and improvements in the technology (especially multi-laser machines), I'm actually not too far from other ultra-high-end seatposts. Consider that ax-Lightness sells their 2200 post for €467 - over $600. Even without significant drops in DMLS pricing, I can already buy my design at under $500 (at quantities of 6), with almost no overhead or fixed costs, no tooling to amortize, etc... It seems to me that there's an opportunity there somewhere, but I'm probably something else?
I completely agree that seatmast toppers aren't necessarily the best application of the technology - and moreover, my design is a pretty inefficient geometry to boot. I'm totally open to suggestions on this front - I'd love to test pricing on low mass/volume, high value consumer parts that aren't bicycle related!
That's really the key for me: To produce consumer products via DMLS. I tend to think that it's an inevitability, given improvements in the technology and a bit of intelligent planning & design. It's totally possible that I'm wrong about that, though - and like I say, it's not as if my planning & design is fully fleshed out either :)
I'd love to hear more of your thoughts, either here or via email (snwright@gmail). Thanks for the feedback!
Spencer Wright
Yes.
This is basically what I want. Still no ATTiny, but otherwise I think it's pretty rad.
If anyone out there reading this has some PCB layout critique in them, I'm all ears!
Likely Changelog
I like having multiple projects going. While I've been working on other things the past few days, I've had a chance to reflect a little on The Public Radio's current configuration. Zach has been doing other things too, but we've had a few chances to reconvene and have assembled a short, rough wishlist:
- Programmable by AVRISP. This means breaking out 6 additional pins on the Pro Mini and adding a 6-pin programming header. Doing so will allow us to remove the bootloader, shortening startup time and pushing us towards an eventual transition to ATTiny.
- Cut parts where possible. The one place this is really possible is on the screw terminals, where we can replace two 2-terminal parts with one 4-terminal part. That'll save up to $.09 per board - not exactly champagne-and-caviar money, but it's something.
The effect of just these two changes means laying out basically the whole board again. The 4-terminal screw block will screw up my whole amp & voltage regulator layout - basically the whole left side of the board. And the programming header (which I'll probably put in the bottom left) will require a few traces crossing the board up/down - likely causing trouble for some of the FM chip circuit.
Tonight I began playing with this a bit, though I didn't get far:
The other thing I'd really like to do is plop a DIP package ATTiny on here somewhere, but there'll be a pretty significant redesign associated with that too, plus a learning curve re: getting off of Arduino, and all in all I think I should just wait until v1.3.
I'm hoping to get a big chunk of this work done early next week, as it's continuing to slip a bit. Still, we're definitely getting closer to our end goal - and learning a ton in the process.
Teardown
After doing a bunch of price research on my Topper, I'm embarking on a near full-scale teardown. The reason is, as I noted earlier this week, that I'm not really taking advantage of the technology as much as I could be. My design requires a lot of support structures, and could also be a bit less massive.
As a result, I'm pursuing a different approach. Early this week I spoke to Sia Mahdavi at Within Labs, and I'm hoping that his company will be able to guide me through this next step - converting what is essentially a hollow tube-like structure into a lattice form.
My first step was to strip my model back down to a primitive shape, which I did this evening.
By removing a lot of the features I had in the model, I can give Sia and his engineers a clean starting point from which to reimagine the design. Ultimately I may end up reconfiguring the part more significantly (the saddle clamp mechanism is, in some ways, sub optimal) but for now I'm just excited to see what they come up with. Expect updates next week.