Last week, I had the pleasure of visiting two excellent resources in the world of additive manufacturing. What follows is all in relation to my titanium 3D printed bike seatmast topper project.
Within Lab
On Wednesday I sat down in the Brooklyn Navy Yard with Kaveh and Siavash of Within Lab. Within's software takes solid models as input and allows the engineer to convert them to 3D lattice structures in order to reduce mass and build time - and maintain structural integrity. Their software is no joke; it's clear that for engineered mechanical products, Within Enhance is going to be key to making 3D printing a viable manufacturing method.
There were a few key takeaways:
- The base portion of my topper is a thin walled sleeve. I suspect it could be latticed (instead of having a consistent wall), but I don't believe Within's software will generate curved lattice segments. The demos they ran all assumed a thin skin on the ID of the cylinder, but I suspect there's a better way - which would likely require a curved lattice.
- It's possible that many of the theoretical benefits of Within's process will be somewhat tempered by the nature of my relationship (as a designer) with the job shops that will eventually produce the parts. Optimally, the job shop has an intimate understanding of the design intent of the part - both its function *and* the assumed build characteristics. In other words, I would hate to optimize my part for a vertical build orientation, and then find later that my supplier was building horizontally. Big things like that should be easy to avoid, but it'll require a bunch of management and communication on my part.
- I'm unsure whether Within Enhance will be able to find an elegant design for the pinch bolt on the front of the Topper. I'd prefer to eliminate the bolt altogether, but I'm trying to redesign as little of the wheel as possible here. This isn't a criticism of the software itself - just an anomaly of my particular design (and the design of bike parts in general).
- Within's software deals entirely with STLs, which are limited in their portability. I don't think this will be a serious issue, but I was a bit surprised about it.
It's also worth noting that I really need to redesign the saddle clamp if I'm going to take full advantage of the manufacturing process. Again, though, I'll probably hold off for now and just focus on getting one of these made - and on a bike - ASAP.
Incodema
On Thursday, I got a facility tour of Incodema (warning: autoplaying audio on their site!), a job shop in Ithaca NY with DMLS, CNC, stamping, wire EDM, and welding capabilities. I also got a chance to talk in depth with Scott about their DMLS capabilities and the idiosyncrasies of my project.
A few interesting things that I learned here:
- Incodema uses wire EDM extensively for post processing. I had just assumed that part cleanup was either manual or machining, but EDM makes a lot more sense for lots of parts. Incodema keeps a bank of EDM machines, as uses them both for DMLS cleanup and for toolmaking for their stamping shop.
- Incodema is developing a proprietary surface finishing treatment for DMLS parts. I'm aware that this is a hot topic (another supplier bragged of their ultra secretive process), and grumblings continue in the traditional manufacturing world re: DMLS's low (Ra ~400) surface finish. It's unclear where Incodema is with their process, but the first articles I saw were quite pretty.
- After hearing Within's off-the-cuff recommendations about build orientation, Scott and I spent a little while setting up a build platform and support structures for my part. It appears that we could build 20 parts per build with the part oriented roughly upside-down, and we were able to reduce support structures a bit too. We did, however, increase build height significantly, and it's unclear what effect that'll have on the per-part price. (I should have more info on this soon.)
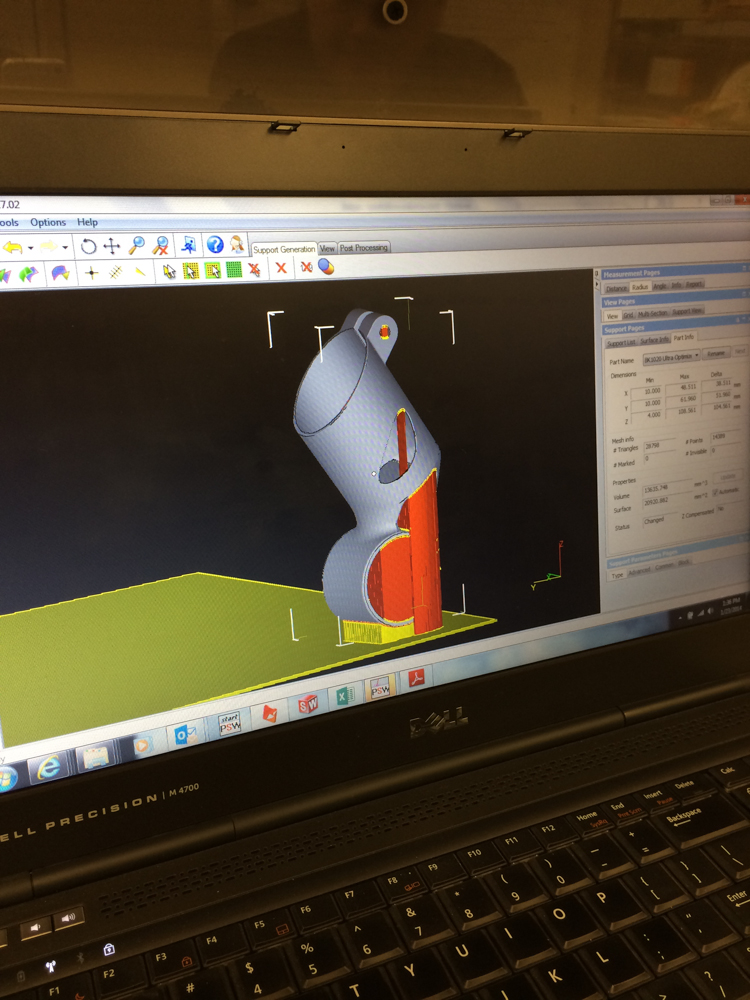
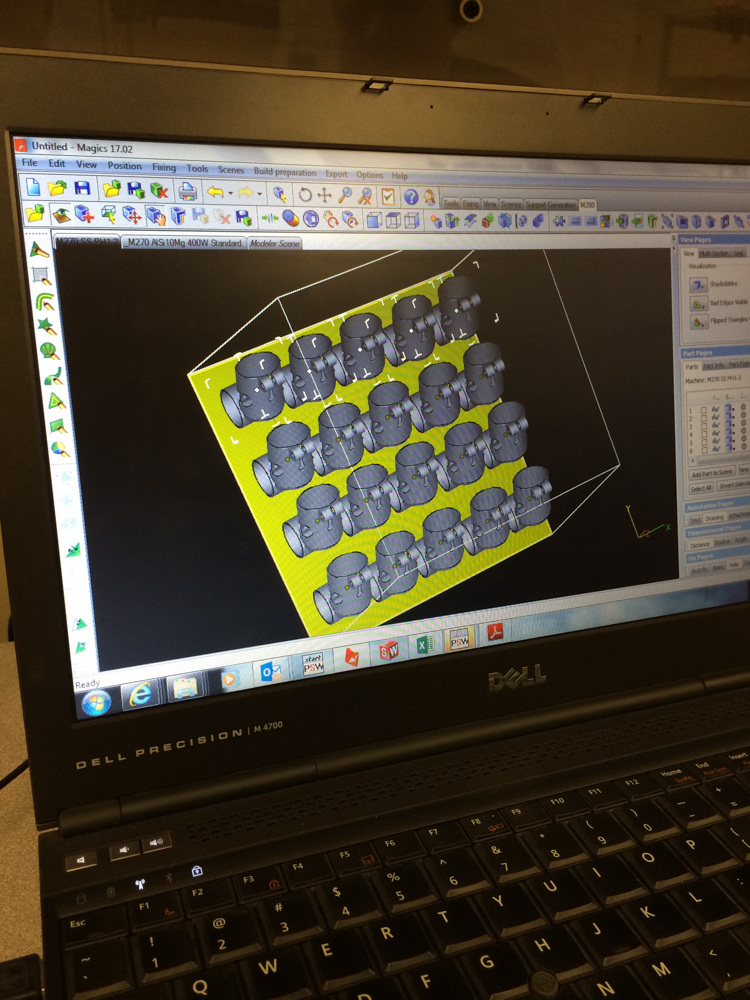
I also got a chance to see a bunch of other DMLS parts in their shop. Most were NDA and couldn't be photographed, but this demo knife blade was pretty cool :)
It's a little hard to see, but almost everything on the top left side of this image is support structures (the part is built with the blade edge up), which can be snapped off manually. Support structures on parts like this are built with perforations in a couple different dimensions, including along the part edge, so removal isn't too hard. The resulting blank still needs to be post processed pretty heavily, though - this knife will require polishing, probably some tapping, and the blade will need to be sharpened as well. My part had an estimated 1 hour of post processing, which seems really reasonable to me.
Next Up
I need to spend some time reconfiguring my design. It's likely that I strip away a few more features, and possibly redesign the bolt boss as well. I then need to think a bit on how I can prep for support structures, and whether I can remove areas of the part (especially around the saddle clamp tube) in order to reduce build time and mass. It's possible that I'll reduce the offset of the topper as well, as it both increases mass and also requires a lot more support in order to build the part.
I'll be putting a bit more time into this project over the coming week; expect updates.