In October, I visited a Taiwanese investment casting shop with Brilliant Bicycles. It was *great.*
We started in the wax casting room. Here, aluminum molds are used to cast wax positives, which basically resemble finished parts:
Then we moved to wax tree assembly. Here, wax positives are welded (with an iron) to sprues. It was a really quick process. On one side there was a guy molding the sprues themselves:
And on the other side they're welded to parts. The whole room was air conditioned and very cool (it was hot outside), to keep the wax from melting.
Once the trees were assembled, they're dipped in clay and sand. There are a number of dipping stages, and the aggregate goes from fine to coarse. First comes a liquid dip:
Then a dry aggregate, which is continuously shaken to make the process easier:
This is one of maybe three areas where dipping was happening:
Then there were a bunch of dipped tree drying racks. The dipped trees need to dry before they can move forward in the process.
Then there was a big room full of kilns, where the trees were fired and cast. Nearby were big bags of raw material - iron and alloying elements - that would be melted down to cast whatever alloy was necessary.
After the trees are baked and cast in steel, the resulting steel trees need to be cut apart:
And then the individual parts are checked in QC and cold-set into place where they've distorted:
Okay, photos:
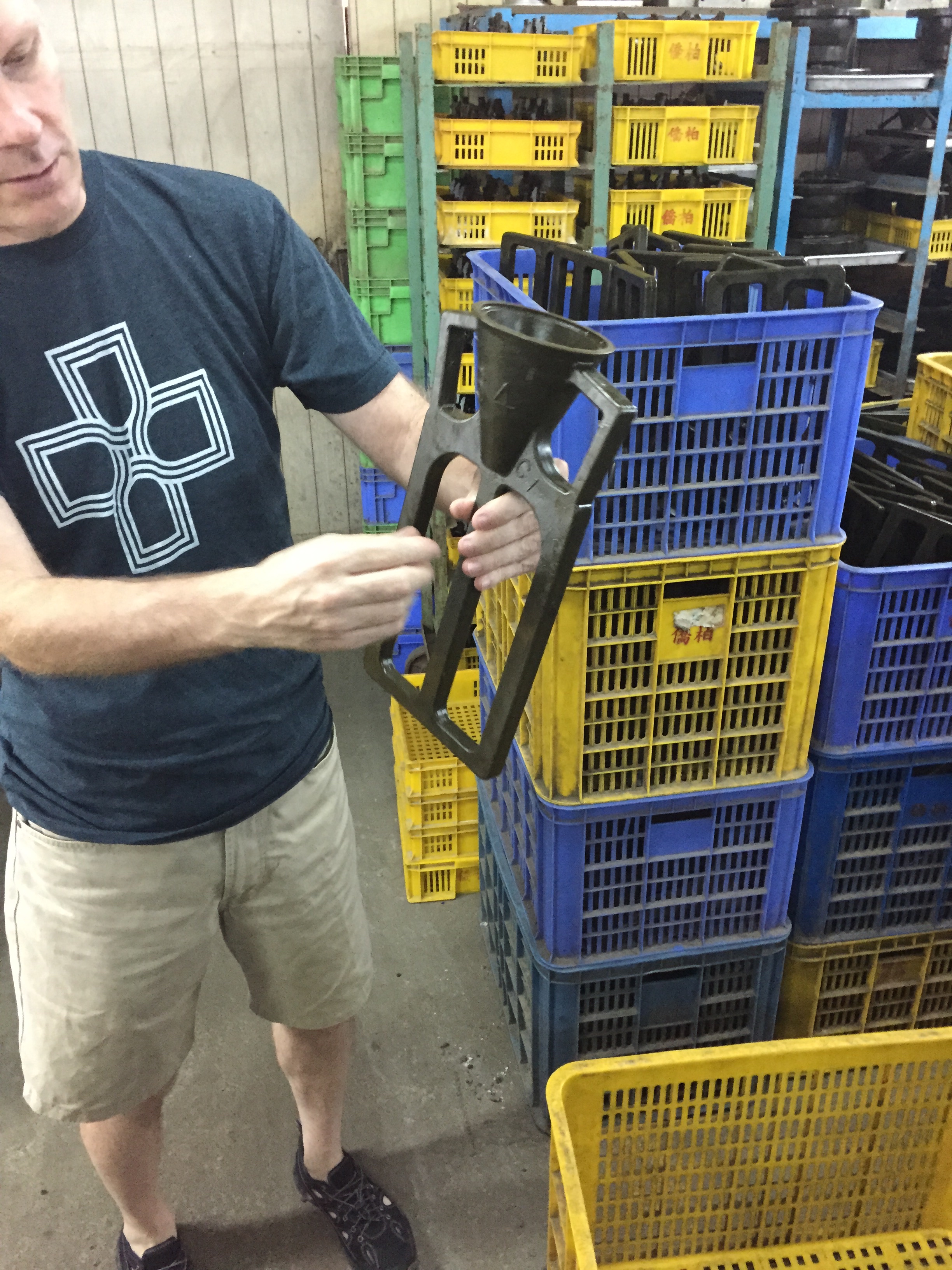
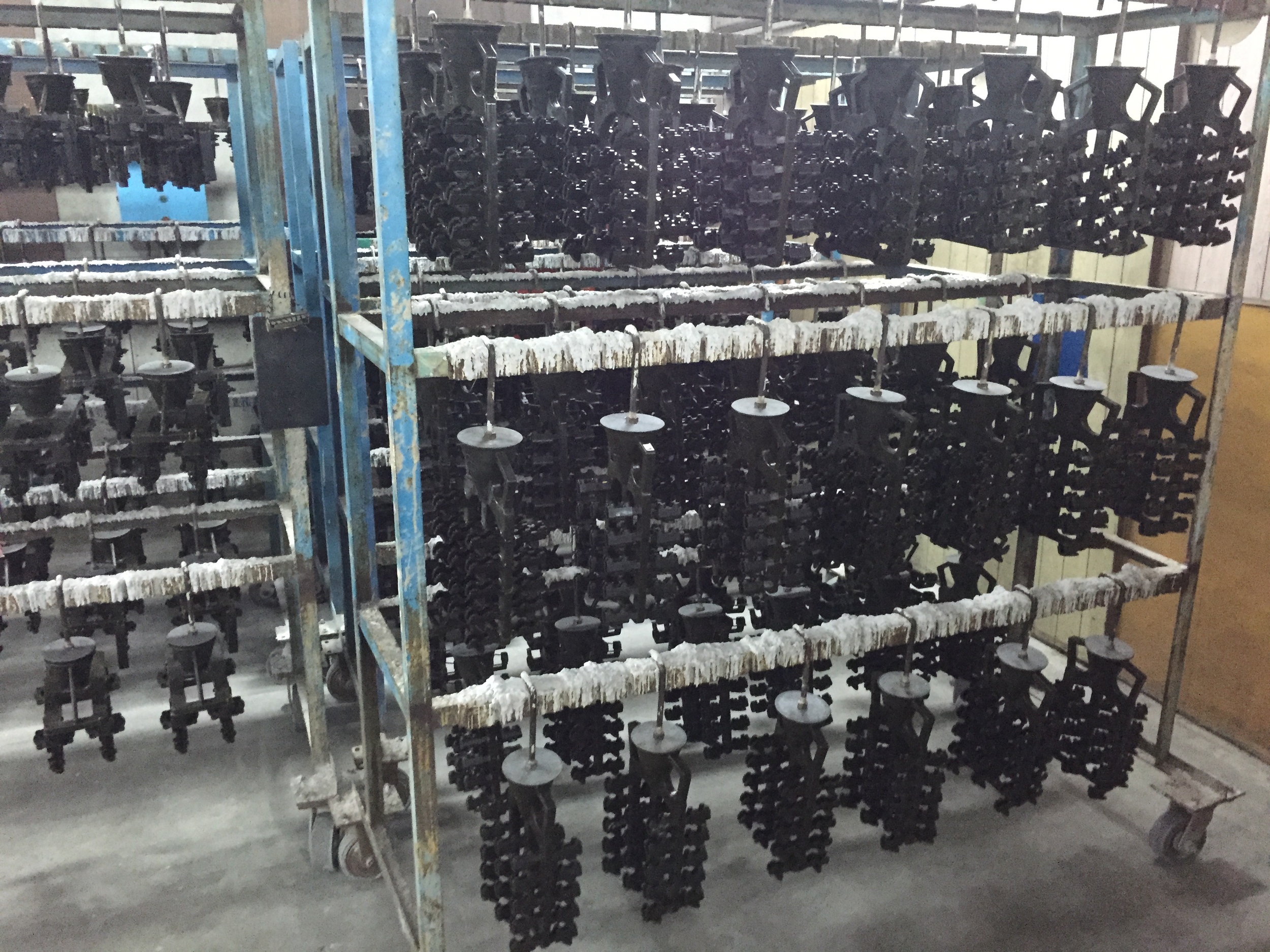
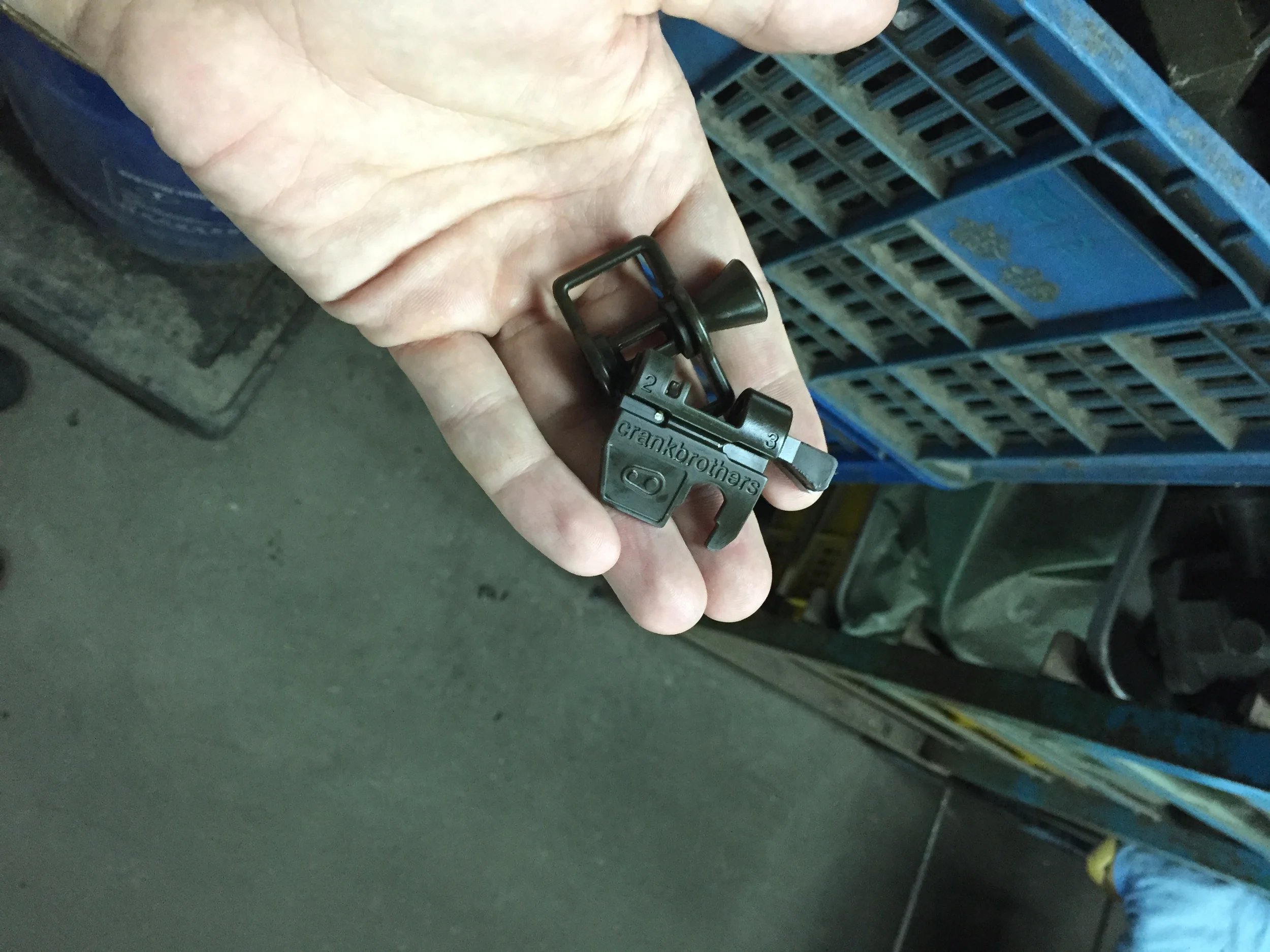
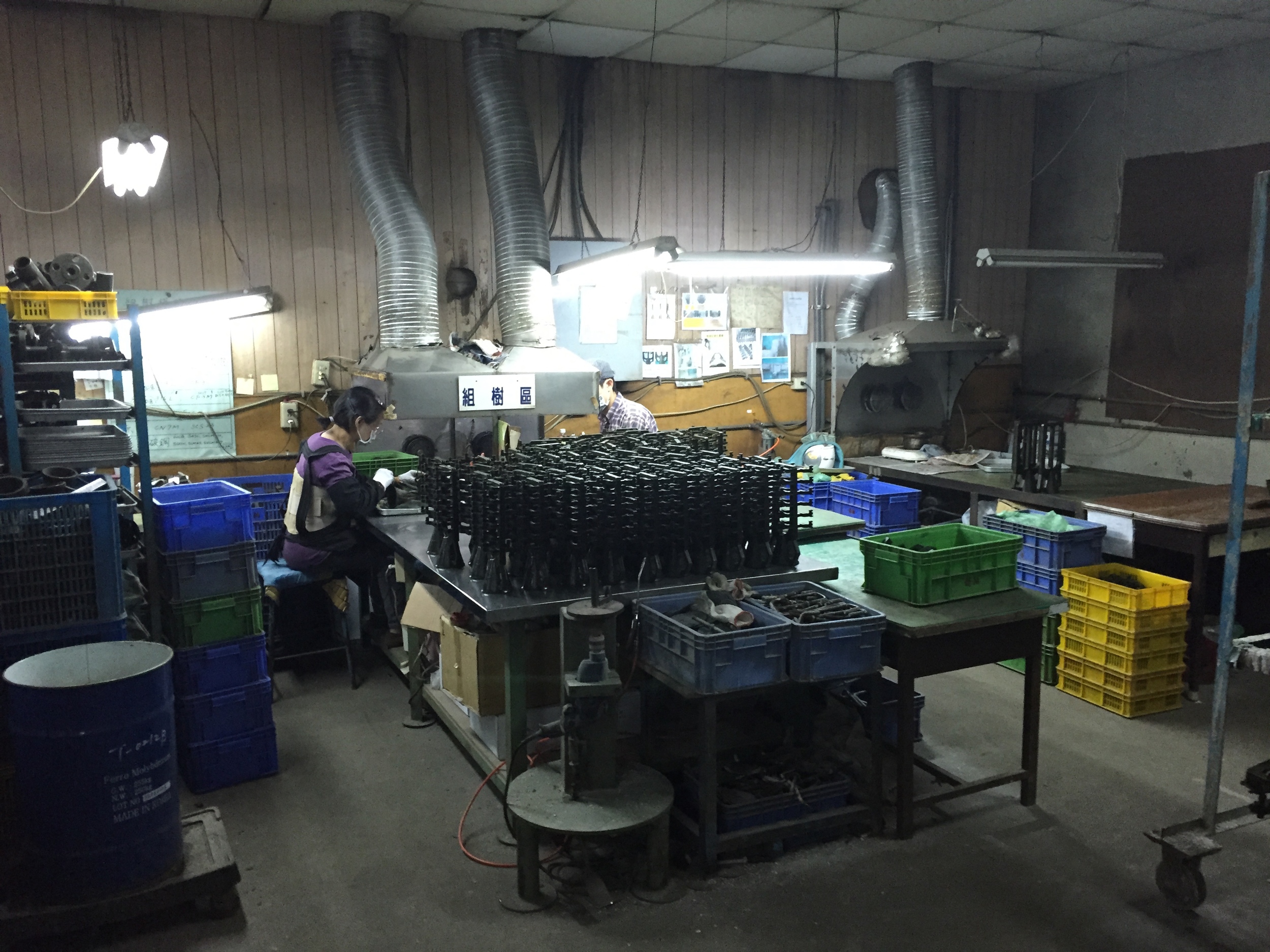
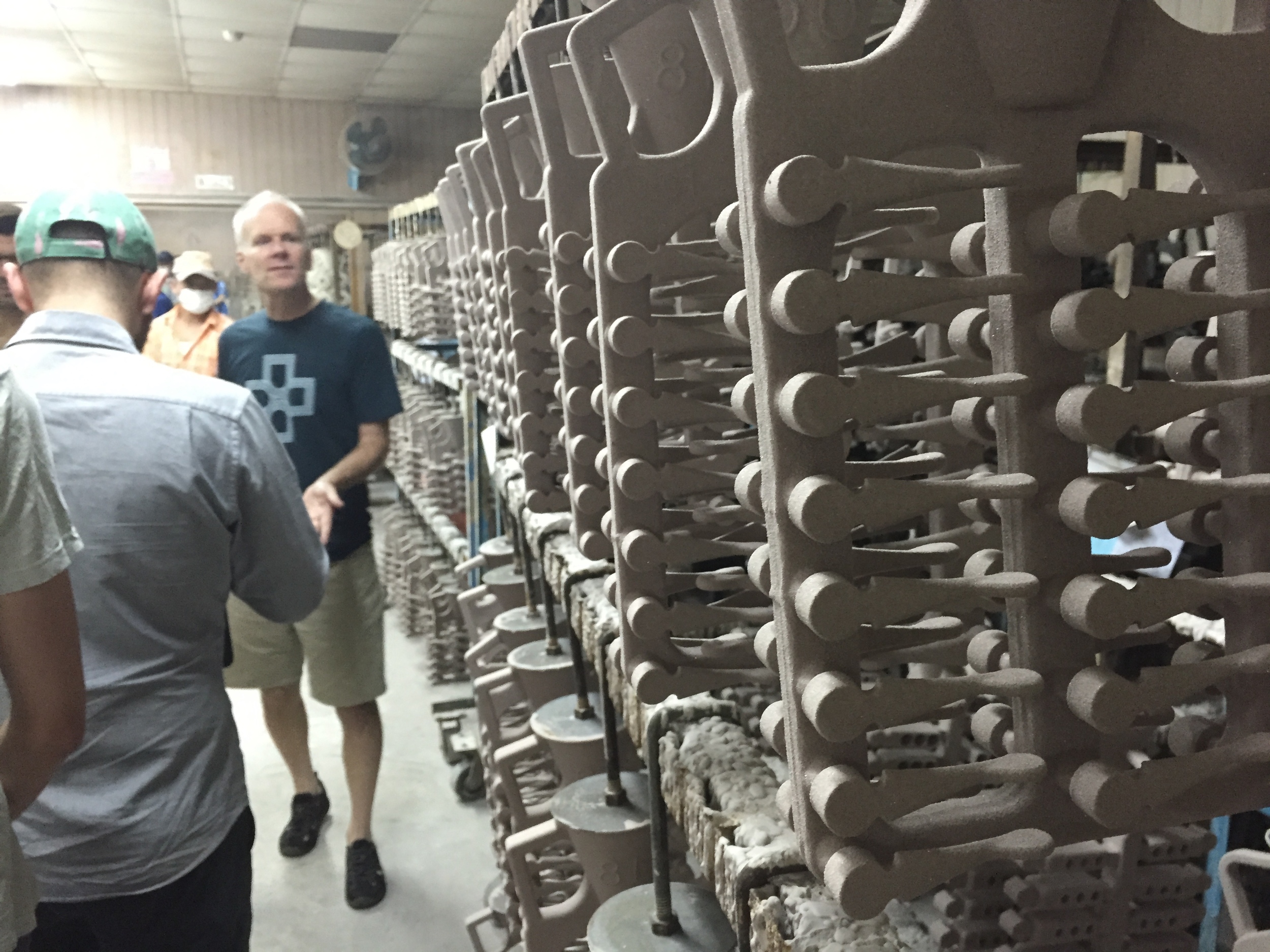
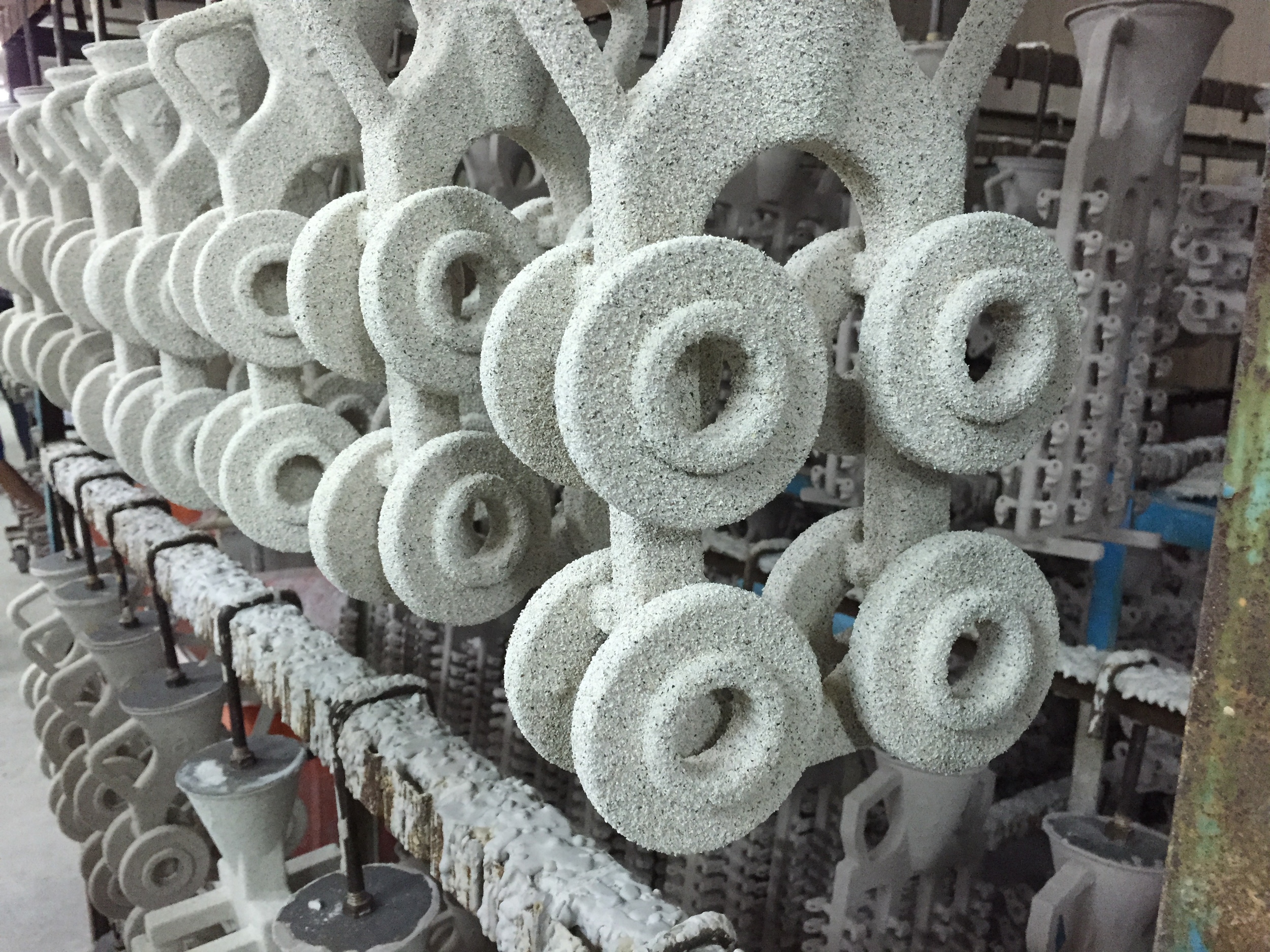
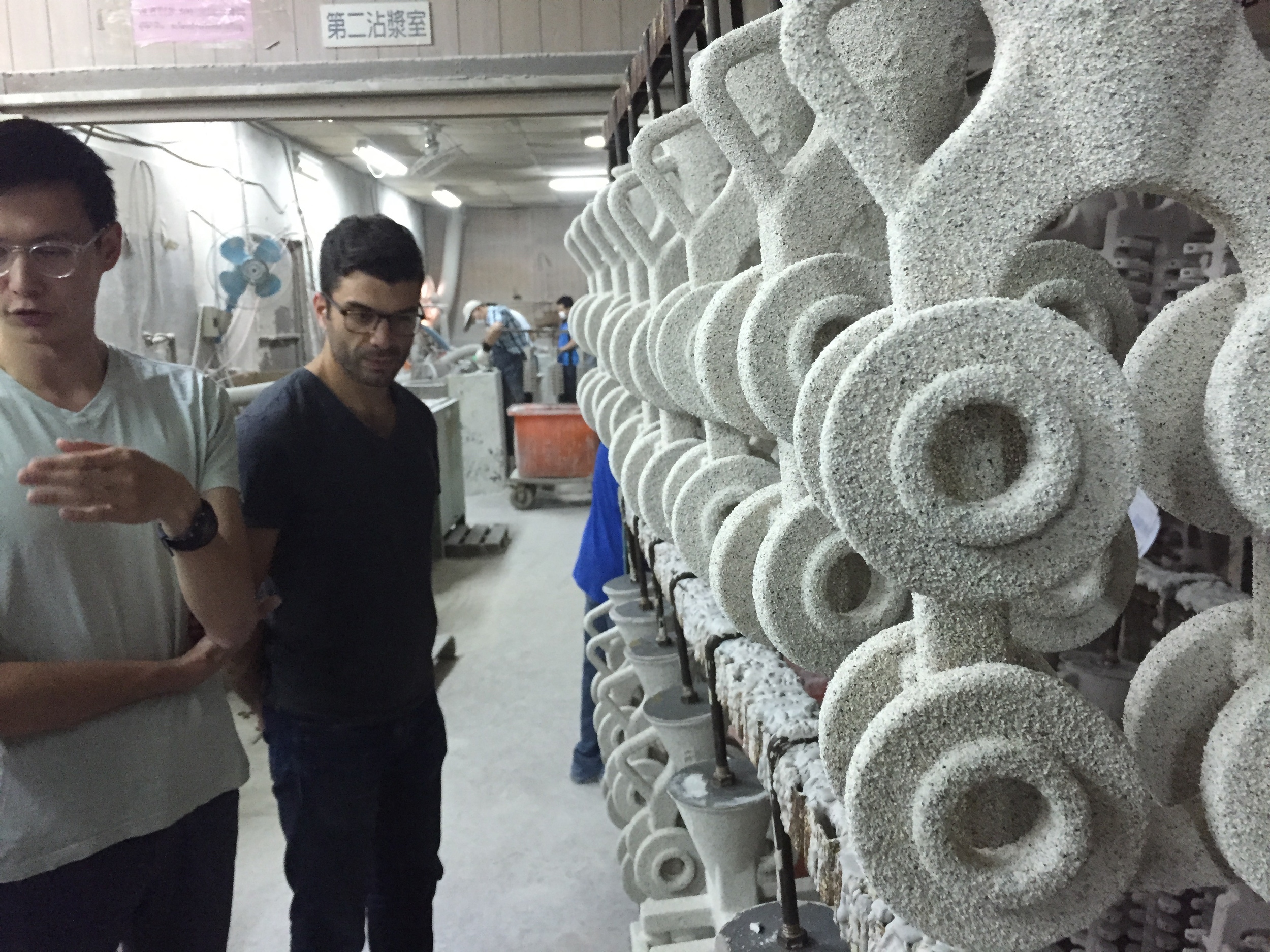
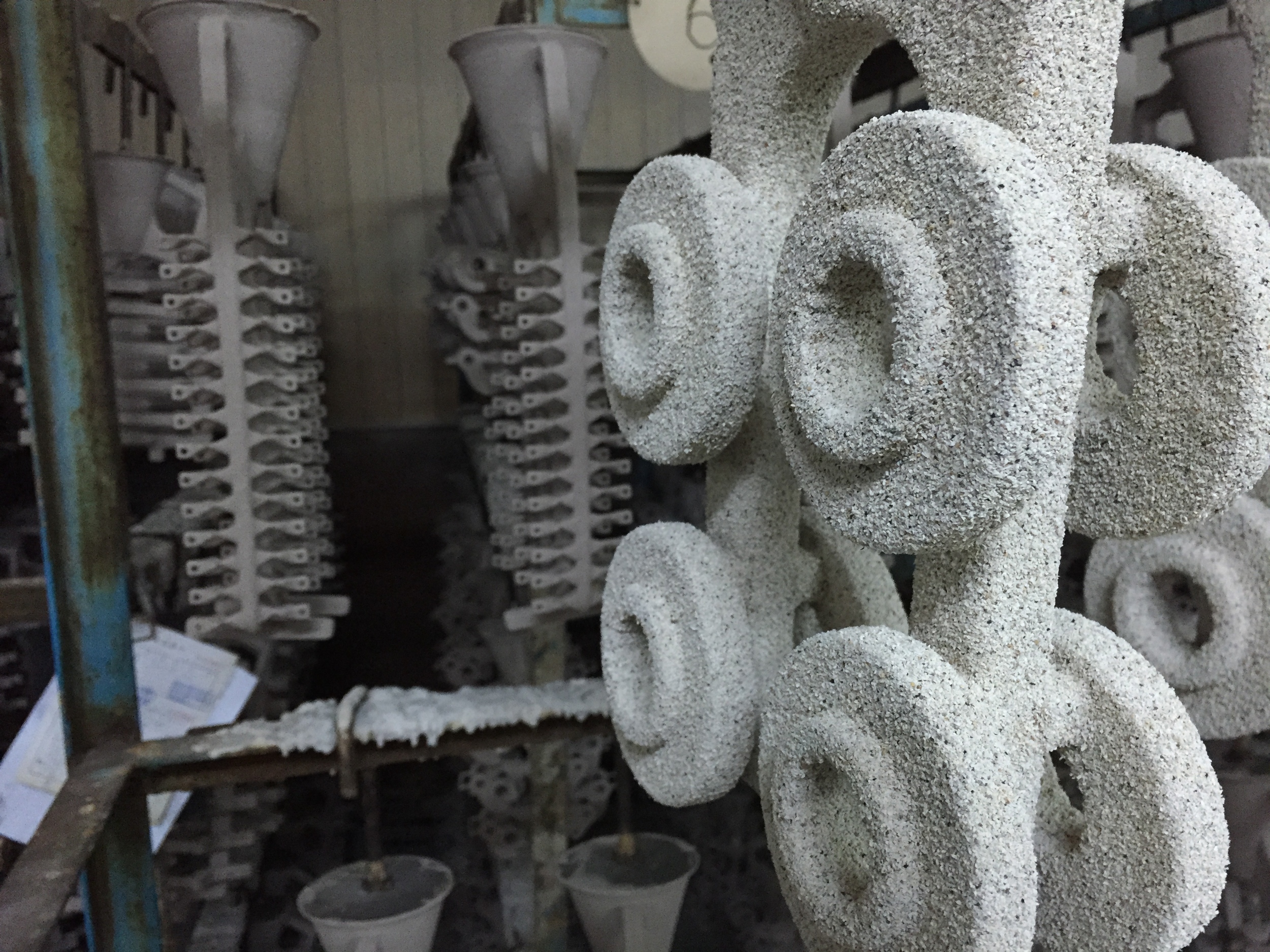
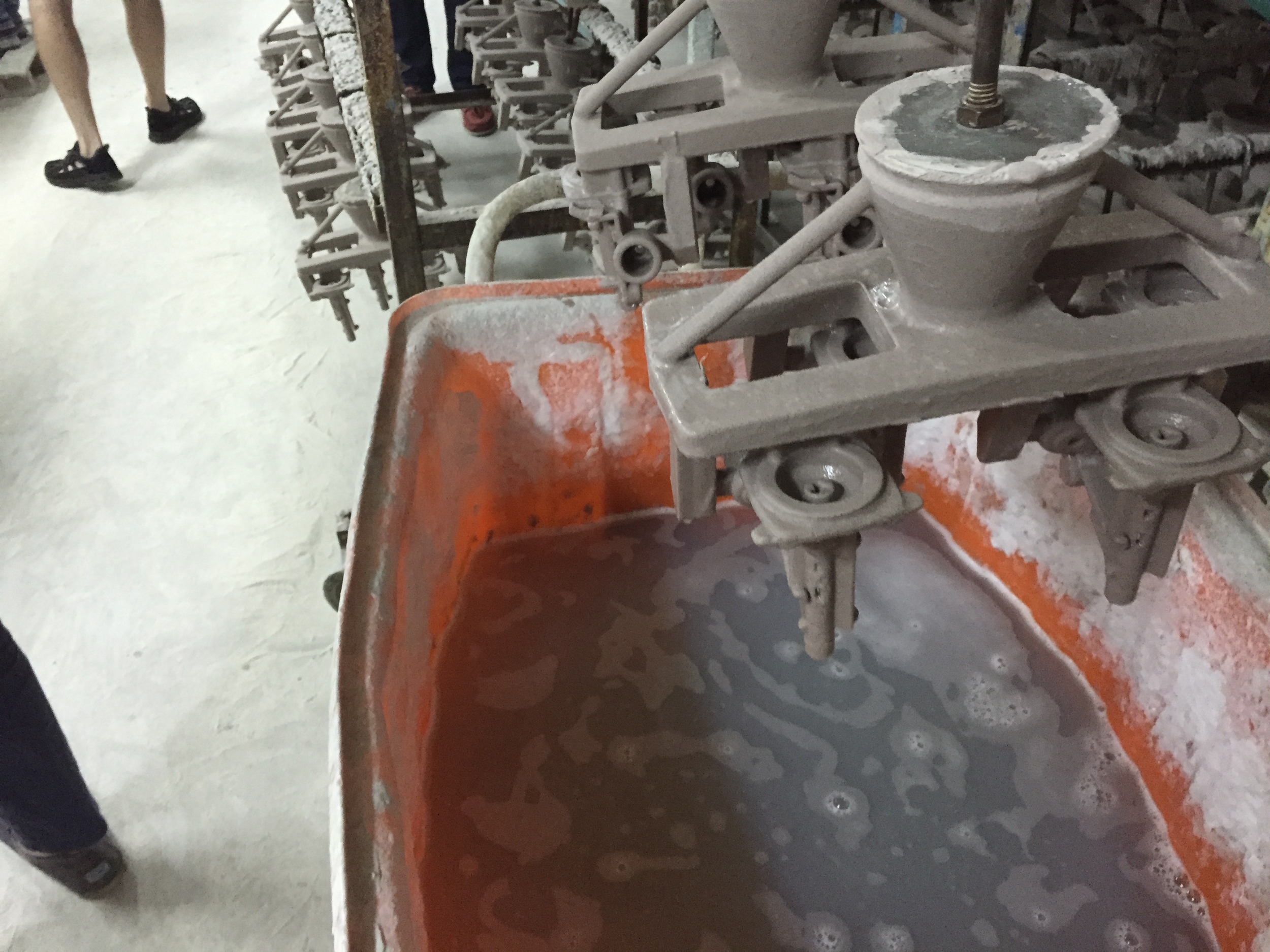
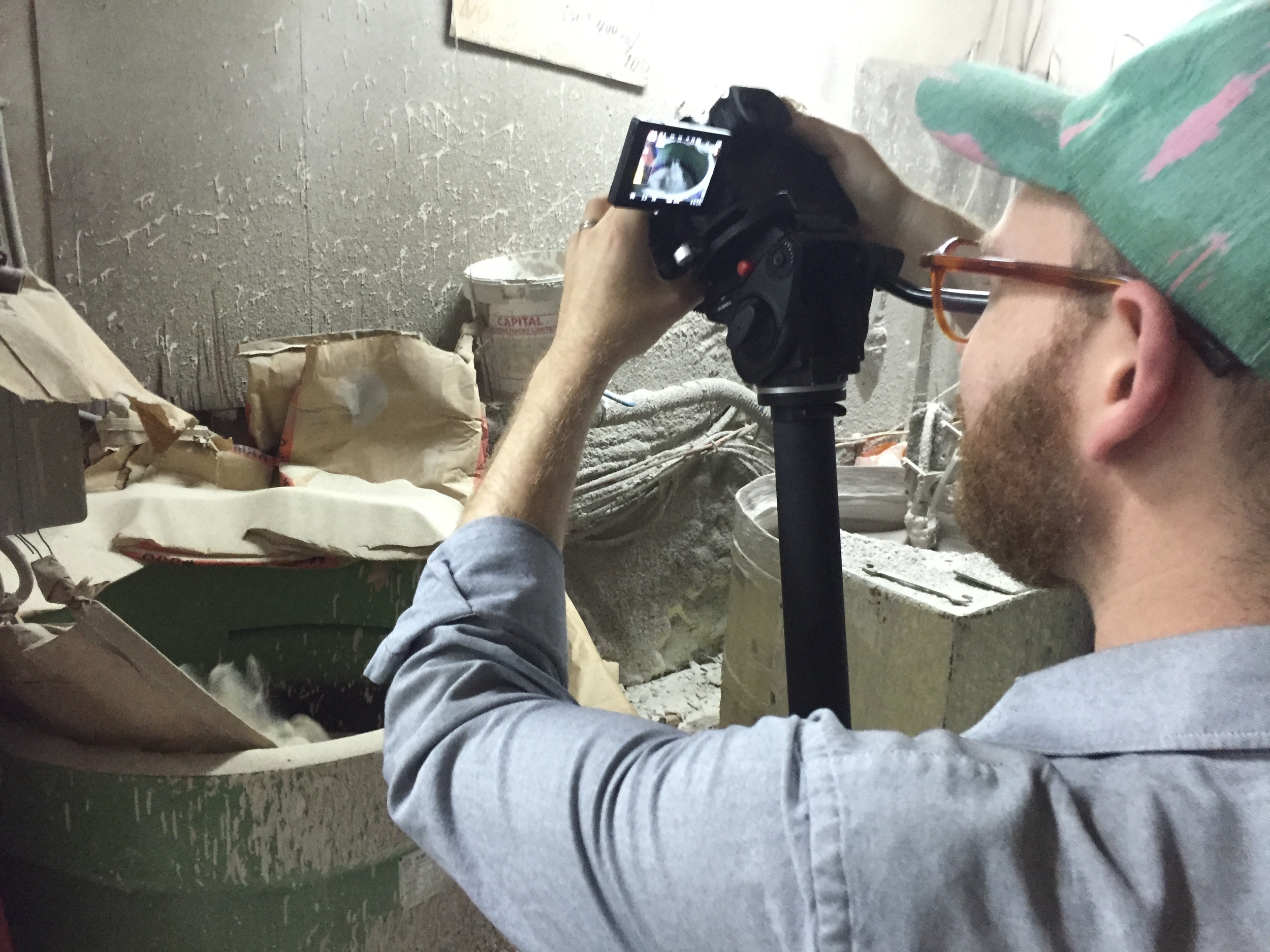
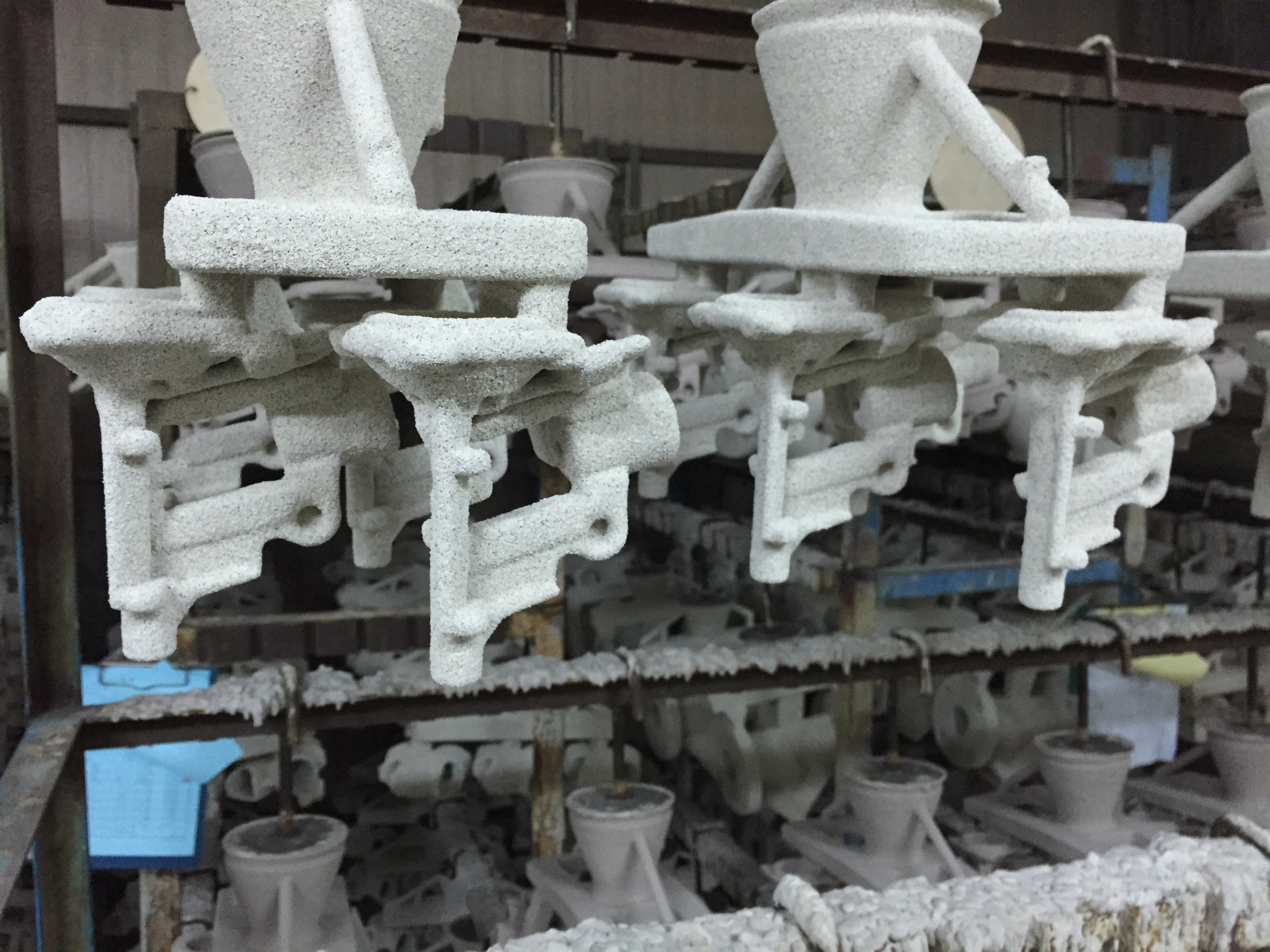
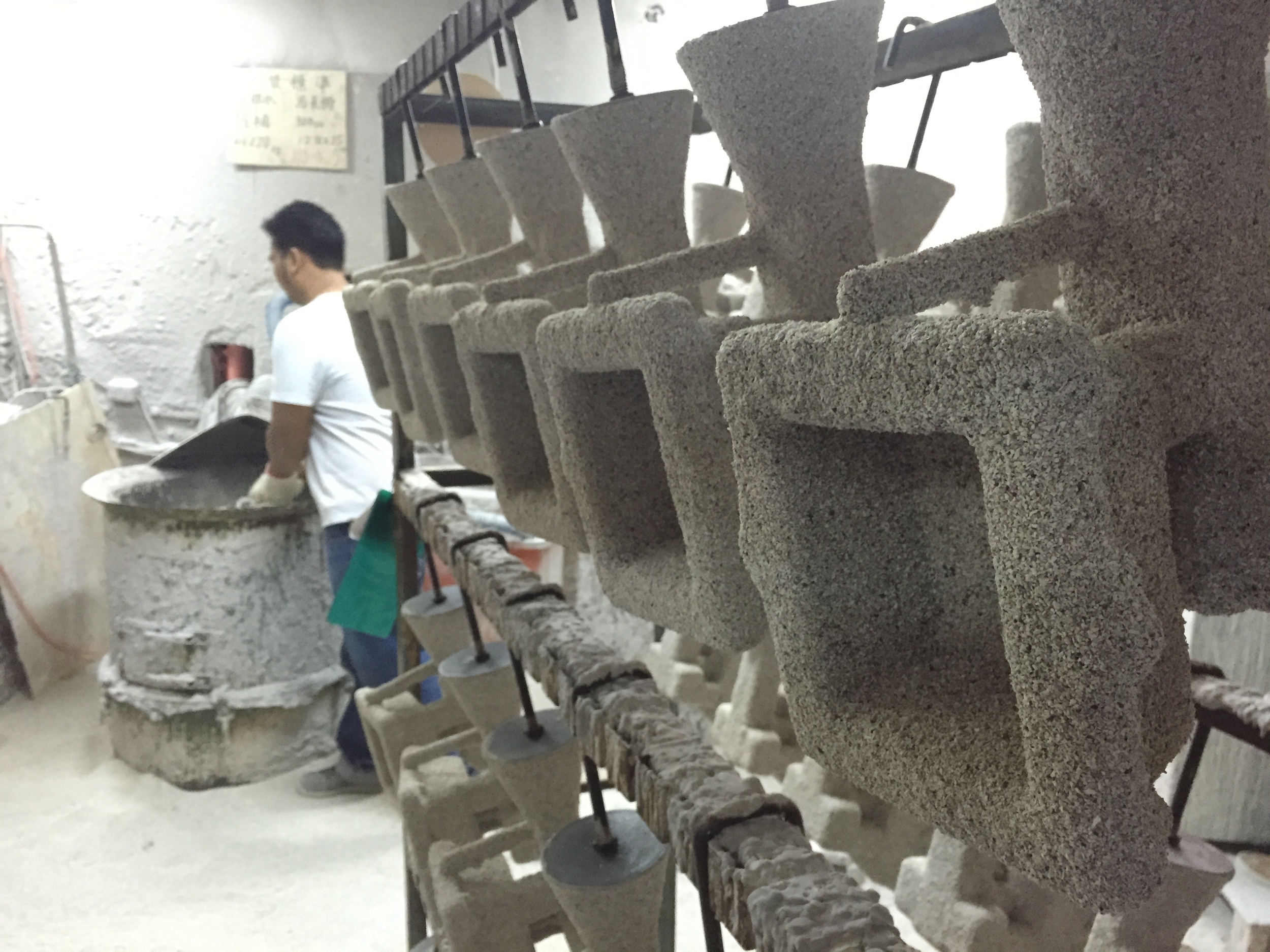
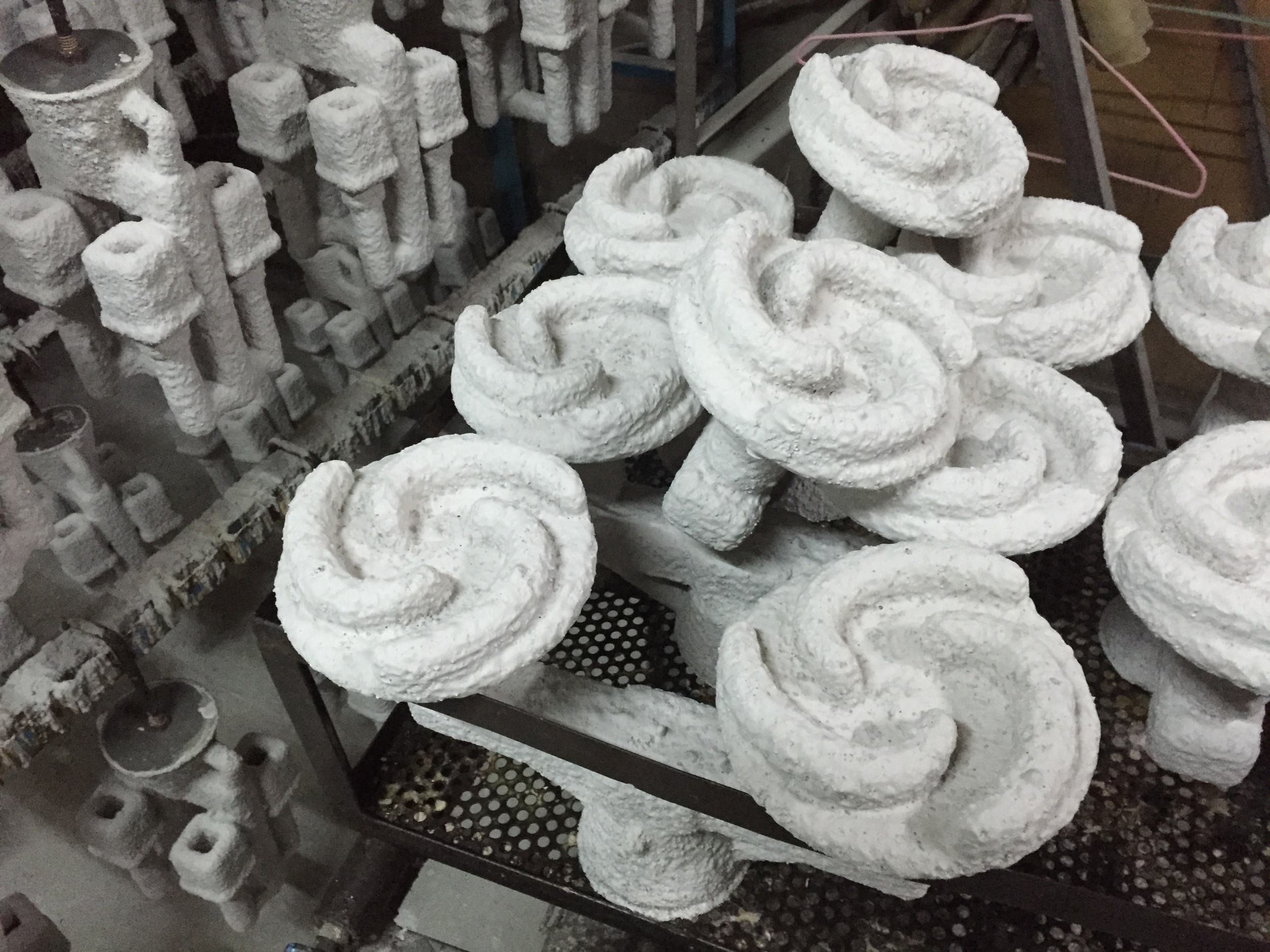
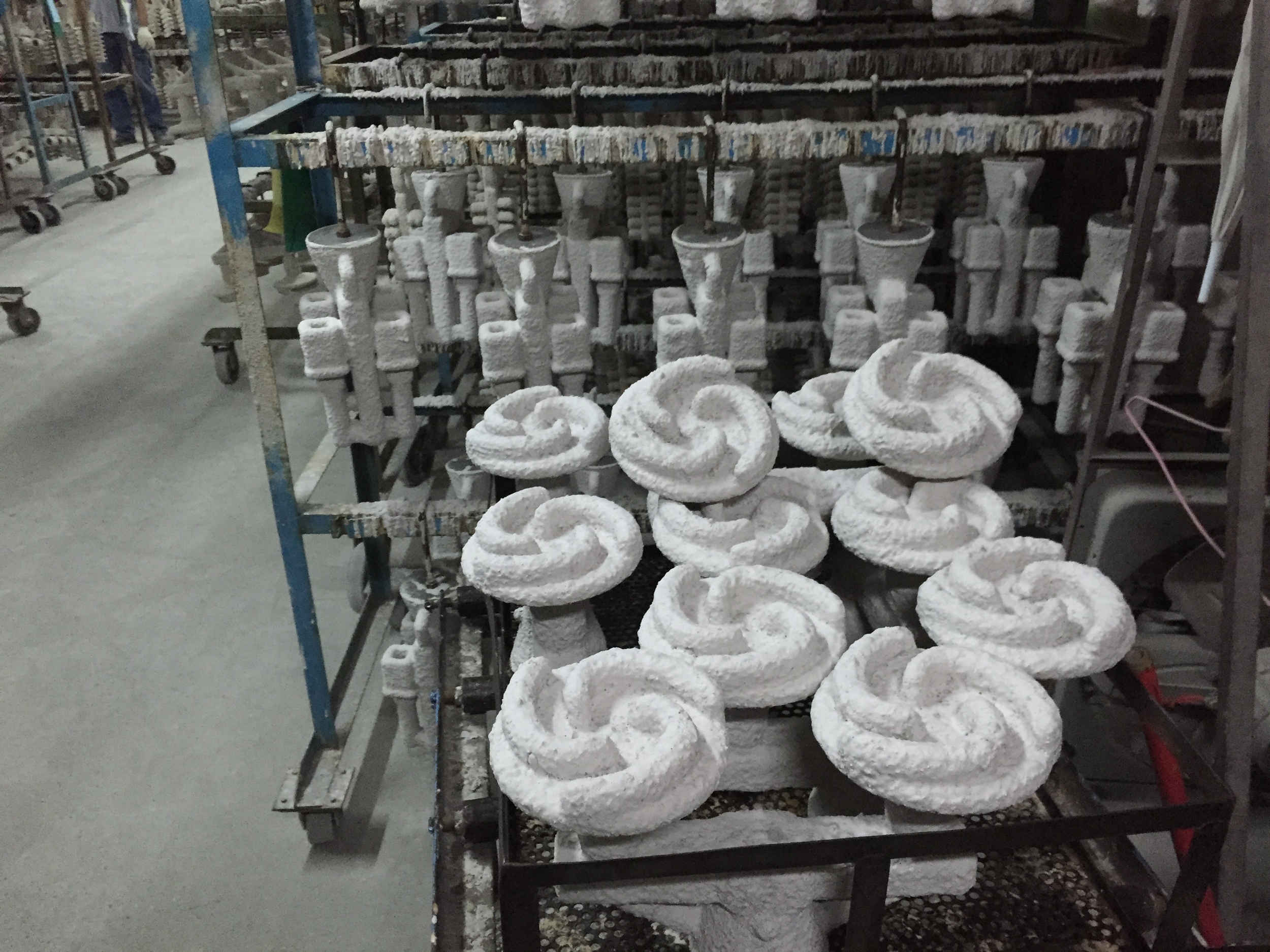
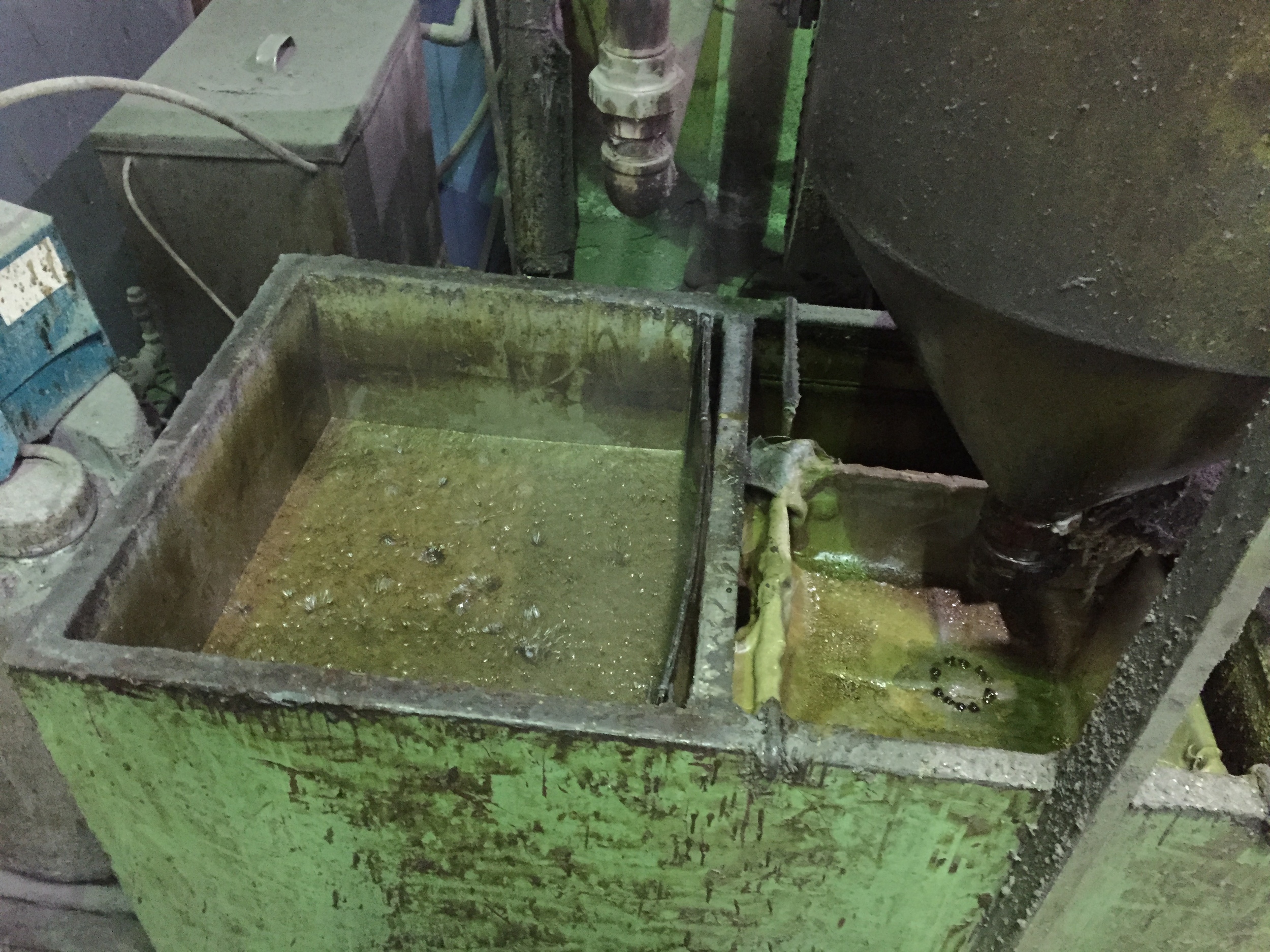
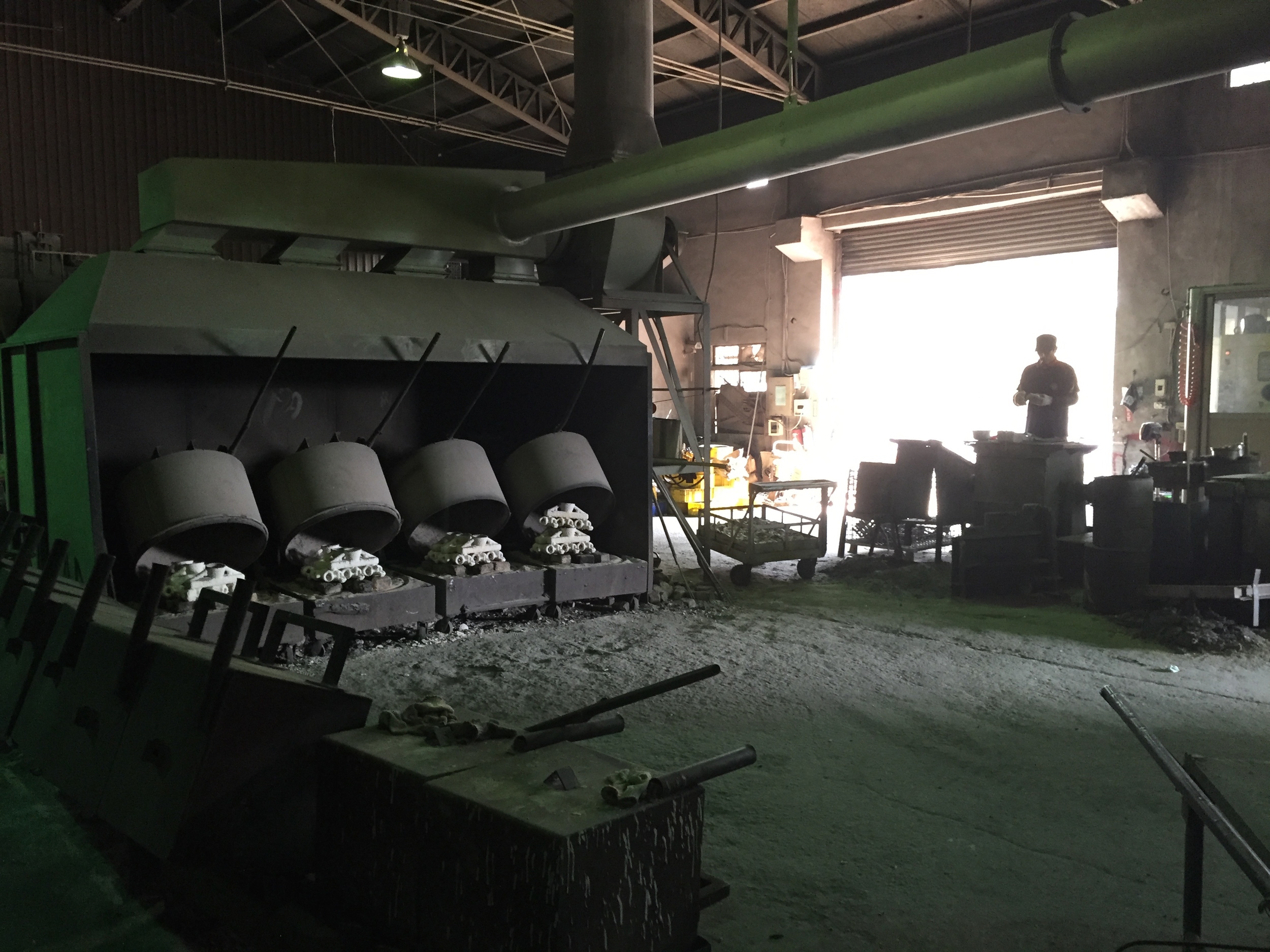
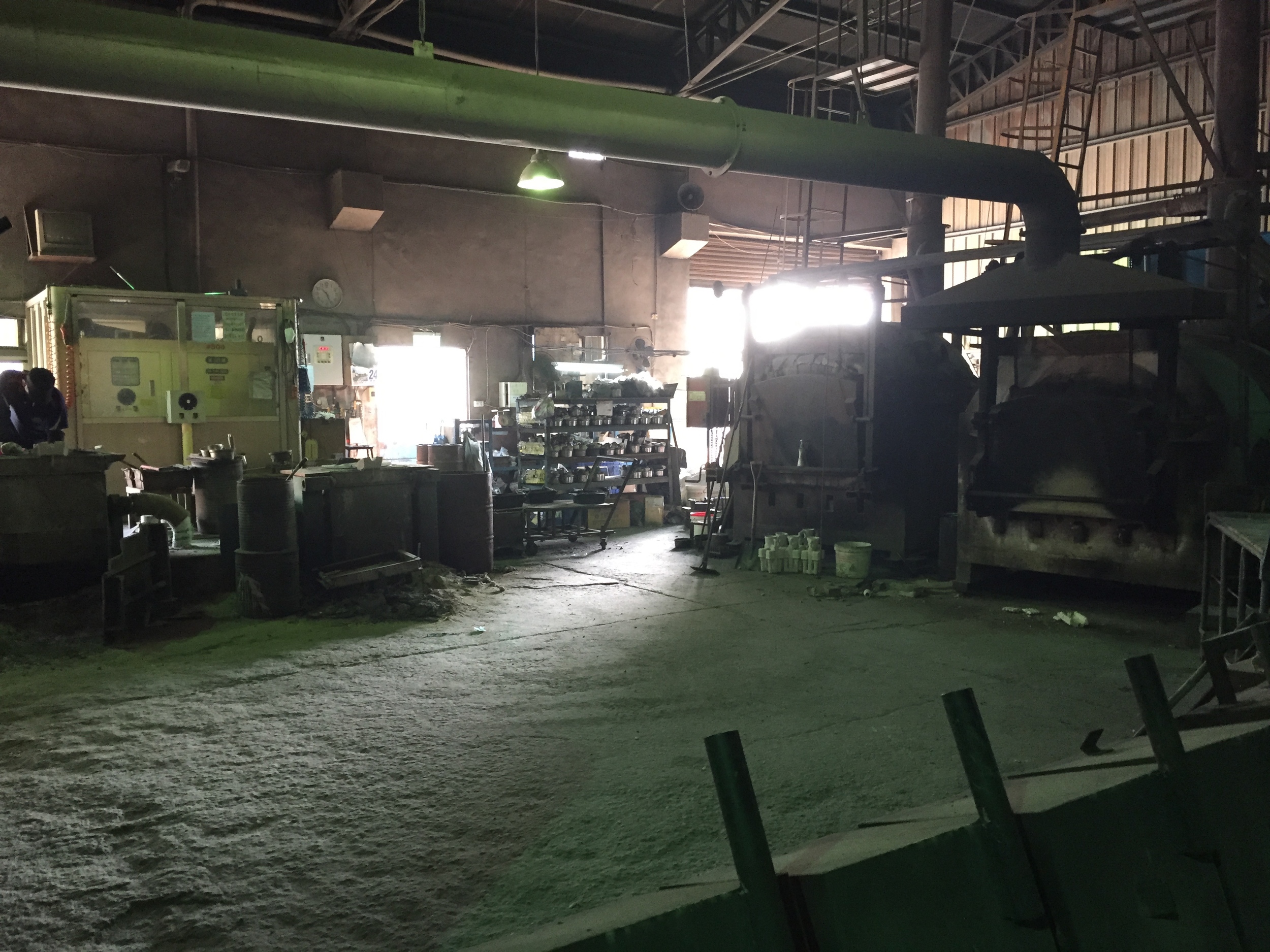
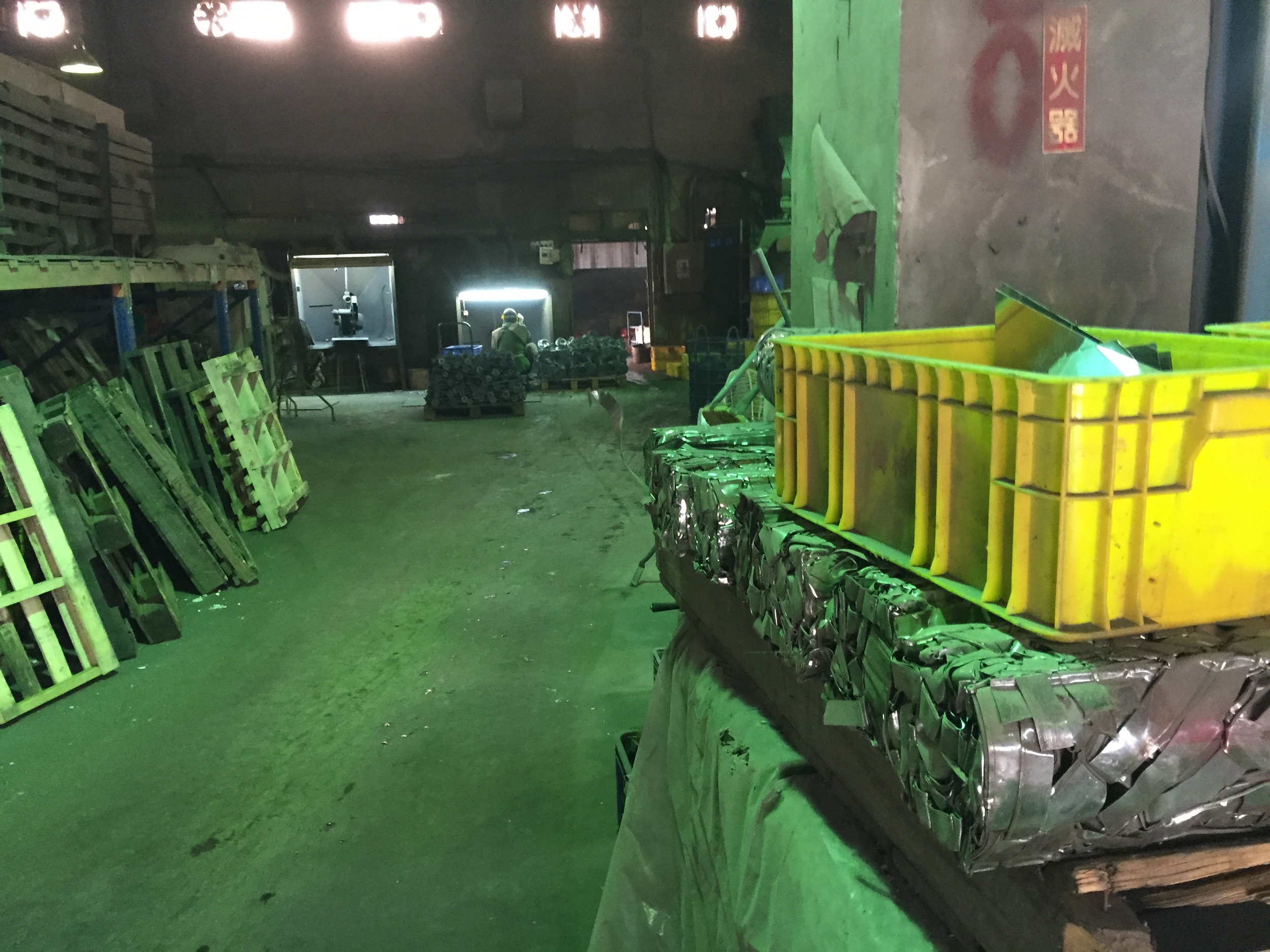
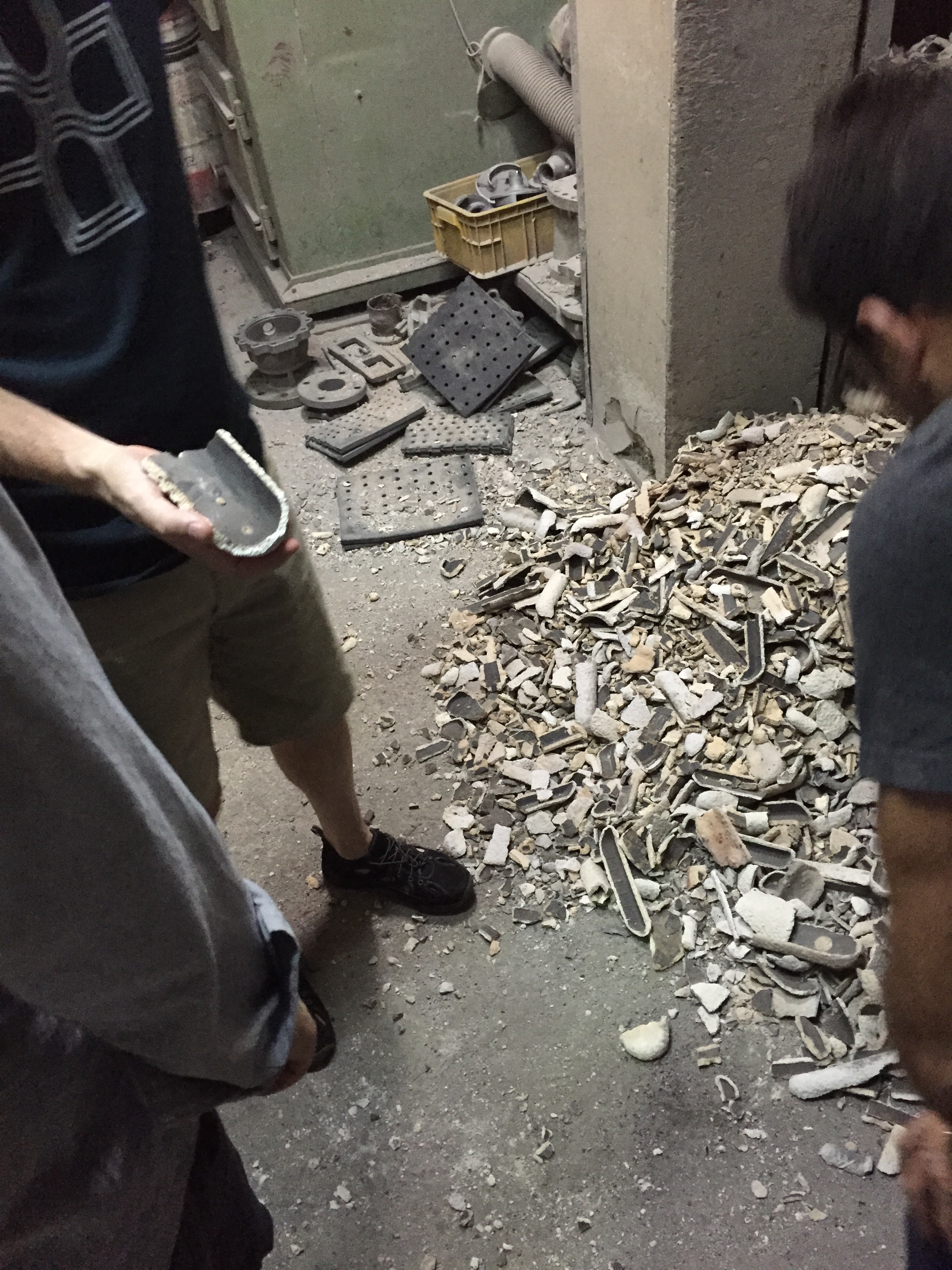
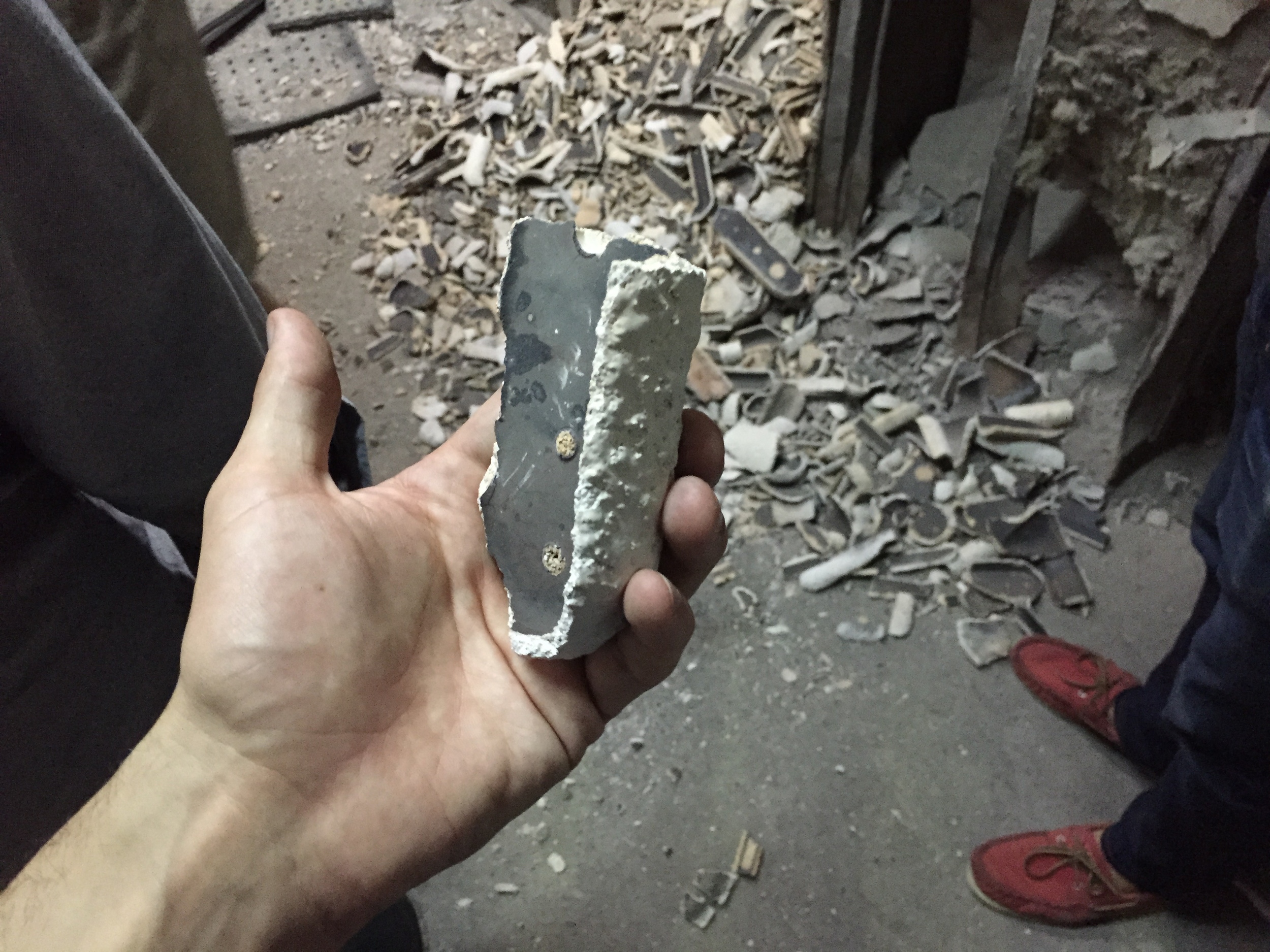
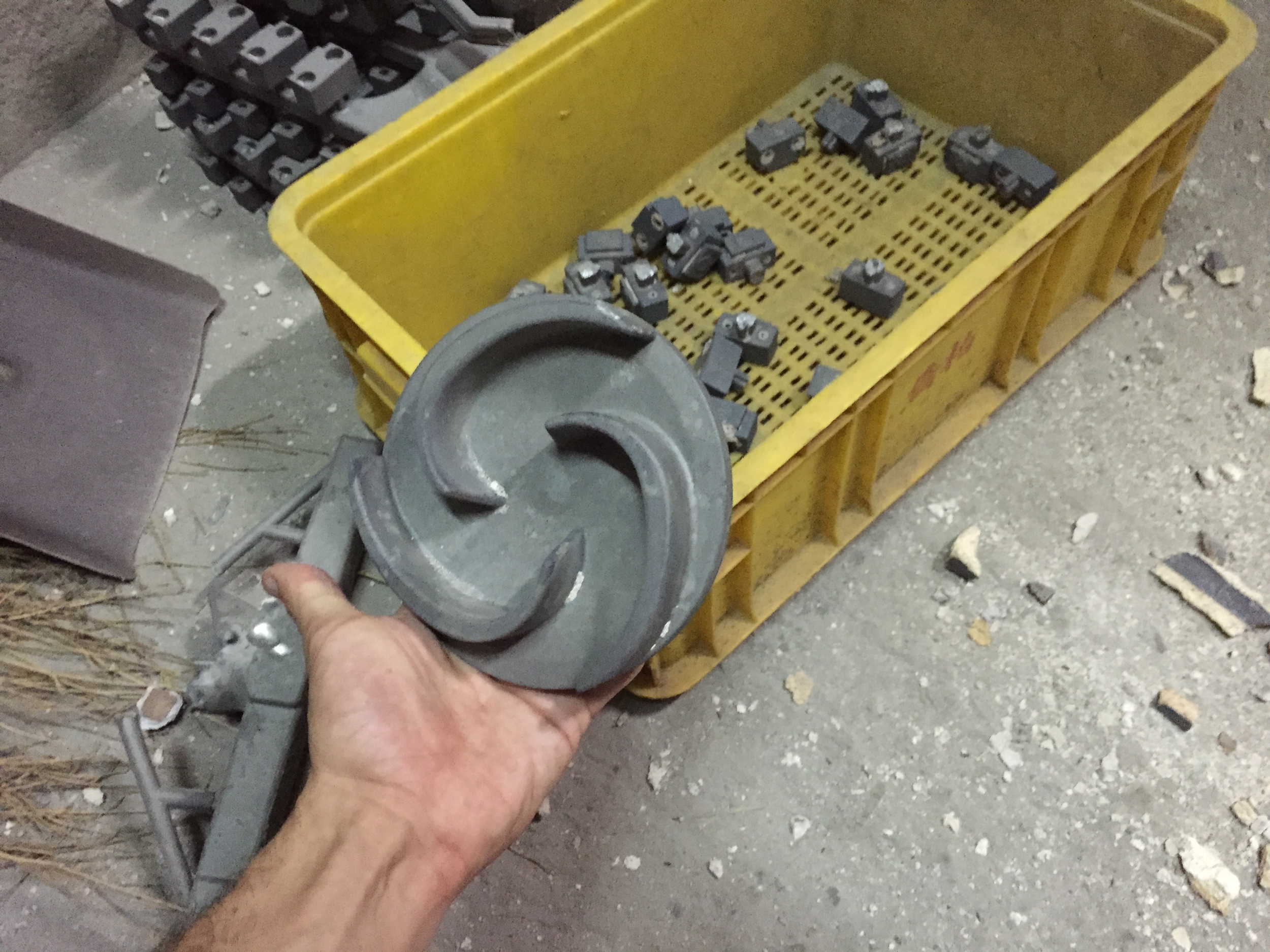
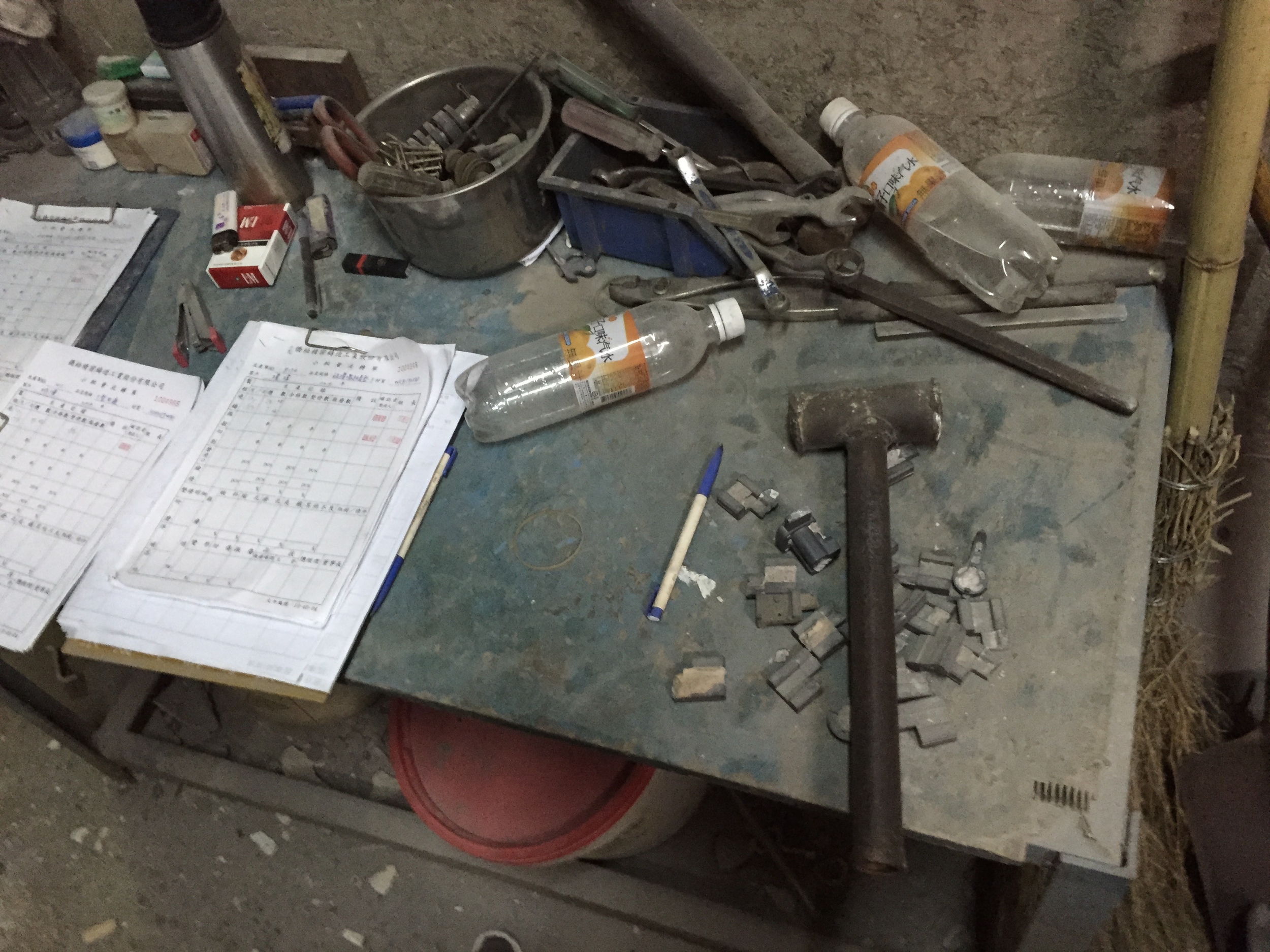
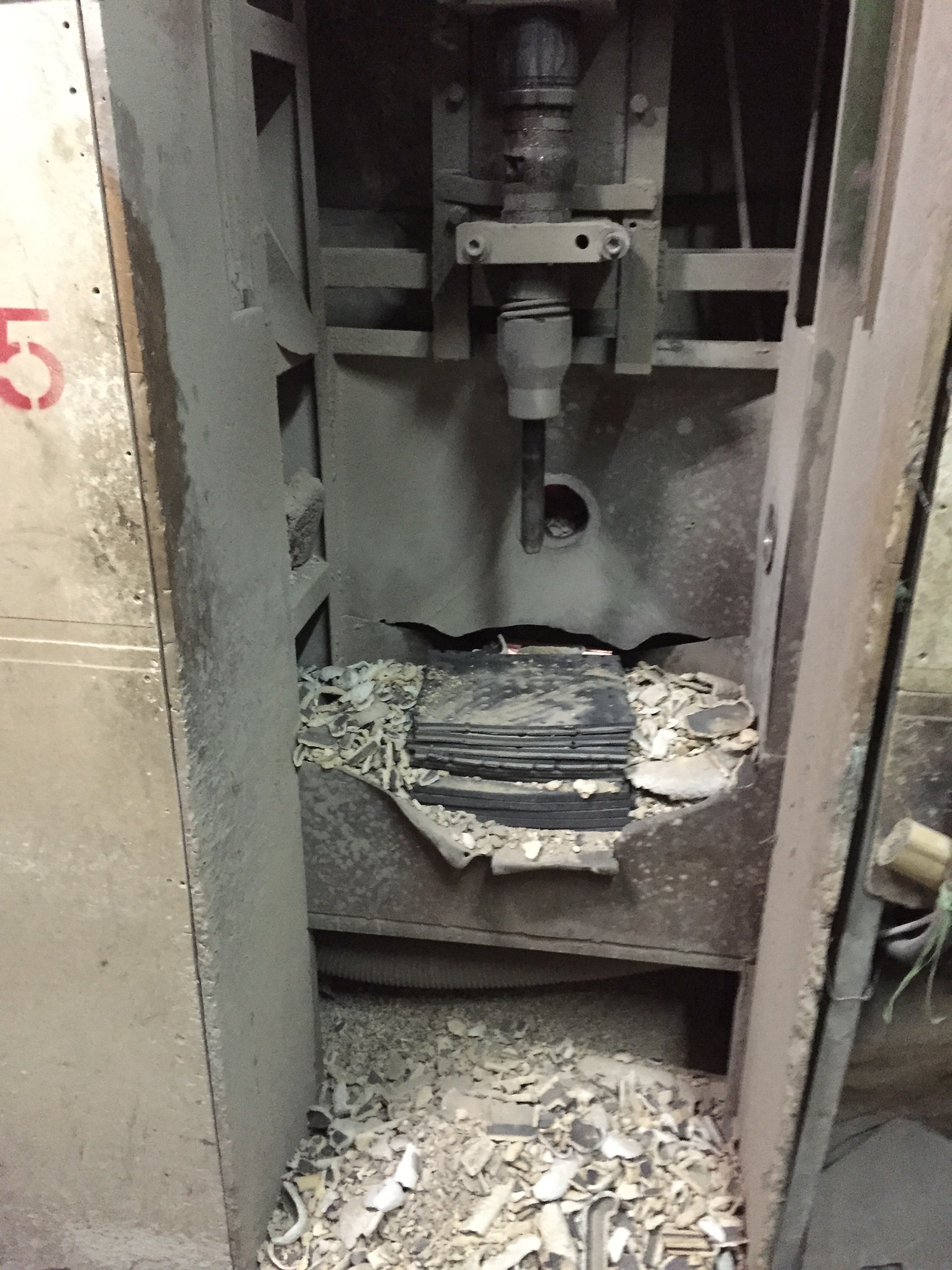


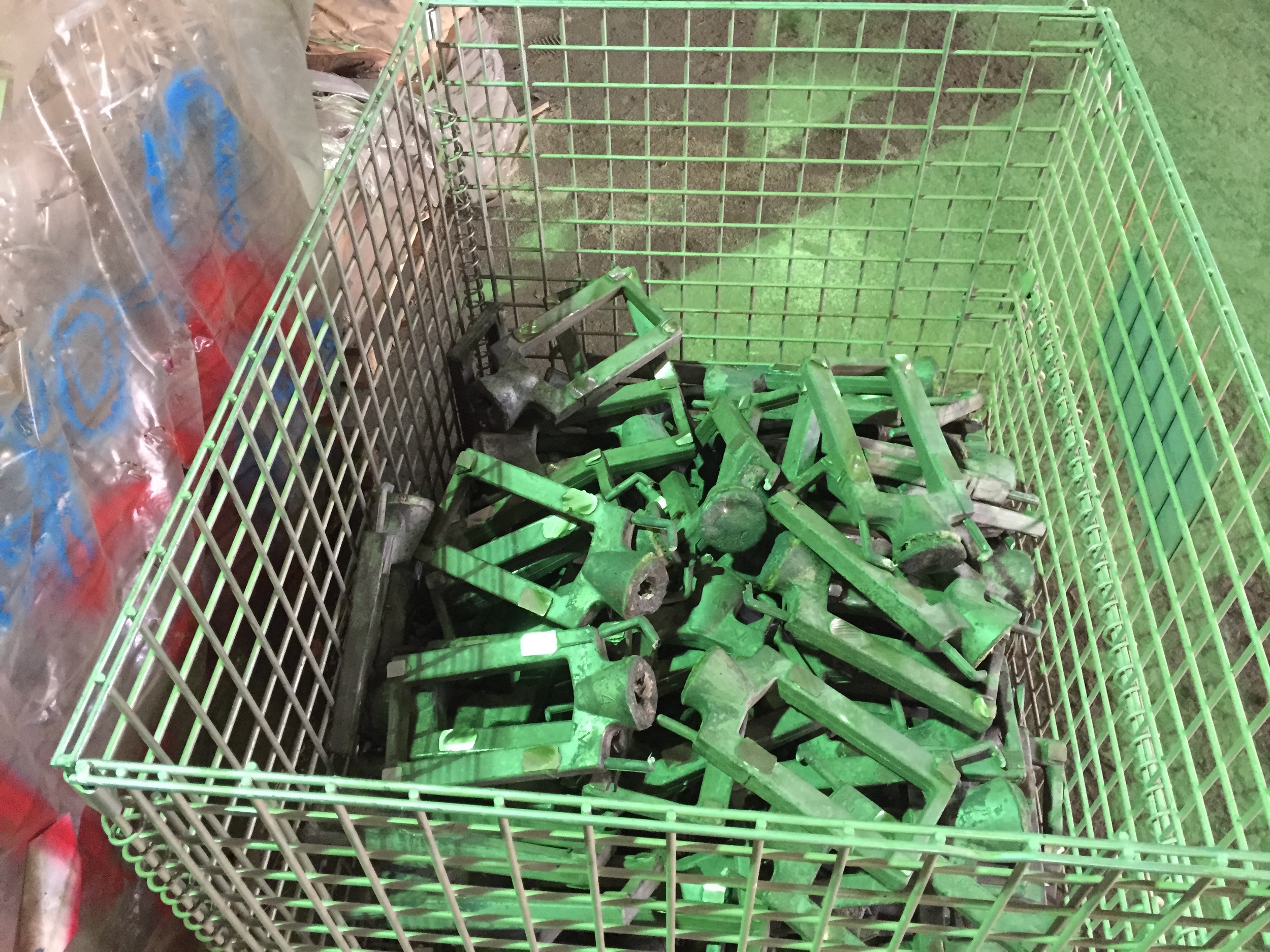
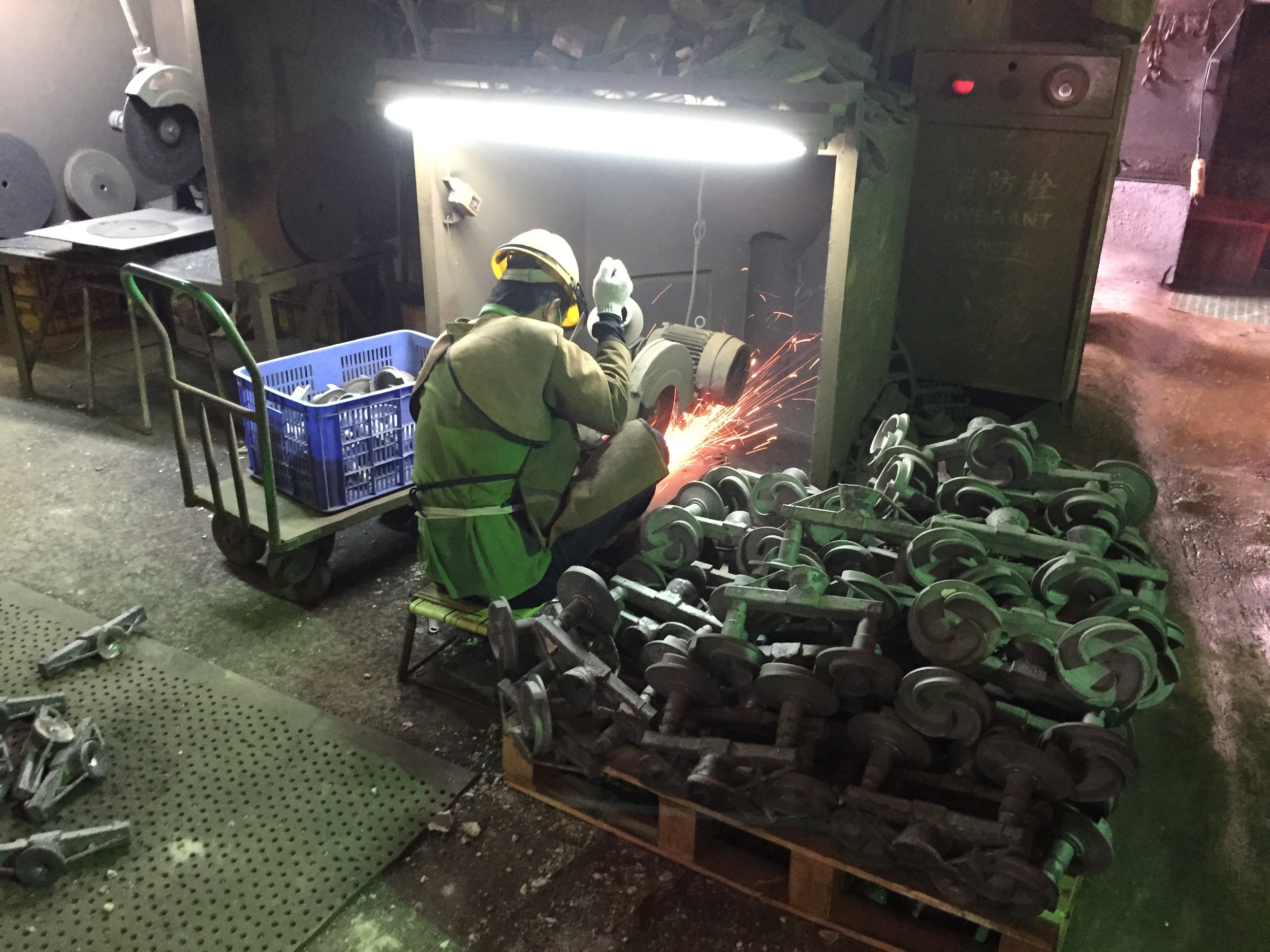
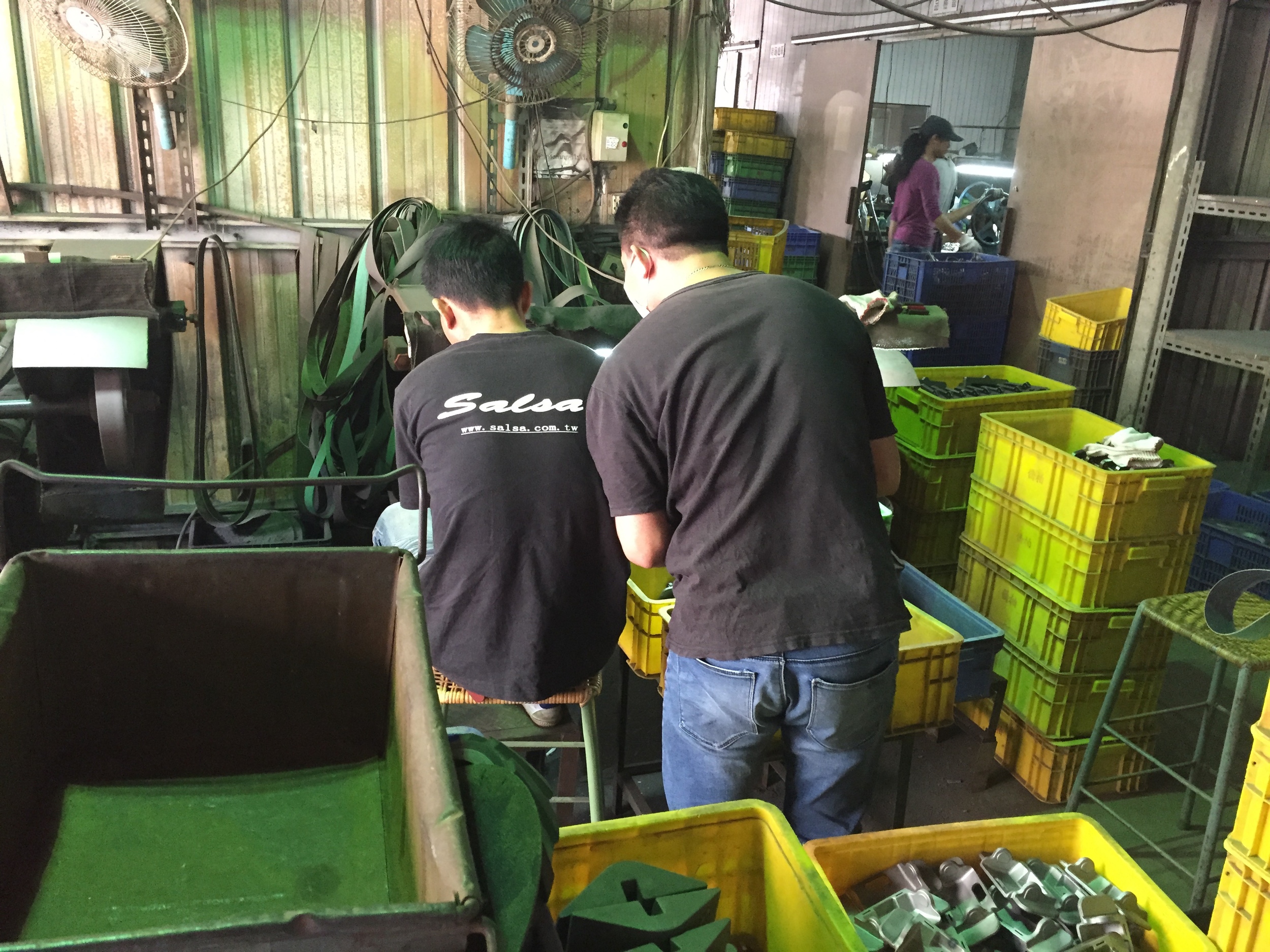
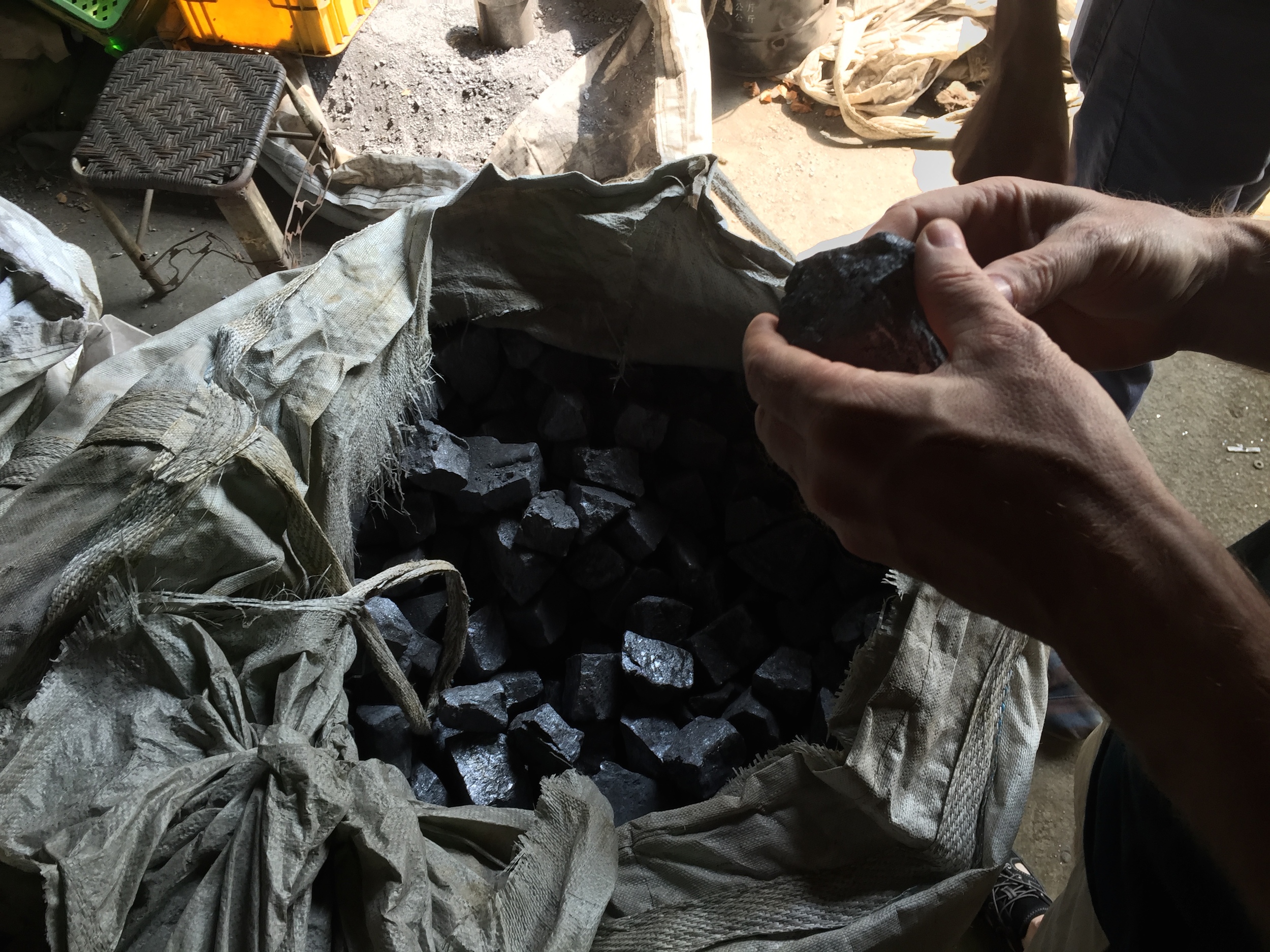
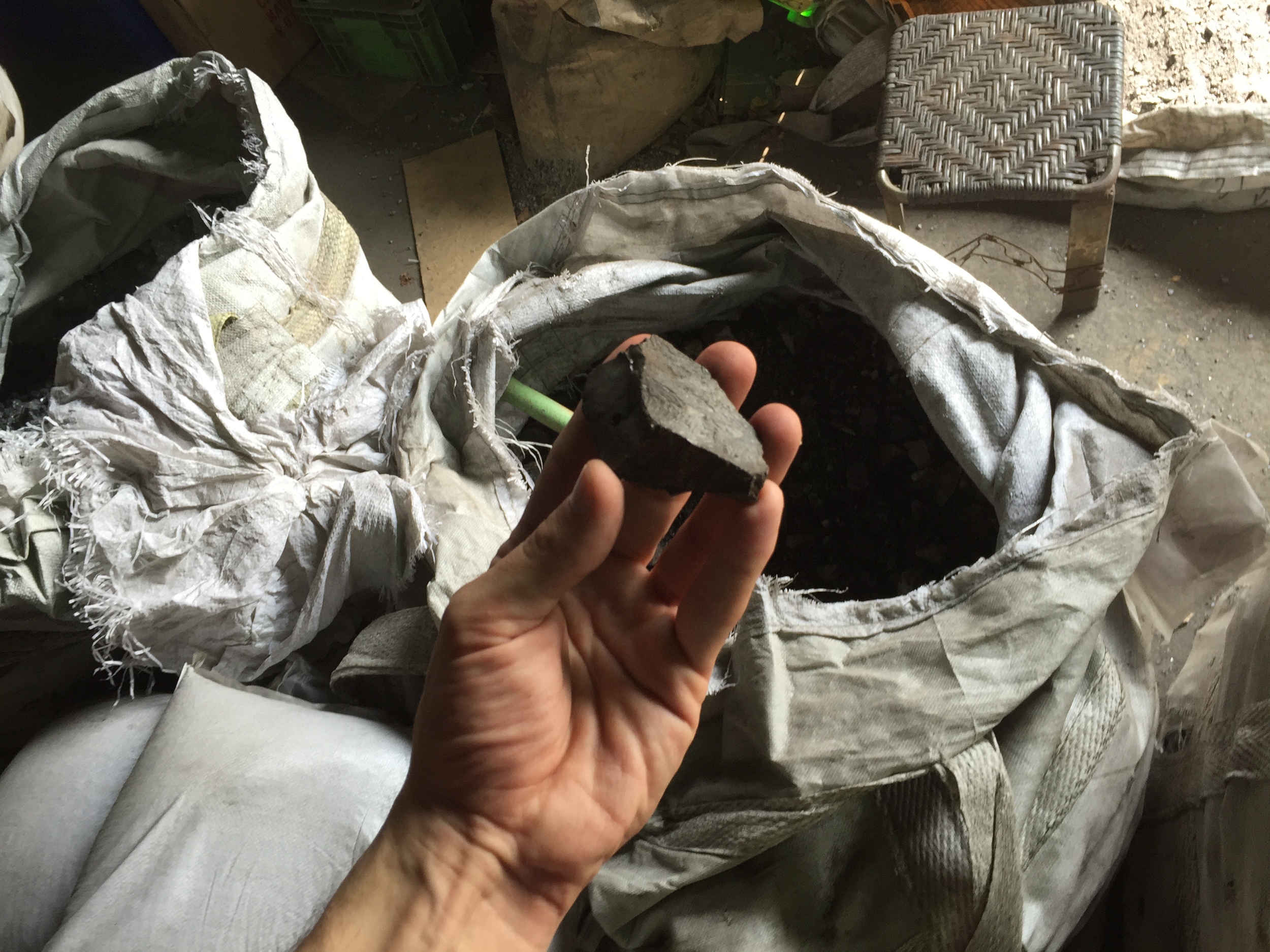
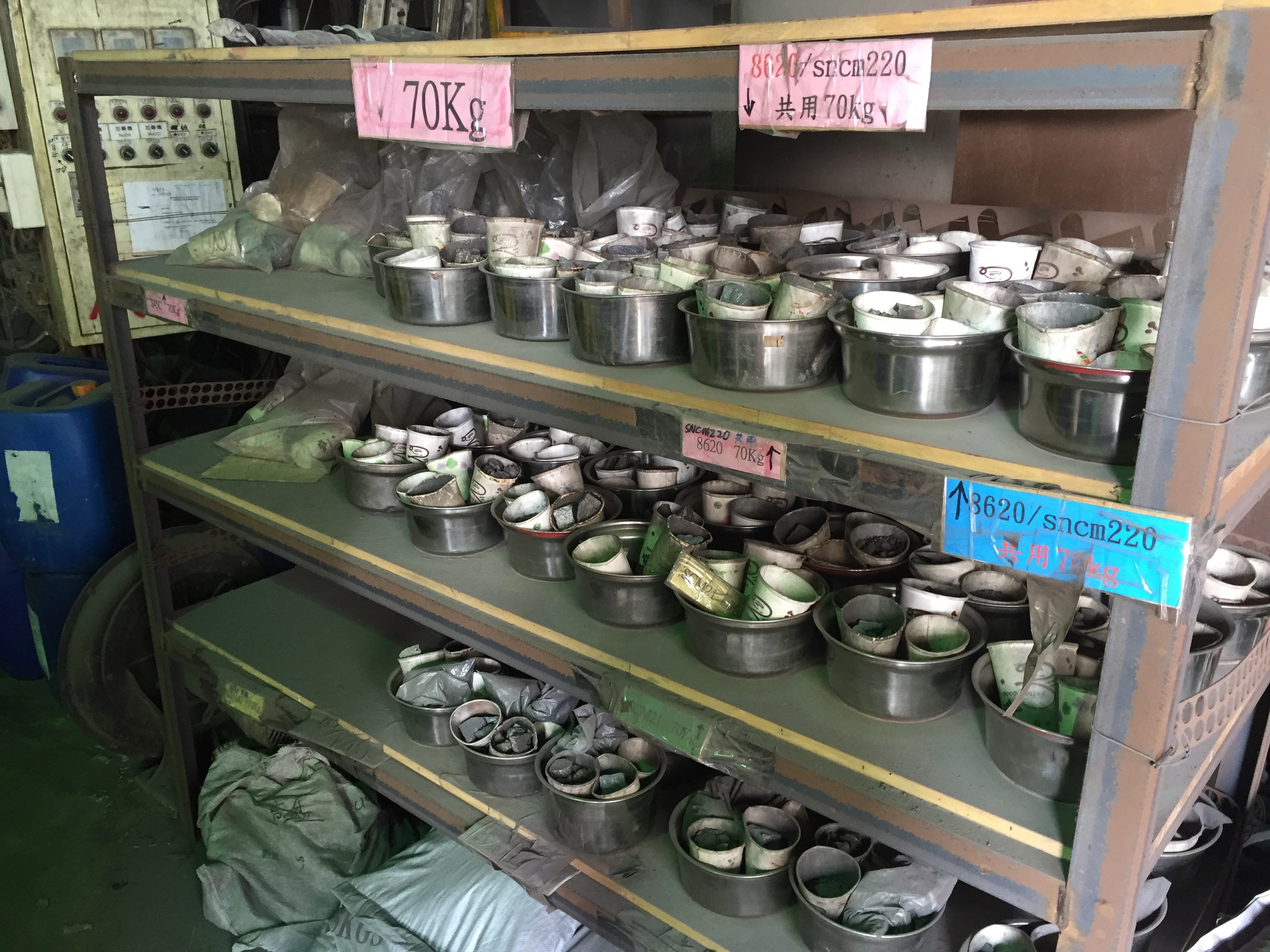

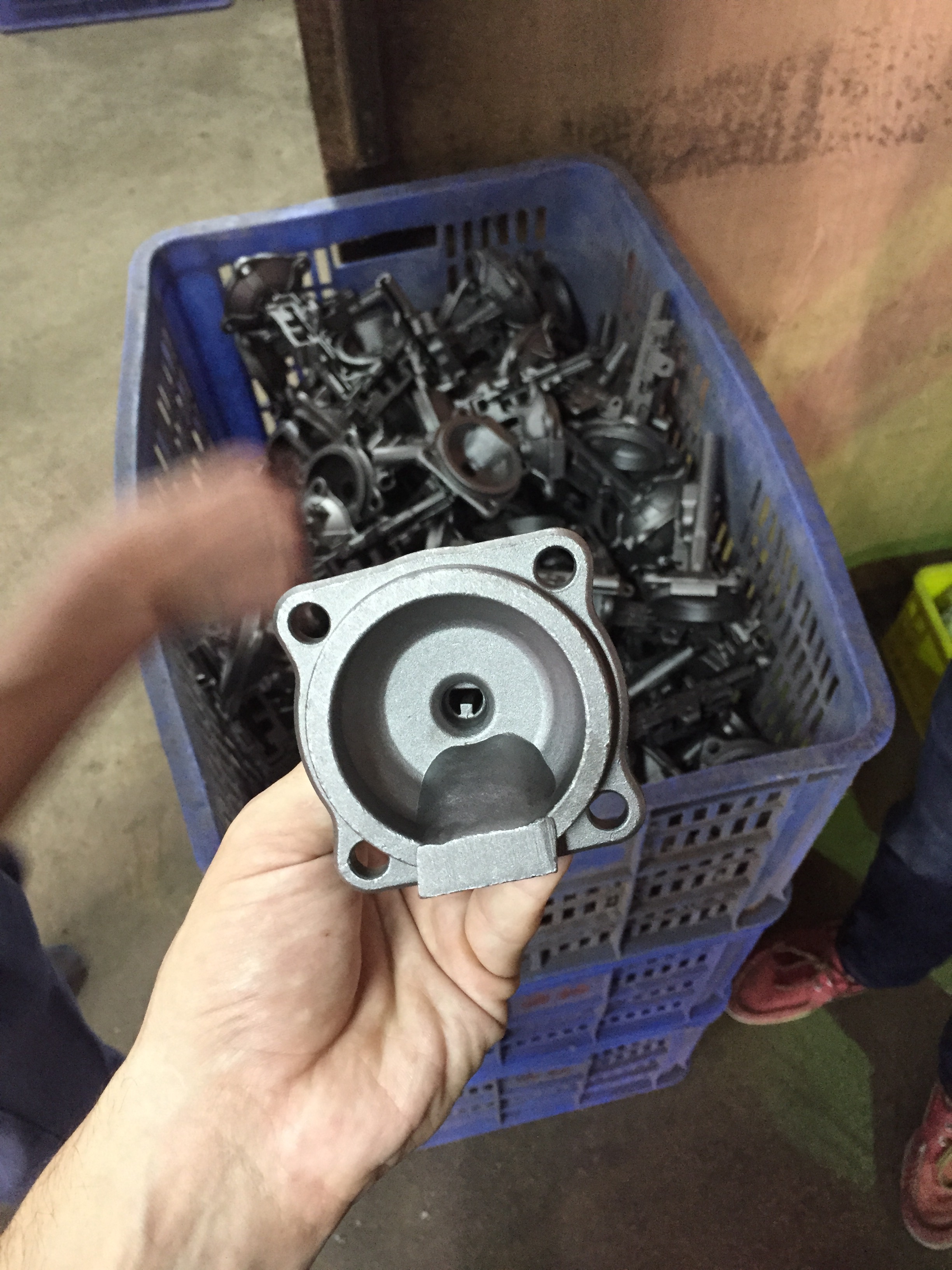
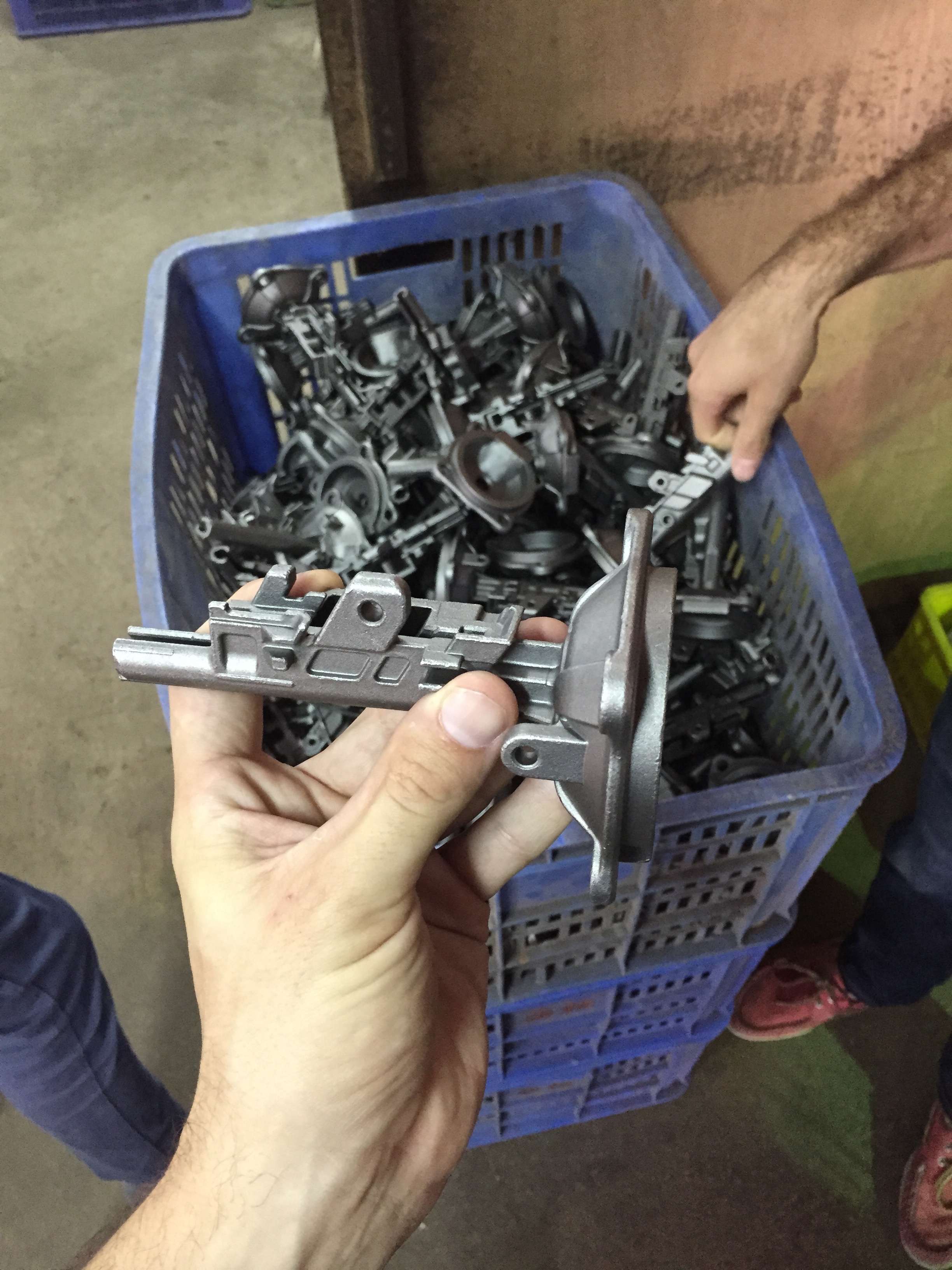
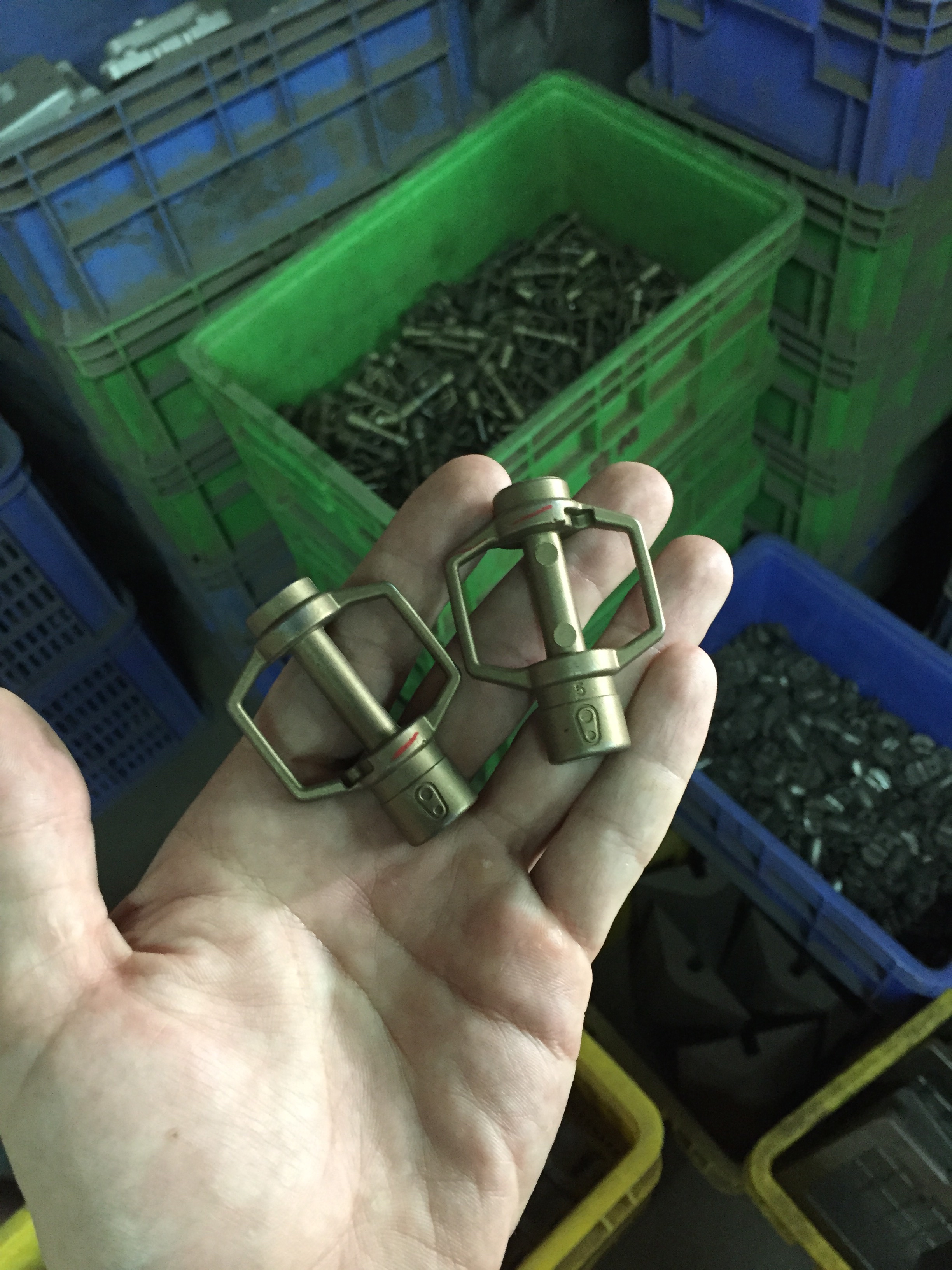
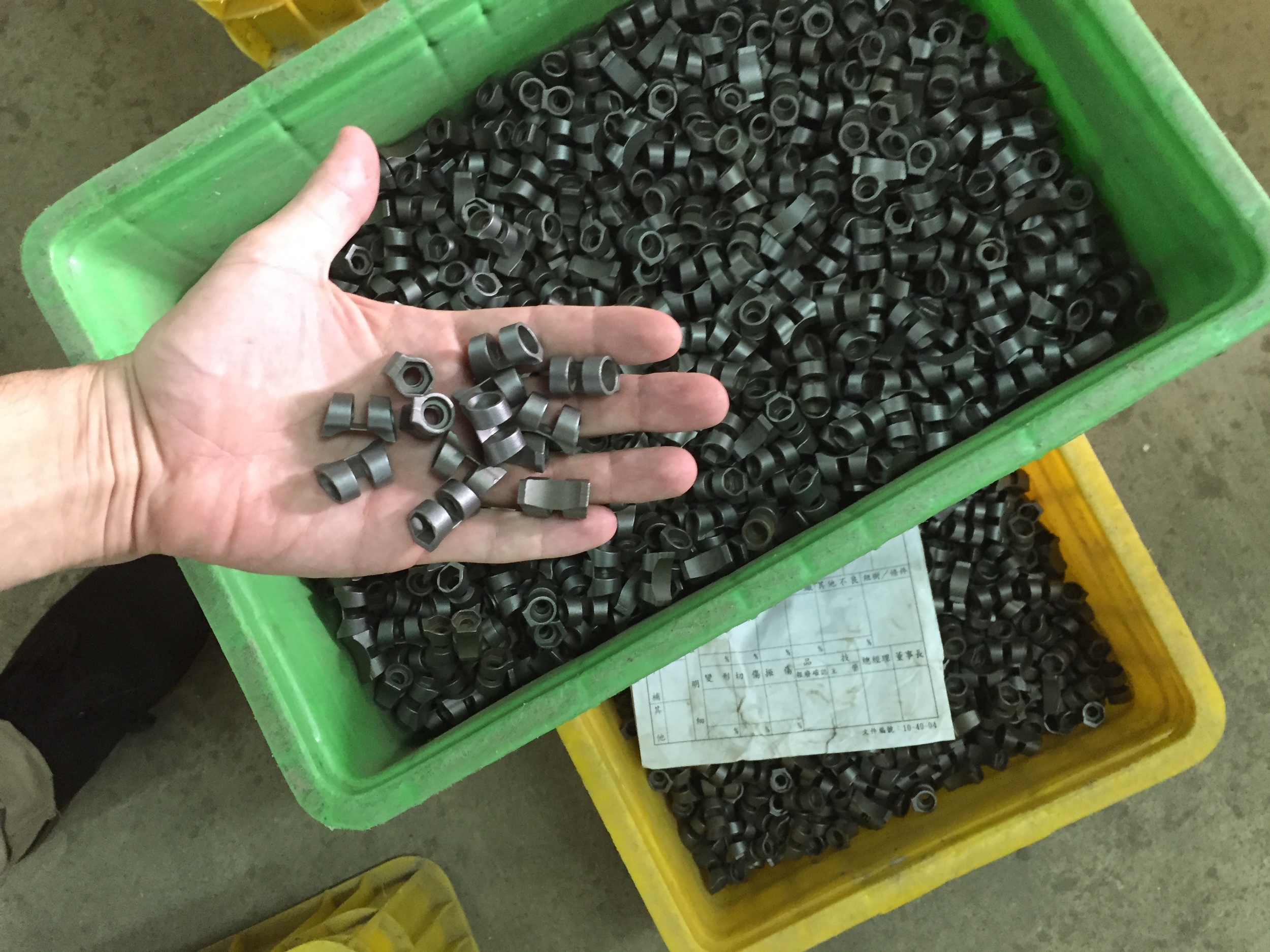
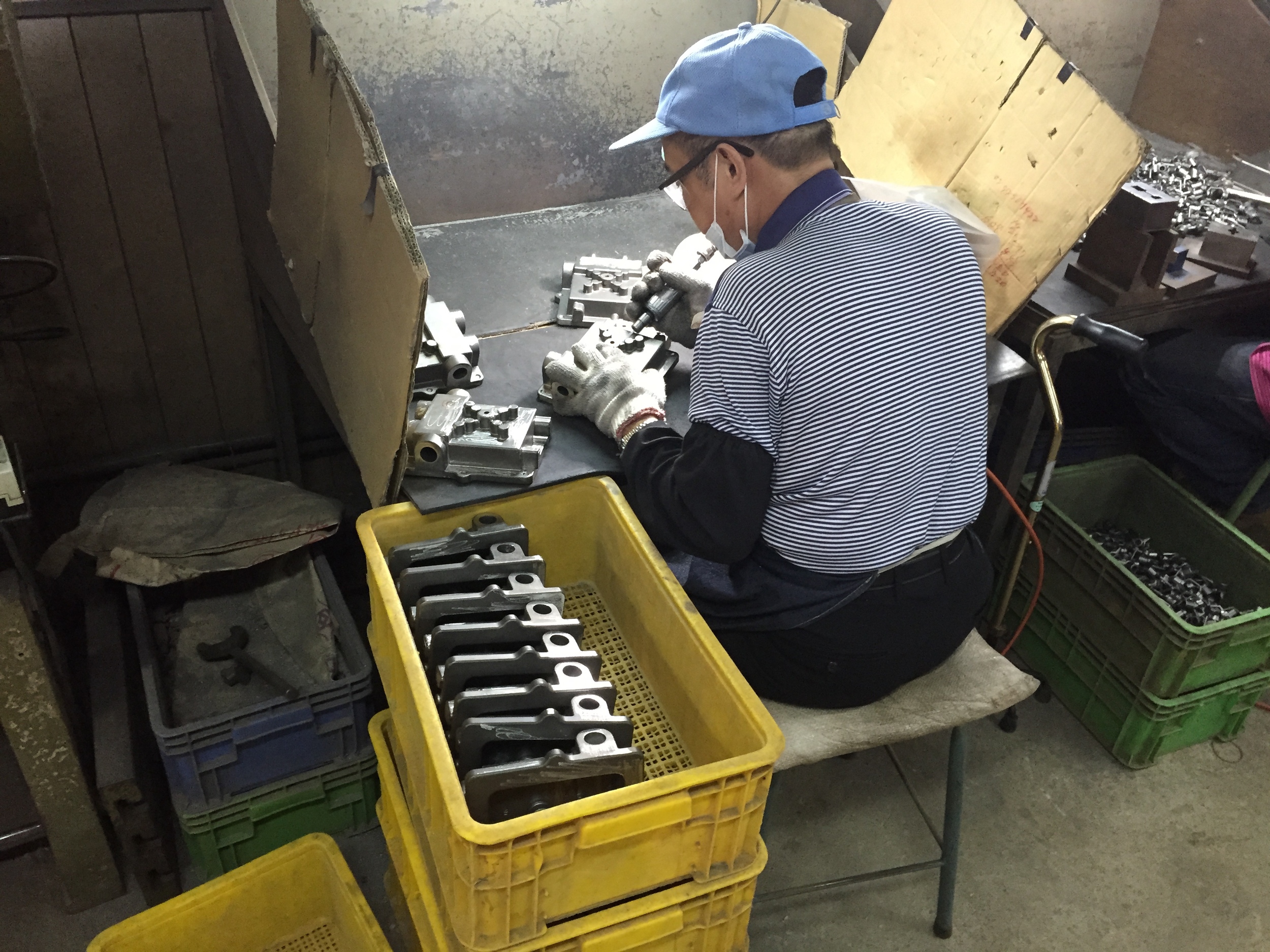
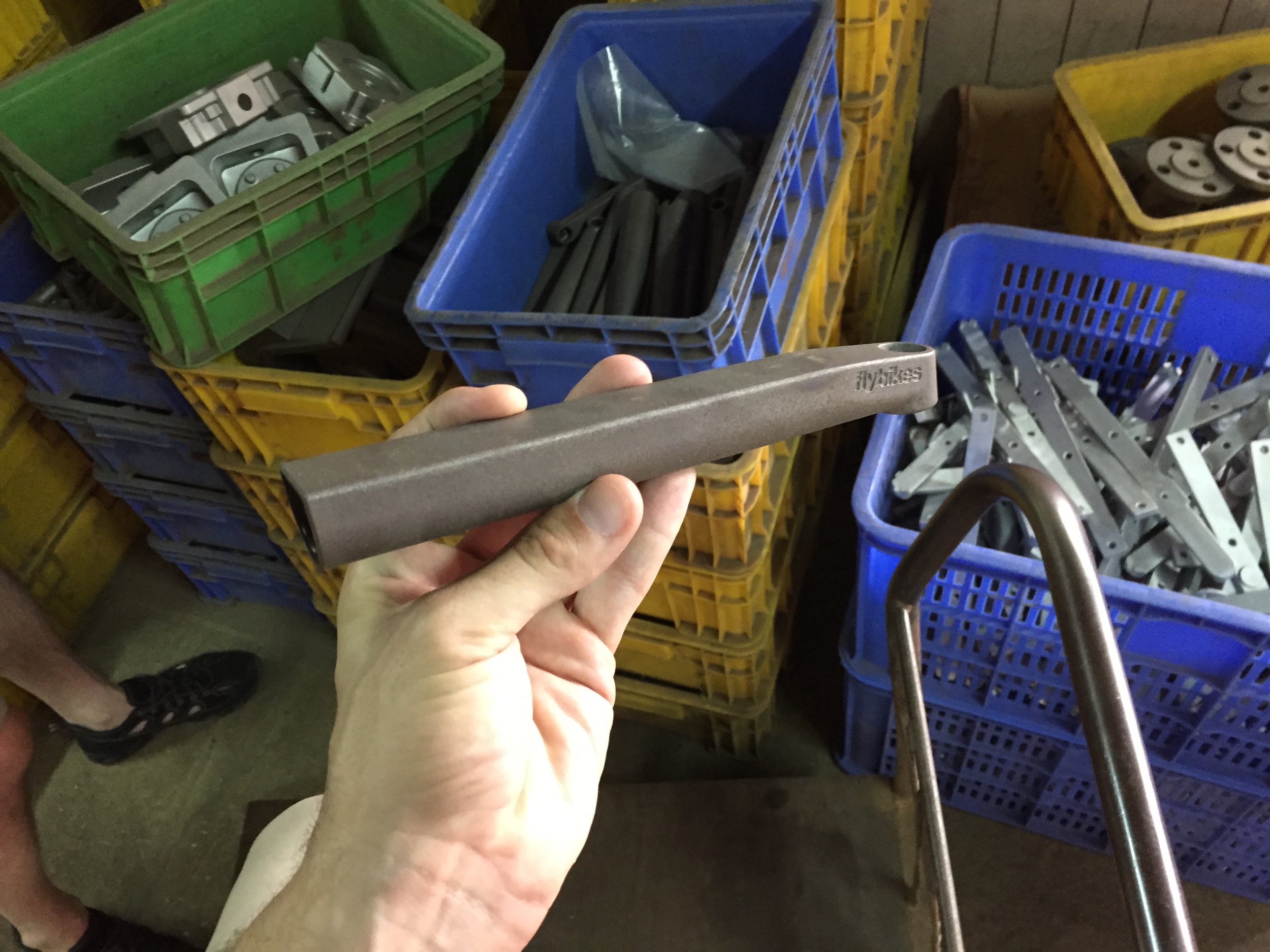
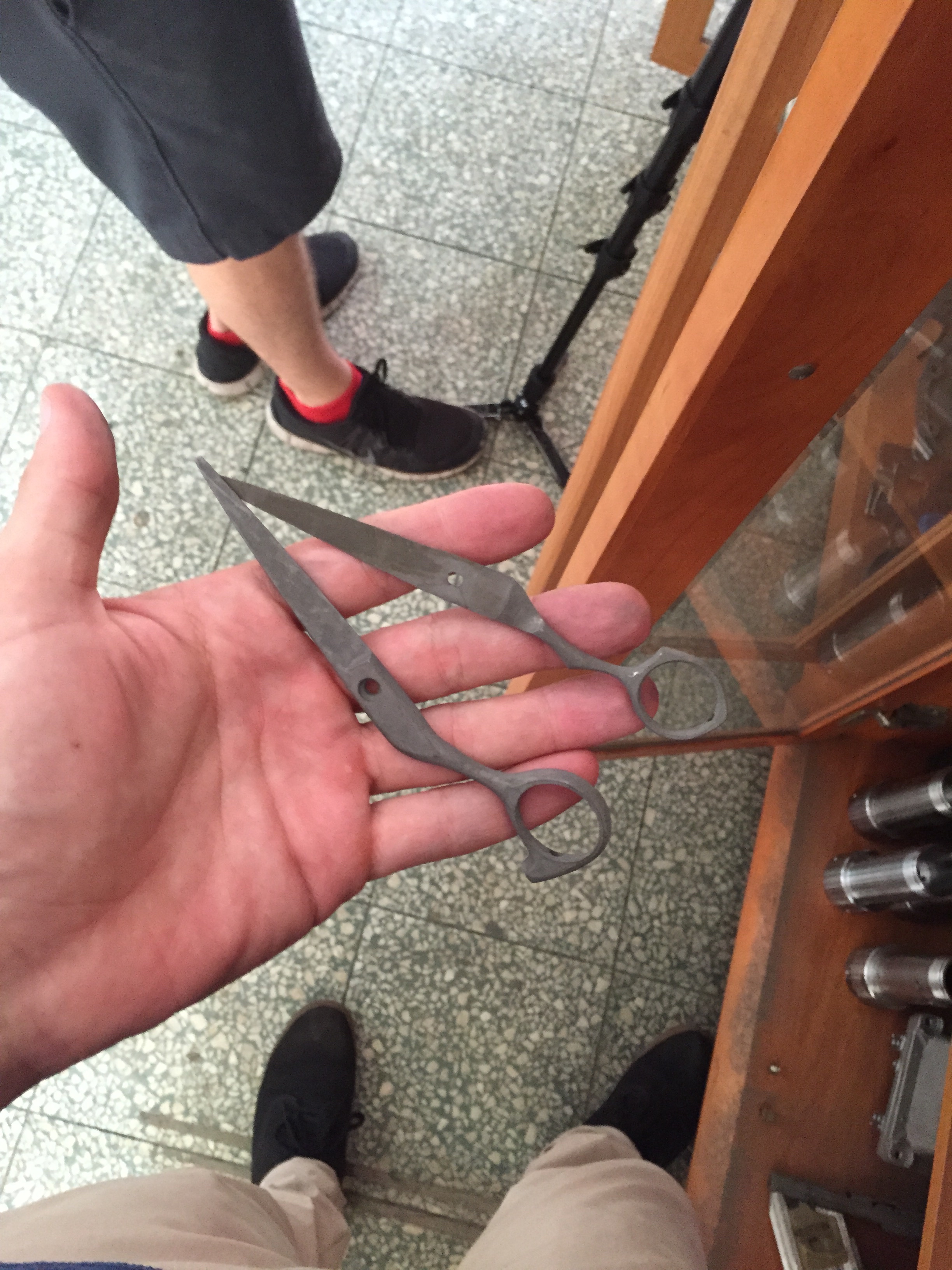
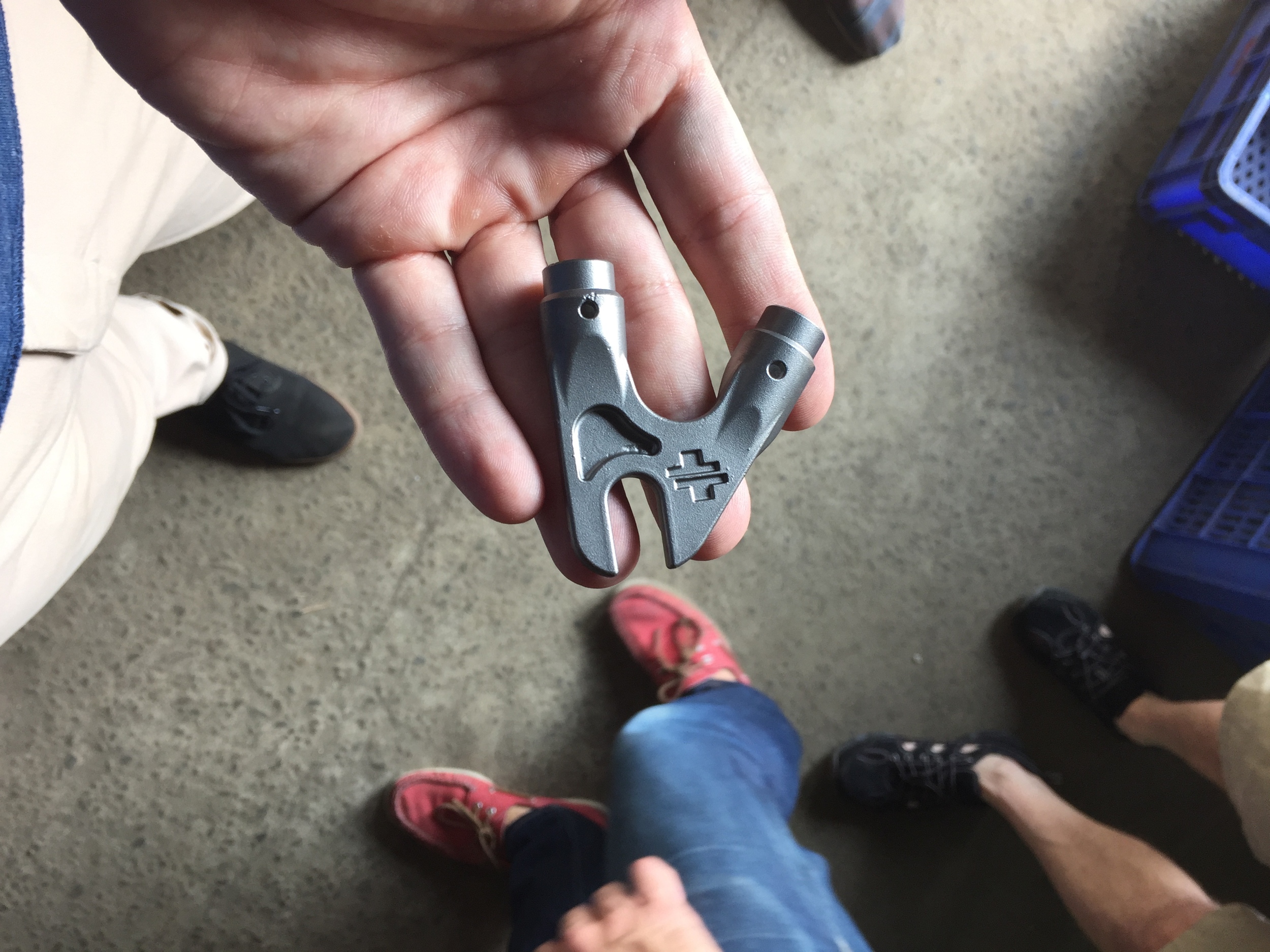
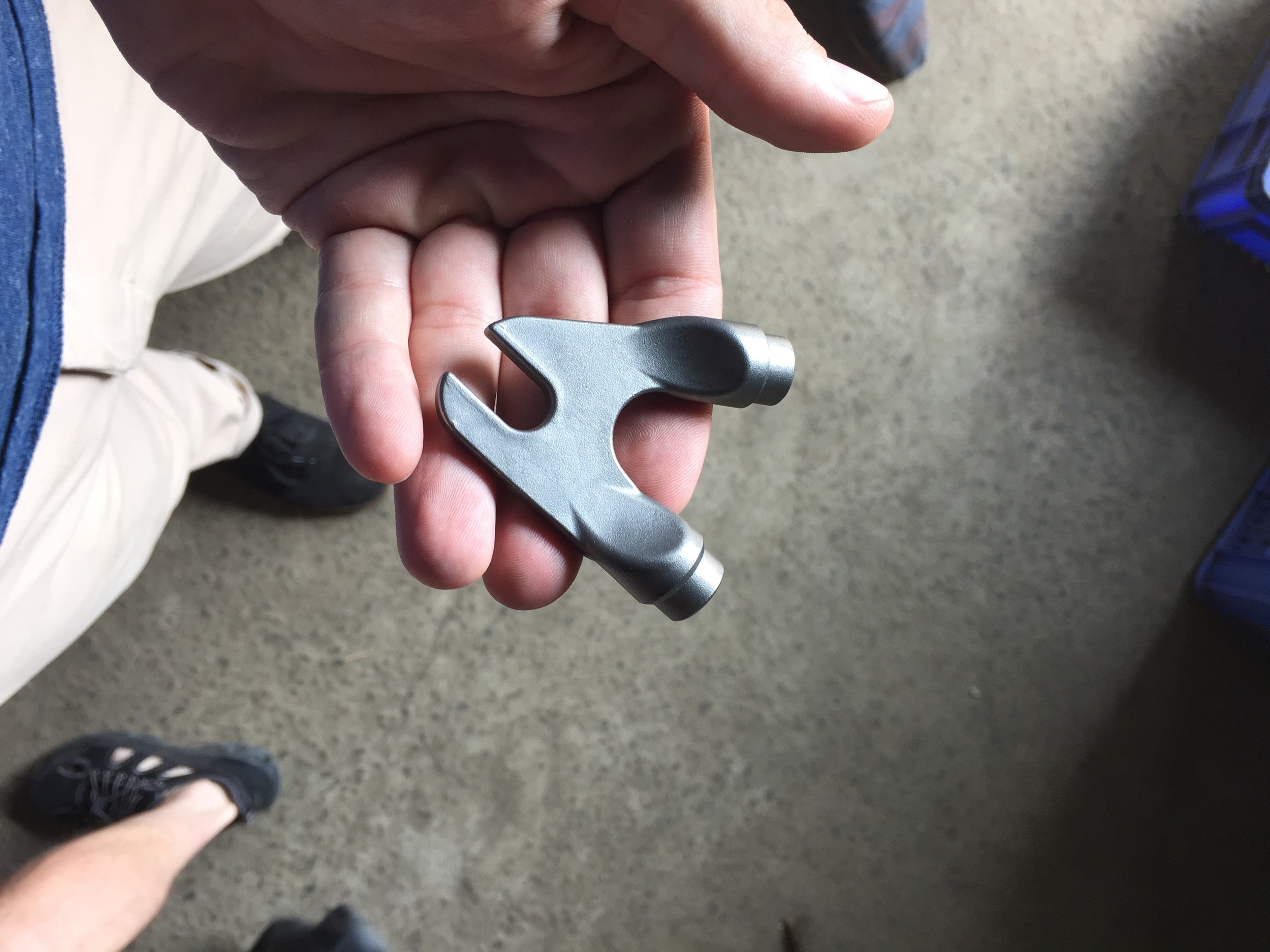
This factory was one of the coolest shops I've ever seen. Being able to see so many steps of the process coming together sequentially was really great. So many manufacturing processes happen in a distributed, disjointed manner; it was fun walking through this shop and seeing parts be transformed from wax to steel as we went.