In October, I visited a Taiwanese cardboard factory in Taiwan with Brilliant Bicycles. A few notes:
- Paper comes in, finished cardboard boxes go out.
- The paper rolls come in various shapes, sizes, and presumably thicknesses, but they're generally *huge* and brown.
- The whole place, but especially the sheet assembly line, was really loud - one of the loudest places I've ever been.
- There are three big portions of the factory: the sheet assembly area, the box printing & slotting area, and *lot* of cardboard sheets stacked up around the factory.
- The sheet assembly area takes brown paper rolls, each of which weigh upwards of a ton, and transform them into cardboard sheets. The machine that does this is huge - probably 20 feet wide and maybe 200 feet long. The cardboard we saw getting made was 5-ply, which has three flat sheets (the two faces and one in the middle; think the slices of bread in a club sandwich) and two corrugated sheets (think the bacon, turkey, etc in the same sandwich). Presumably the exact specifications of the corrugation (e.g. its thickness) affect the structural properties of the cardboard; I think the sheets we saw getting made had thicker corrugations (maybe for the inside of the box) on one side and thinner on the other. Anyway, the sheet assembly machine takes five big rolls of paper and spools them out together, corrugating them as necessary and applying adhesive between the sheets. Then it applies pressure and feeds the whole continuous sheet through a pair of heated plates, which help cure the adhesive. Then it trims the sides off, slots the sheet in half lengthwise, and then chops each half into sheets of the appropriate size for what they're making.
- Then the sheets are stored in stacks around the shop. There were a *lot* of stacks of cardboard sheets - a large portion of the factory was just storage.
- The box printing and slotting section was a bit more disperse. There were a bunch of machines to perform these steps; some did one or the other, and some (including the one that Brilliant's boxes were made on) do both. The printing is done with big, colorful, silicone stamps. Most of these were presumably made out-of-house, but there were some (like the "no knives" and "fragile" stamps) which seemed to be standard and were being assembled onto clear plastic sheets (mylar?) by people in one area of the shop. We didn't see steel rule slotting dies being made (perhaps they were outsourced), but they were stored all over the shop. There were a bunch of varieties of those - some were used in manual die presses, and others were loaded into slotting machines and then operated automatically.
- A bunch of work was put into aligning the stamp and dies in the machine. If I were to guess, I'd say 5-10 sample parts were made before the alignment came out right.
- Once the alignment was right, the boxes came out really quickly. We were only having a few hundred boxes made; I'd guess they'd be done within a few hours.
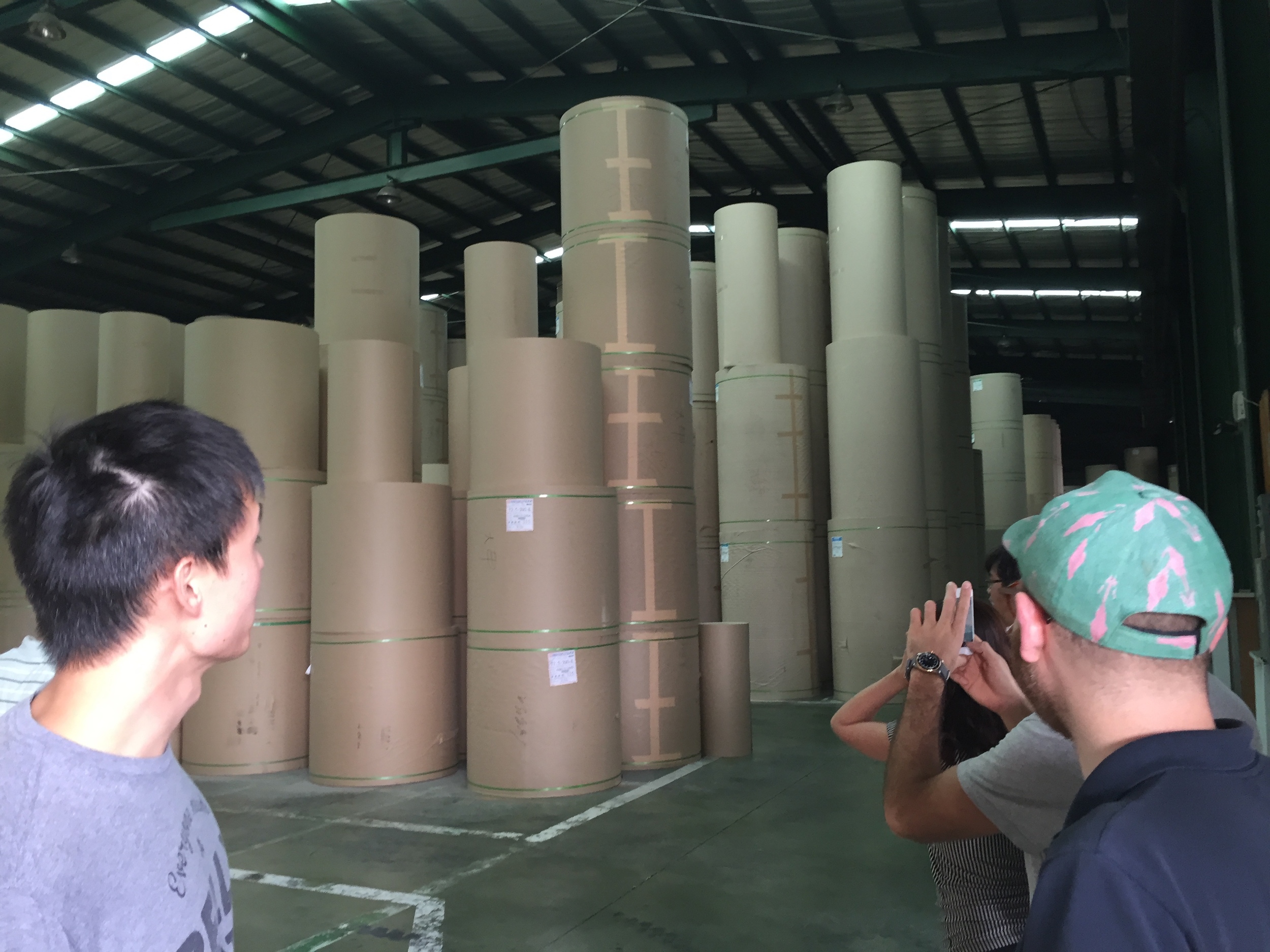

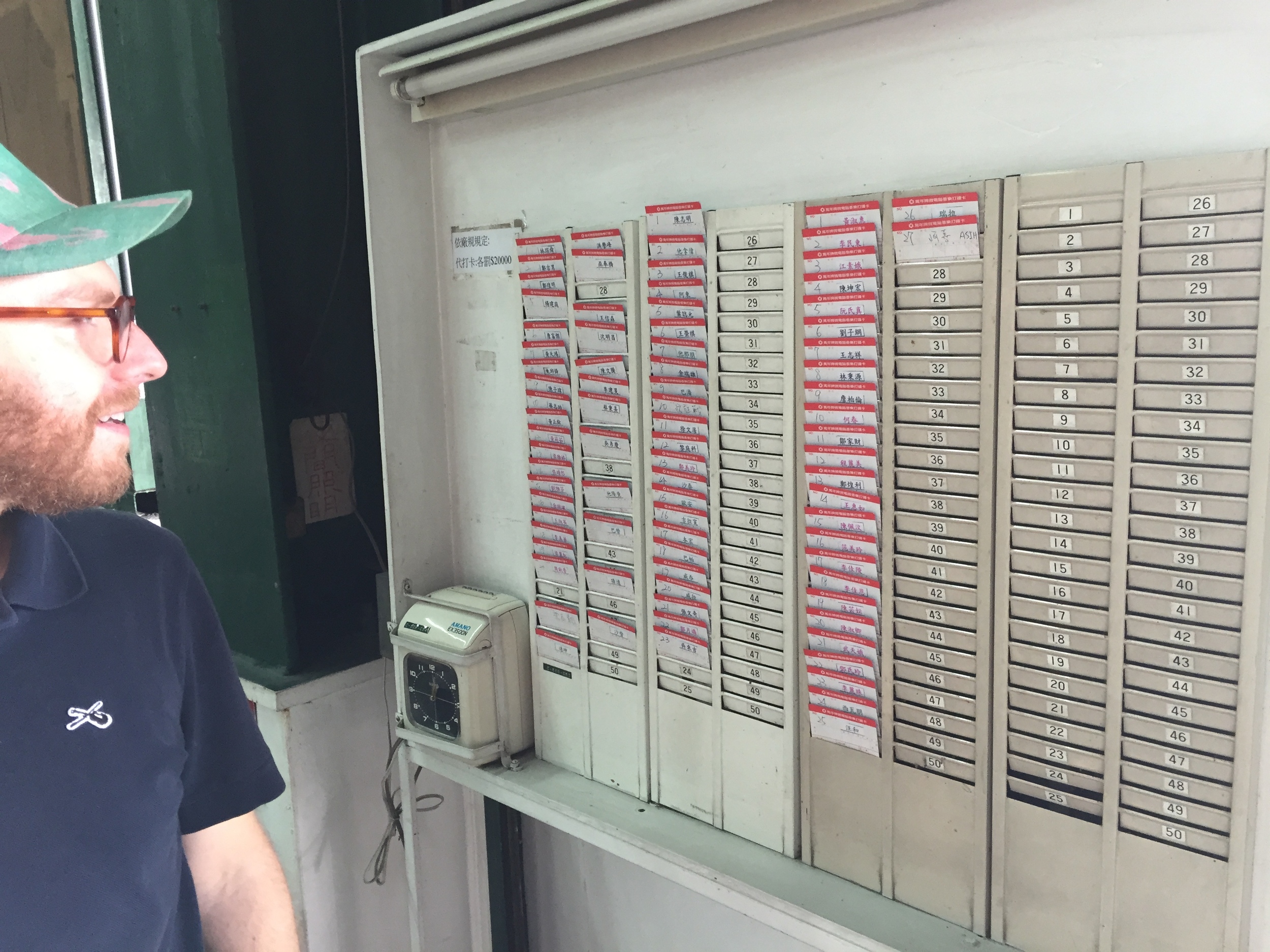
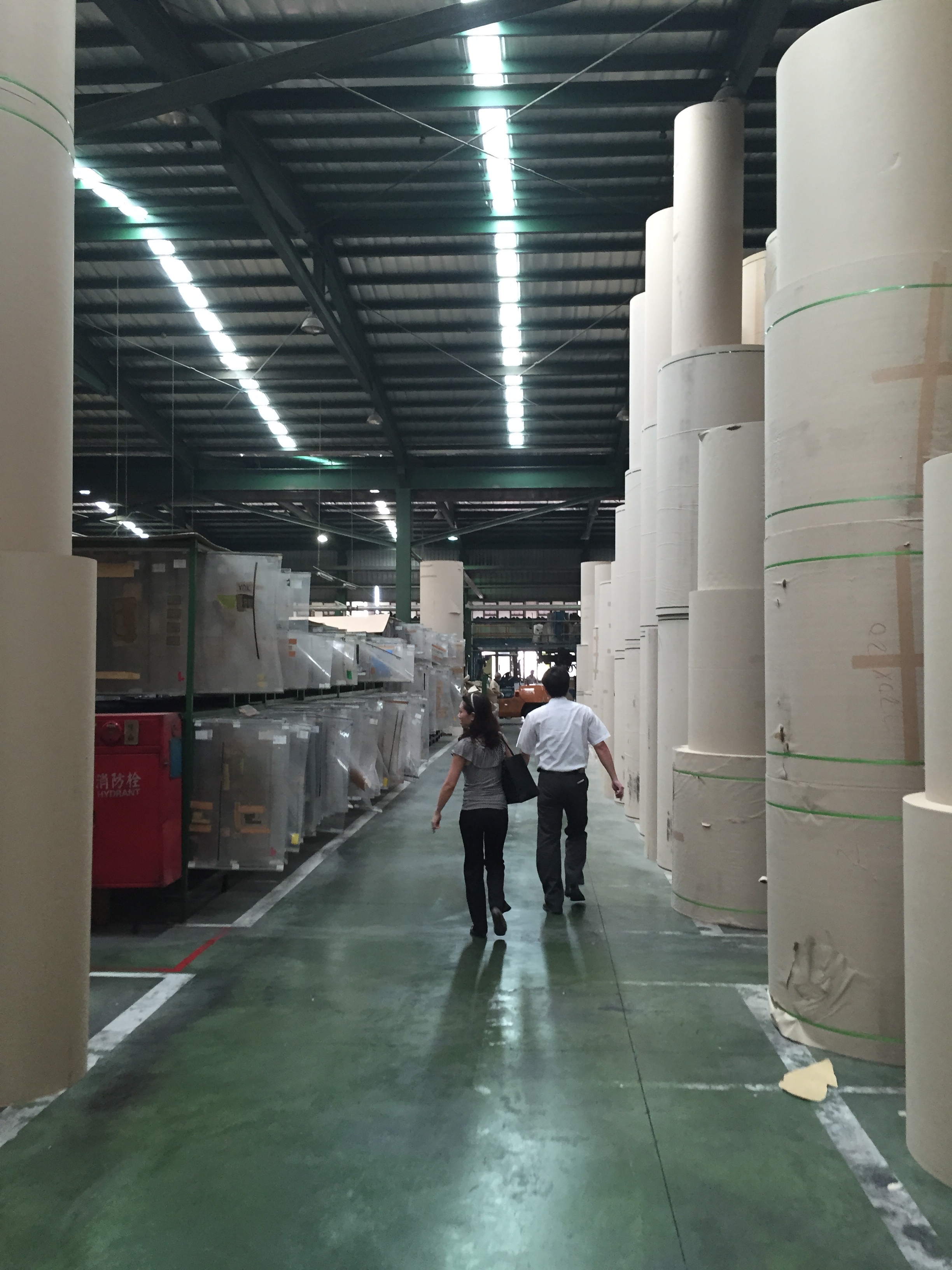
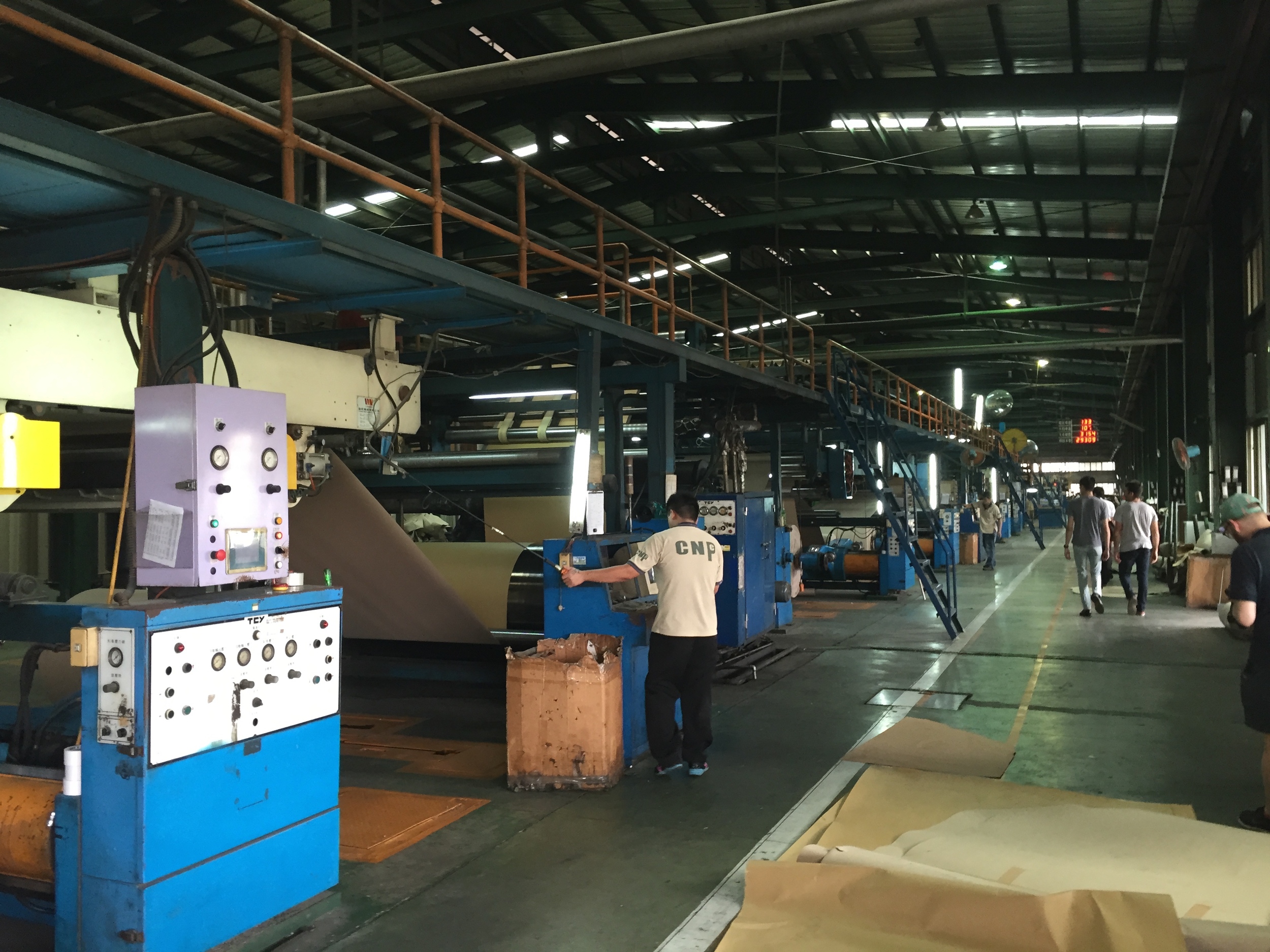
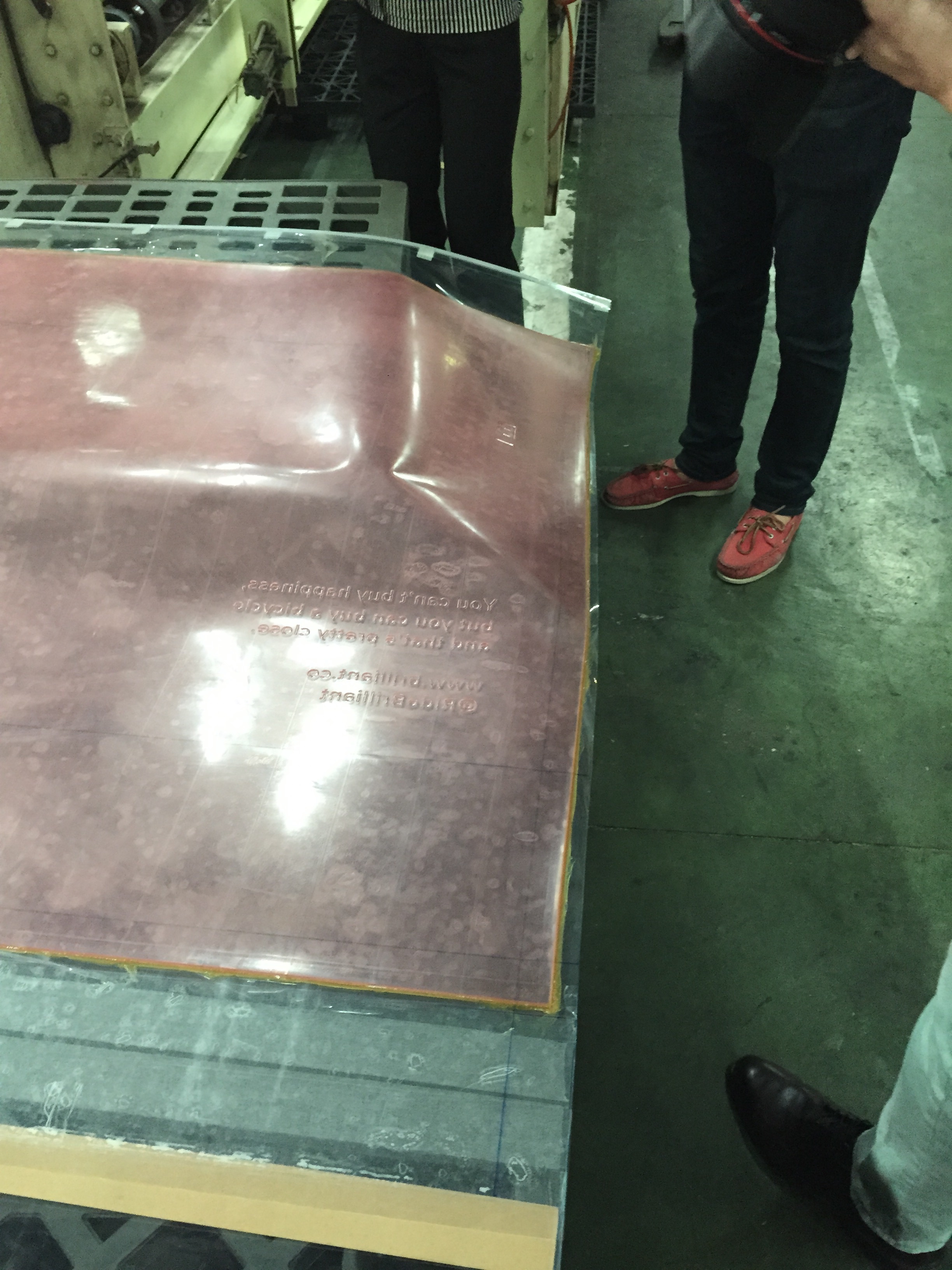
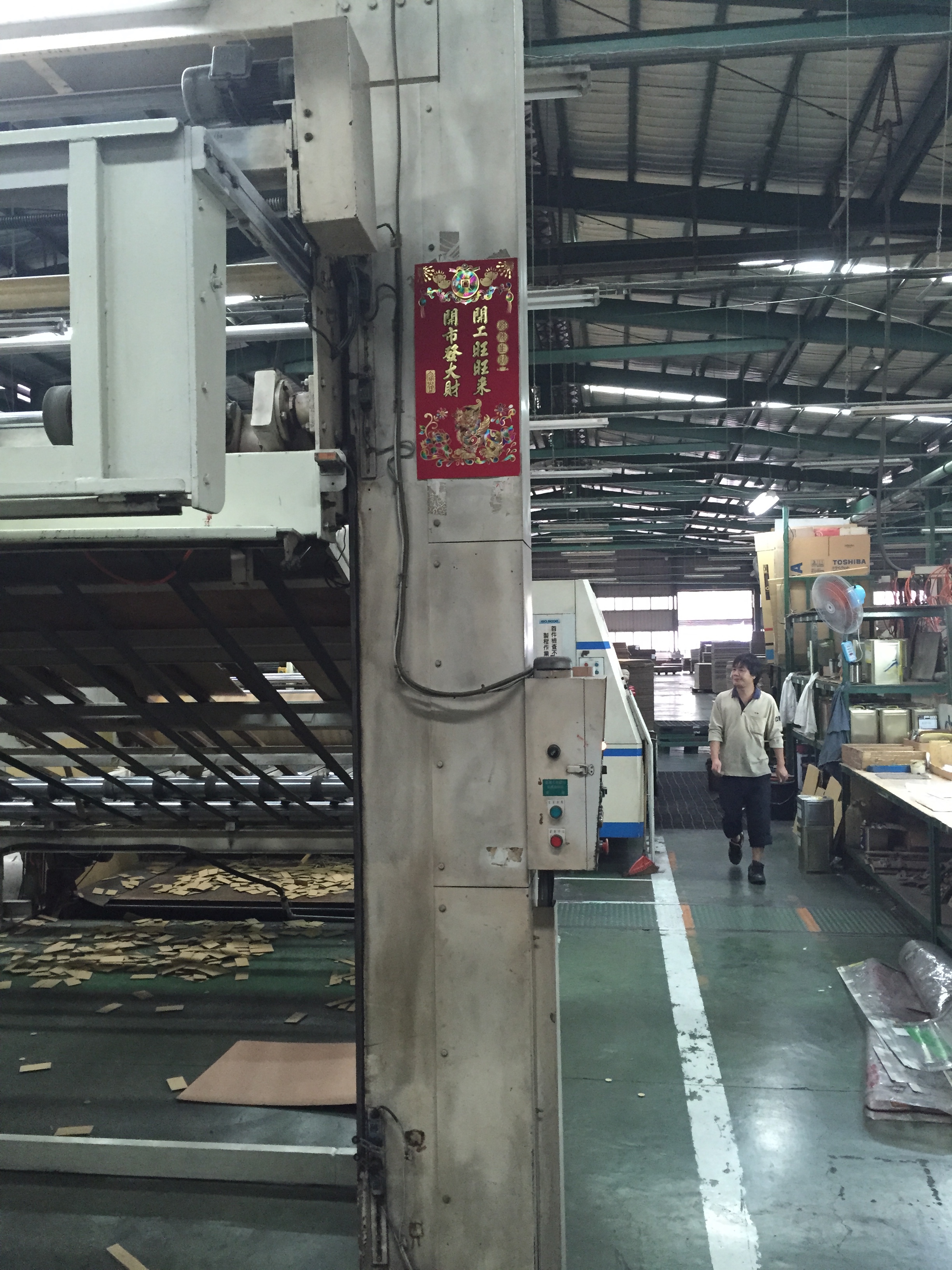
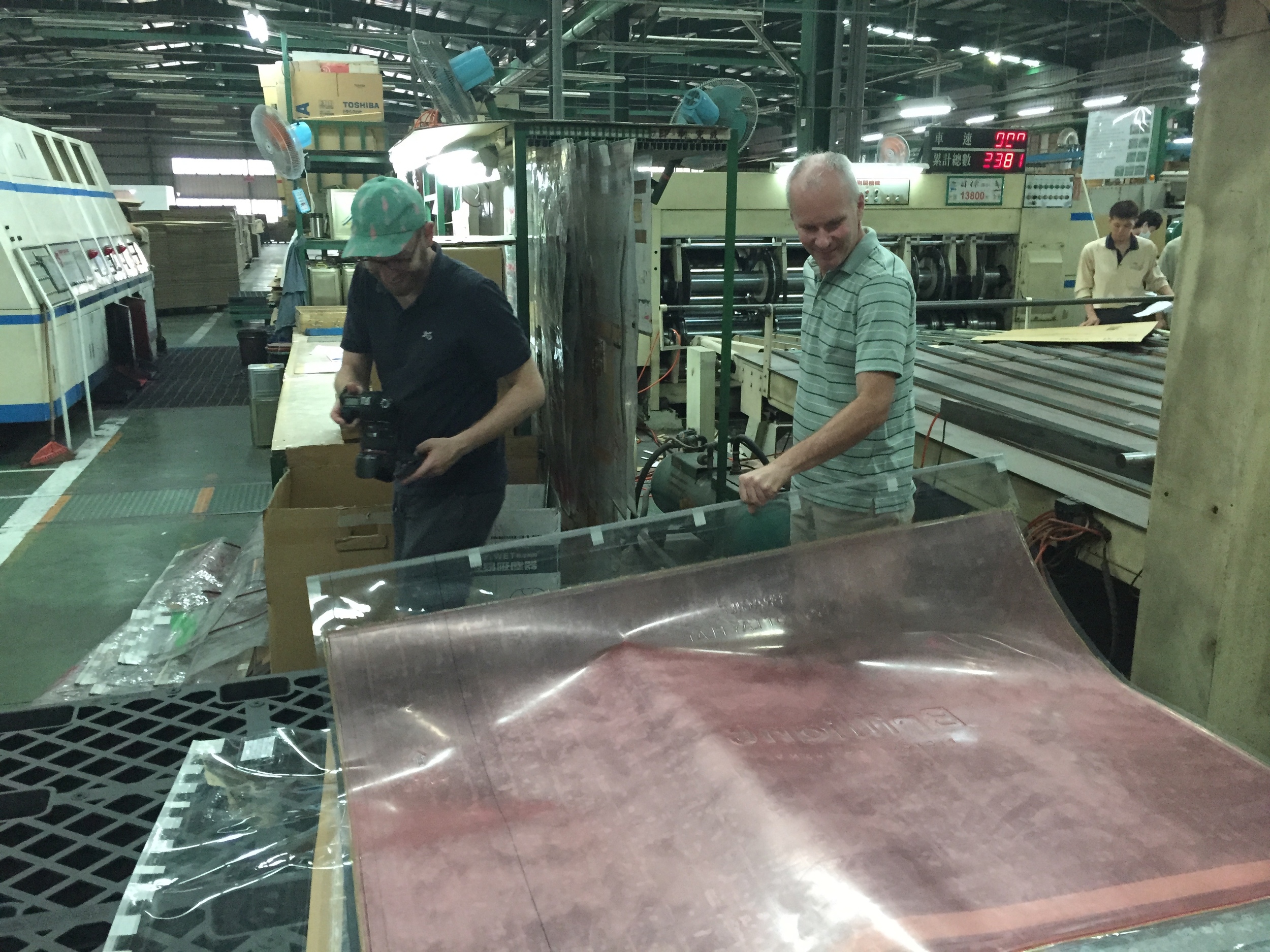
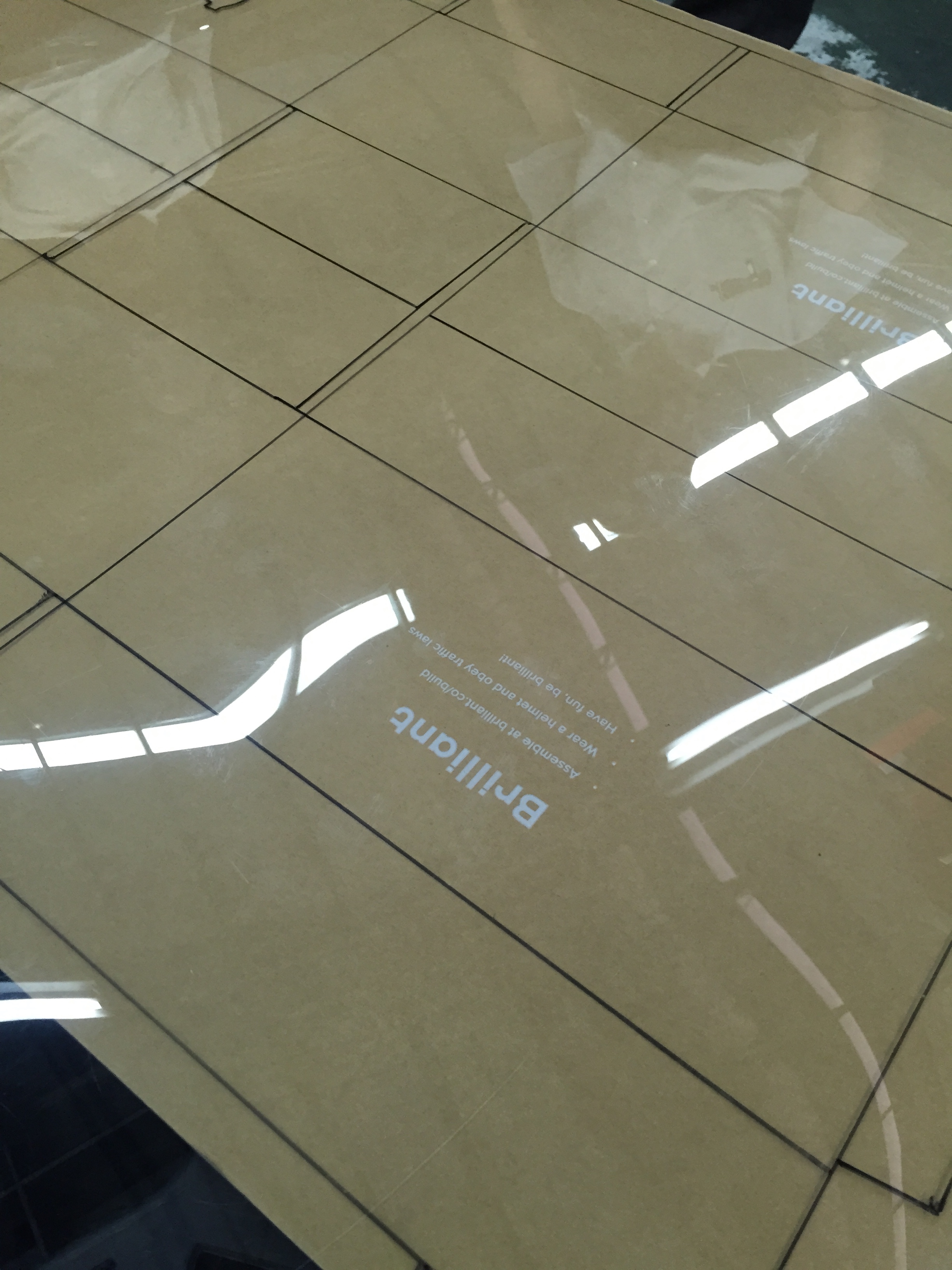
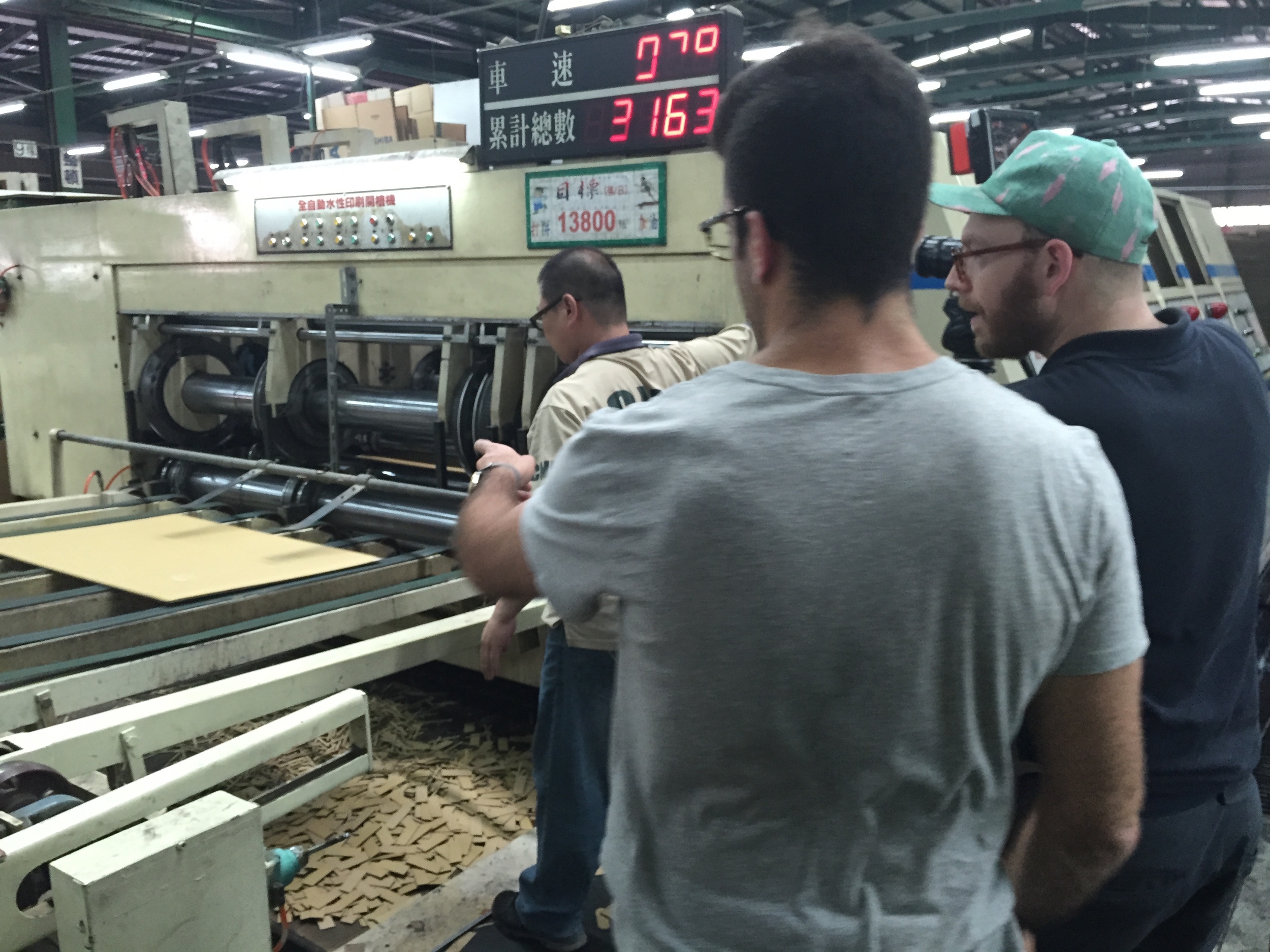
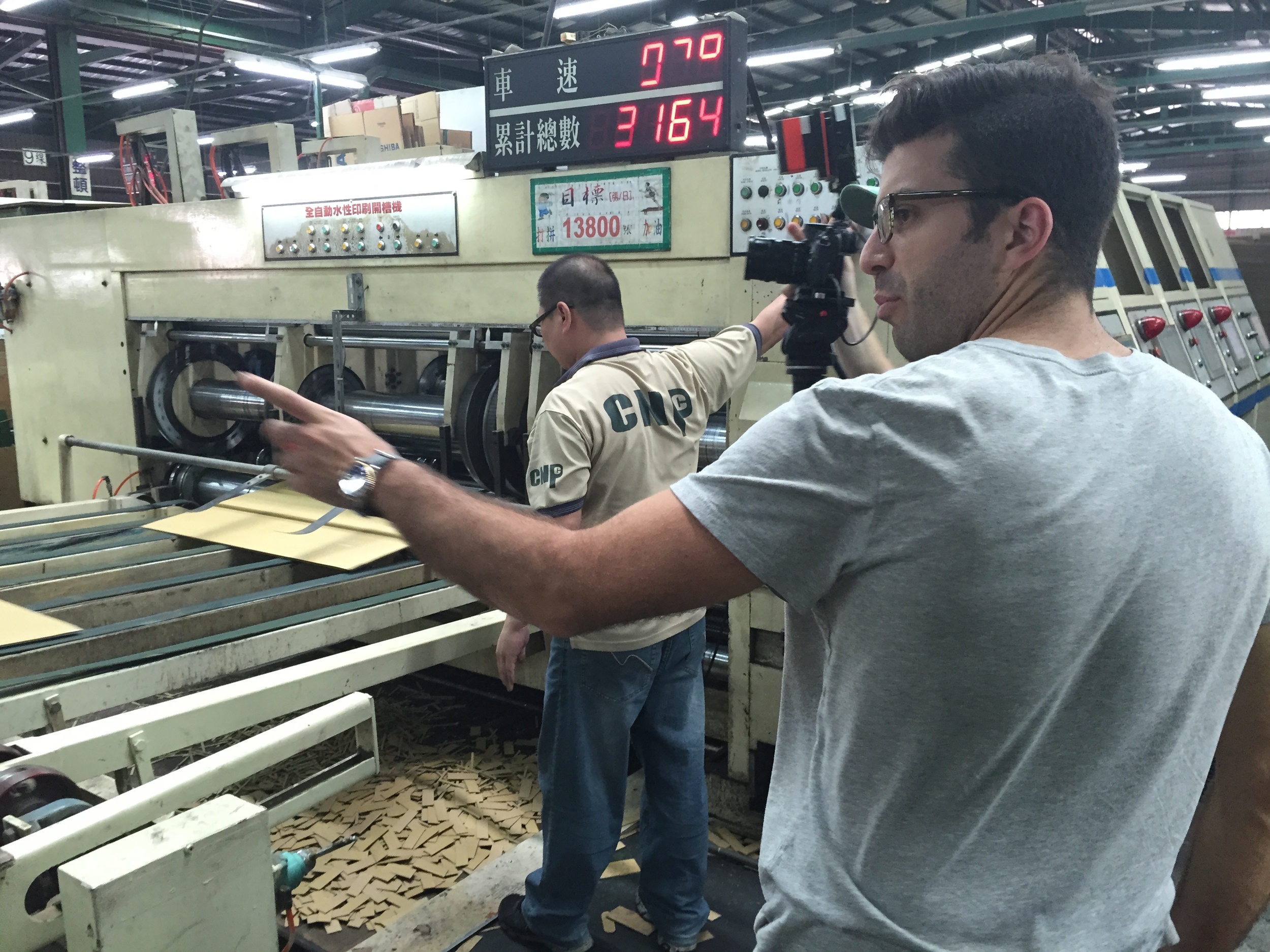
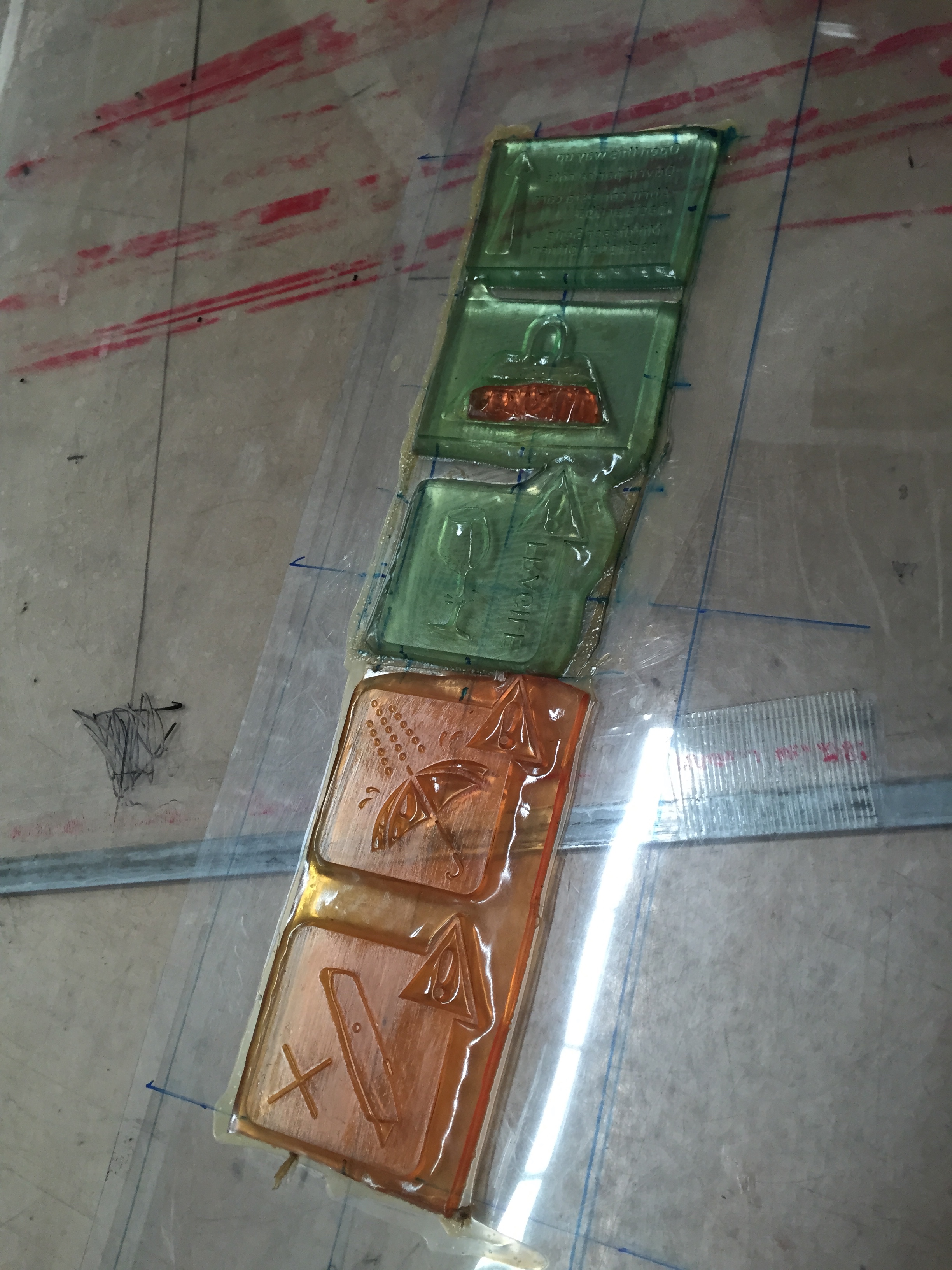
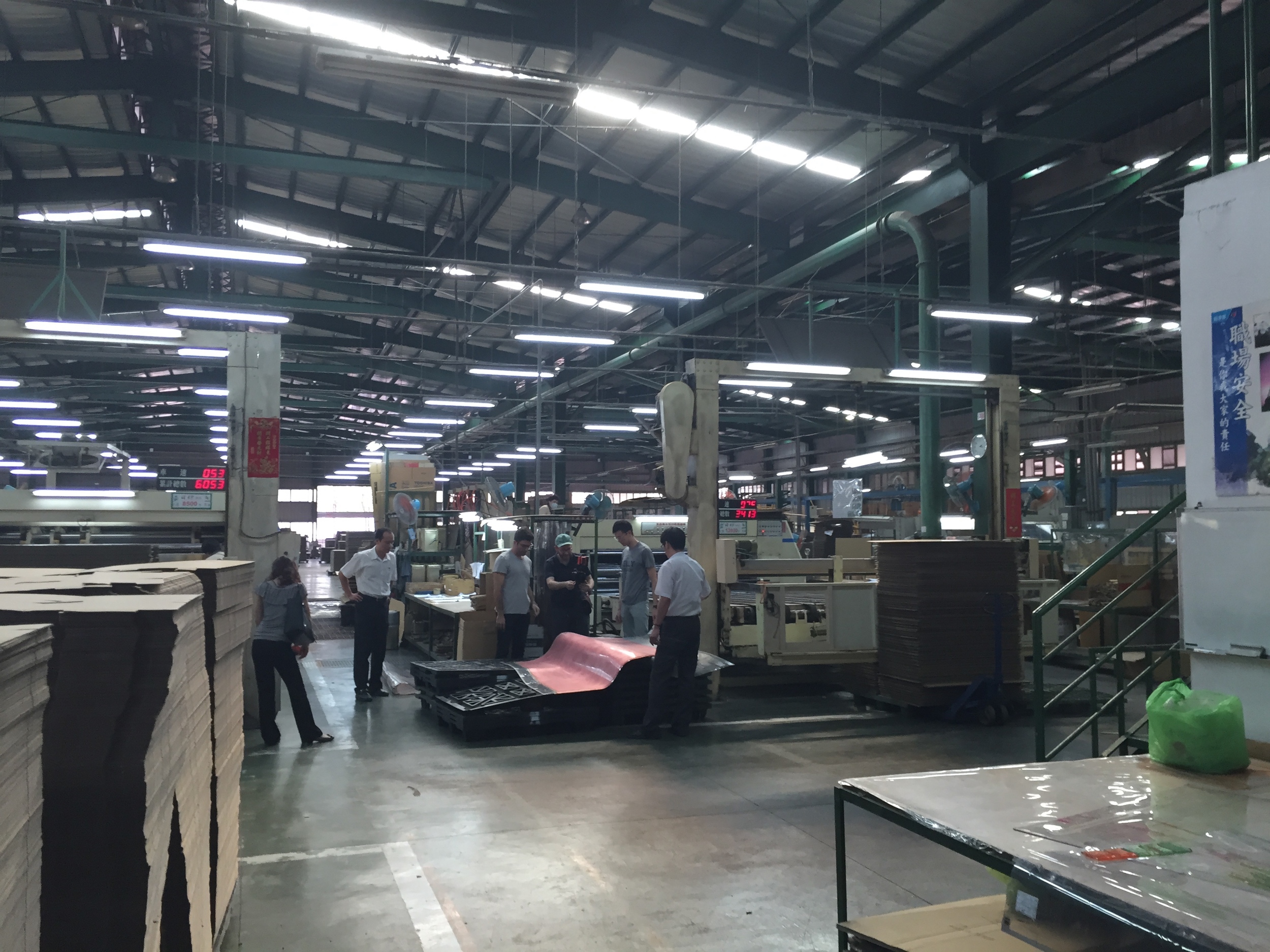
The place was huge - one of the single biggest unobstructed spaces I've ever been in:
The cardboard printing & slotting machine was really cool. There's nothing like a black box that takes raw material in and spits out a useable object on the other side:
Seeing general purpose manufacturing is always a lot of fun. Cardboard boxes are used *everywhere.* Having seen how they're made gives valuable perspective on something that's on basically any BOM.