UPDATE: As of 2024-05-17, I’m selling my restored and upgraded drill press. If you’d be a good parent for it, and can pick it up in NYC before the end of the month, shoot me a note here.
Late last summer I took on what at the time seemed like a reasonable project: Restoring an old (1940s) Walker-Turner 15” drill press. I had acquired it for an attractive price (free) but it had a number of issues, including:
A pretty bad repaint job, on top of a pretty old original paint job, resulting in paint chips everywhere
A missing belt guard, which I was able to replace with an unpainted (and cracked) belt guard
A step pulley drive system, which made for laborious speed changes & general annoyance
…and 80 years of general wear & tear
Nevertheless, it was a functional drill press and that’s infinitely better than no drill press at all. I got to work.
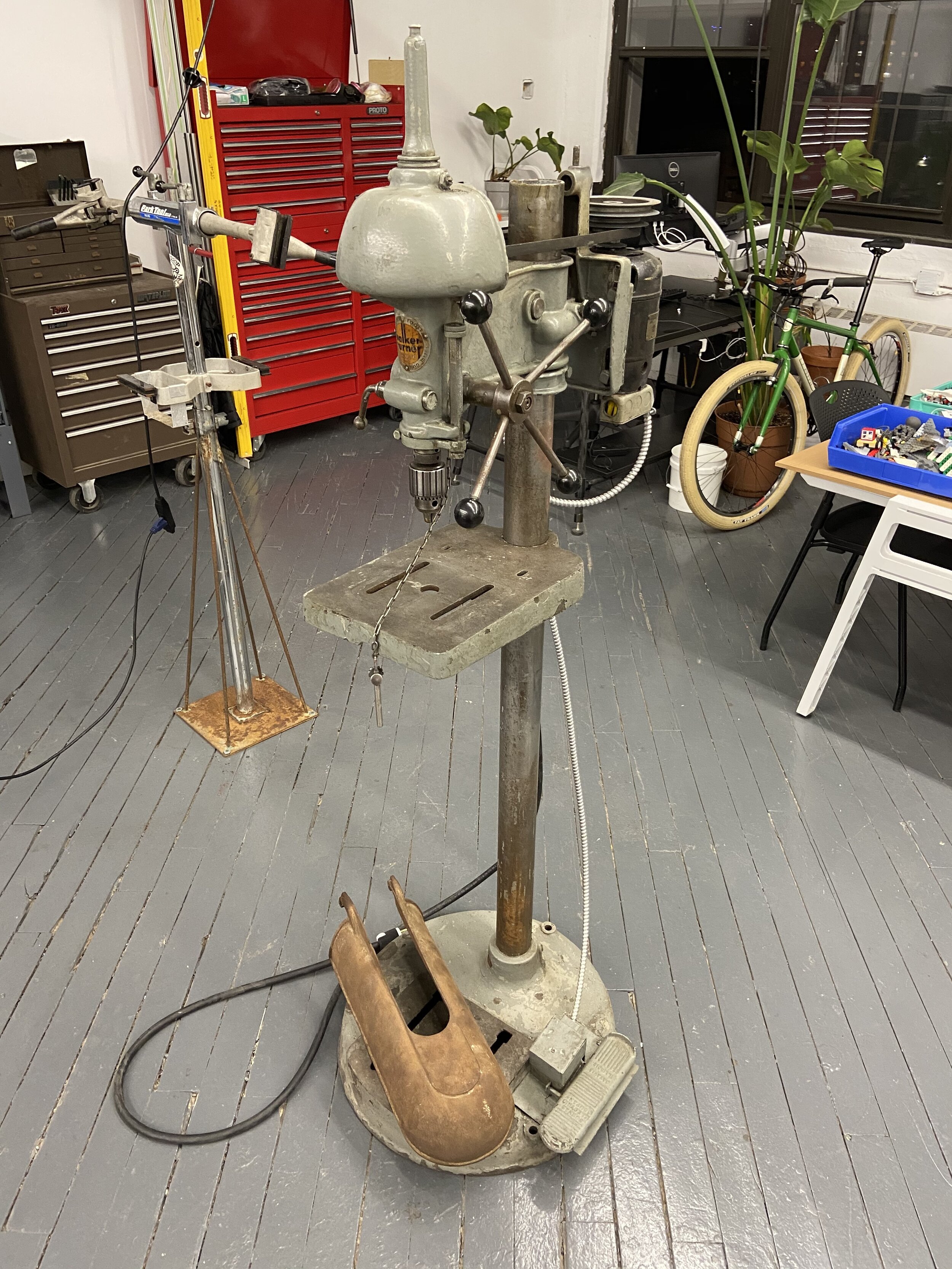
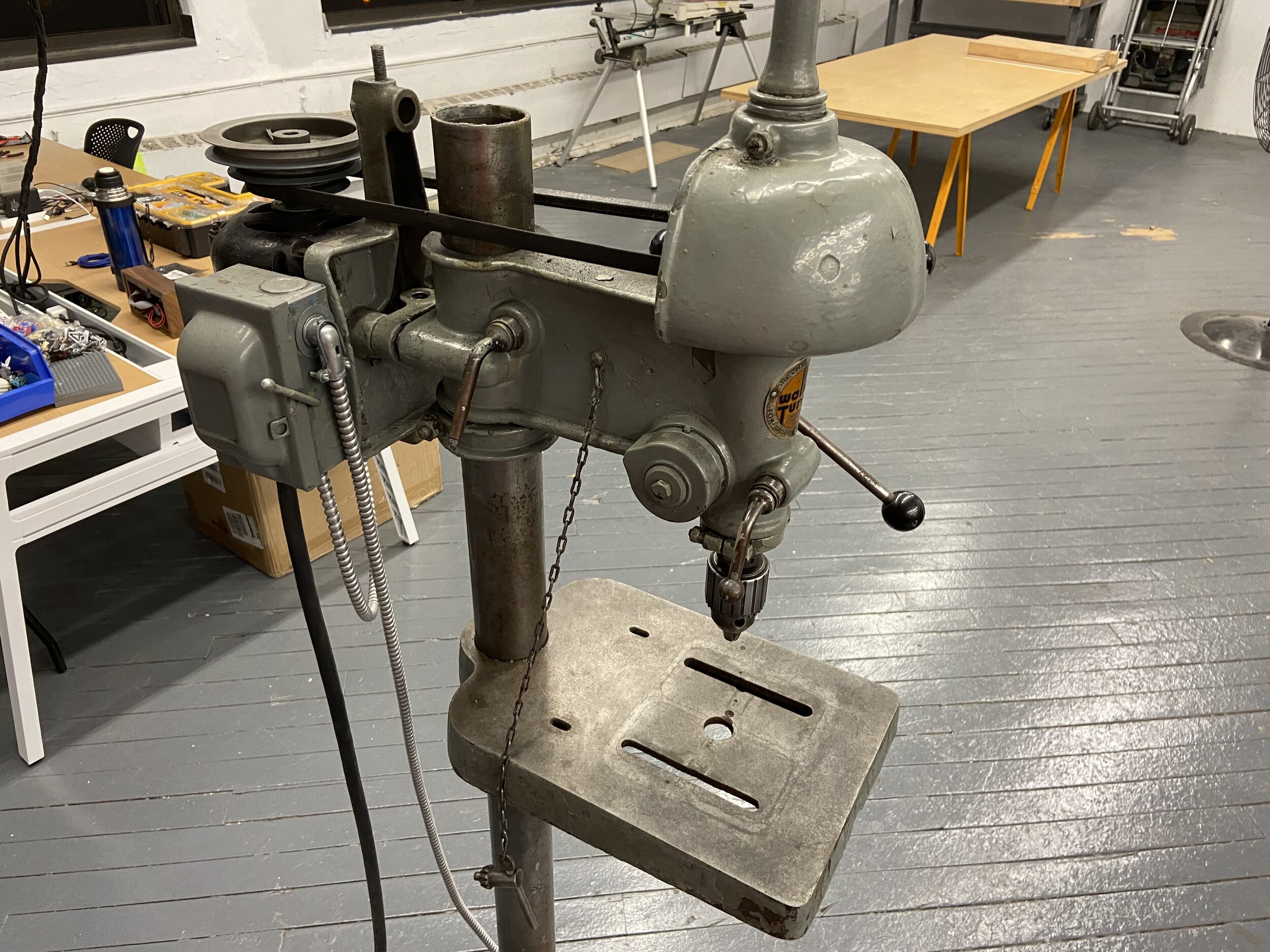
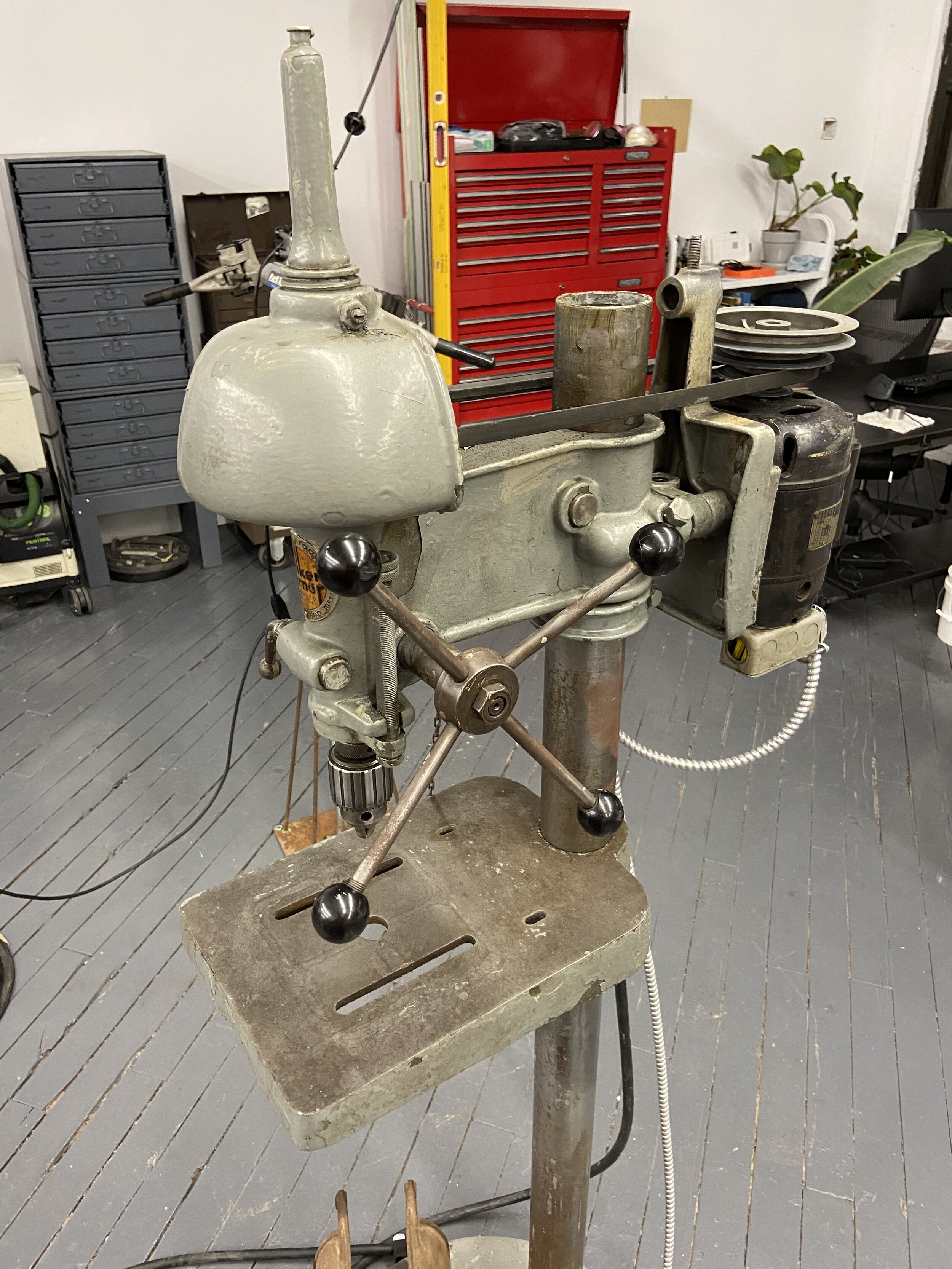
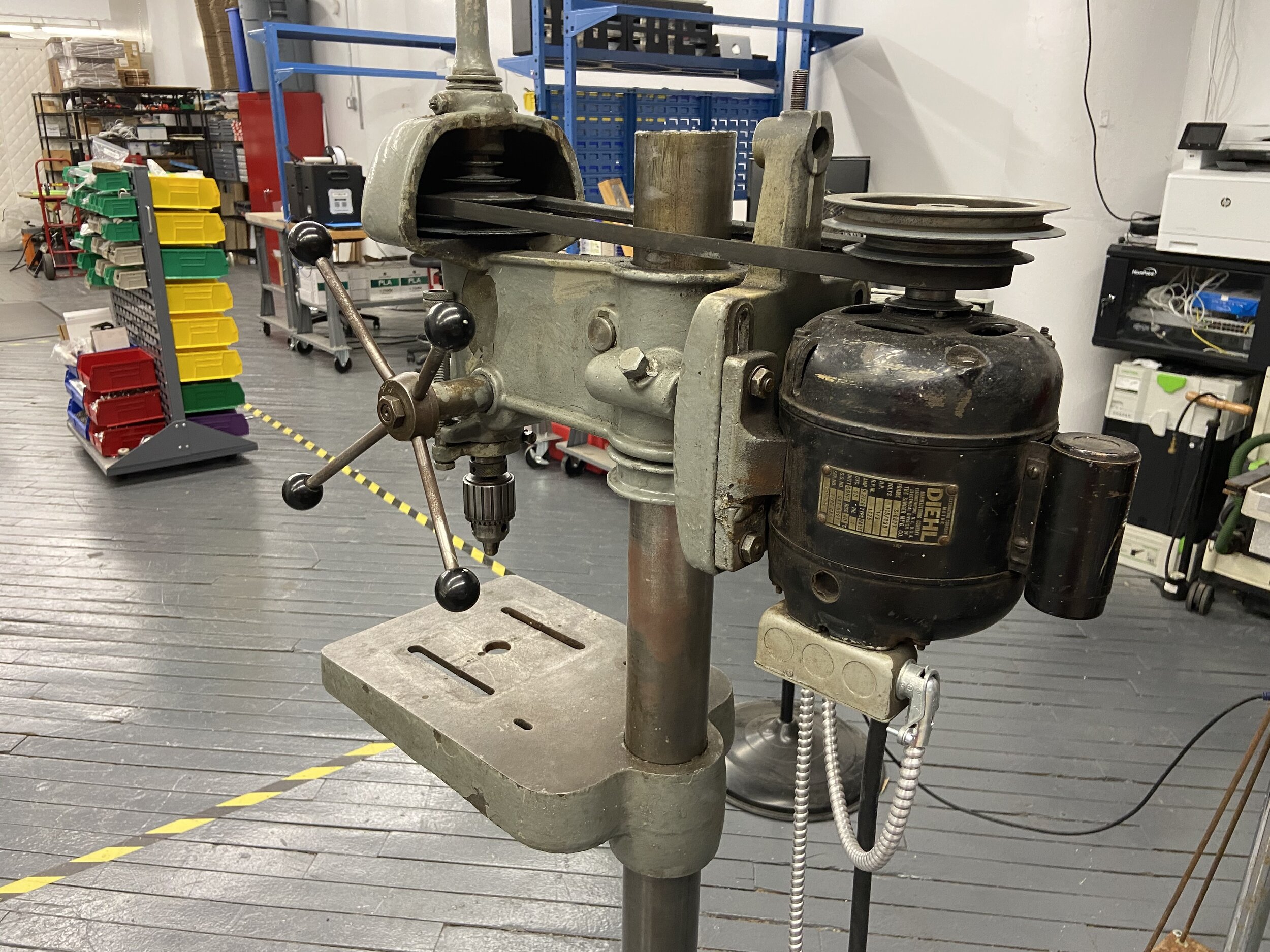
Few things are less fun than stripping paint, and this project had lots of paint to strip - from irregular and rough (cast iron) surfaces, no less. Much time was spent on this: First with scrapers, then with sandpaper, then with (ew) paint remover, Simple Green, and *lots* of time with stainless steel brushes. It was, to be honest, exhausting, and were it not for the fact that I had already announced the project on Instagram it may have destroyed my resolve. Perhaps the lowest moment was when I wheeled a bunch of these parts - a load weighing probably 150 lbs - to a friend’s shop a few blocks away to use his sandblaster. I spent a few hours there hunched over listening to podcasts, and then left with less than half of the parts in a paintable state.
Defeated, I turned to aircraft paint remover - a deeply disappointing surrender, and one with its own set of challenges. Paint remover is no more foolproof - and much more toxic - than mechanical means of removing paint. I used it years ago once, and did not enjoy the experience.
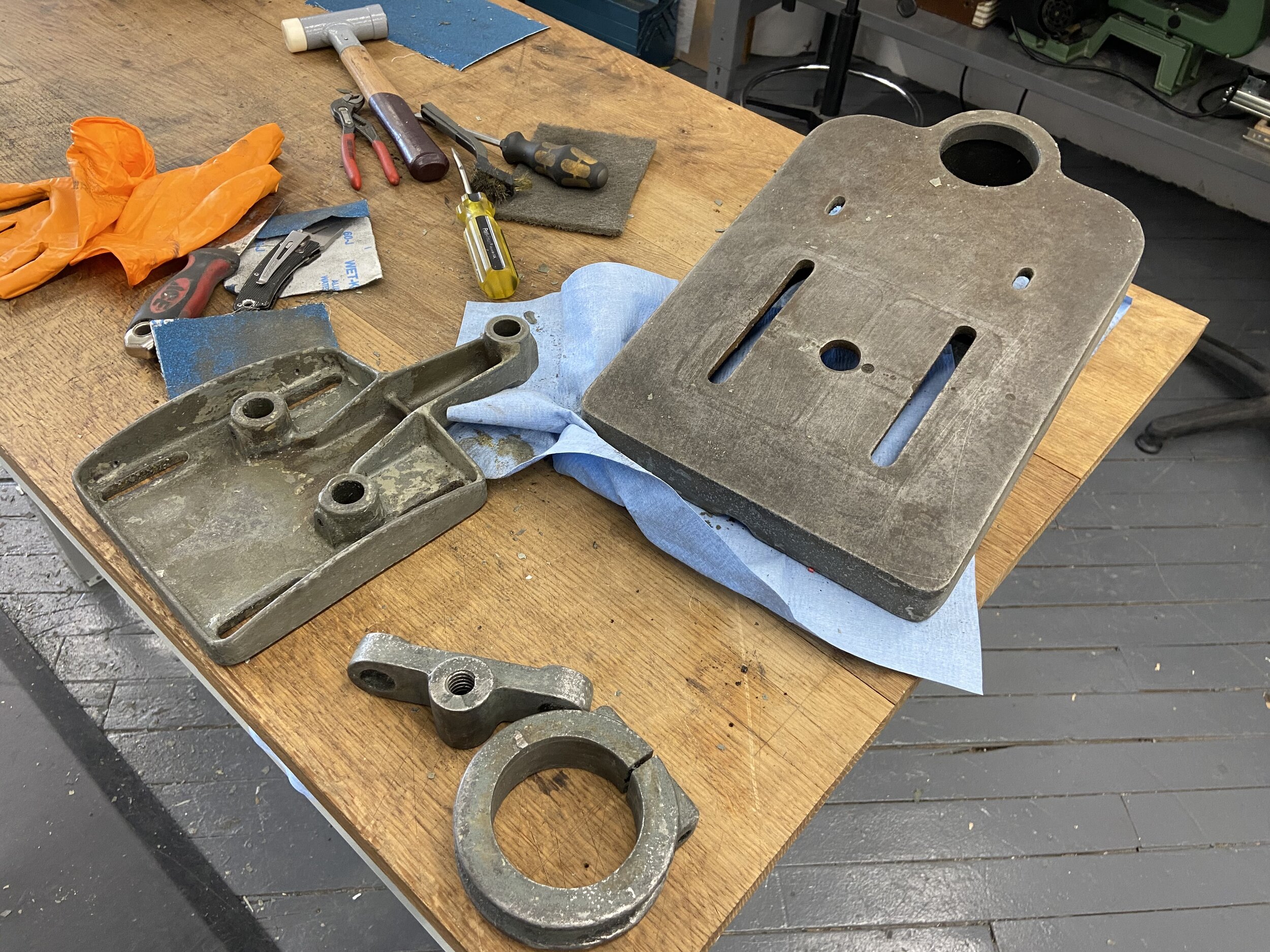
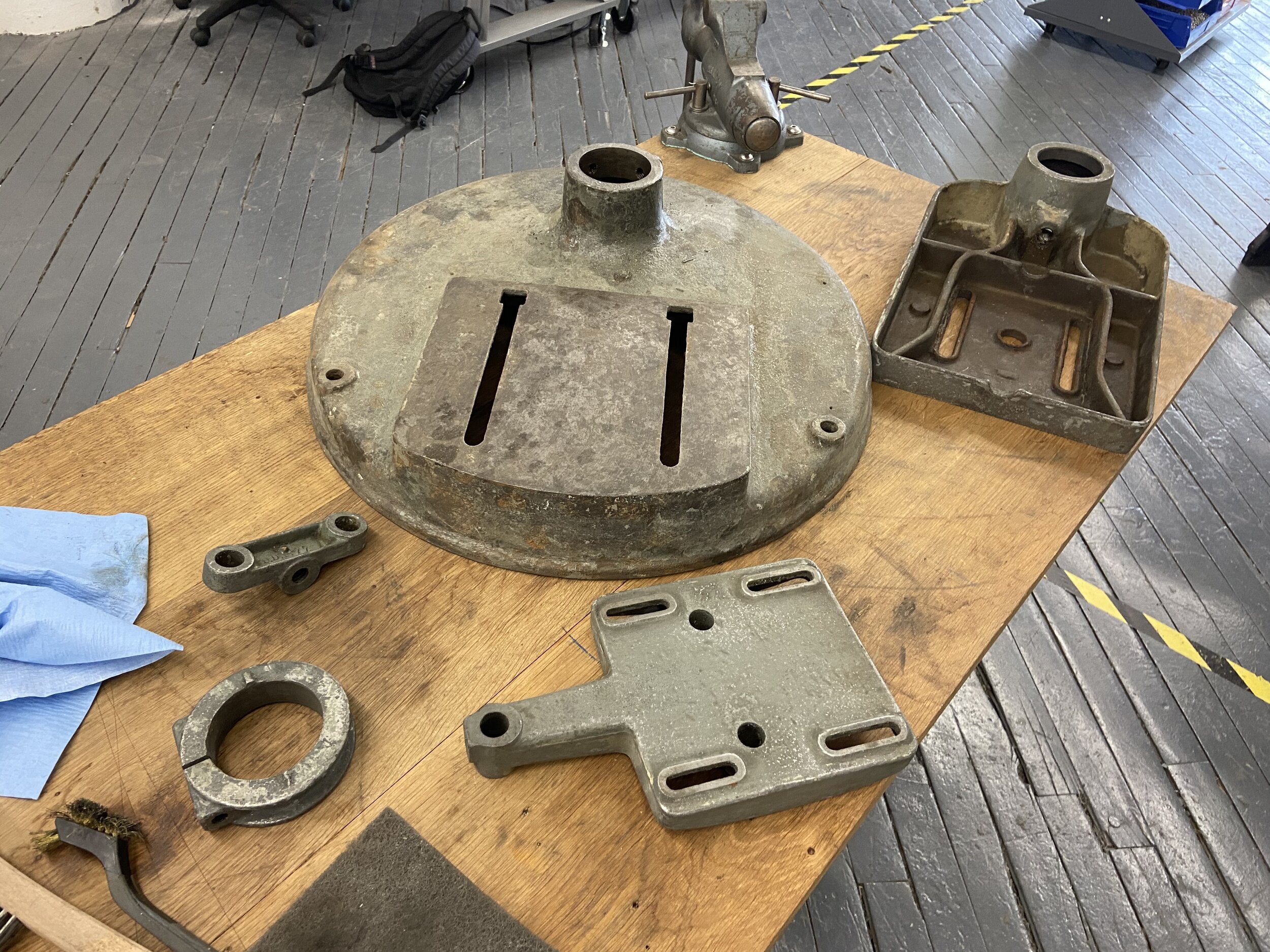
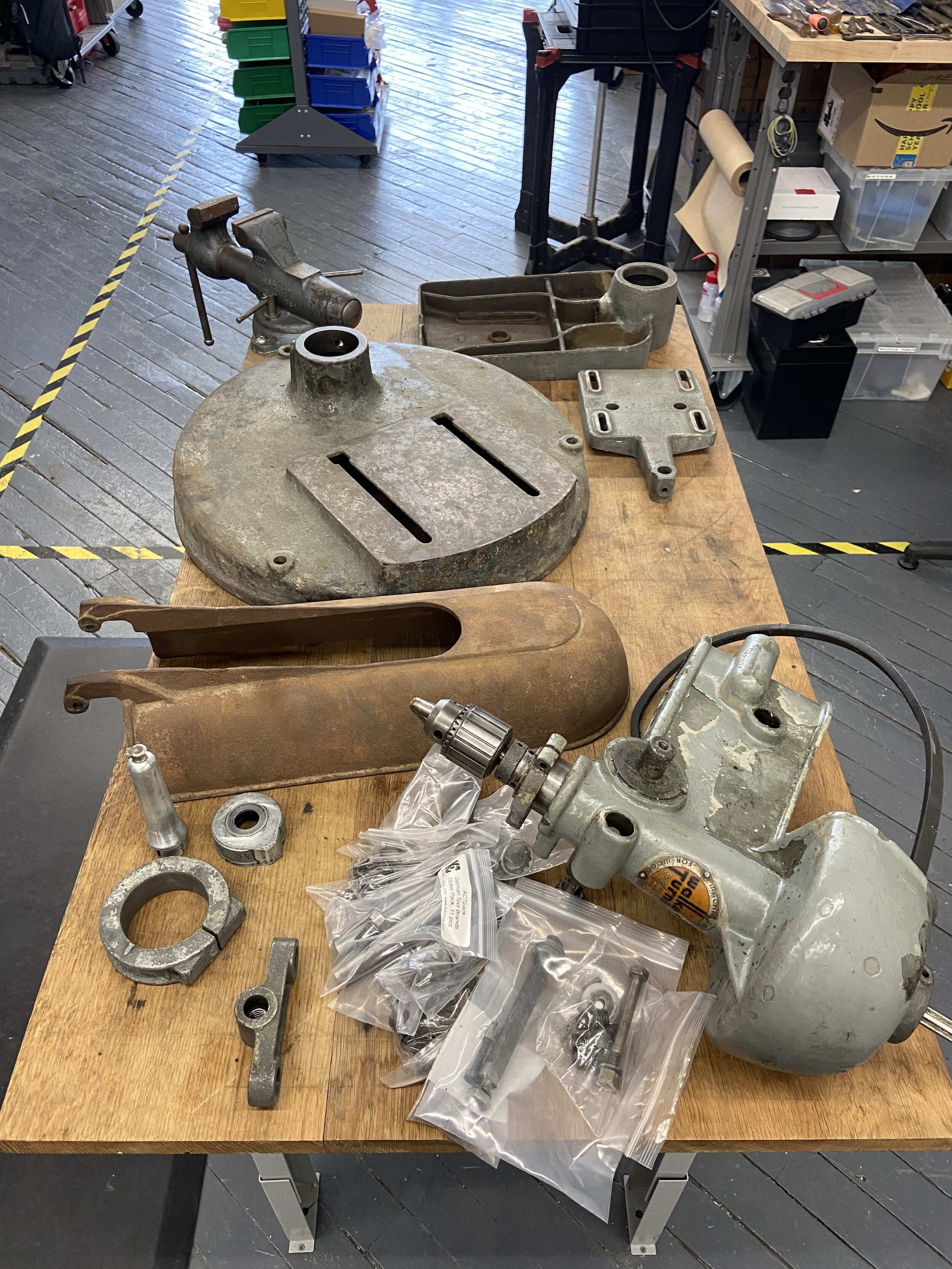
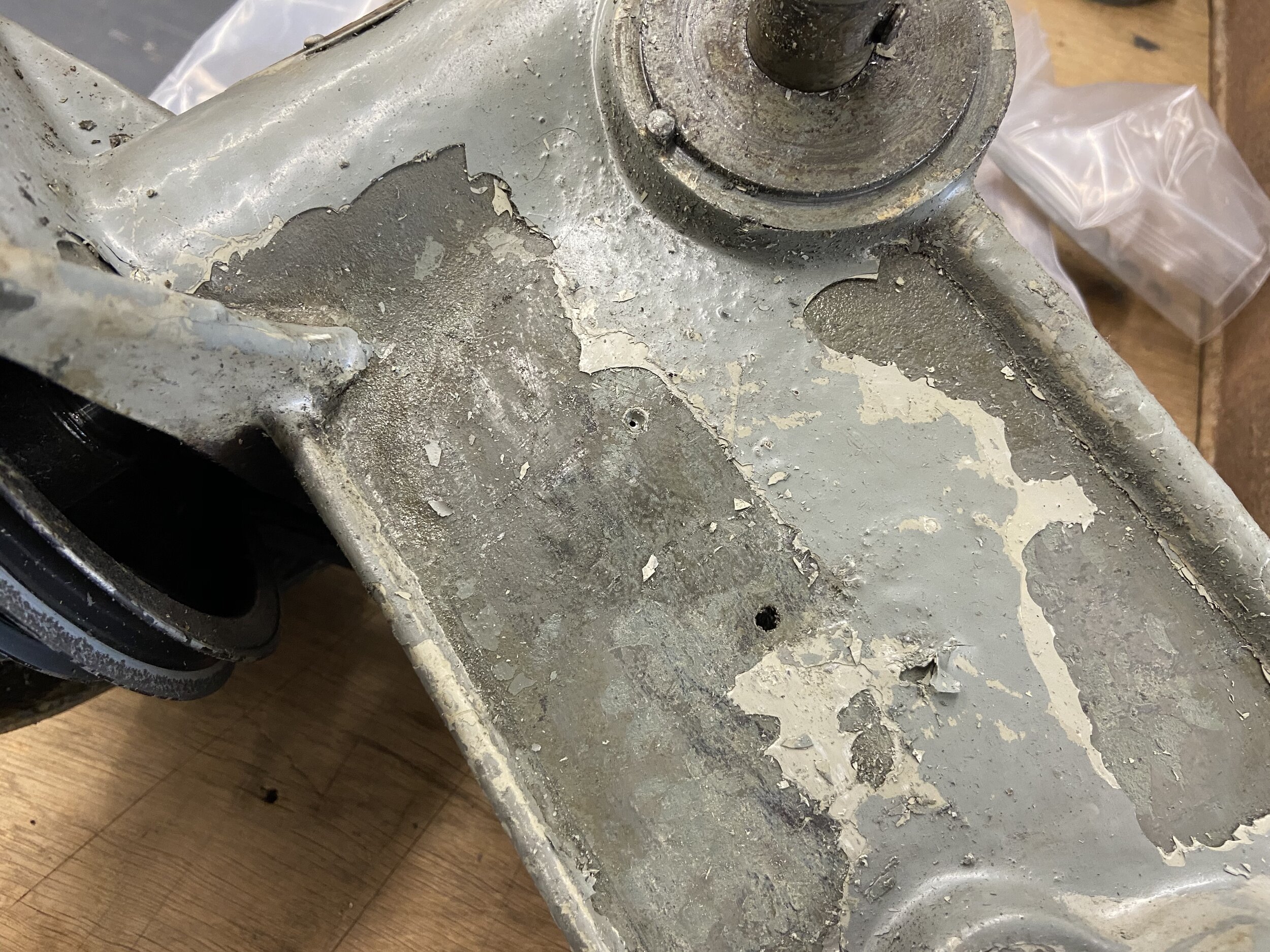
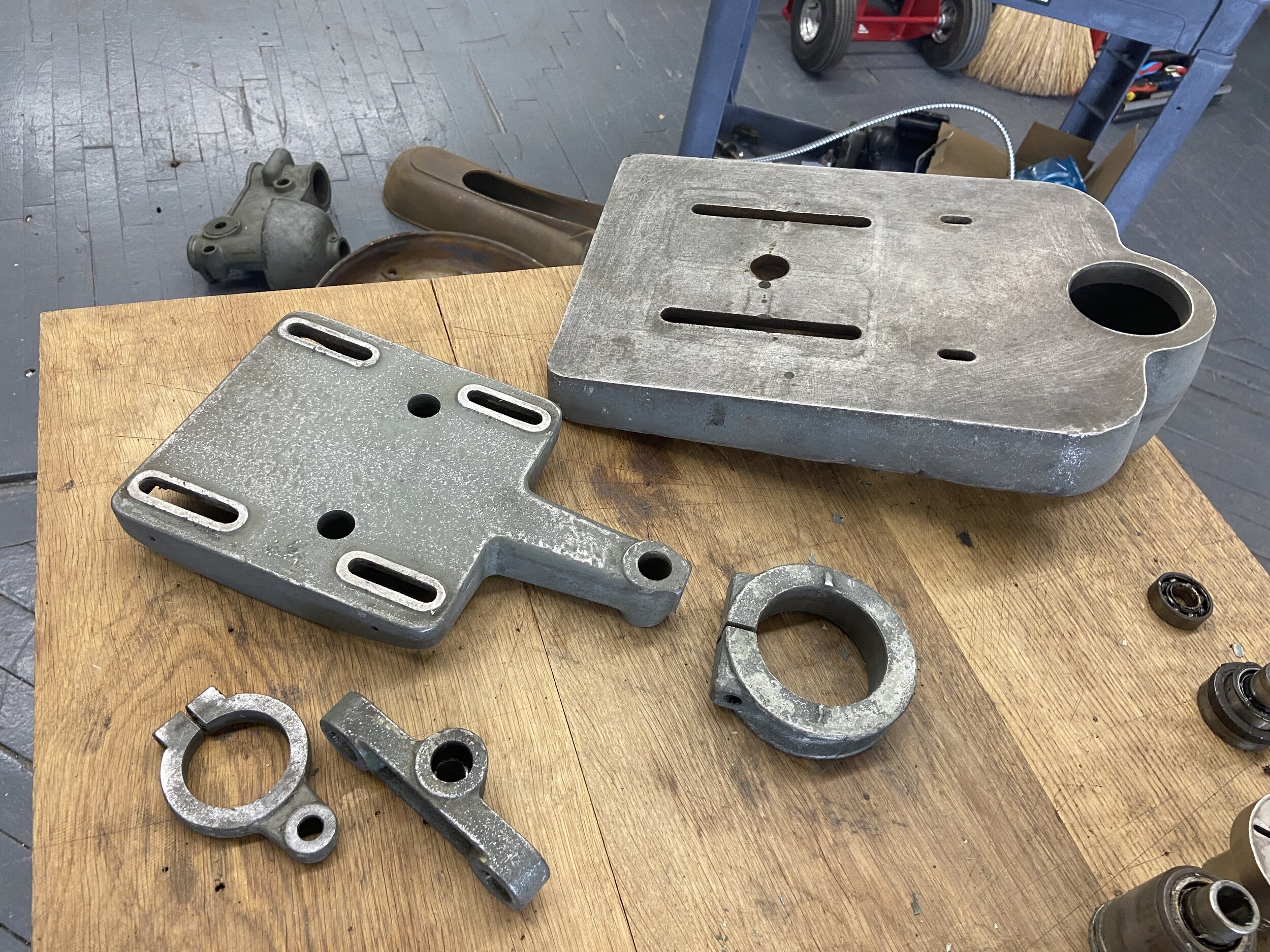
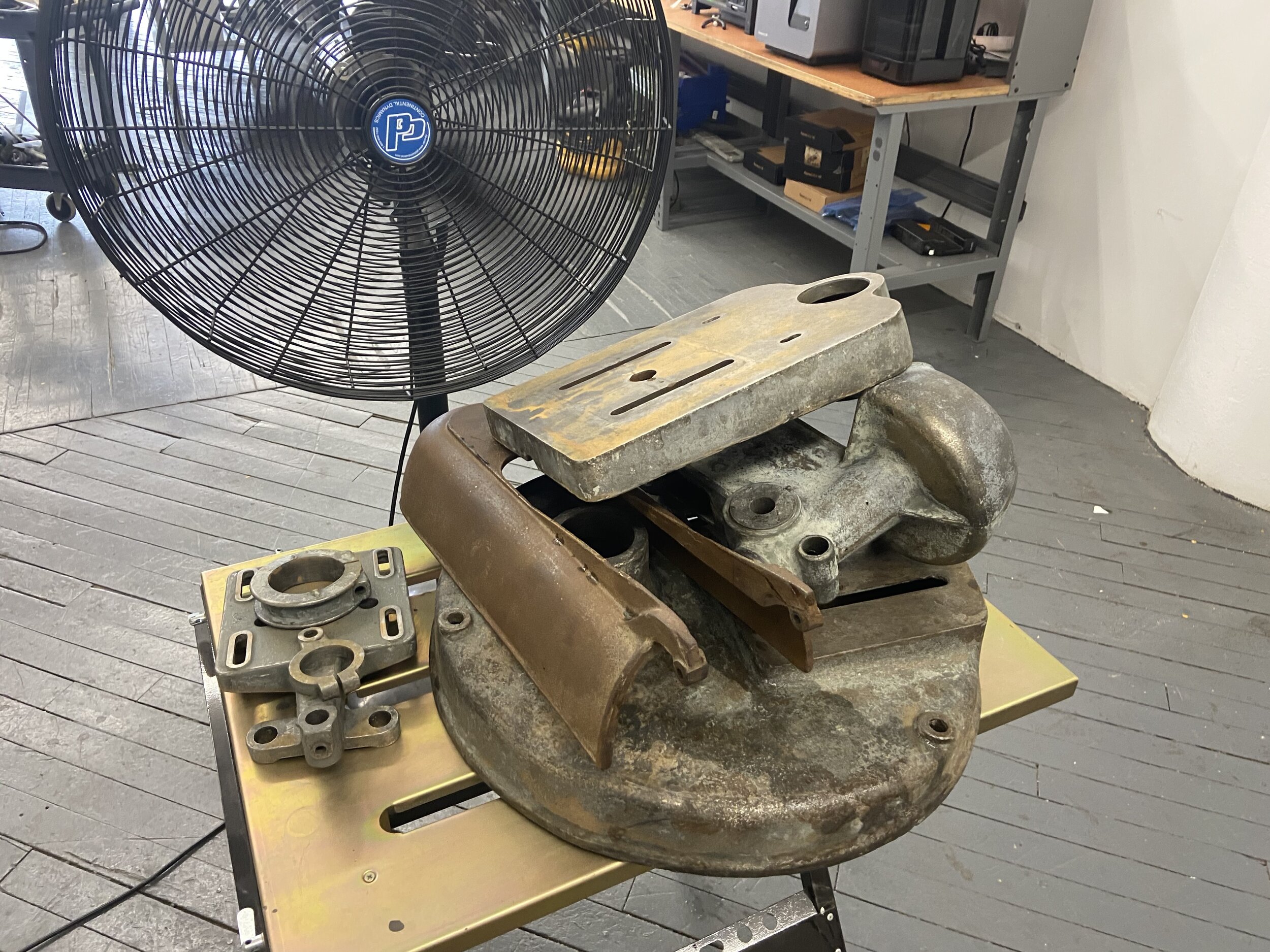
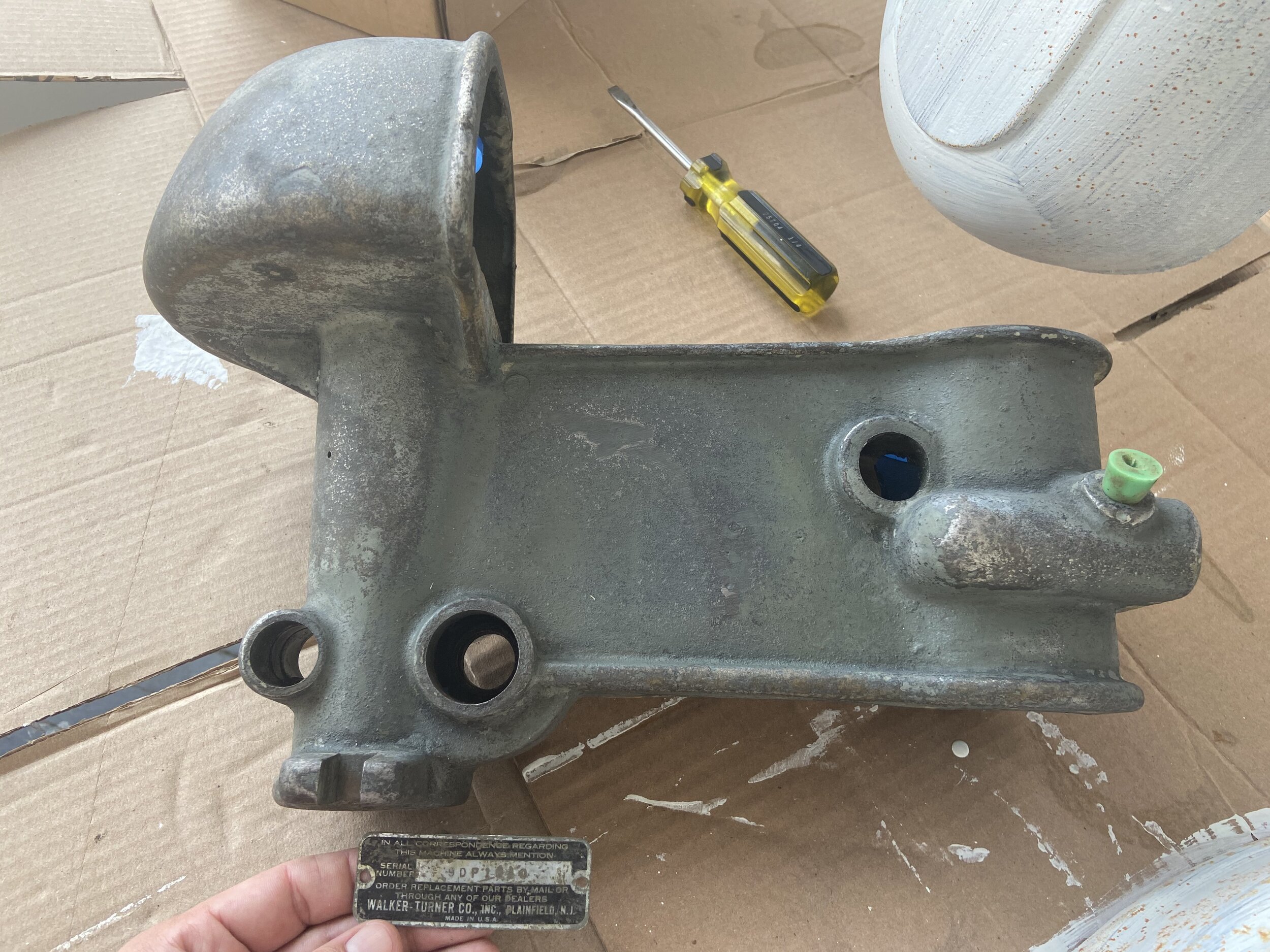
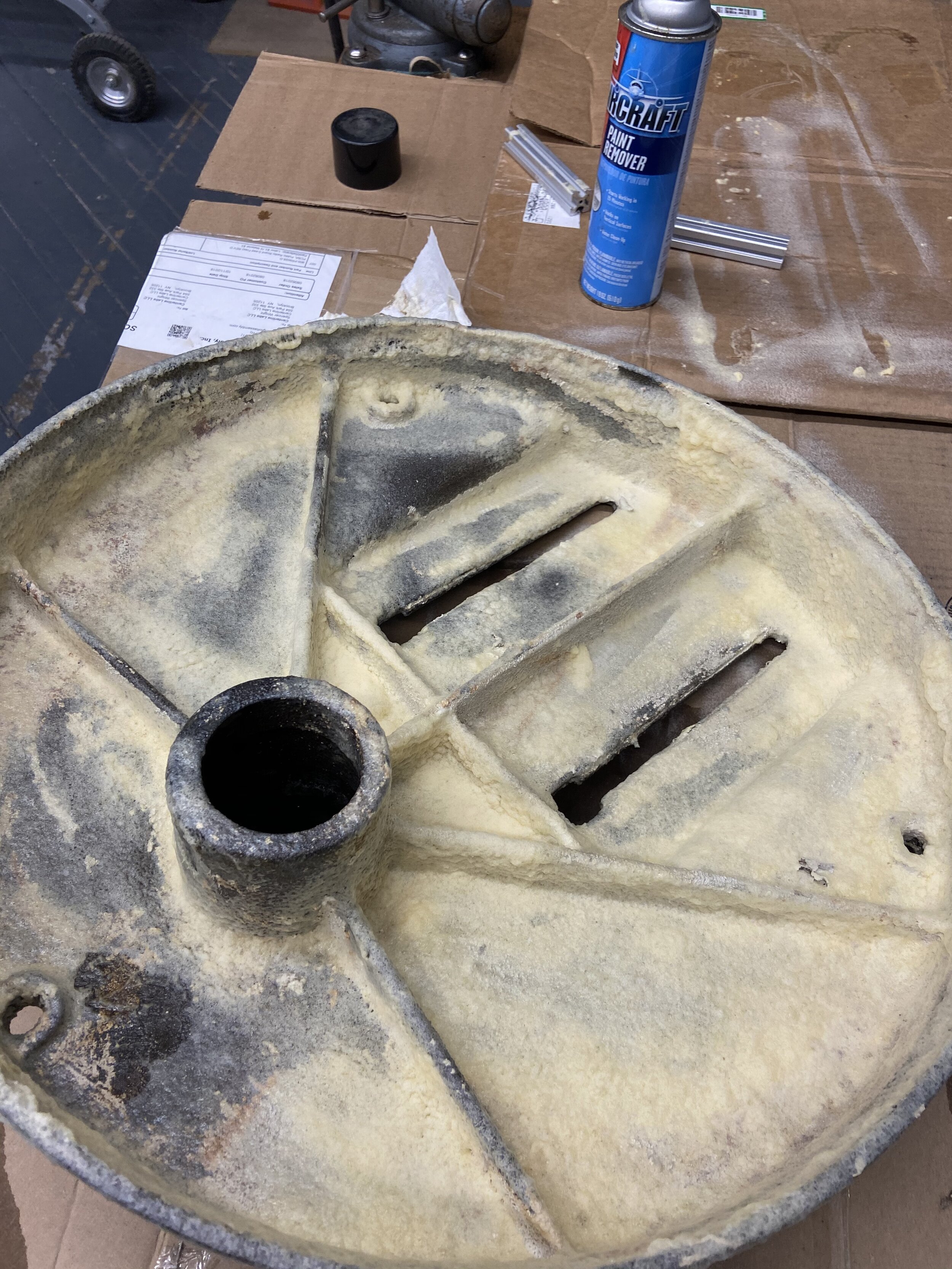
There was one satisfying interlude here, which was cleaning (with a degreaser and then a wire wheel) all of the non-painted parts in the drill press.
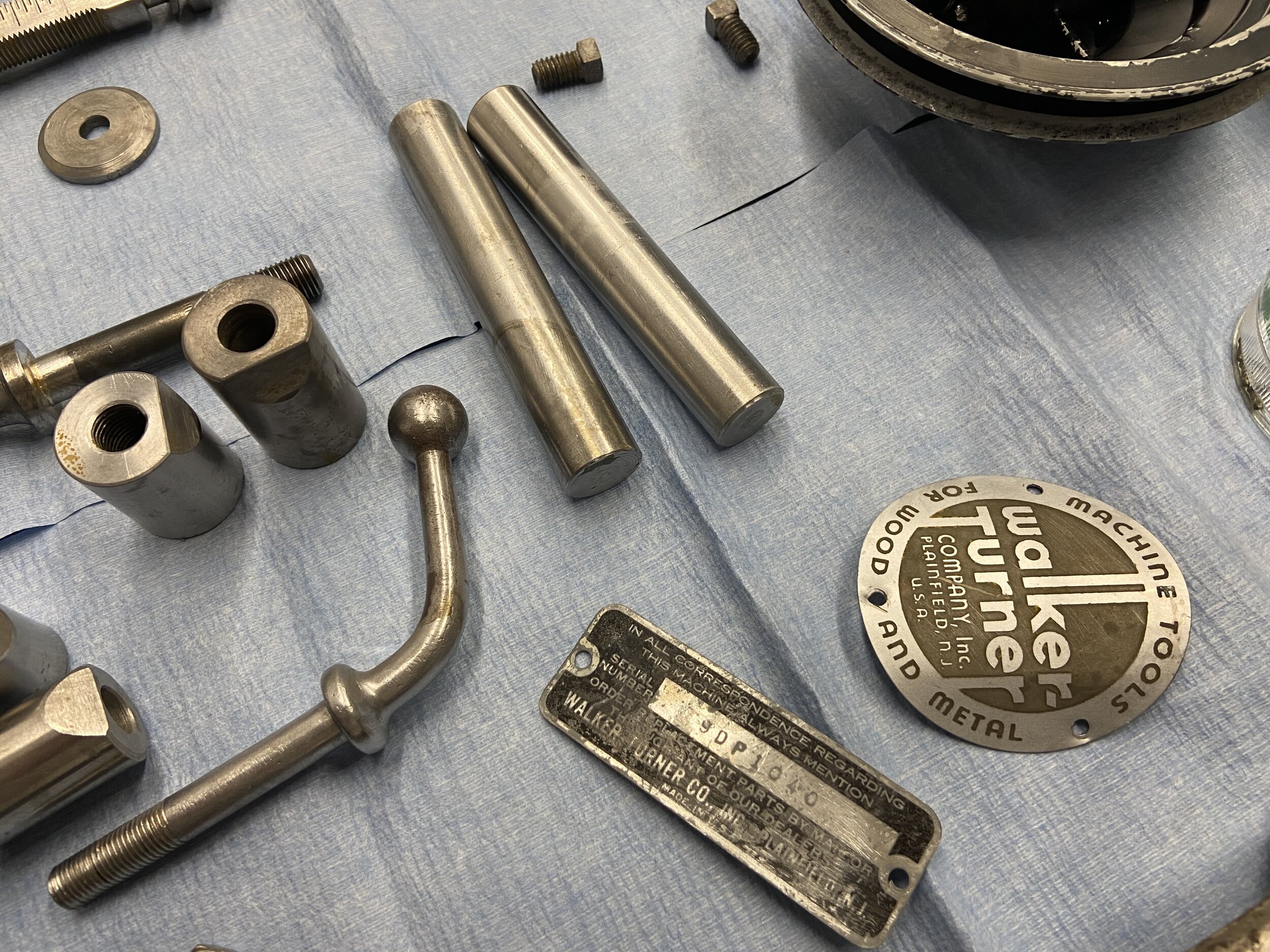
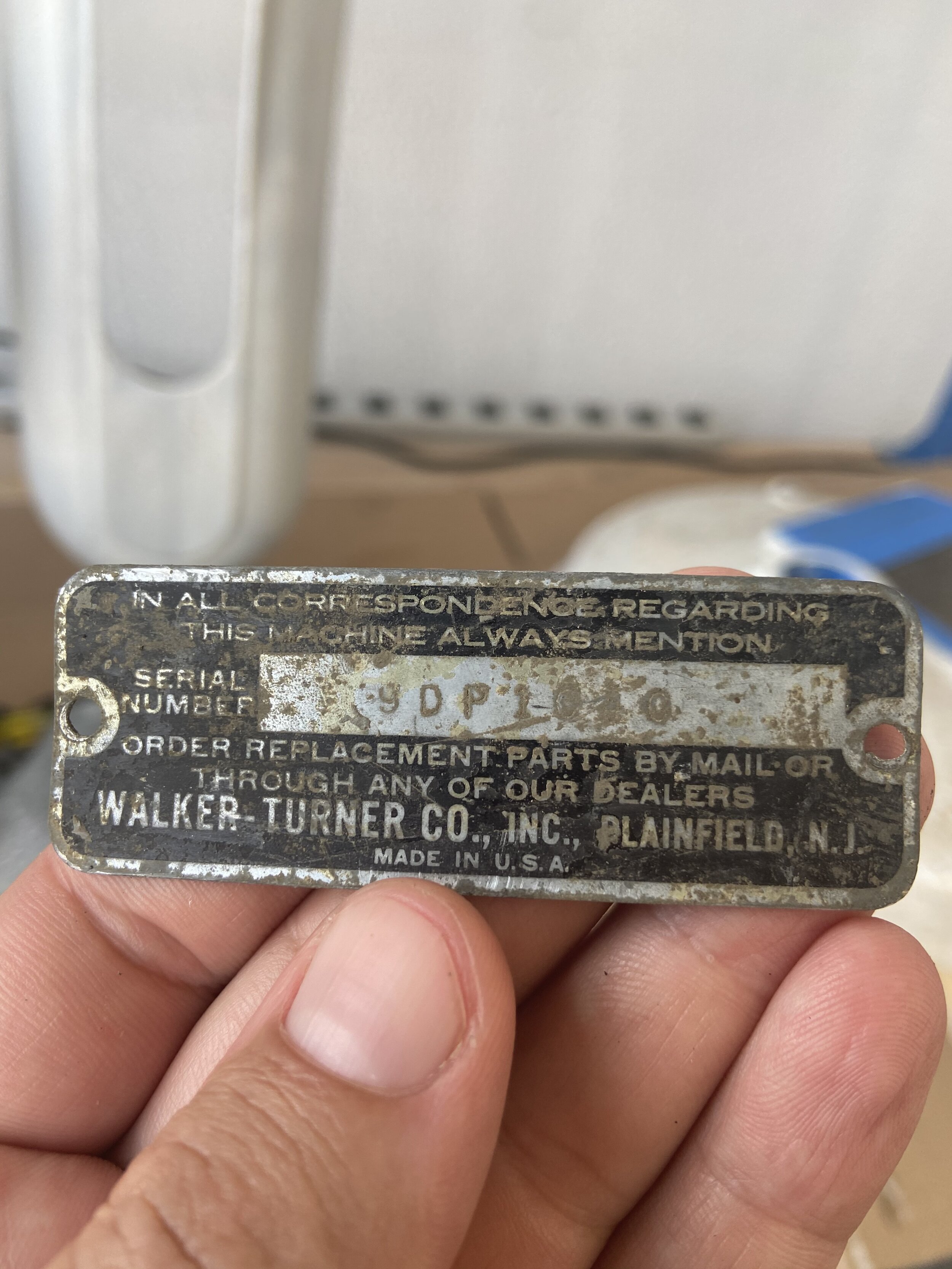
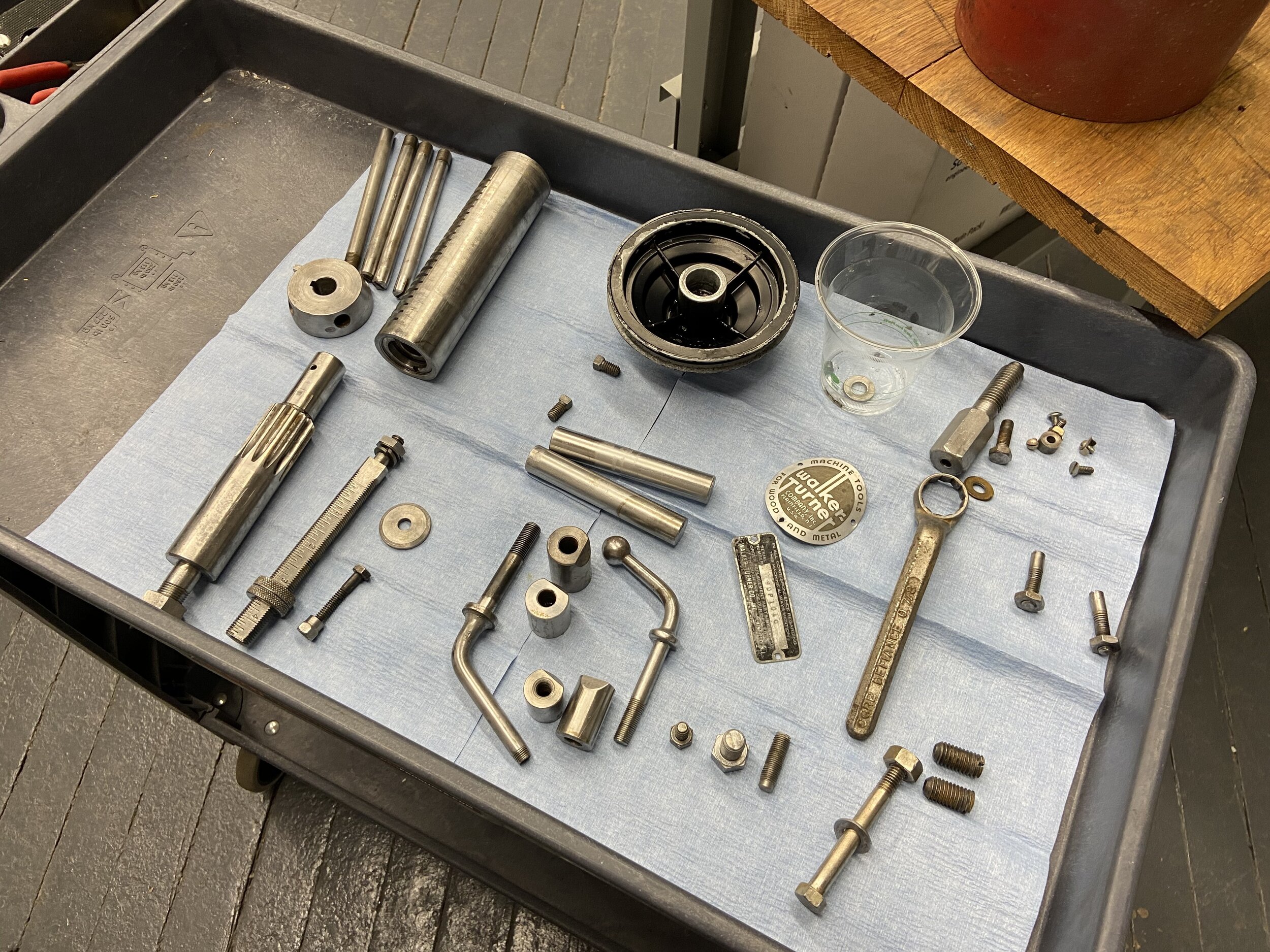
For most of the parts, prep continued with two additional steps. First, everything got a light coat of PickleX, a conversion coating. Second, everything was dried out really well using some hacky methods: A hot plate and a heat gun.
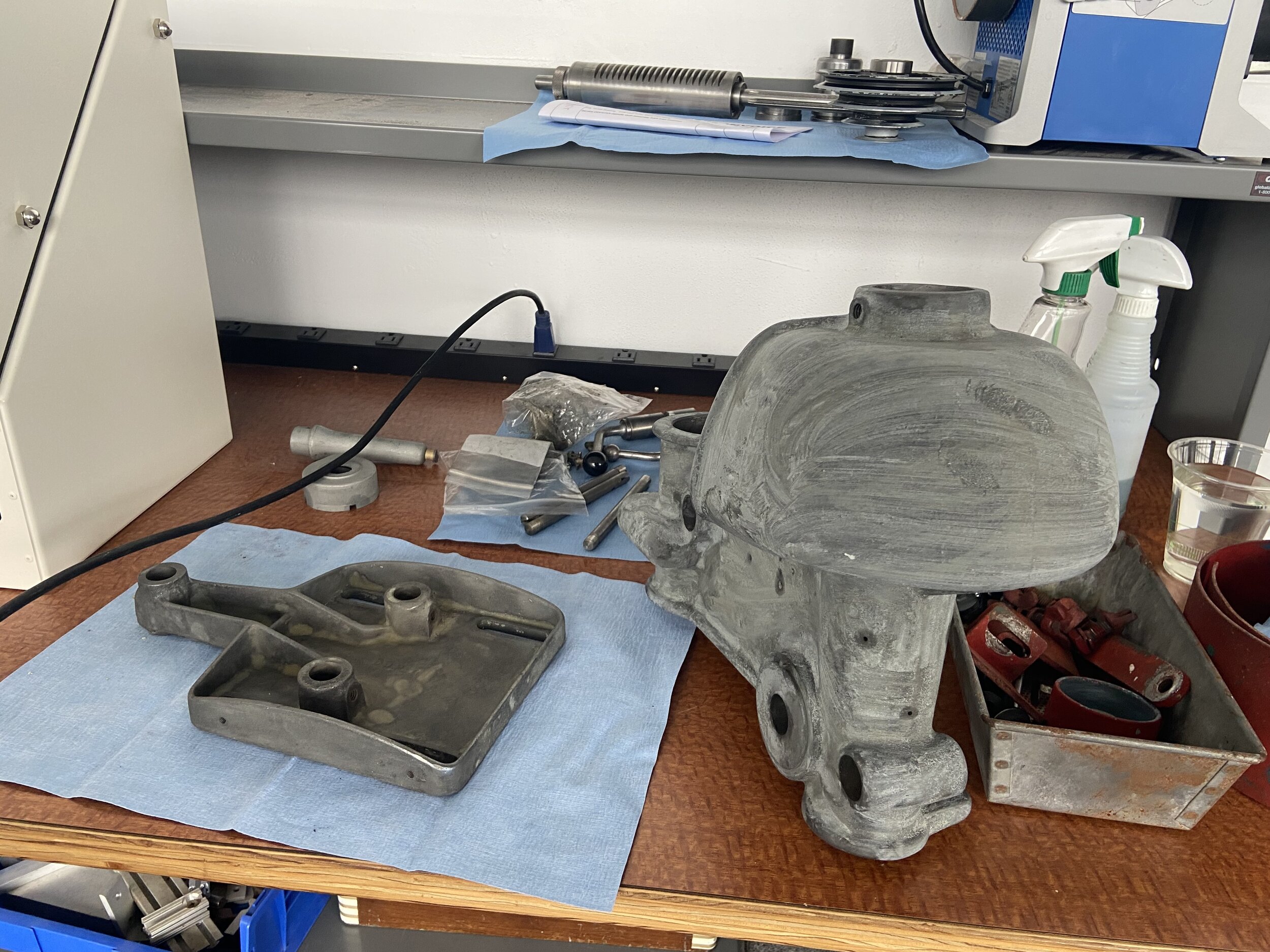
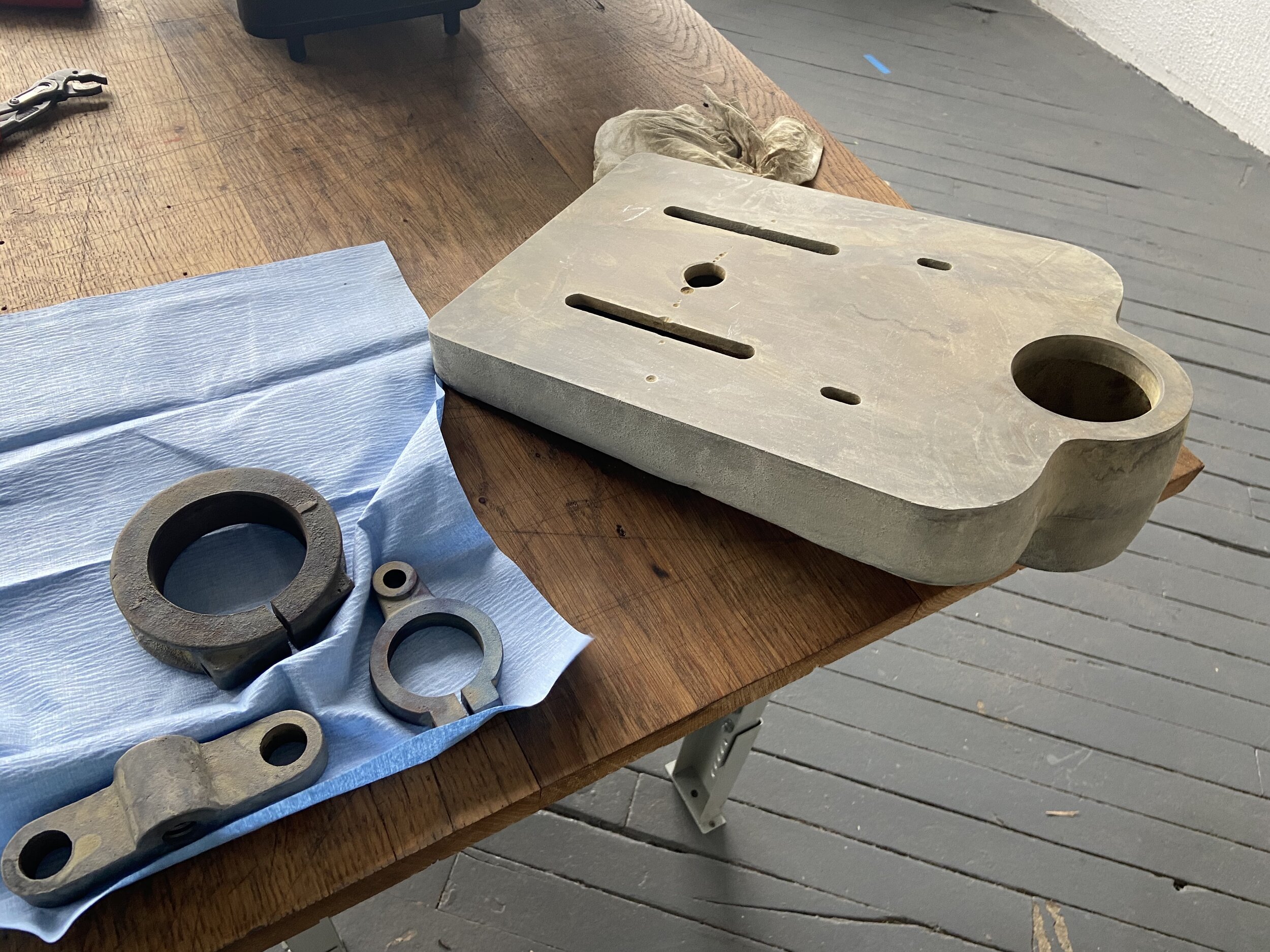
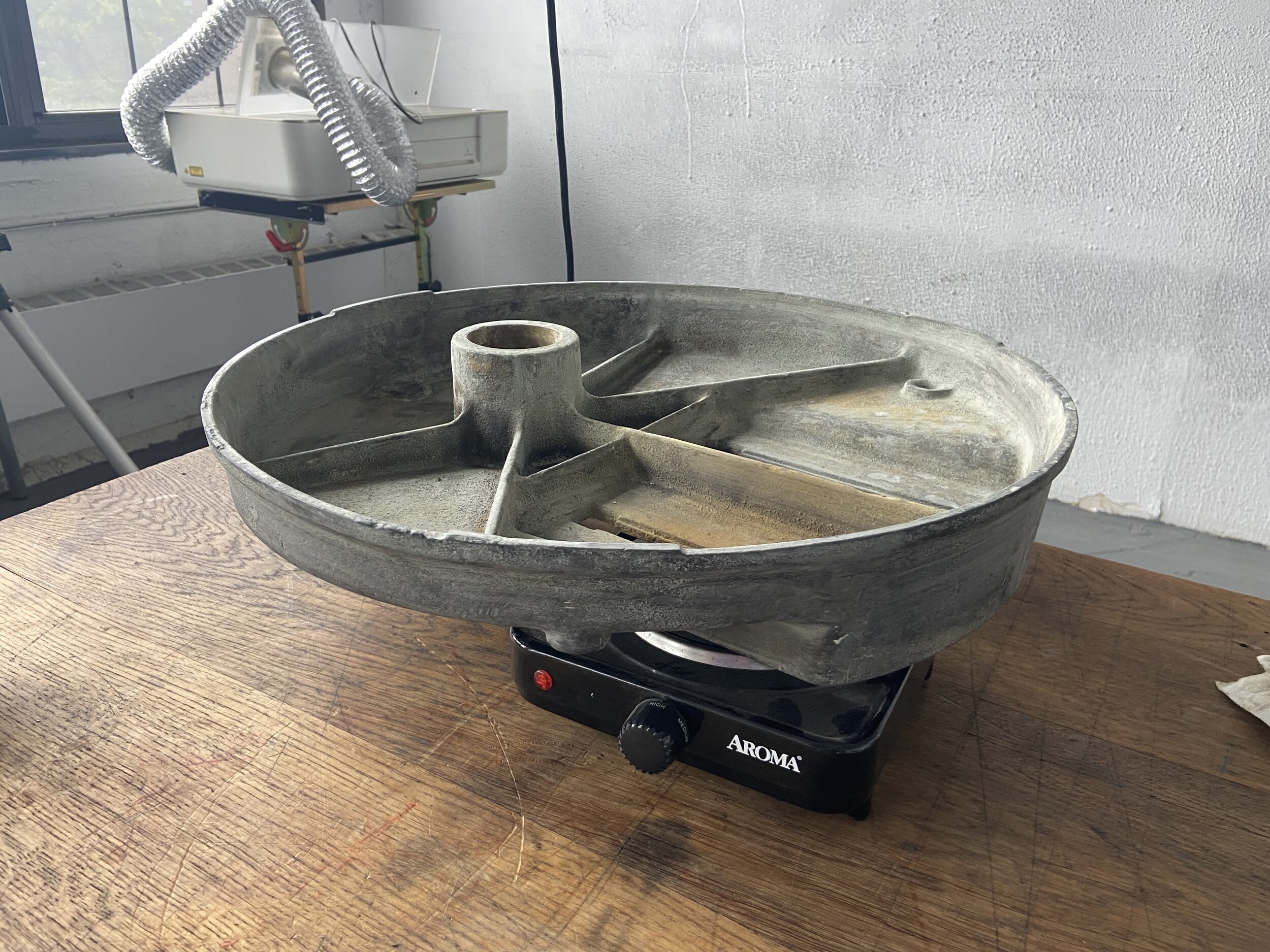
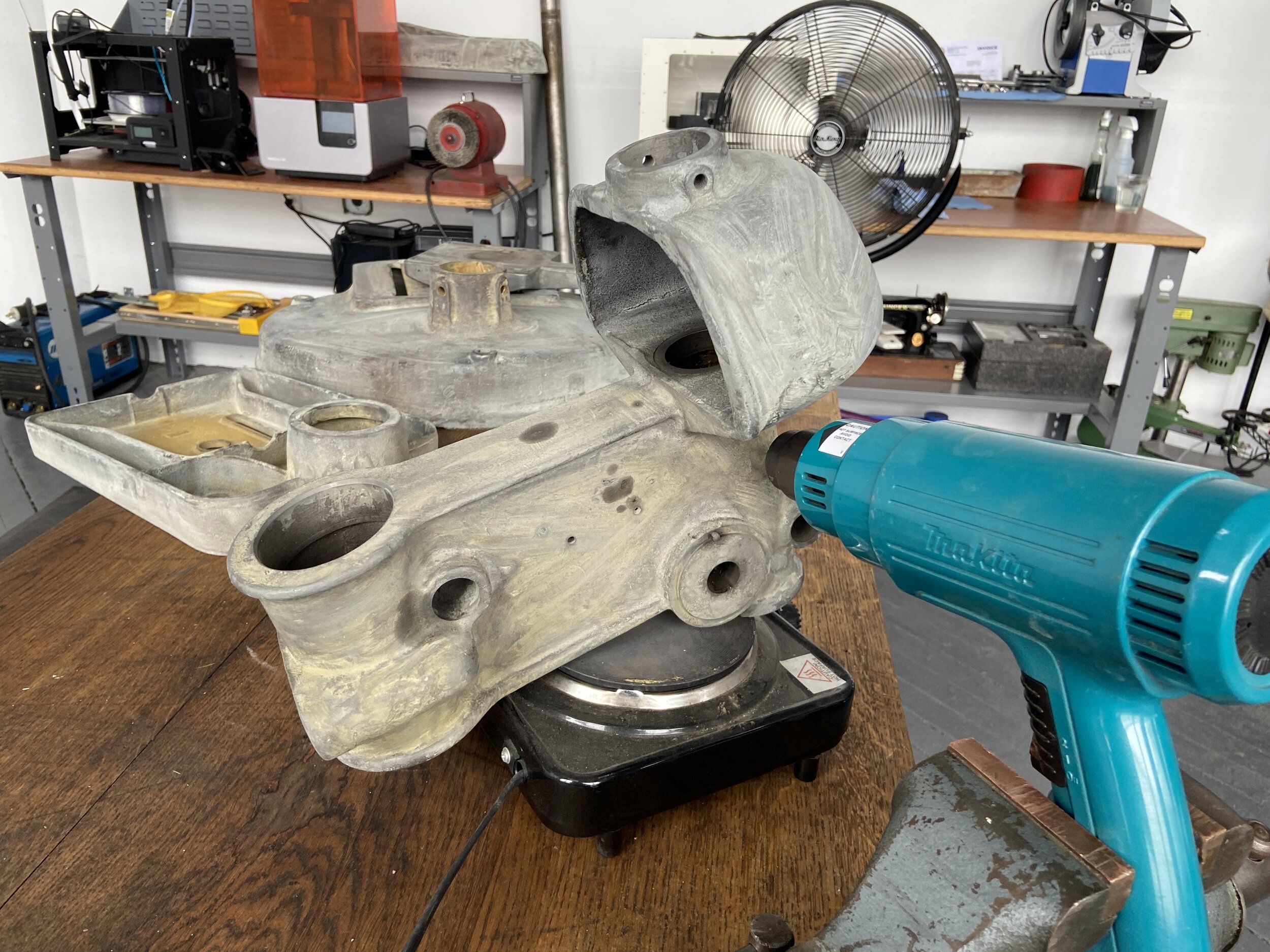
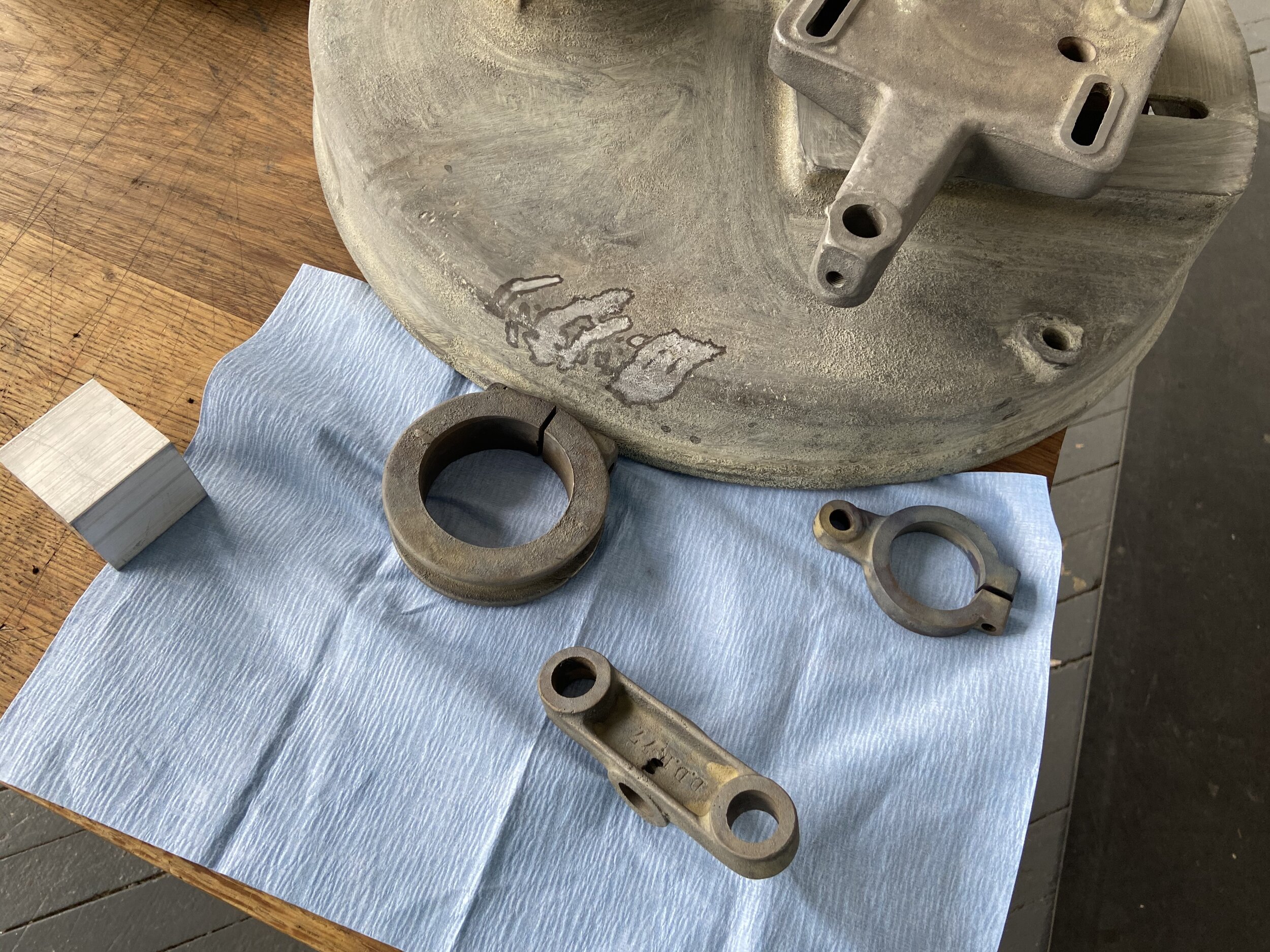
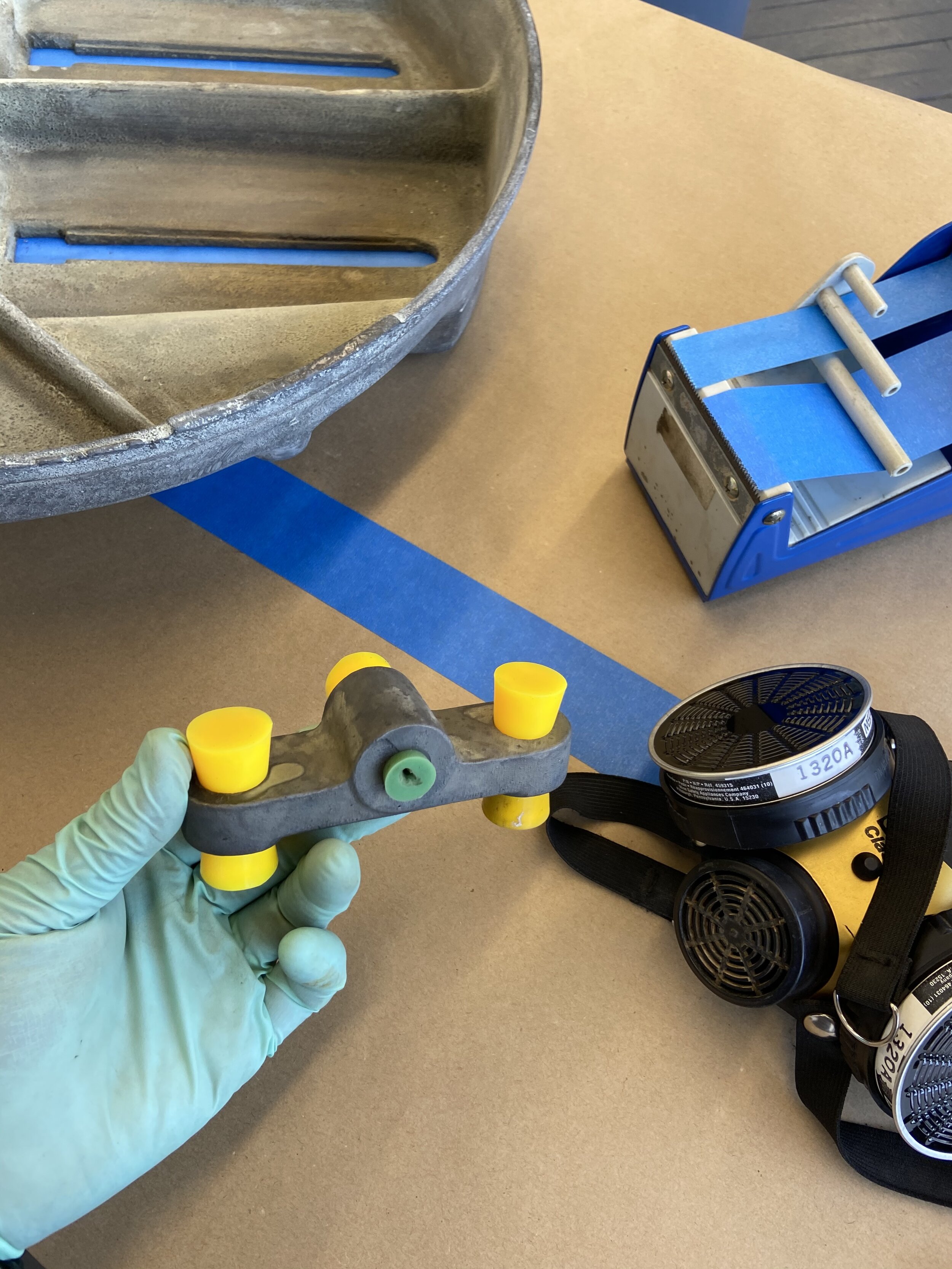
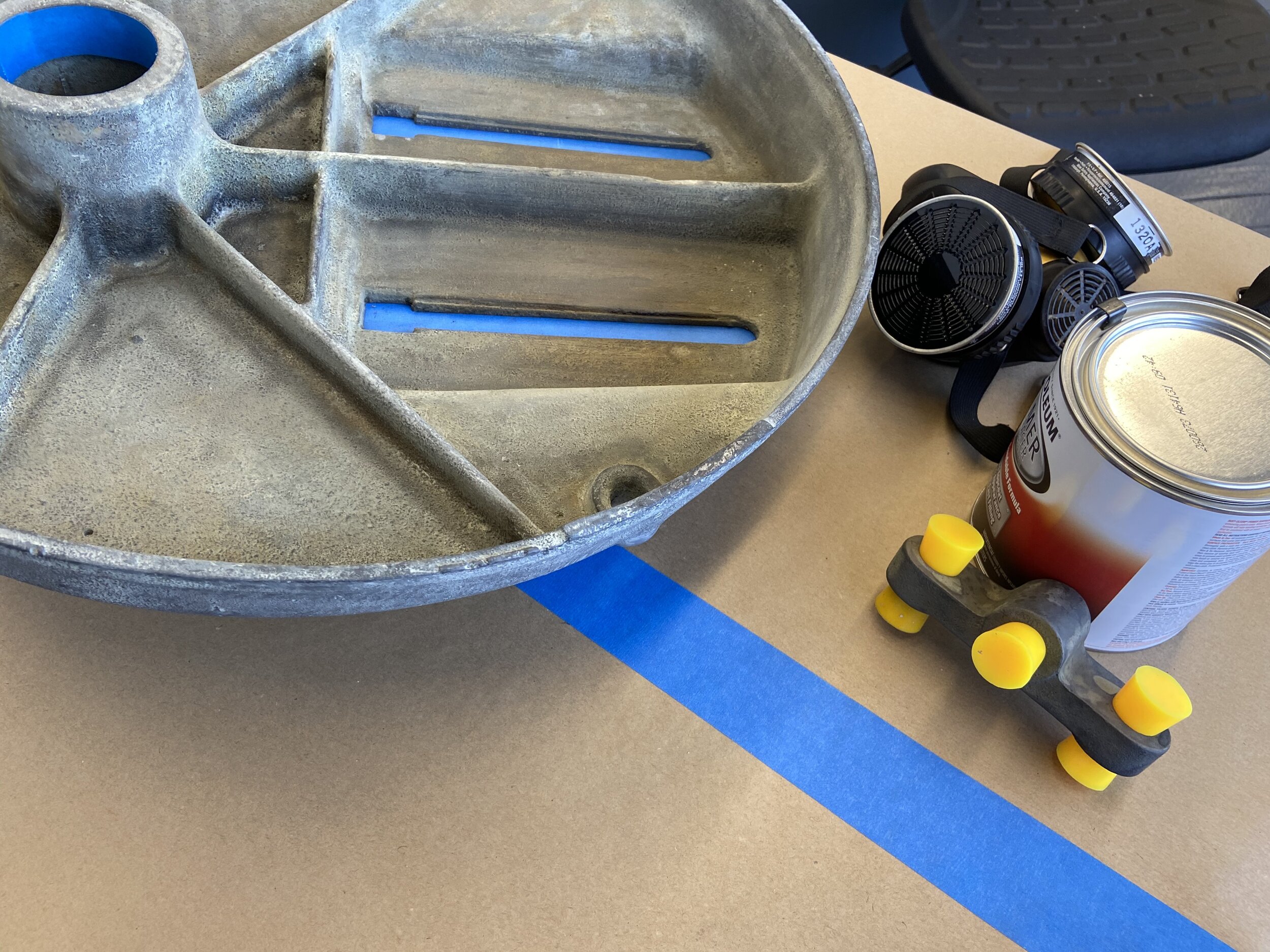

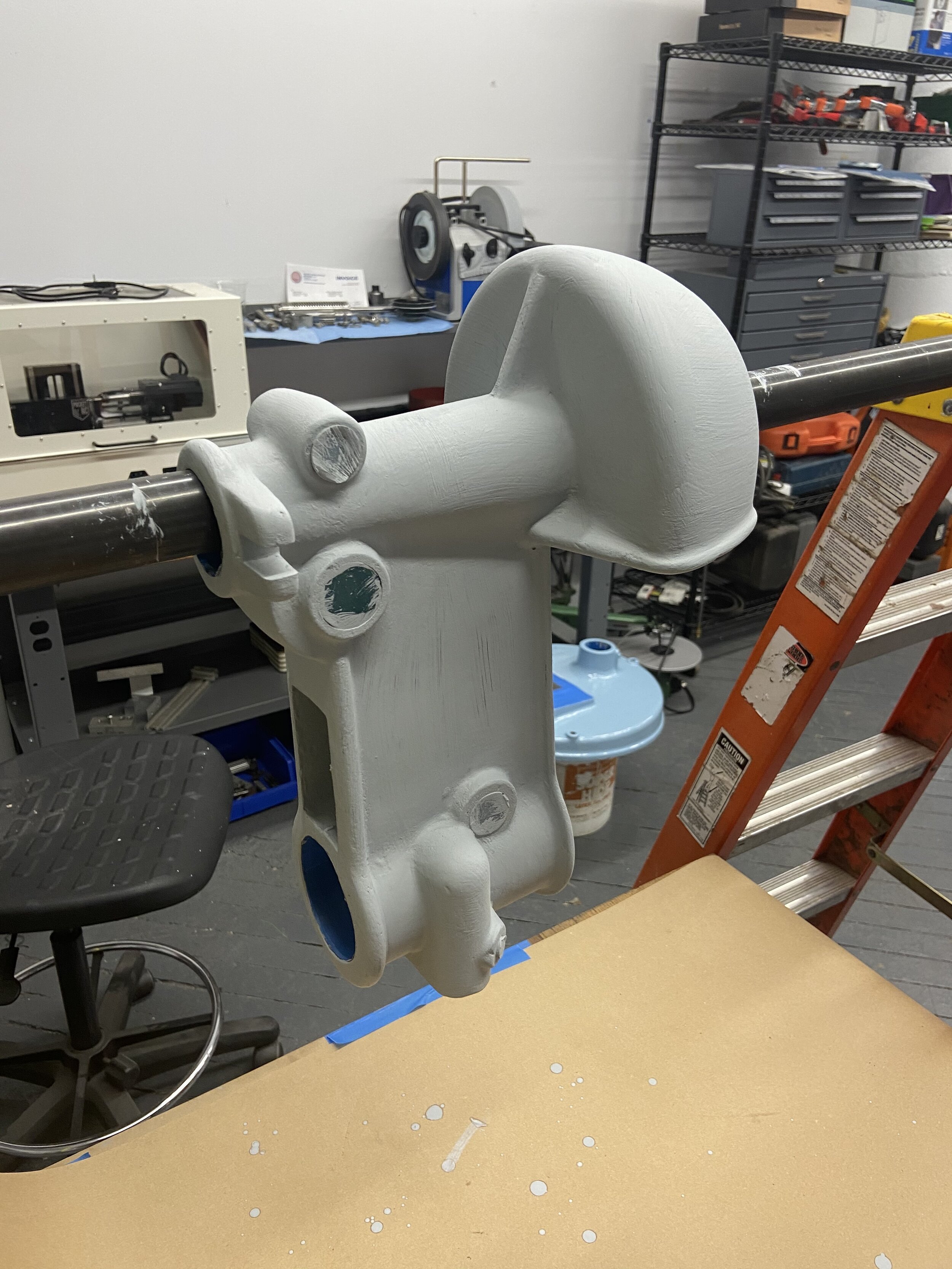
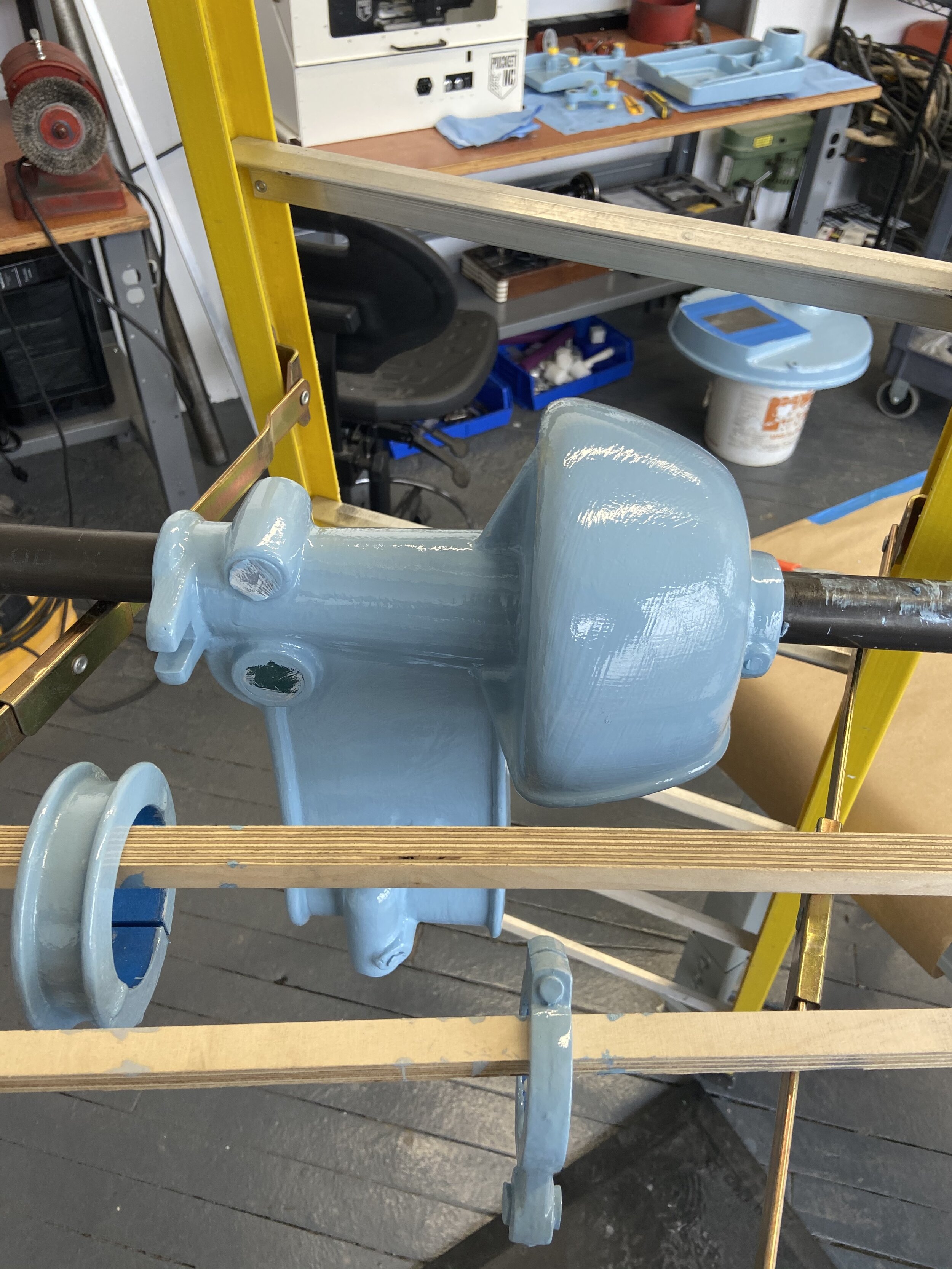
The drill press’s head got one additional step: Bondo, which was rather satisfying to use but didn’t contribute all that much to the final product.
After probably a week’s worth of work (spread out over a month or so), I finally got a brush out. The primer I was using was horrid, a product that was reduced with methyl amyl ketone and was both thin and extremely fast drying. It went on like water, until it turned to a weird slurry just a few minutes later - a rather unnerving transition.
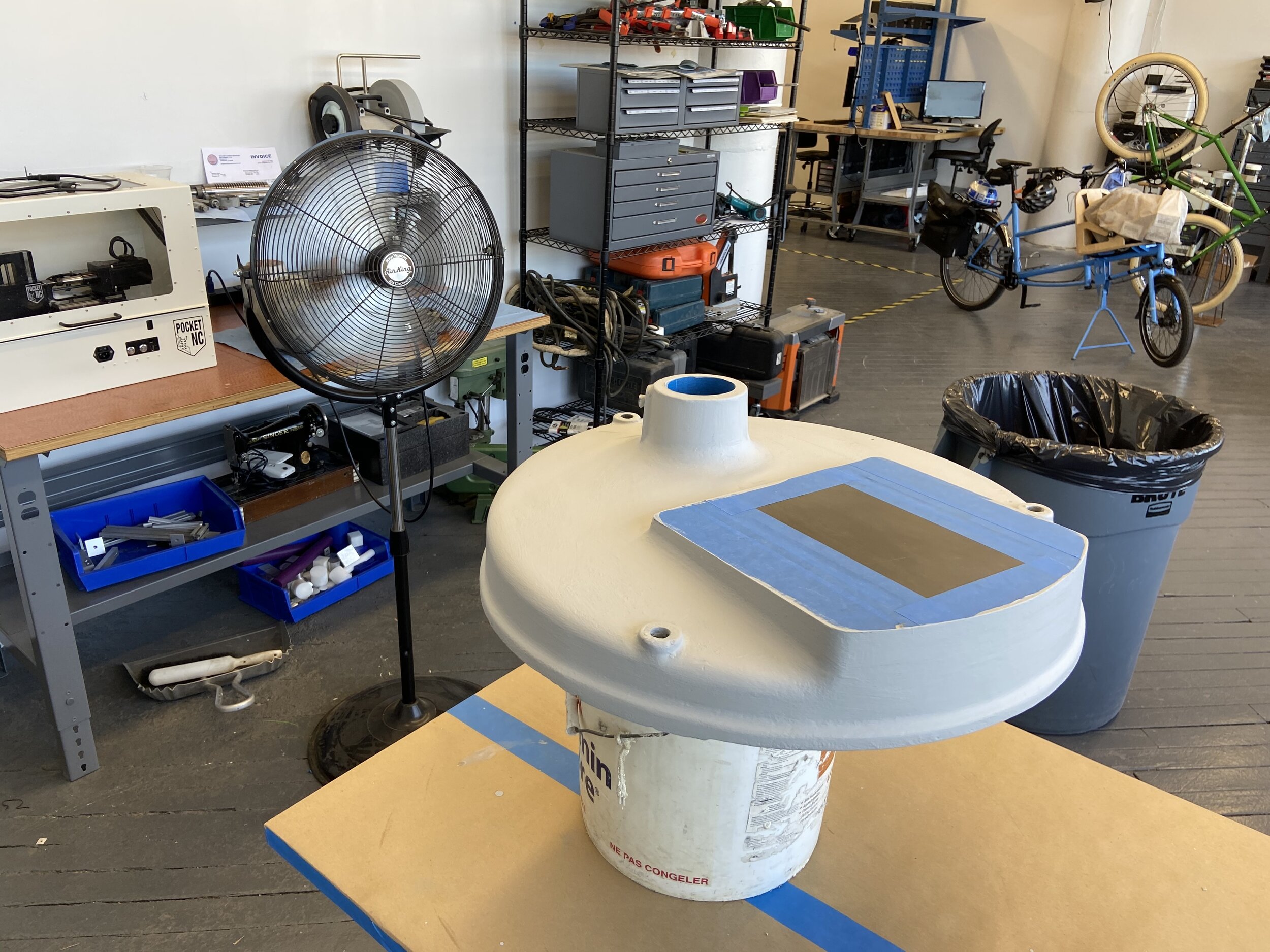
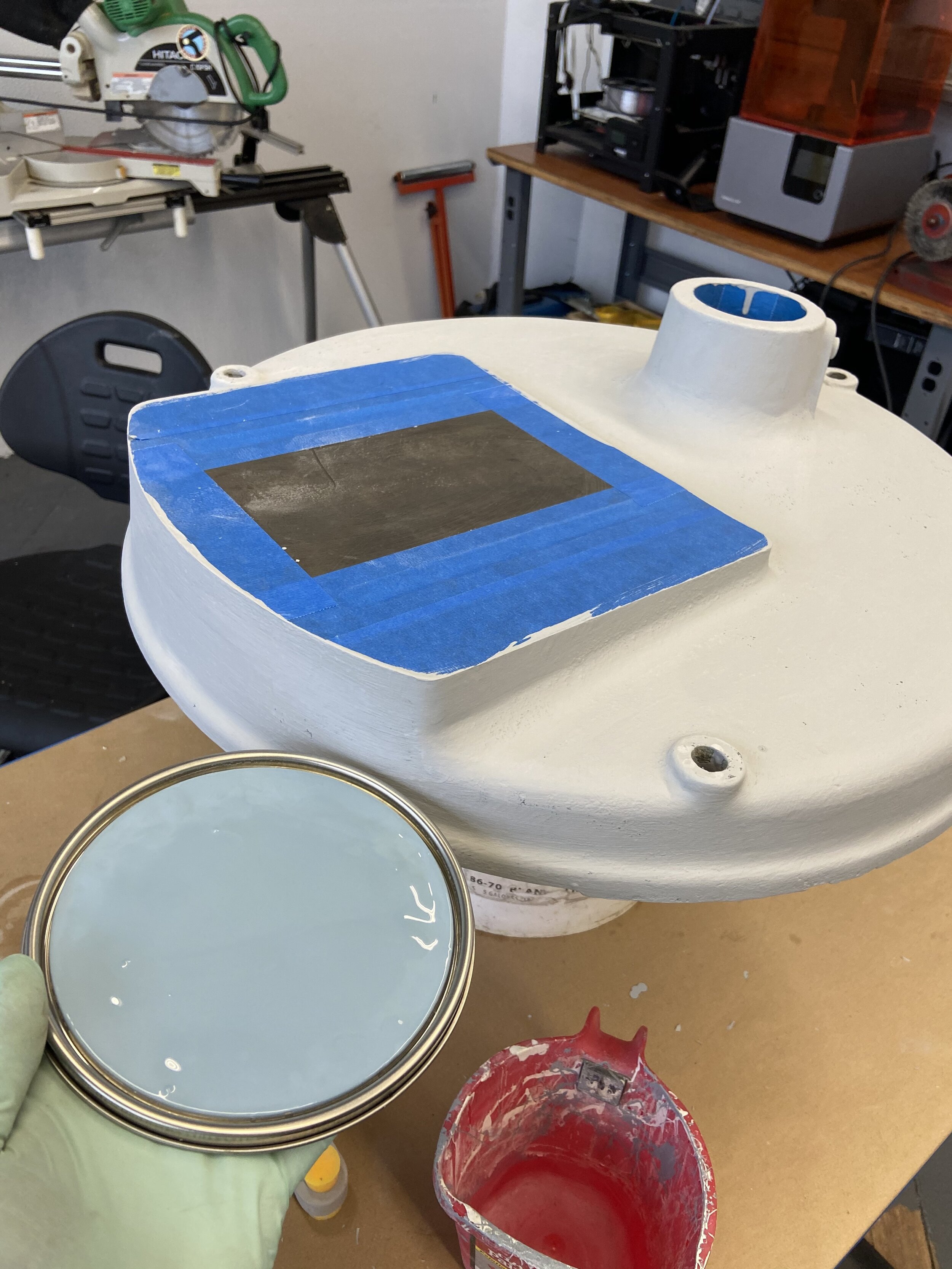
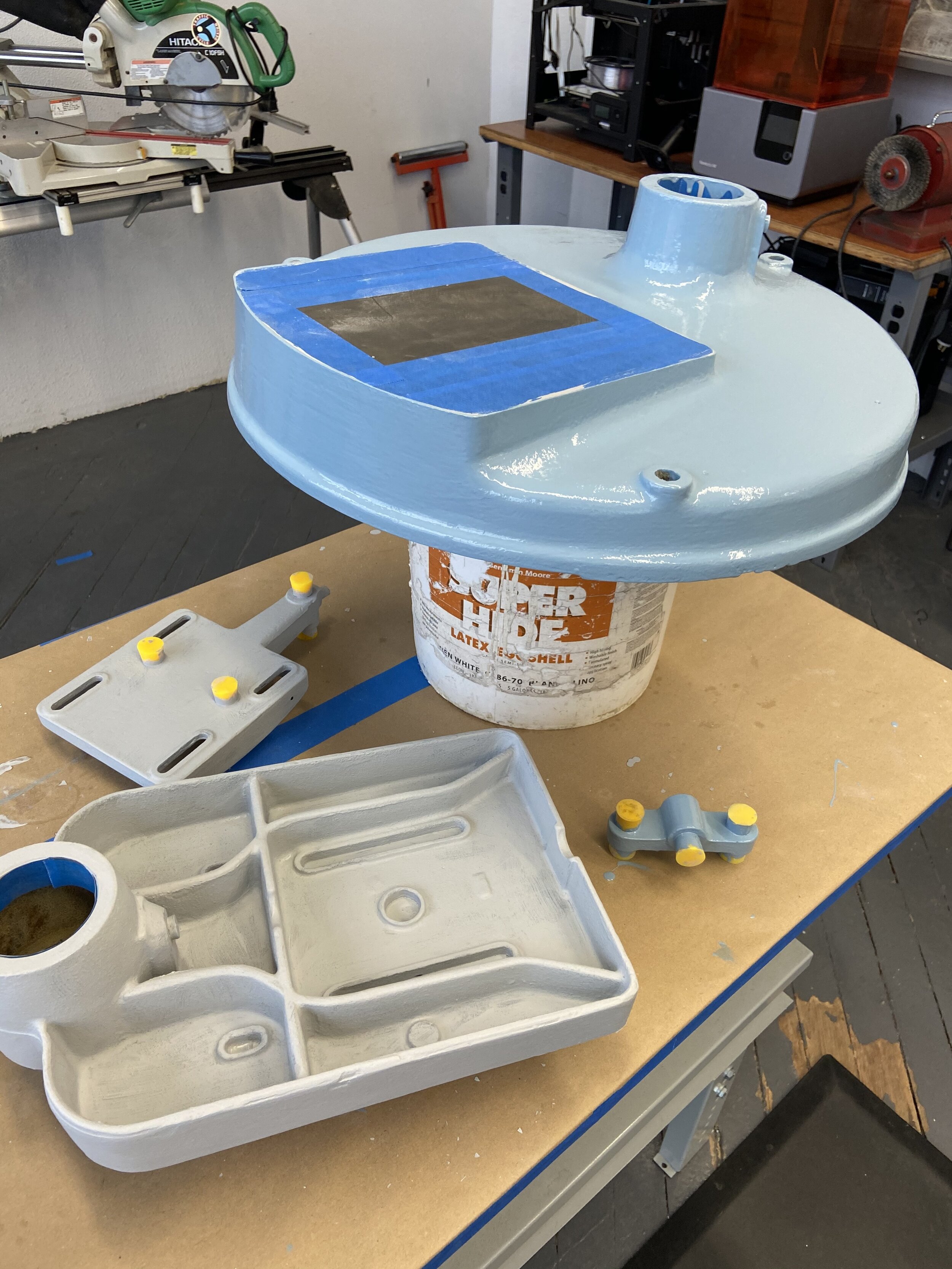
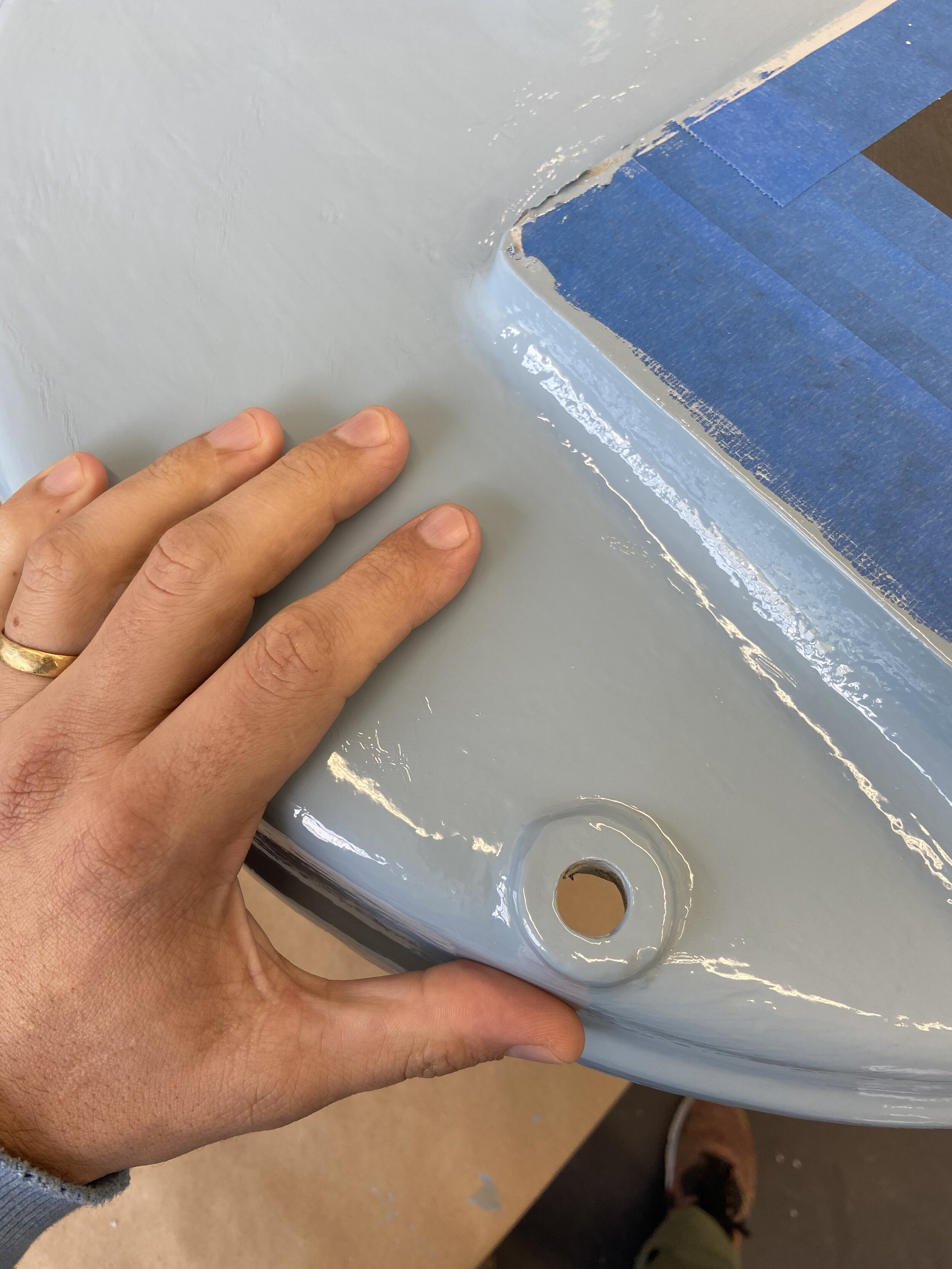
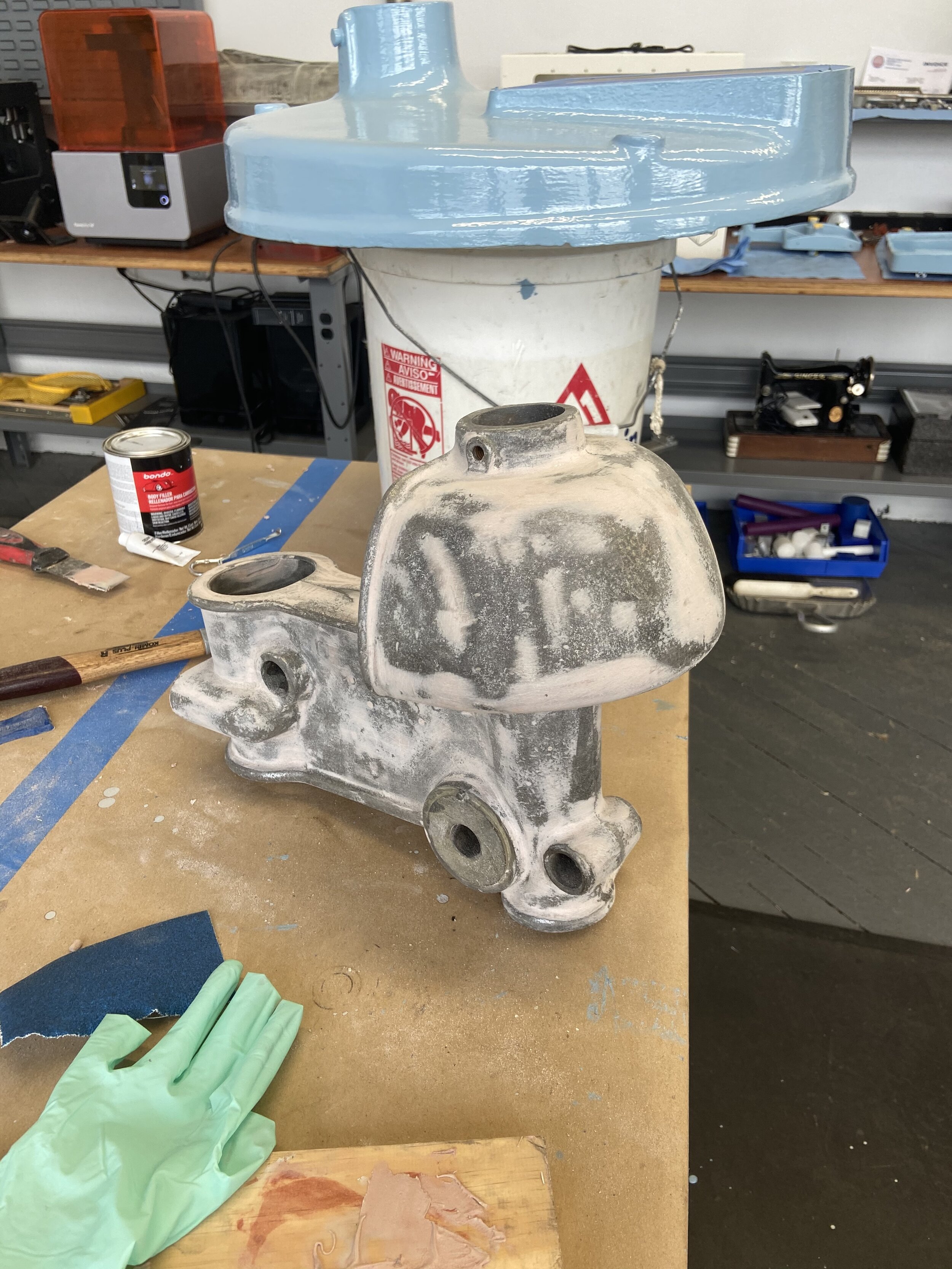
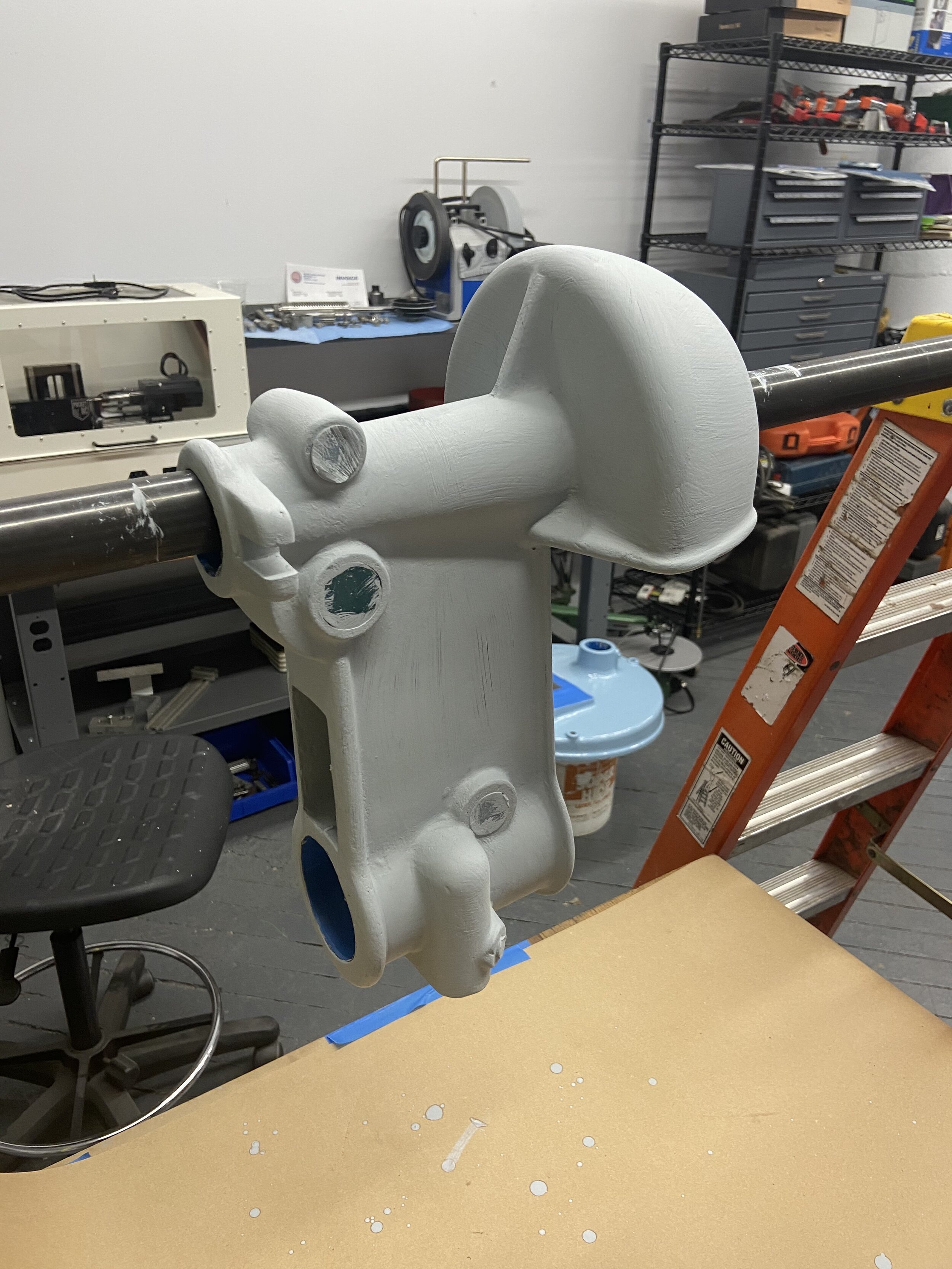
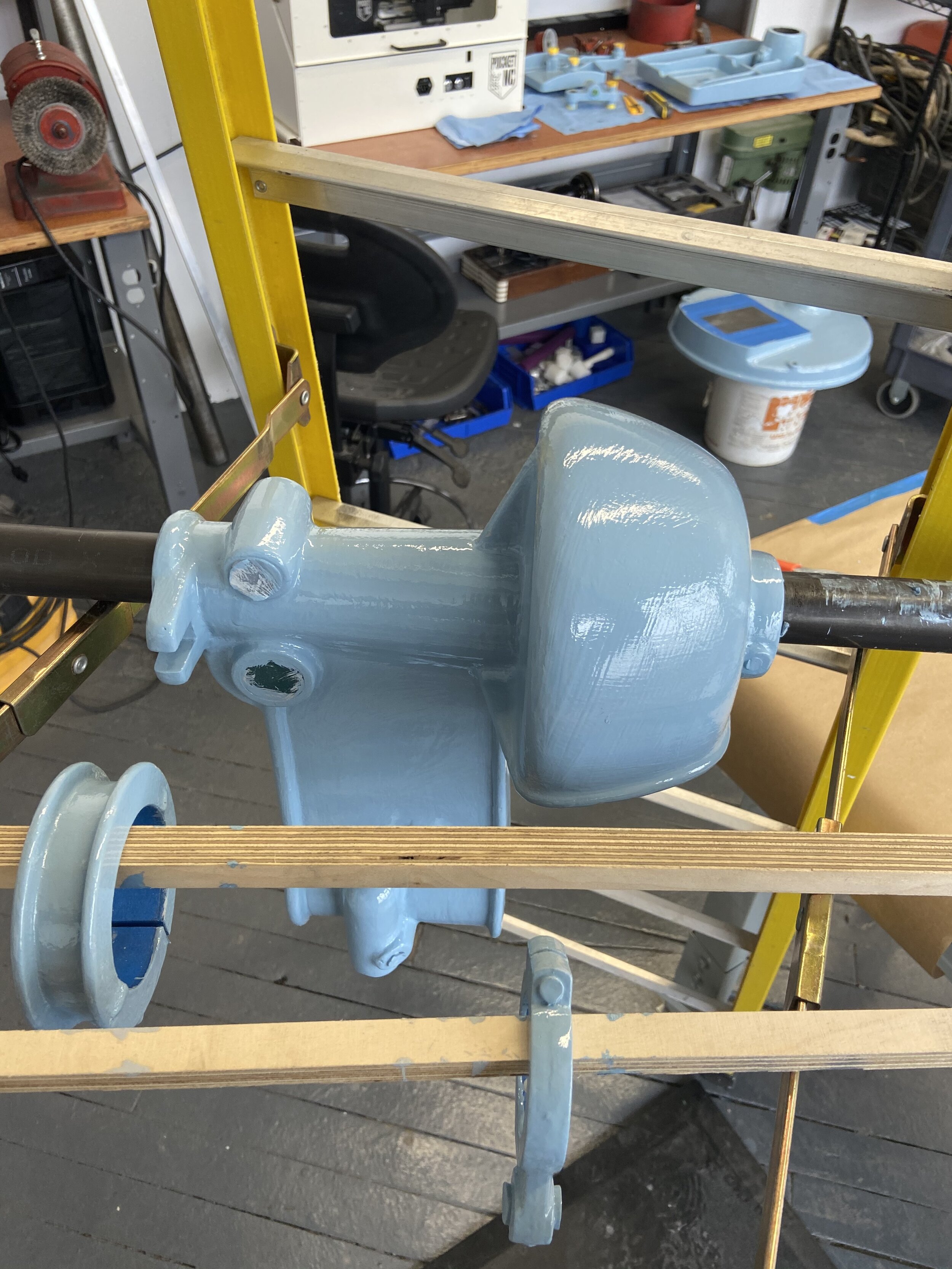
Finally, the drill press was ready to go back together. At this point I had begun to seriously question whether this project would produce results commensurate with my efforts; the 900 series is after all a relatively small drill press, and I had a growing feeling that it might have made more sense to restore a more capable machine. Regardless, it was satisfying to finally see something more or less functional:
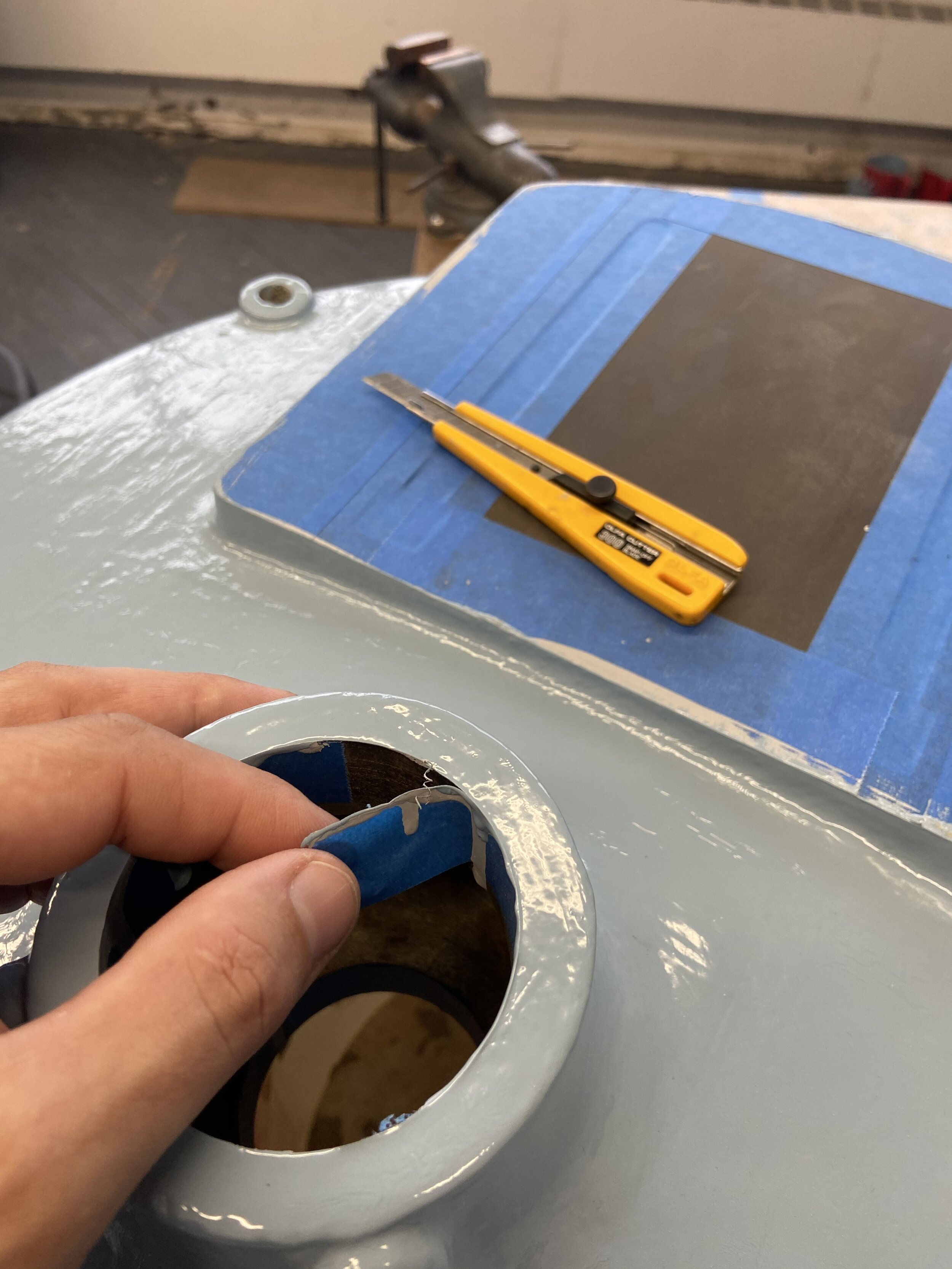
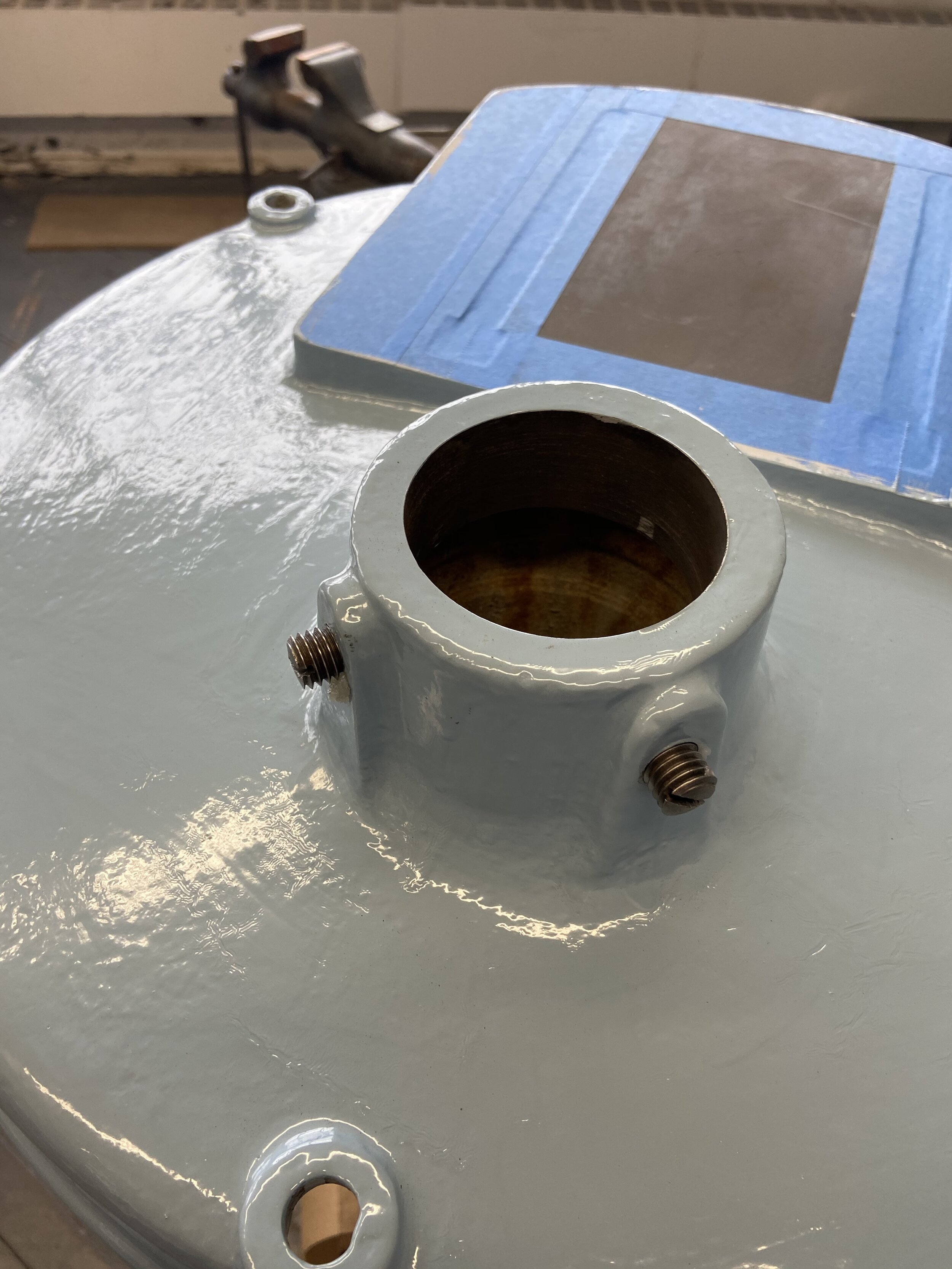
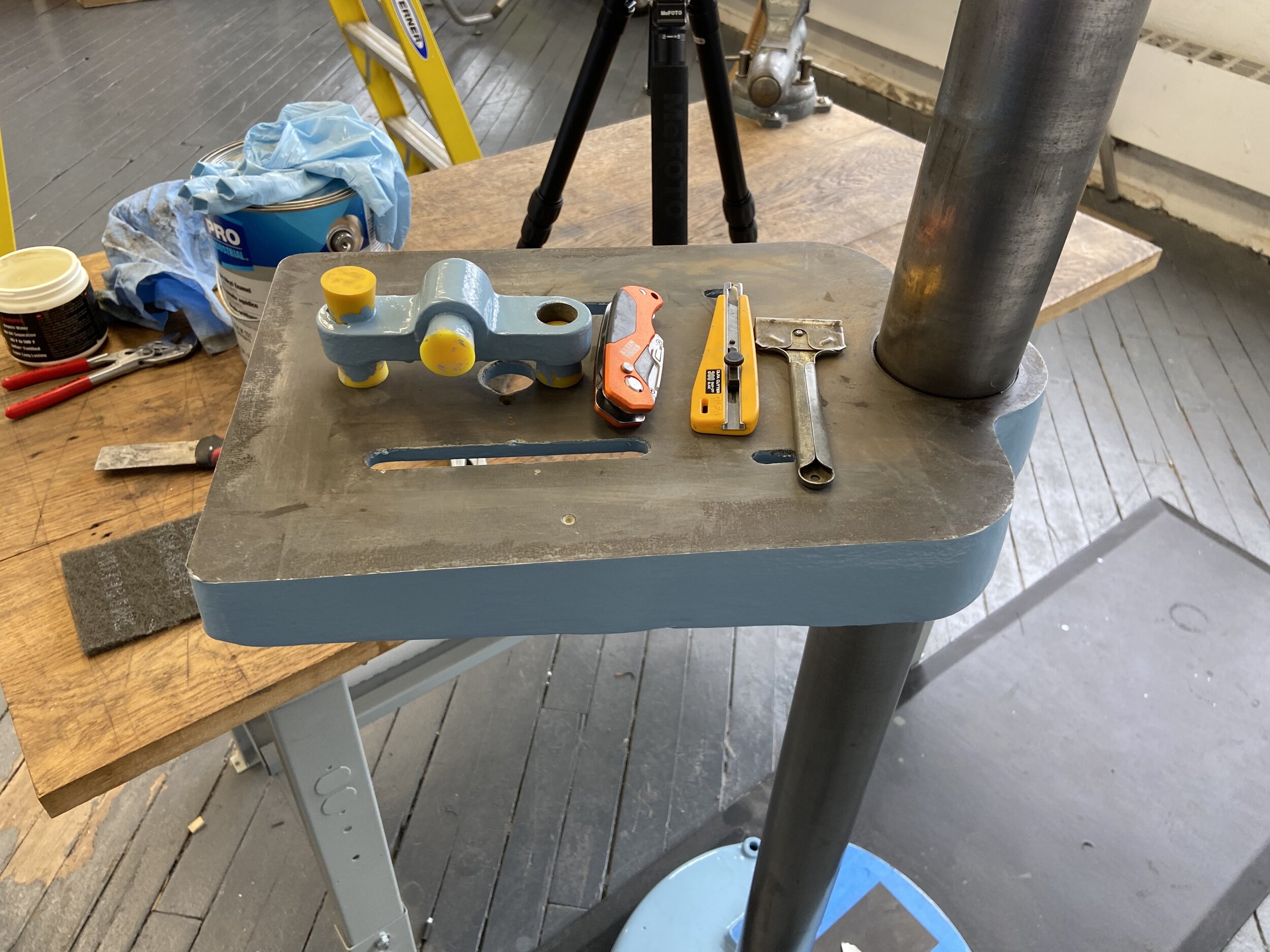
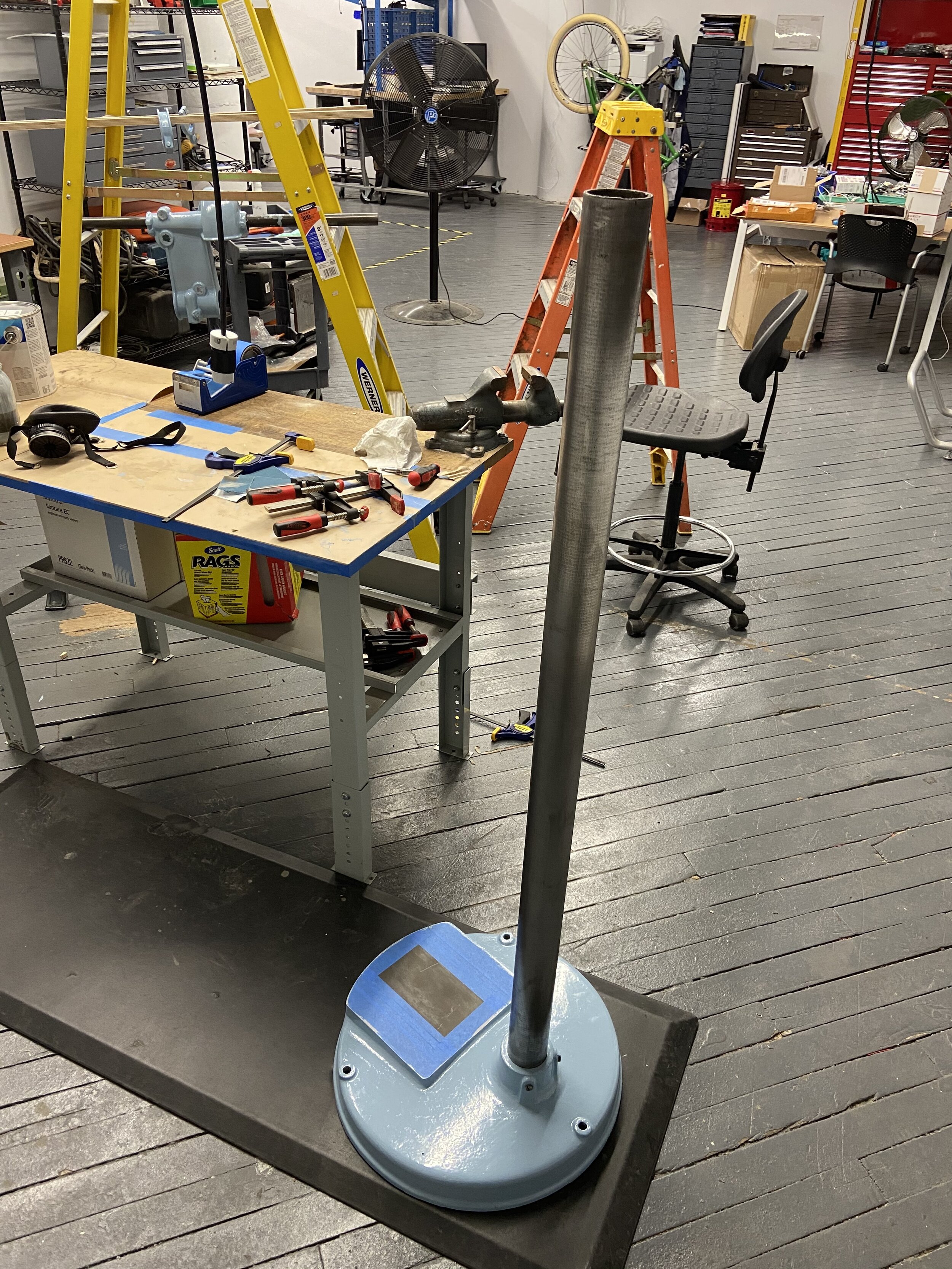
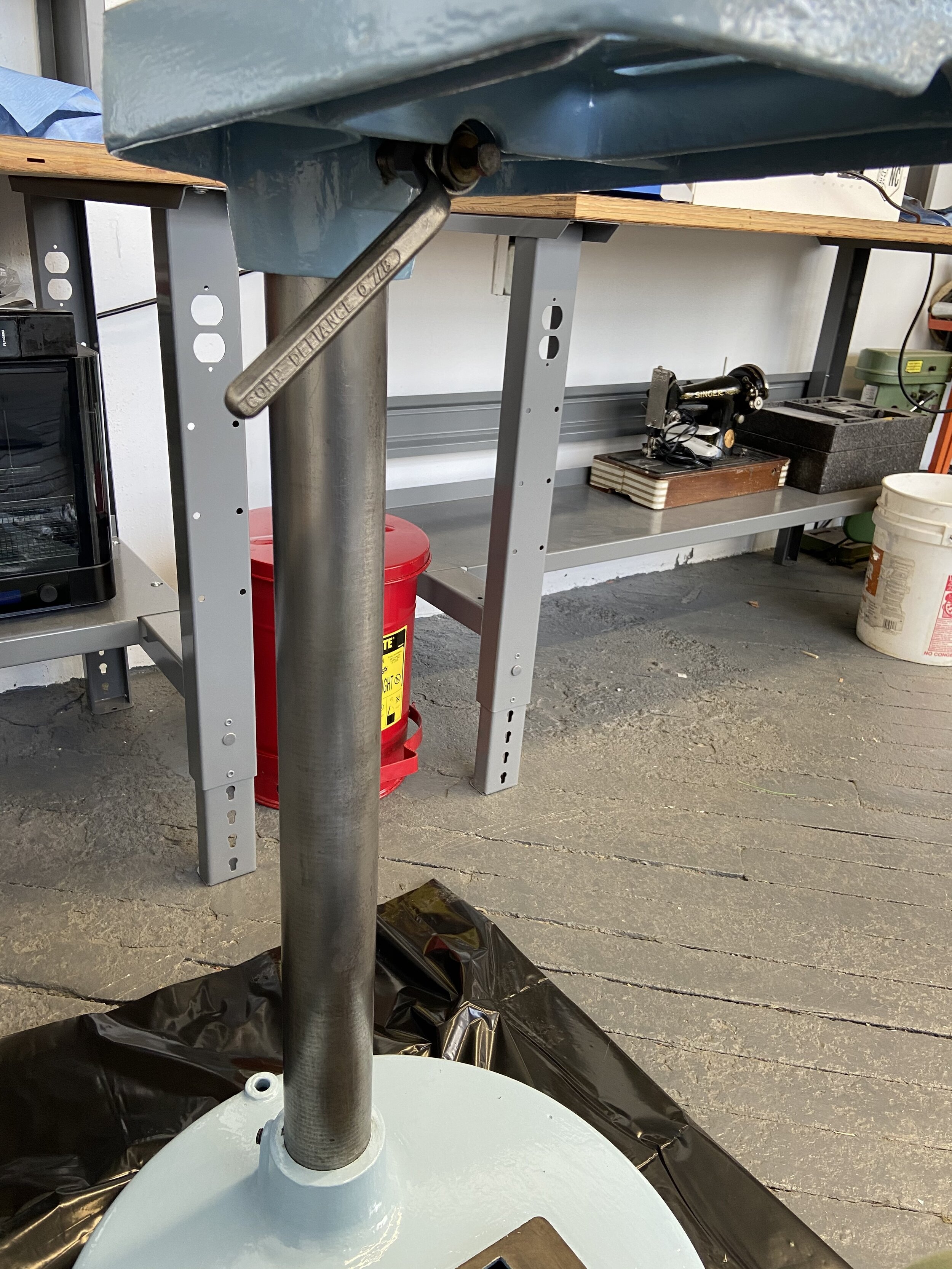
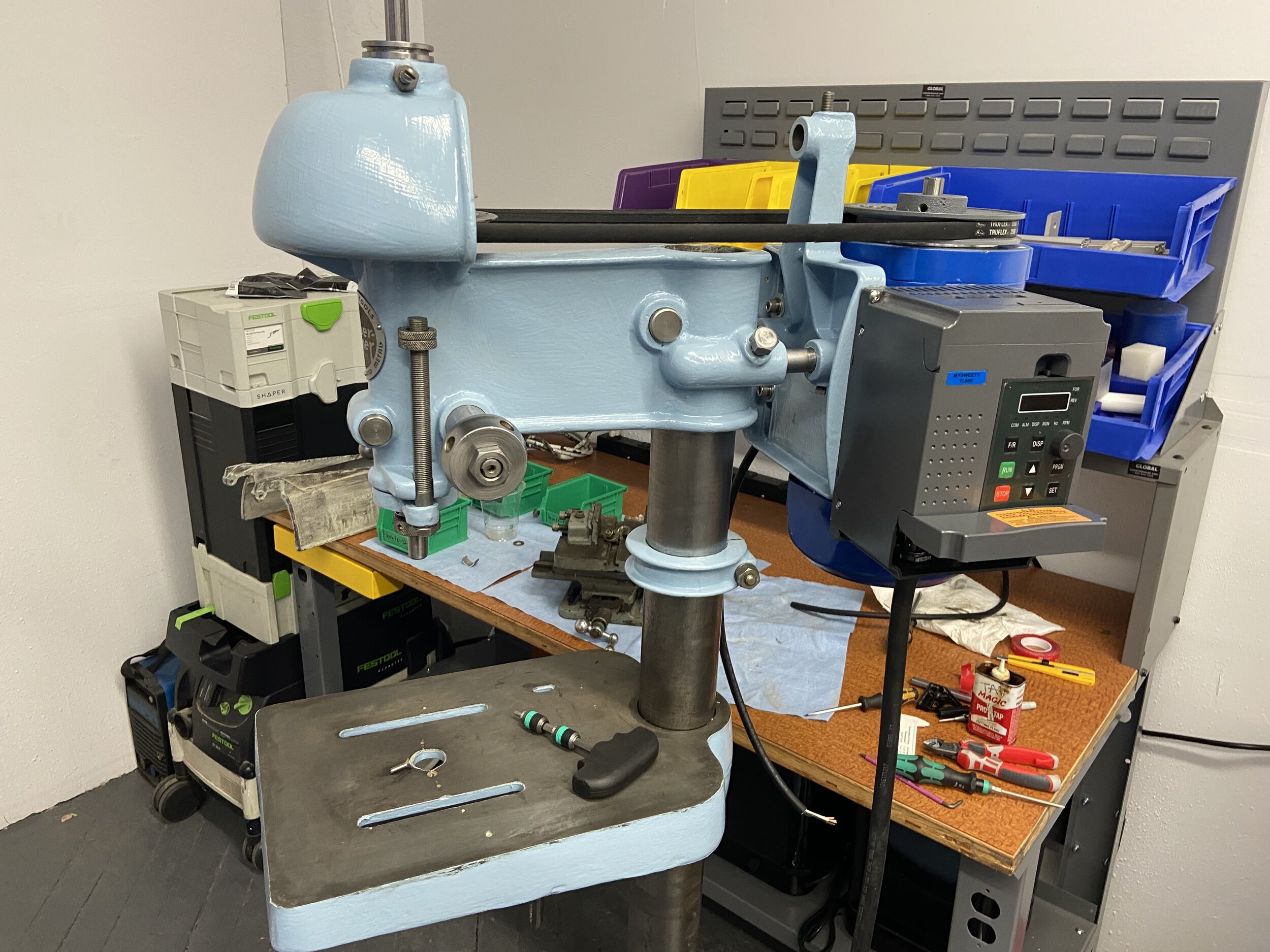
At this point there was one remaining issue: The belt cover. The part, which I bought on eBay, had a crack in it that I wanted to repair and reinforce. I drilled a hole at the end of the crack, cut a piece of low carbon steel to fit on the inside, drilled through the belt cover and tapped the reinforcing plate, and epoxied and screwed the whole thing in place. I then used bondo to smooth everything over, and primed + painted like the rest of the drill press.
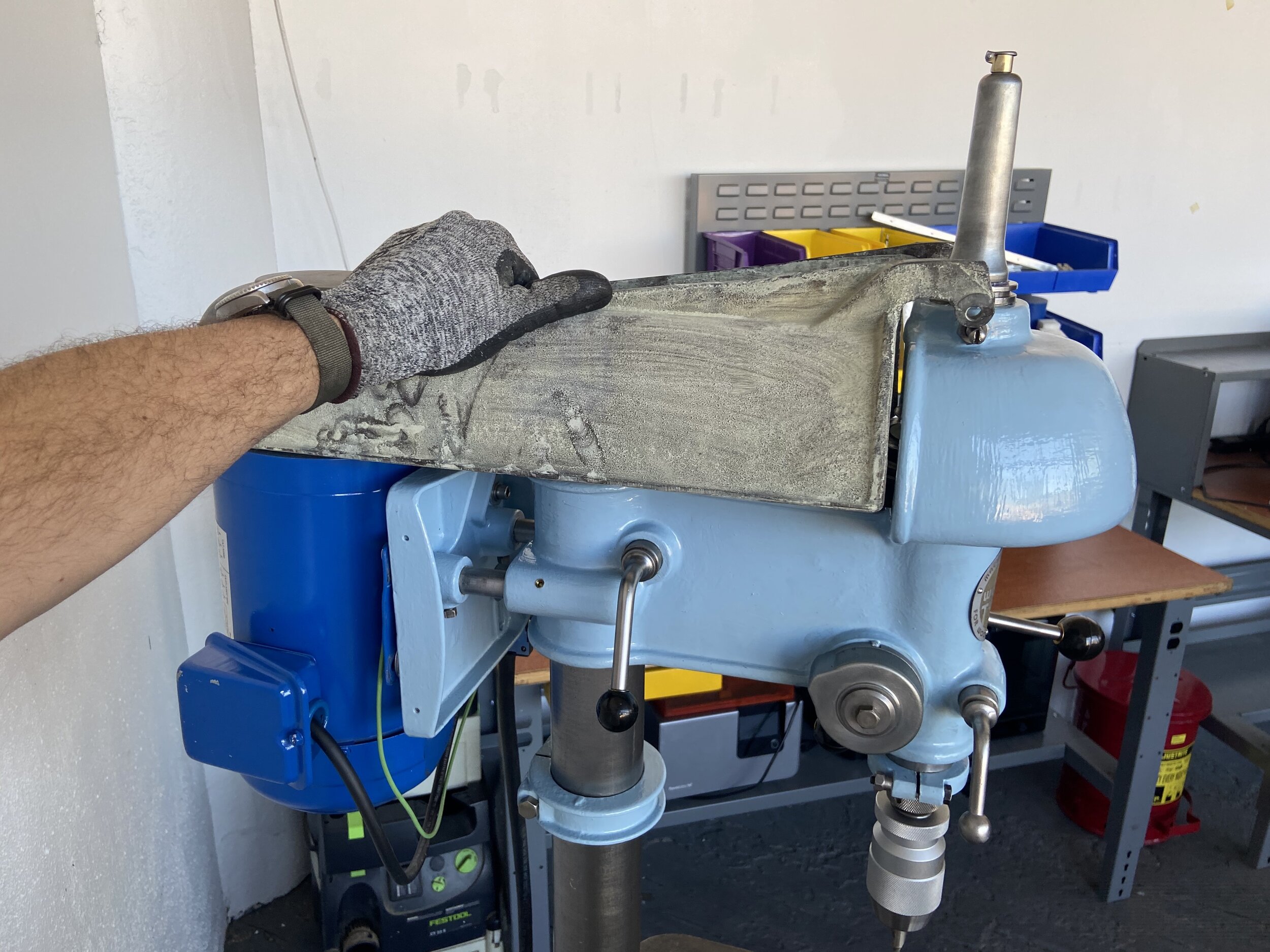
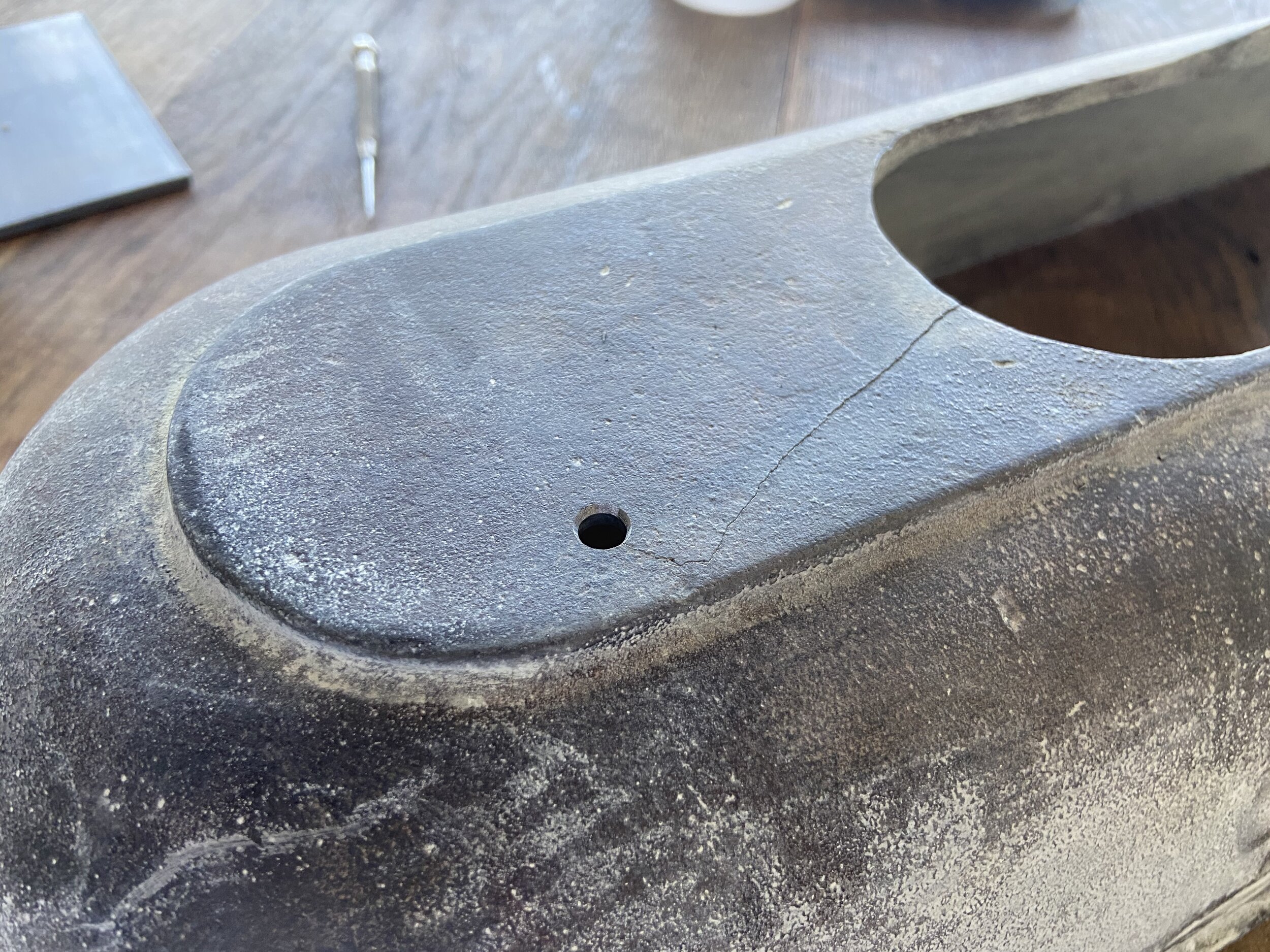
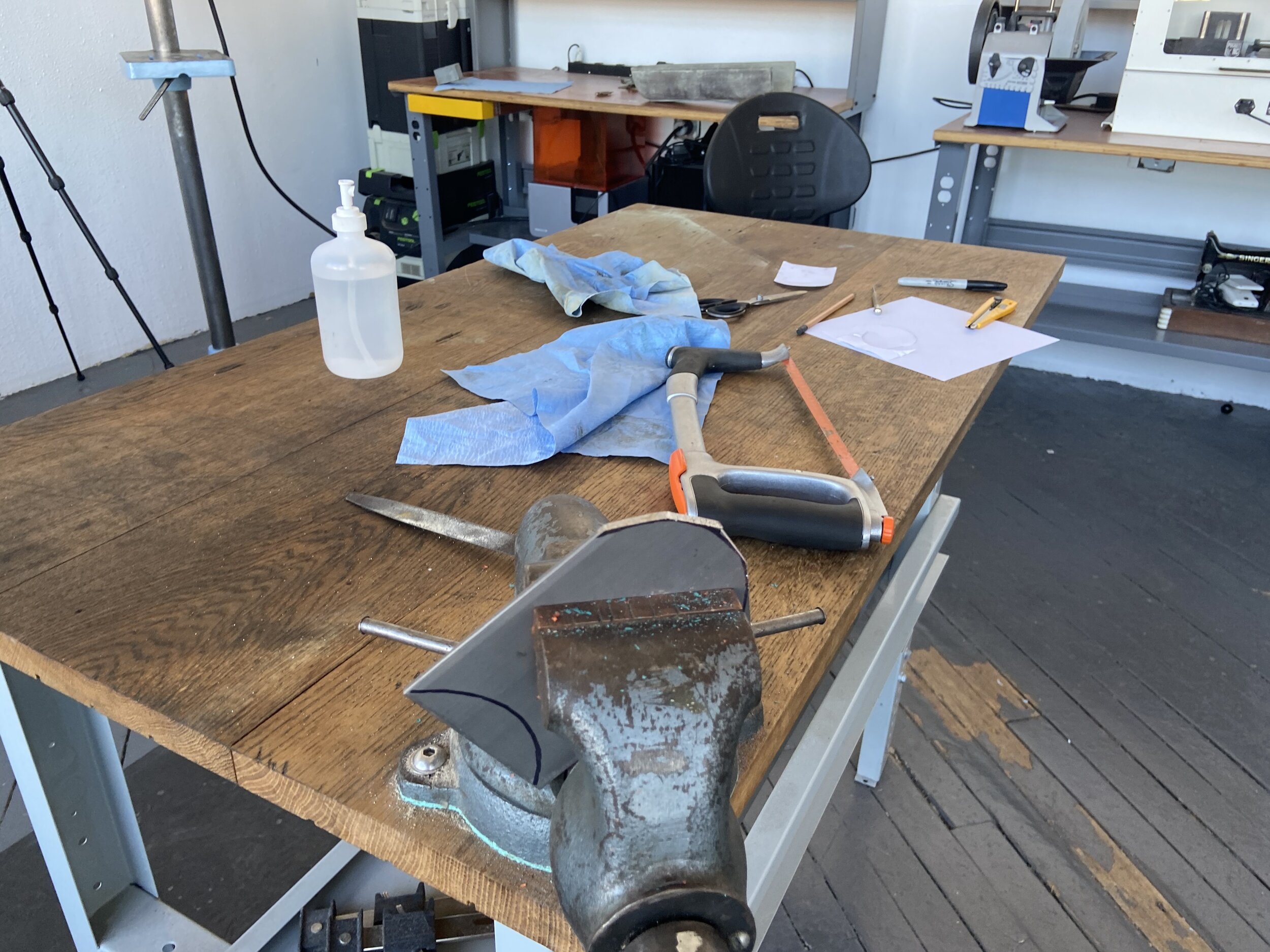
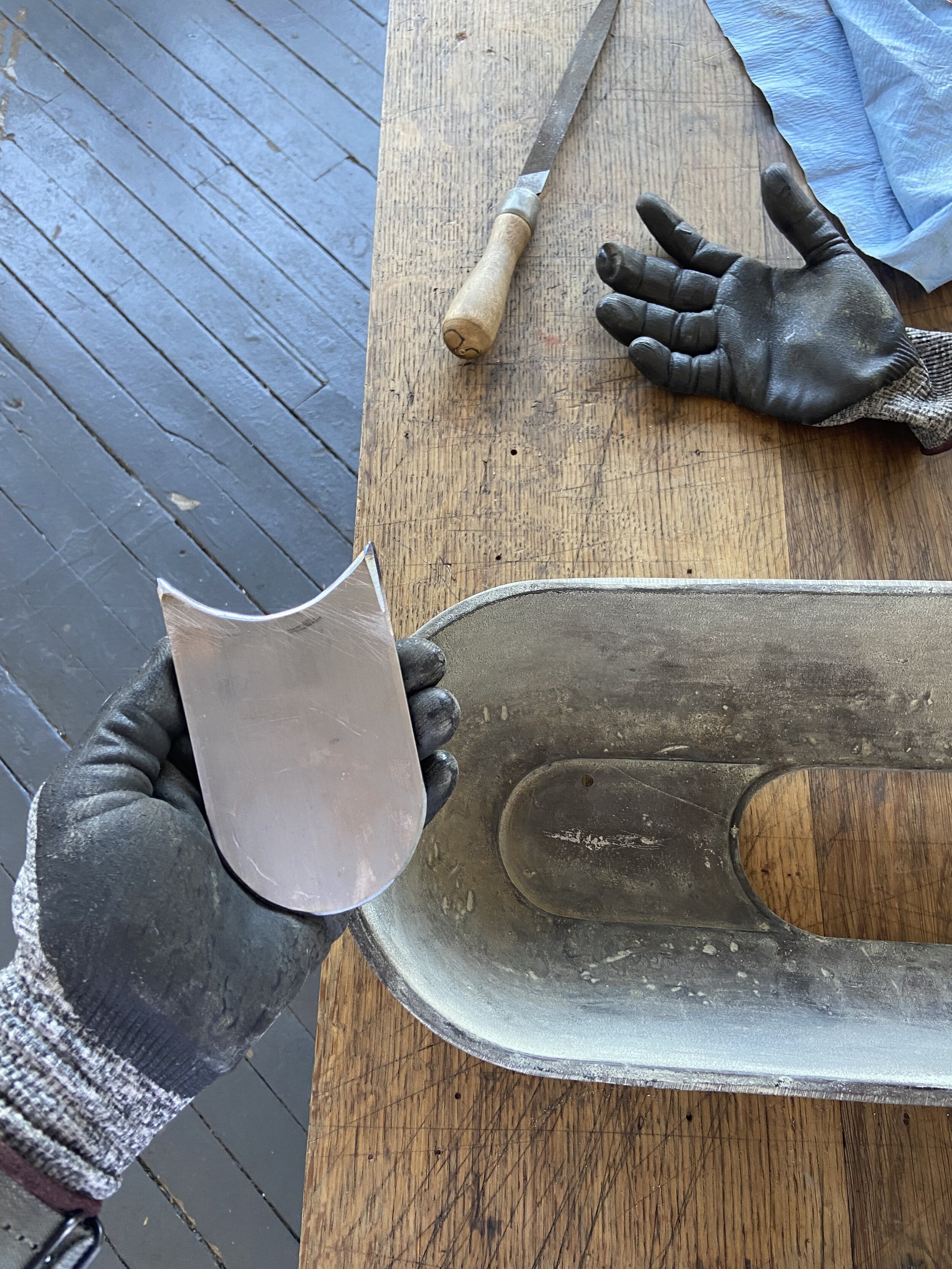
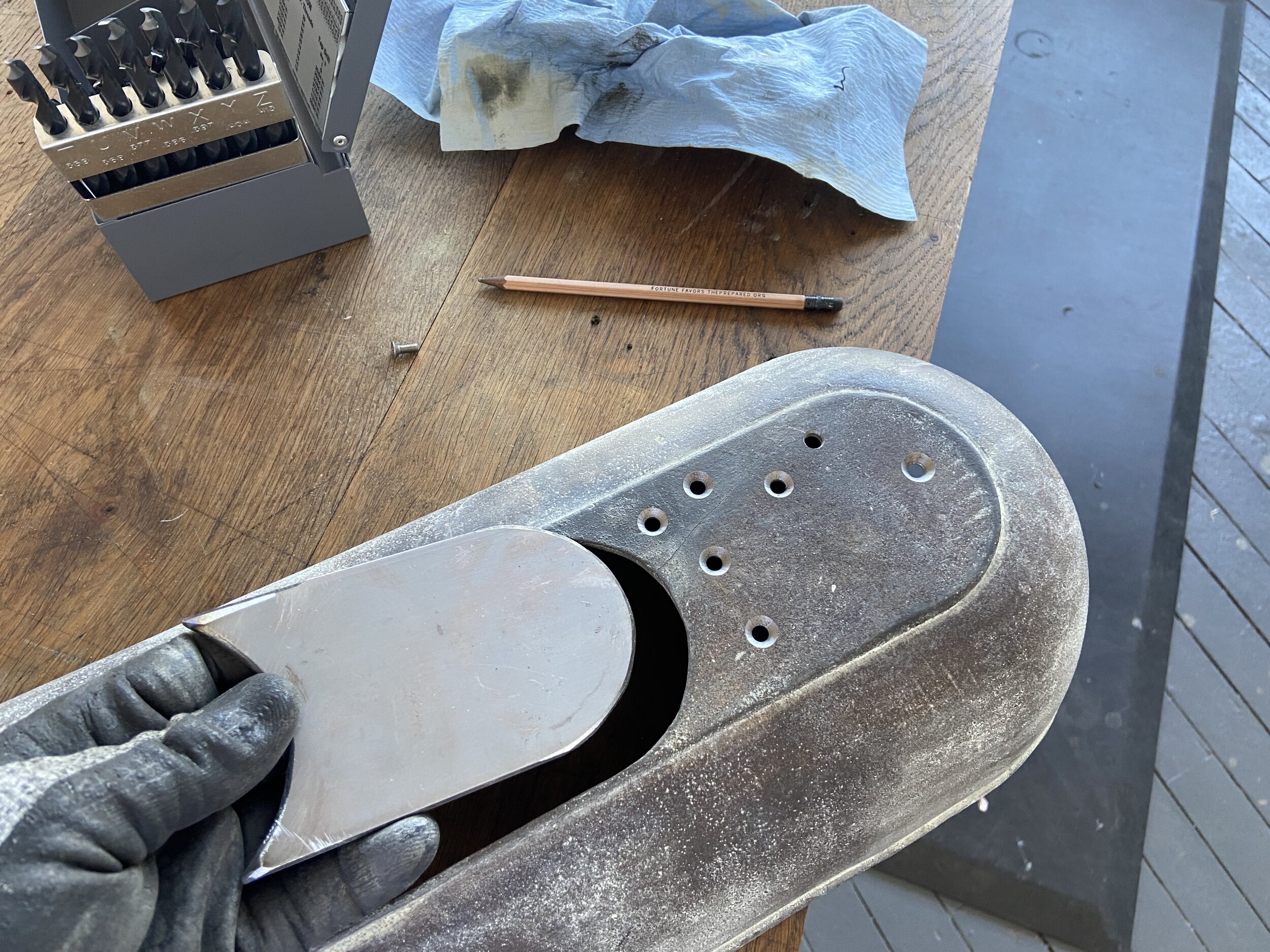
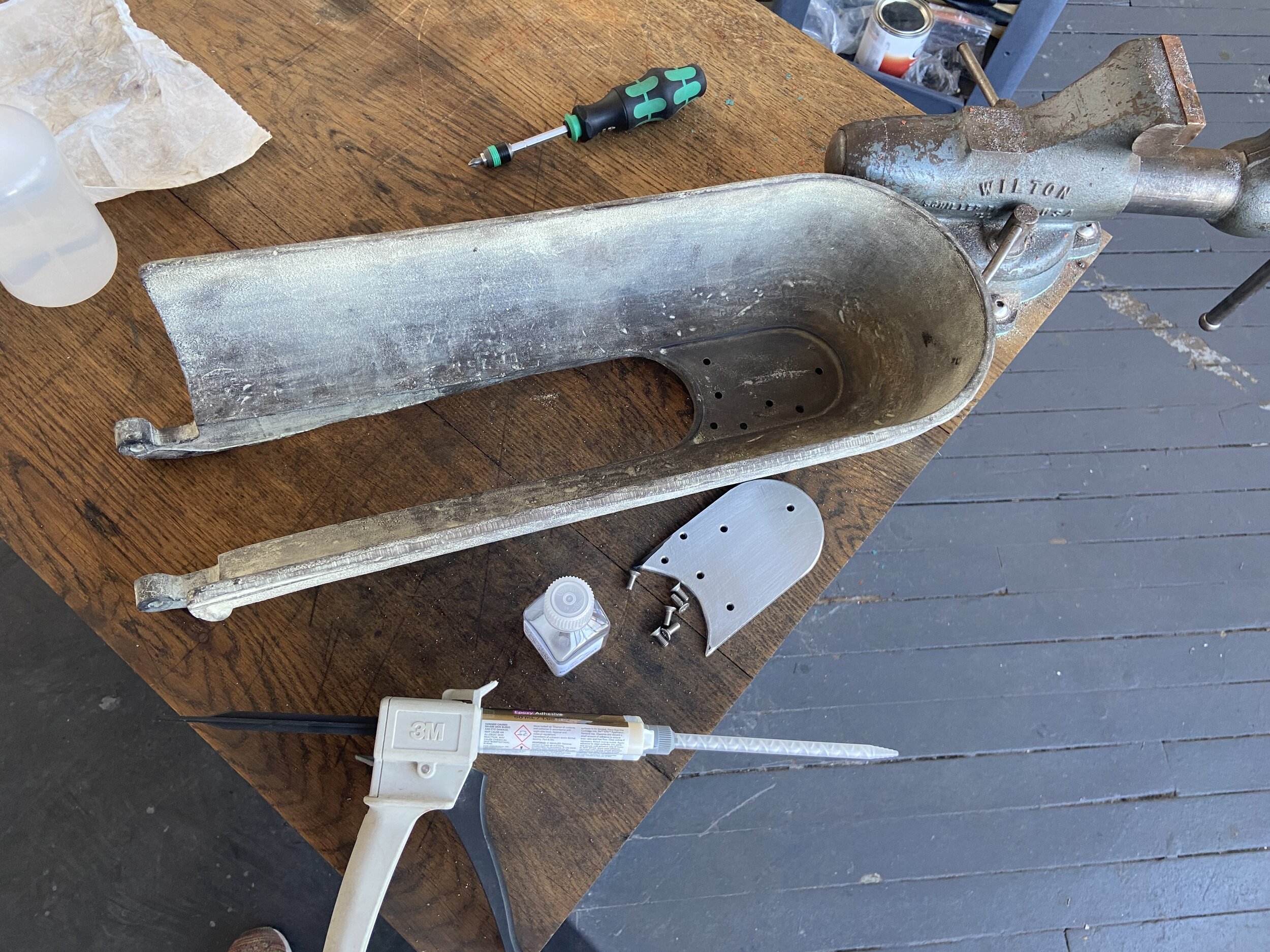
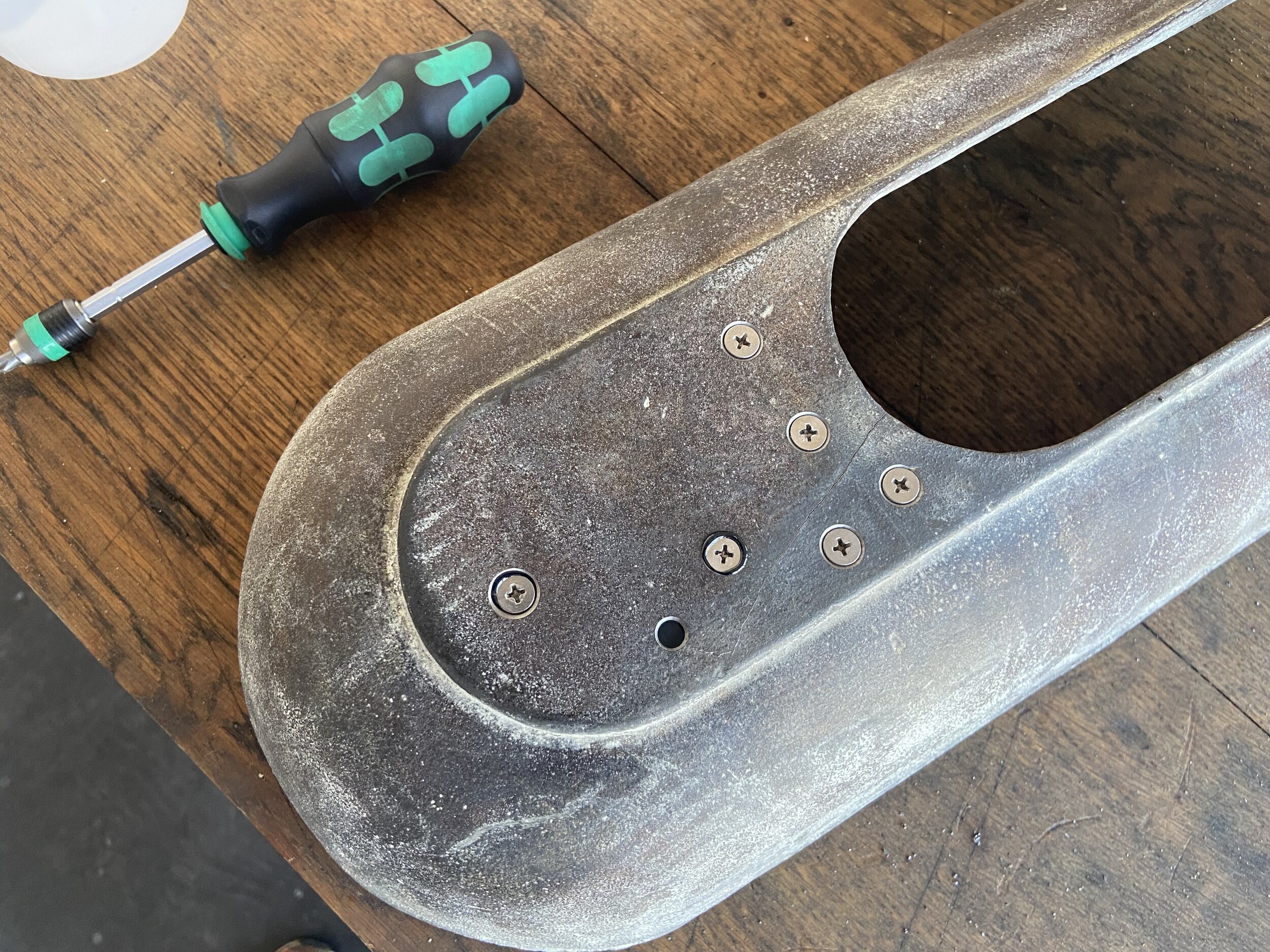
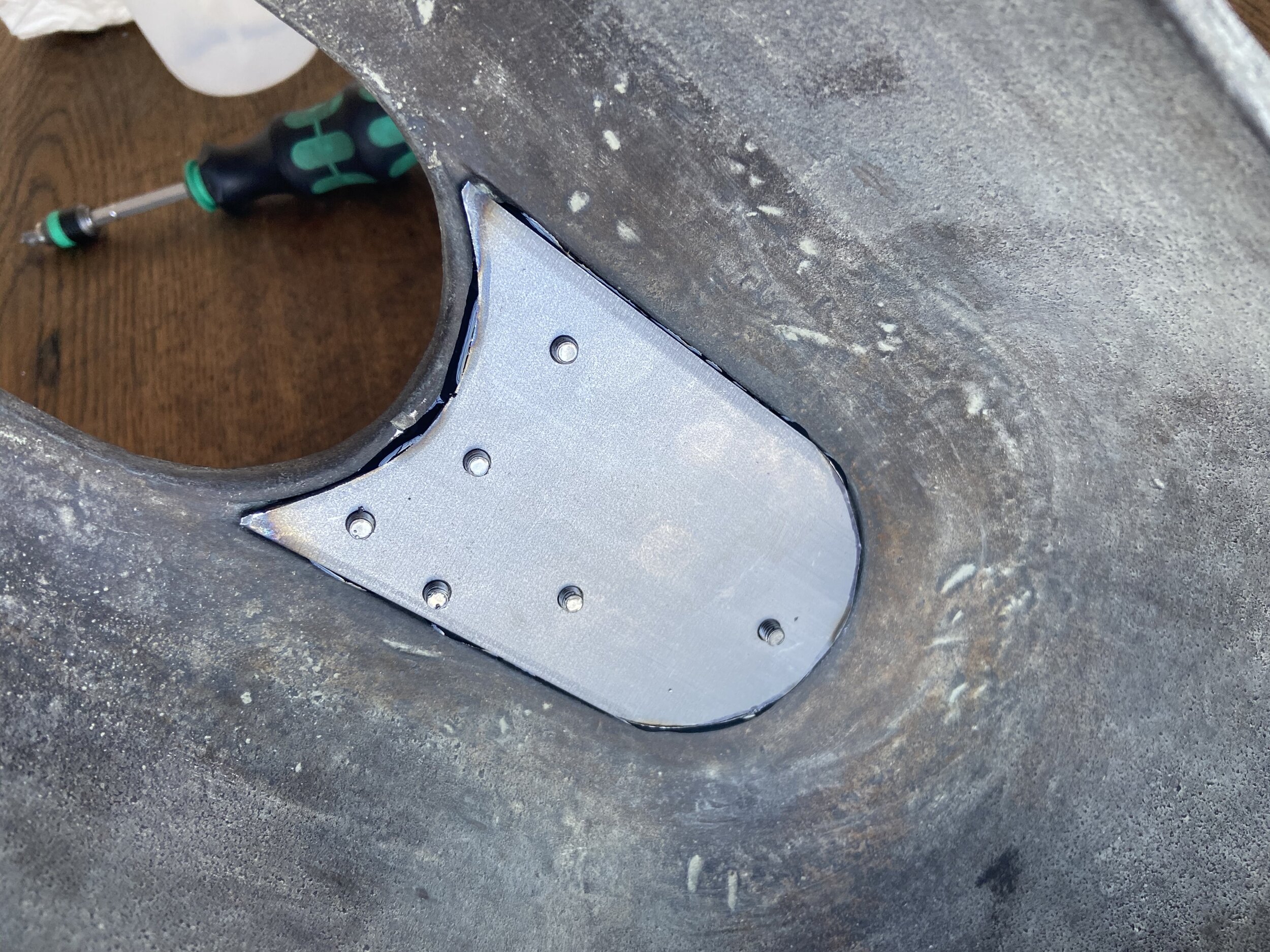
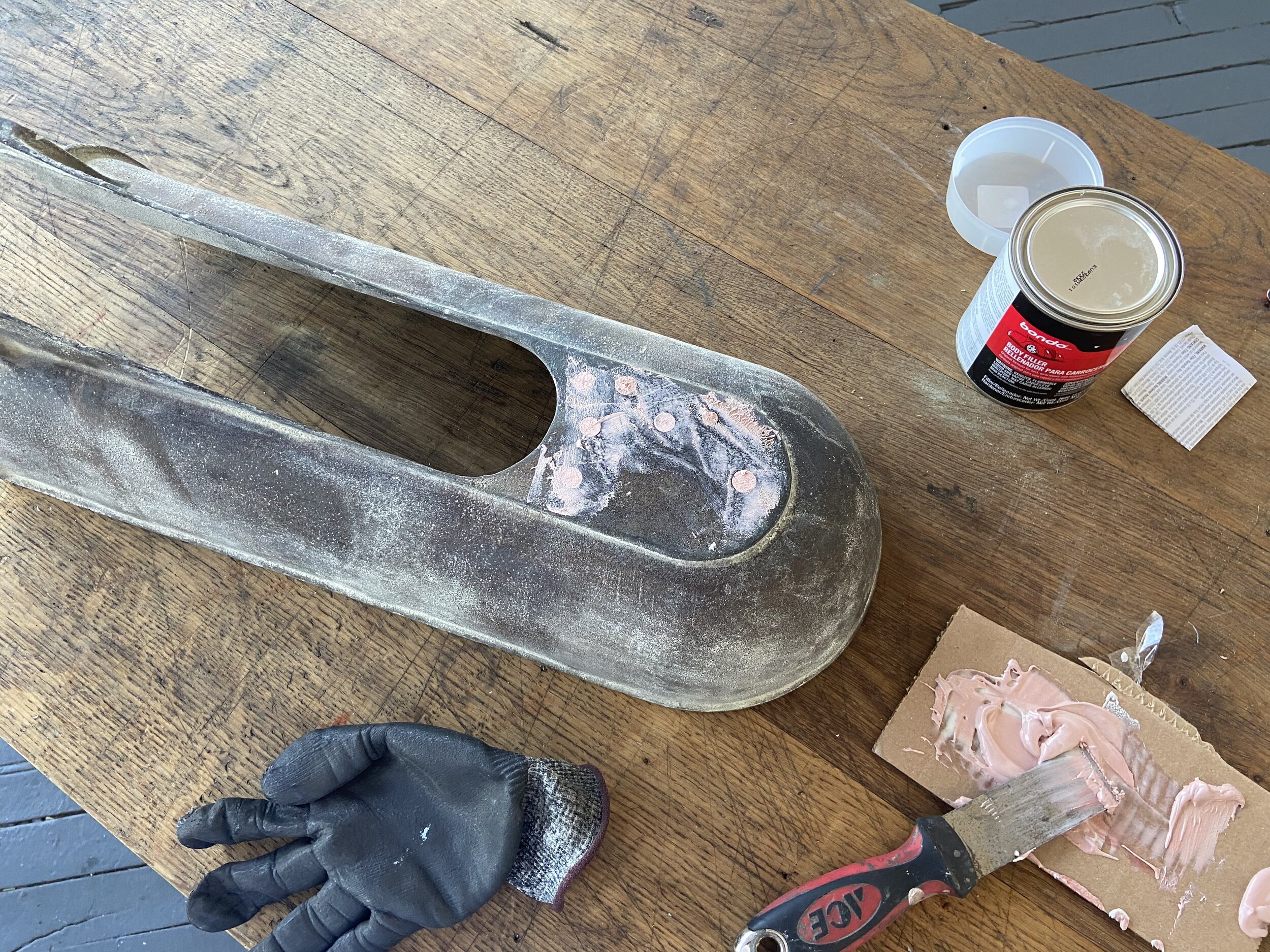
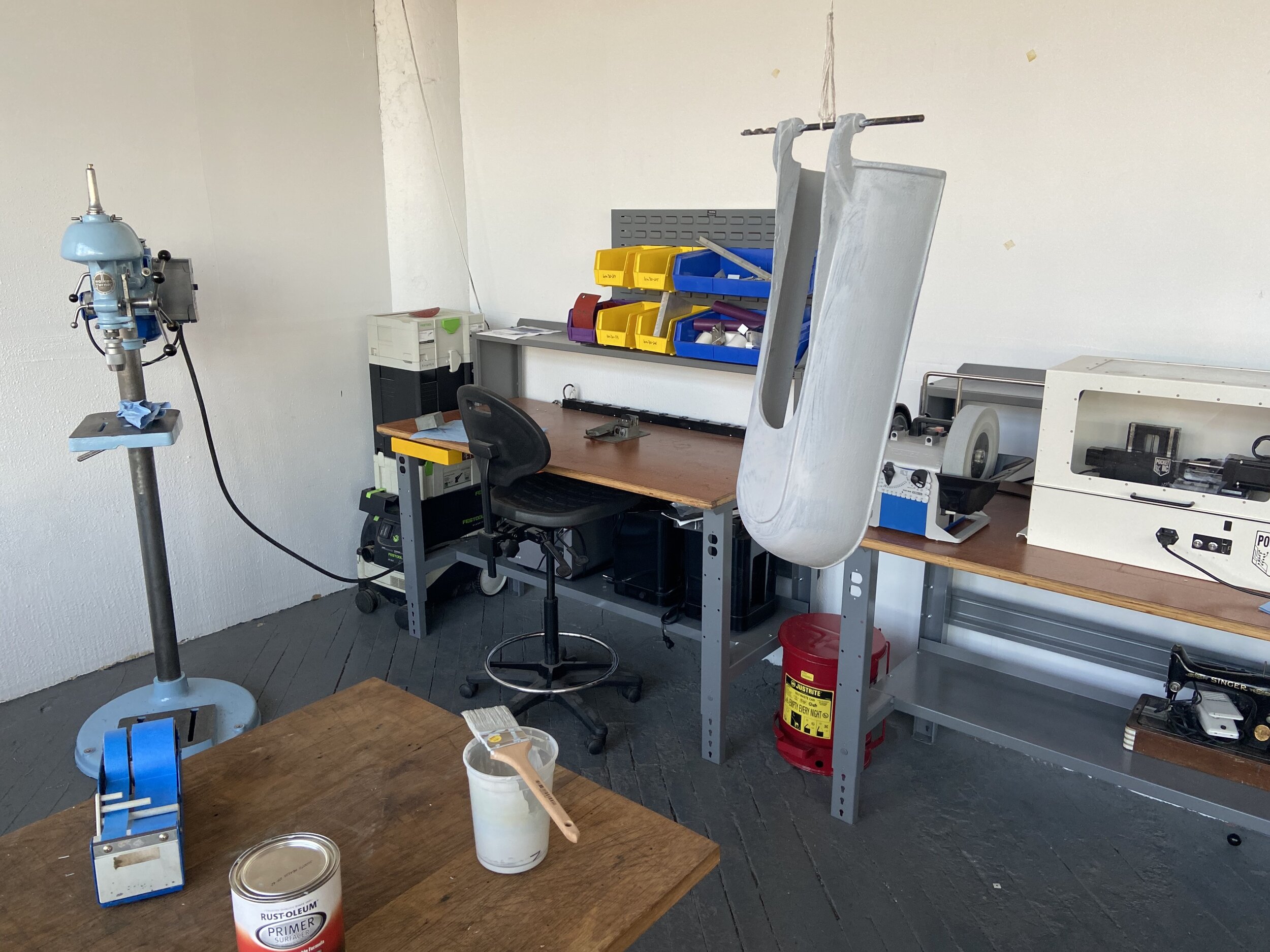
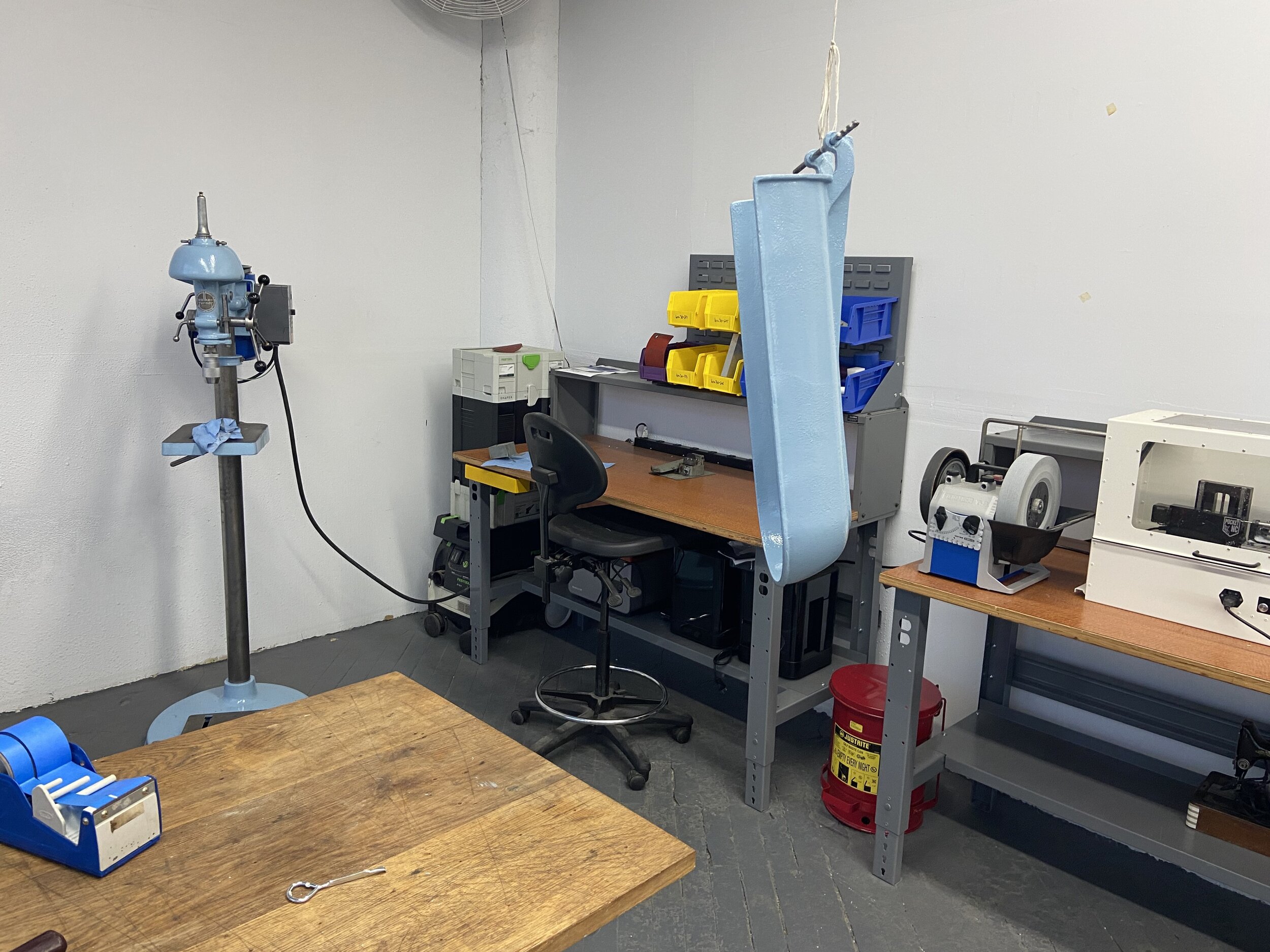
And voila: A working, 80-year-old drill press, painted baby blue and equipped with more or less modern fittings. The result was emotionally restorative, and I’ve got a few key takeaways:
Paint is never the color you think. It may be pretty, but it’s not what you thought it would be.
It really is amazing when replacement parts are easily available 80 years later.
If you can avoid repainting something, you should. A new paint job won’t turn out that nice, and it’ll take you forever to finish.
This Walker-Turner isn’t the drill press I might have wished my life on, but it’s way more of a drill press than no drill press at all. In other words: It’s pretty nice to have it working.