In October, I visited a Taiwanese bicycle fork builder with Brilliant Bicycles. The shop was in a totally rural area; the vast majority of land usage was rice paddies. These photos are taken from directly in front of the shop:
The building on the far left is the fork shop's storage area.
That's the fork shop on the far right.
The shop itself was a couple thousand square feet. It was rectangular, and had a single gable roof. The gable end to the east had a huge open door, and there were fans everywhere to maintain airflow; it was hot inside nonetheless. On the other end the shop adjoined to what I presume were office and a small apartment area.
A few notes:
- Fork legs came in straight. Unicrown fork blades were bent in house from straight legs.
- The dropout end of the fork blades were swaged, slotted & brazed first. I don't have any pictures of the process but it was pretty cool - the brazing especially. They had a big turntable, maybe 6 feet in diameter and with a few dozen fixtures around the perimeter. Each fork blade had powdered flux + brass filler shoved down from the top, and the dropouts were fluxed with paste. The whole assemblies snapped into the machine and sat on an incline, so that the dropouts were on the perimeter and the blades angled up and to the center of the turntable. Then the whole thing was spun very slowly, and a single flame at the perimeter would heat one of the dropouts up until the brass melted and flowed, and then the turntable would advance to the next dropout.
- Then the blades would be assembled into crowns. The whole crown was brazed at once with the tips pointing up (video below).
- Then the forks would be raked. That machine was really cool too - there's a photo below.
- Then the crowns would be drilled & counterbored on dedicated fixtures. They had two or three small drill presses set up to do this, and they were running full time while we were at the shop.
- Alignment was awesome. The guy was really quick with the whole process, and it was a fluid and rhythmic operation. Video below.
- It looked like they did mostly lugged forks, but that could have been just the time we visited - there was a TIG setup there, but it wasn't being used while we were there.
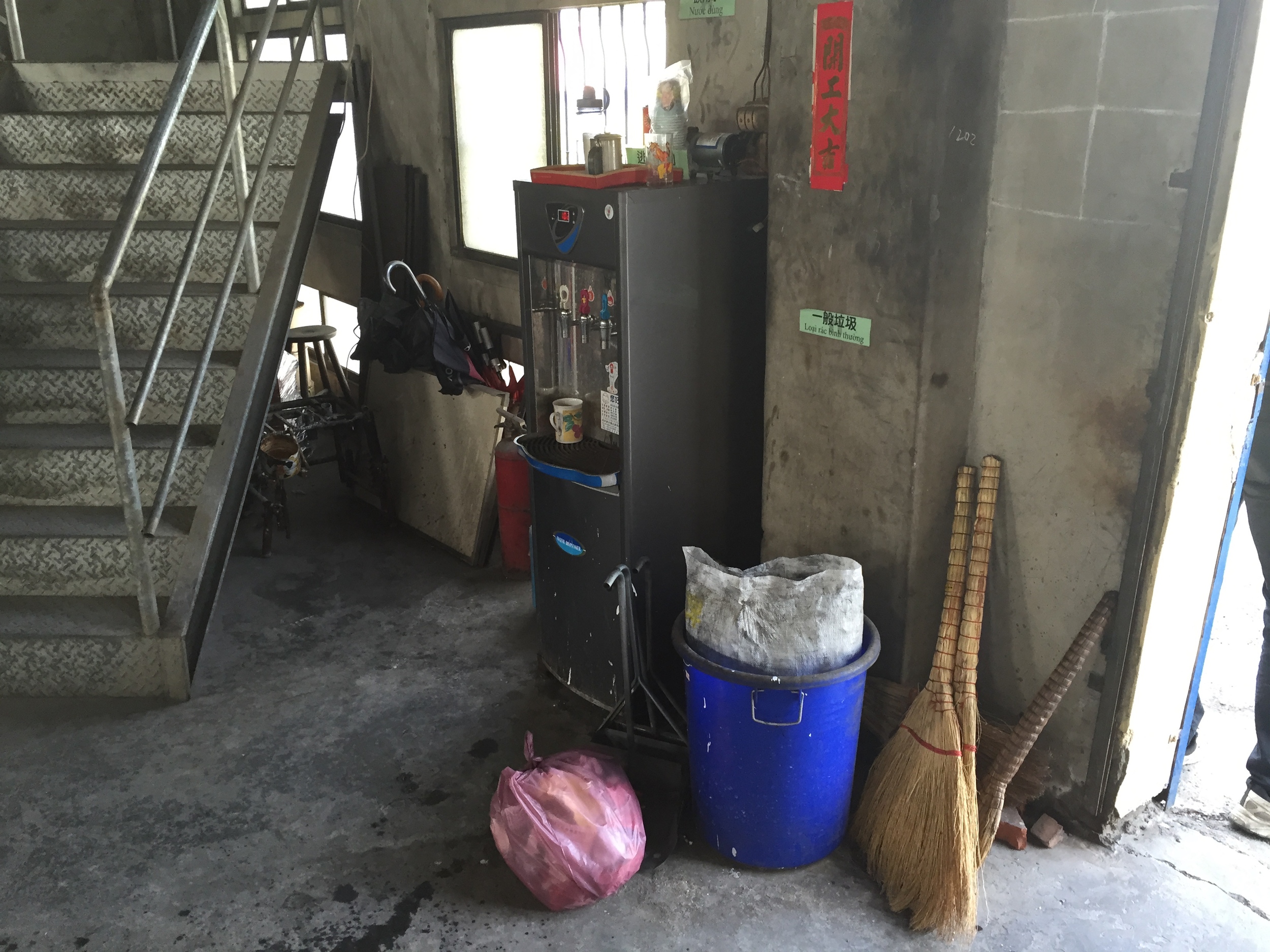
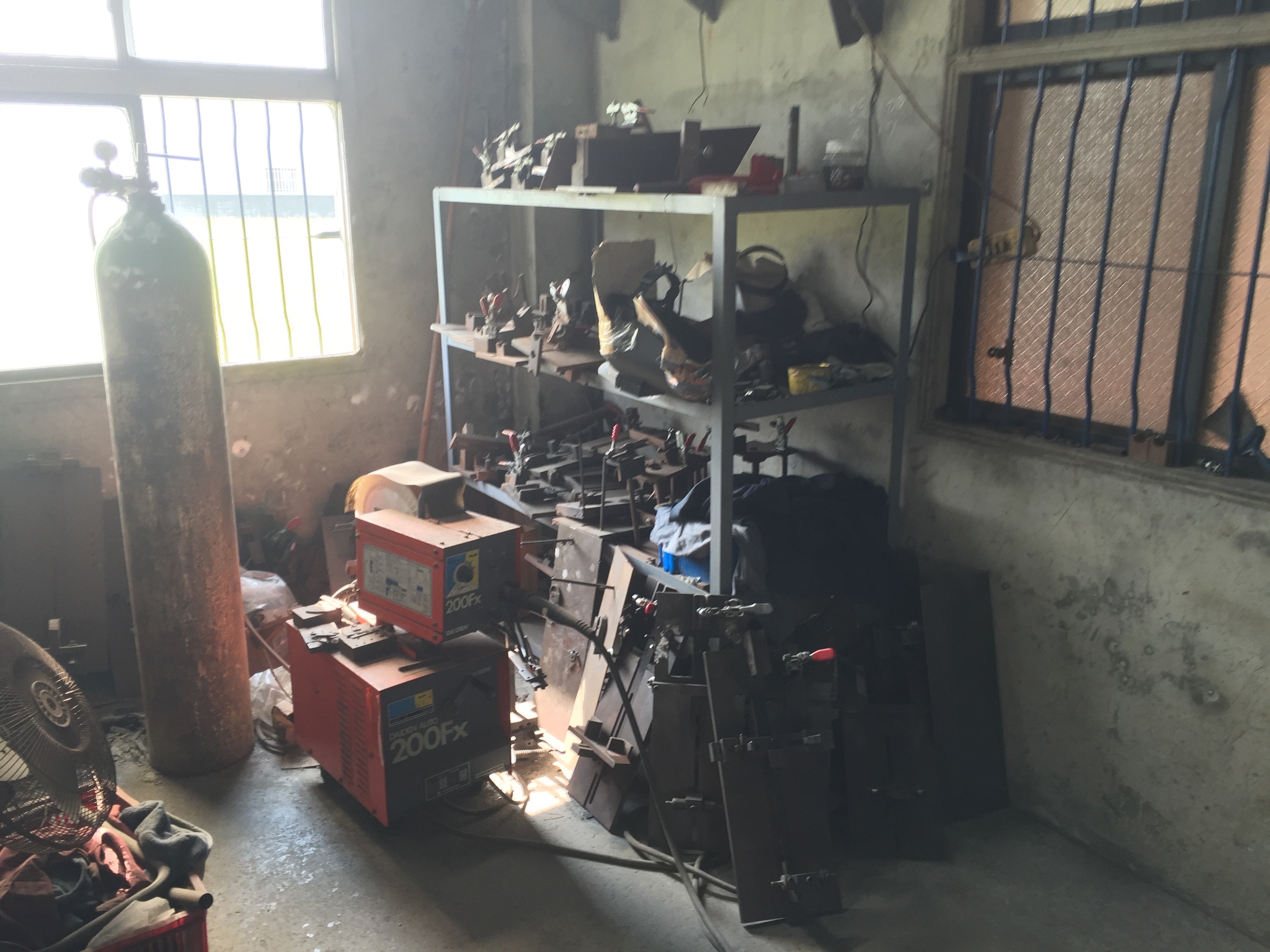
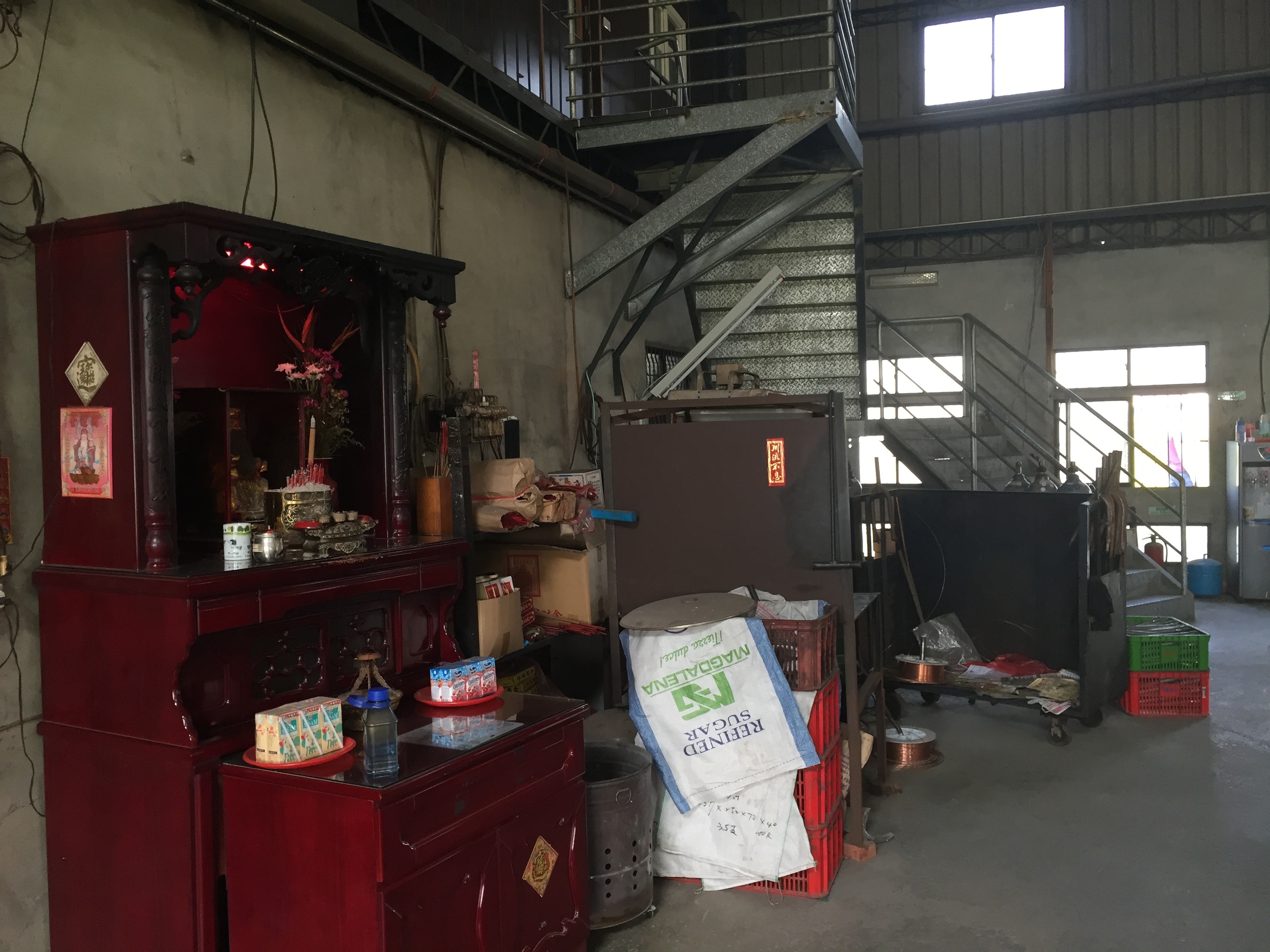
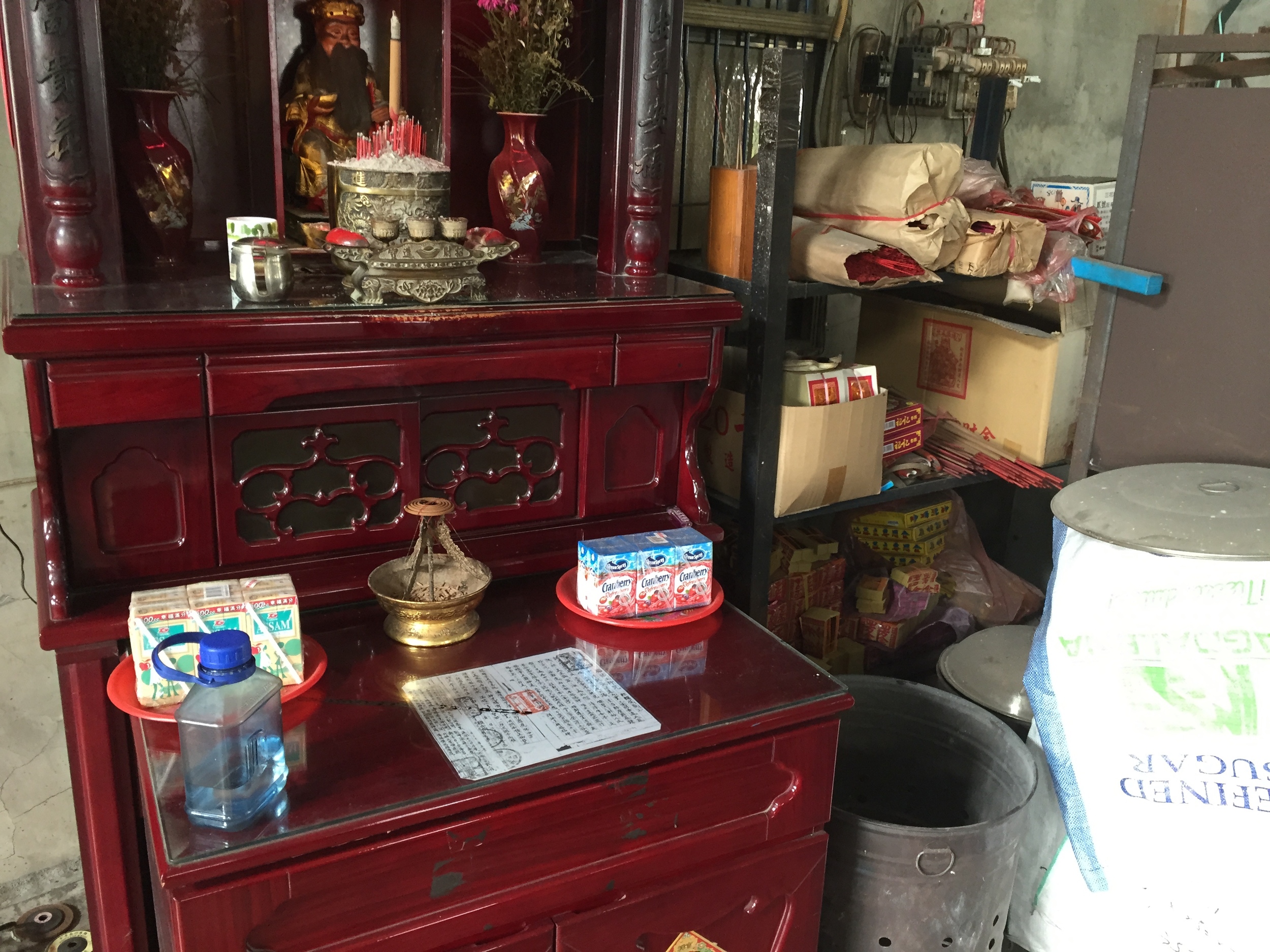
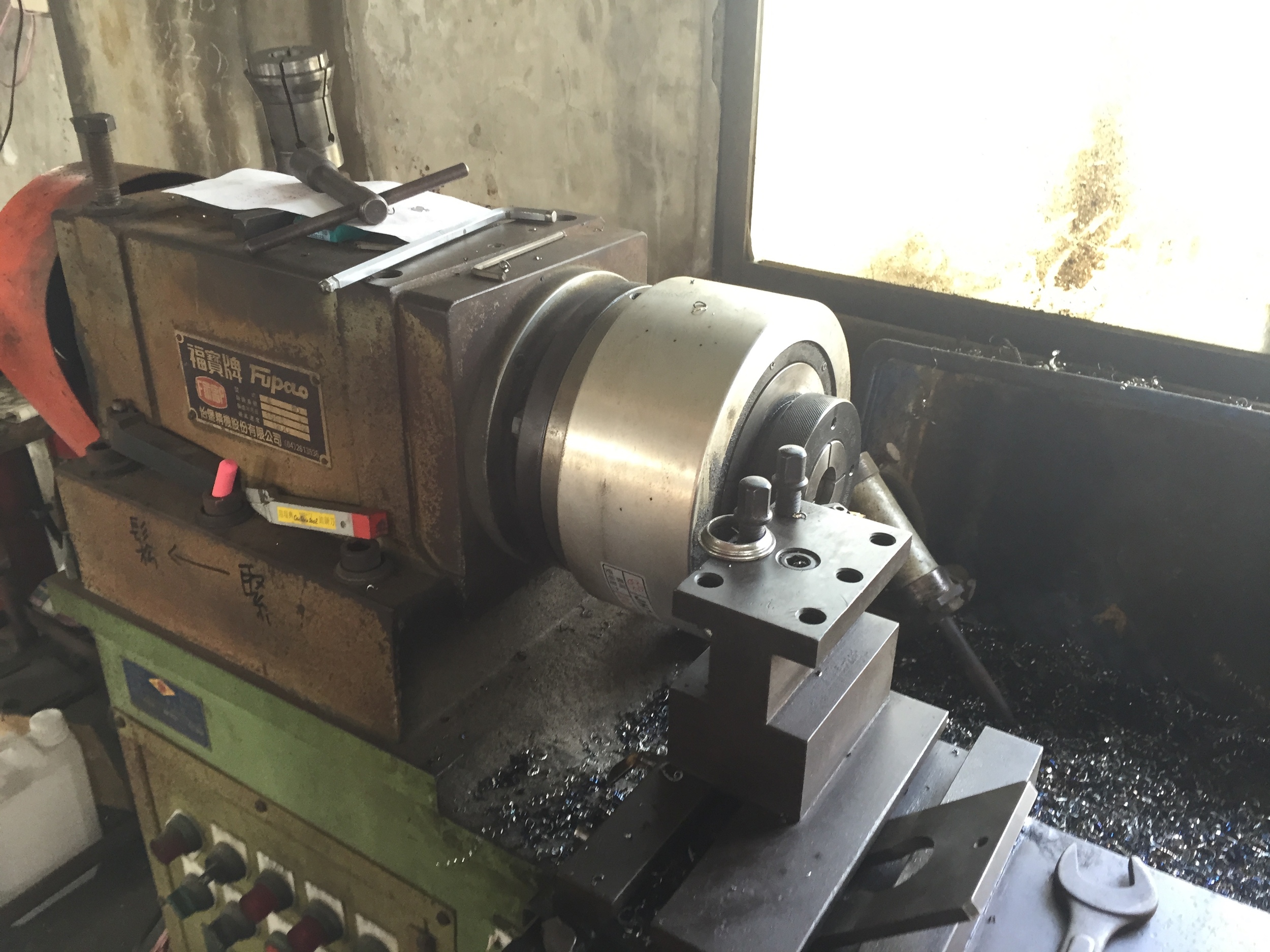
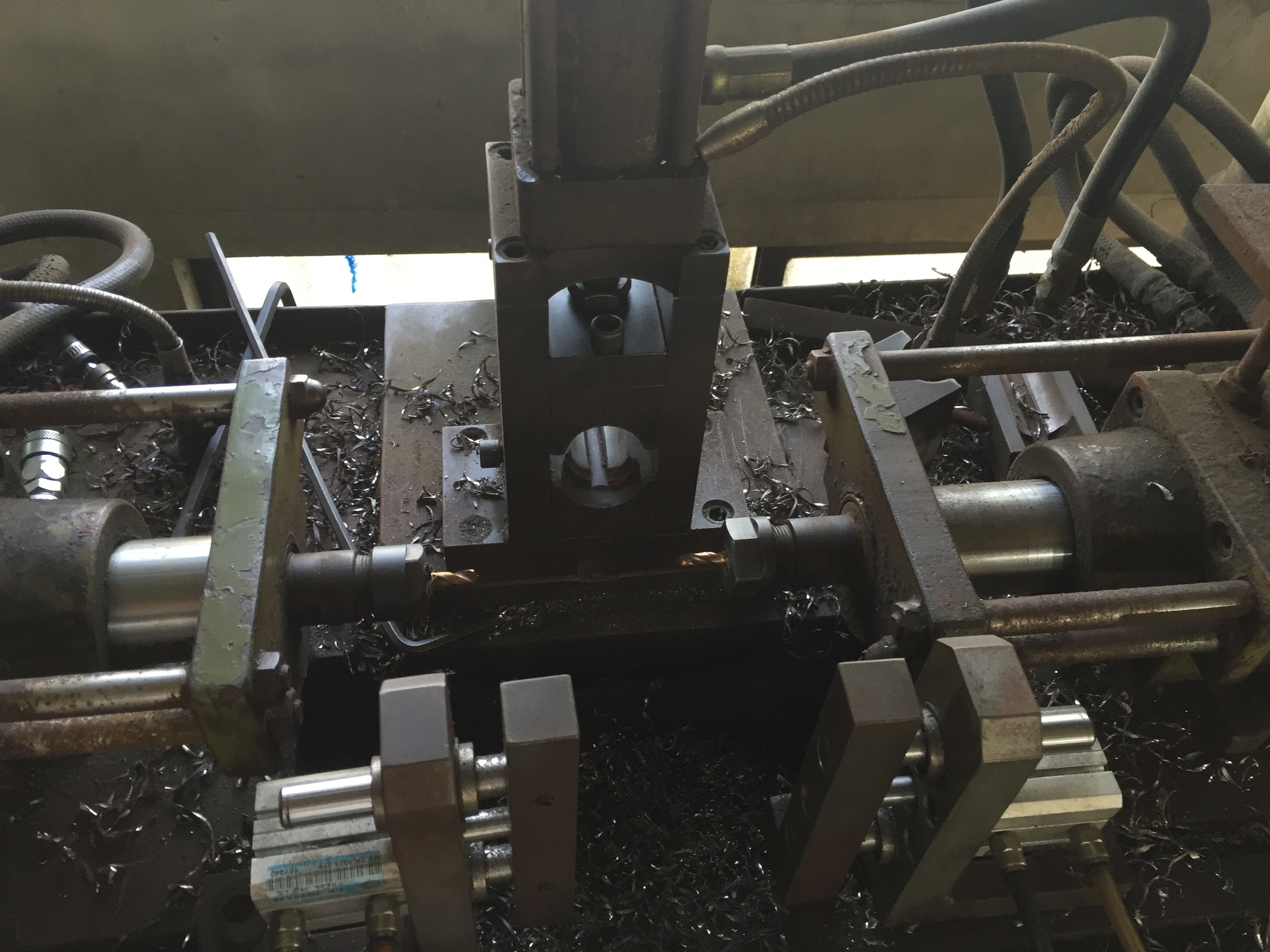
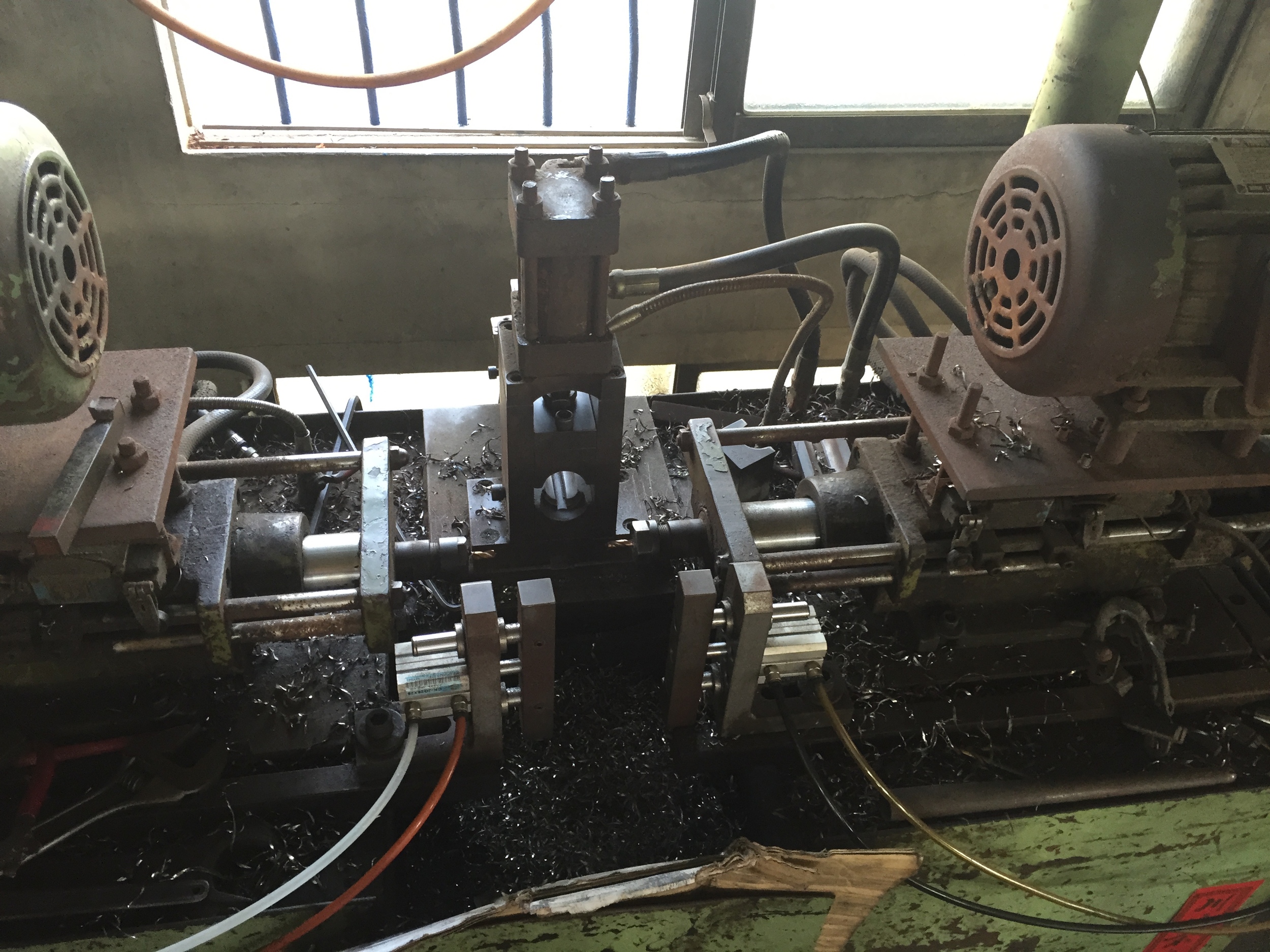
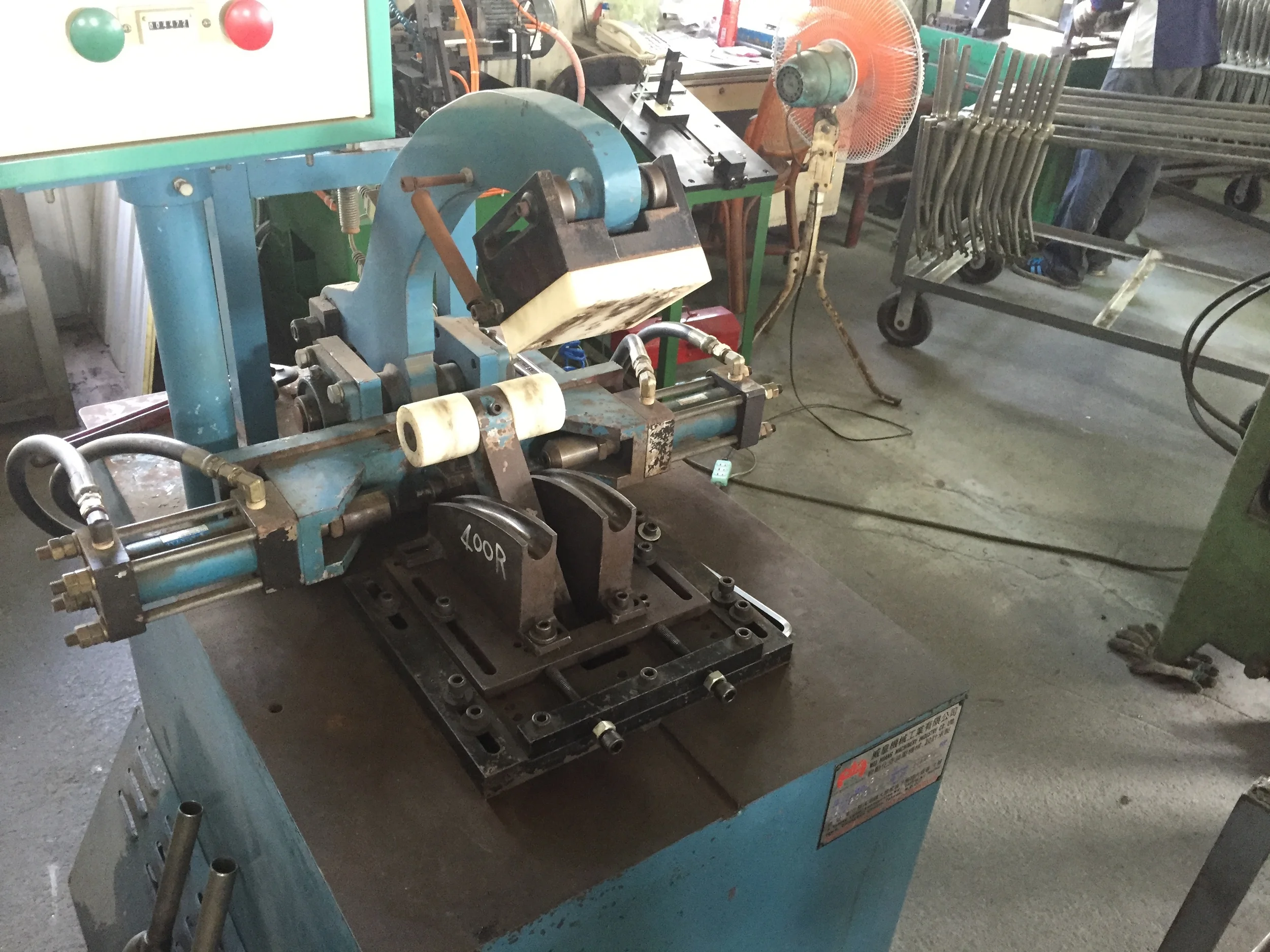
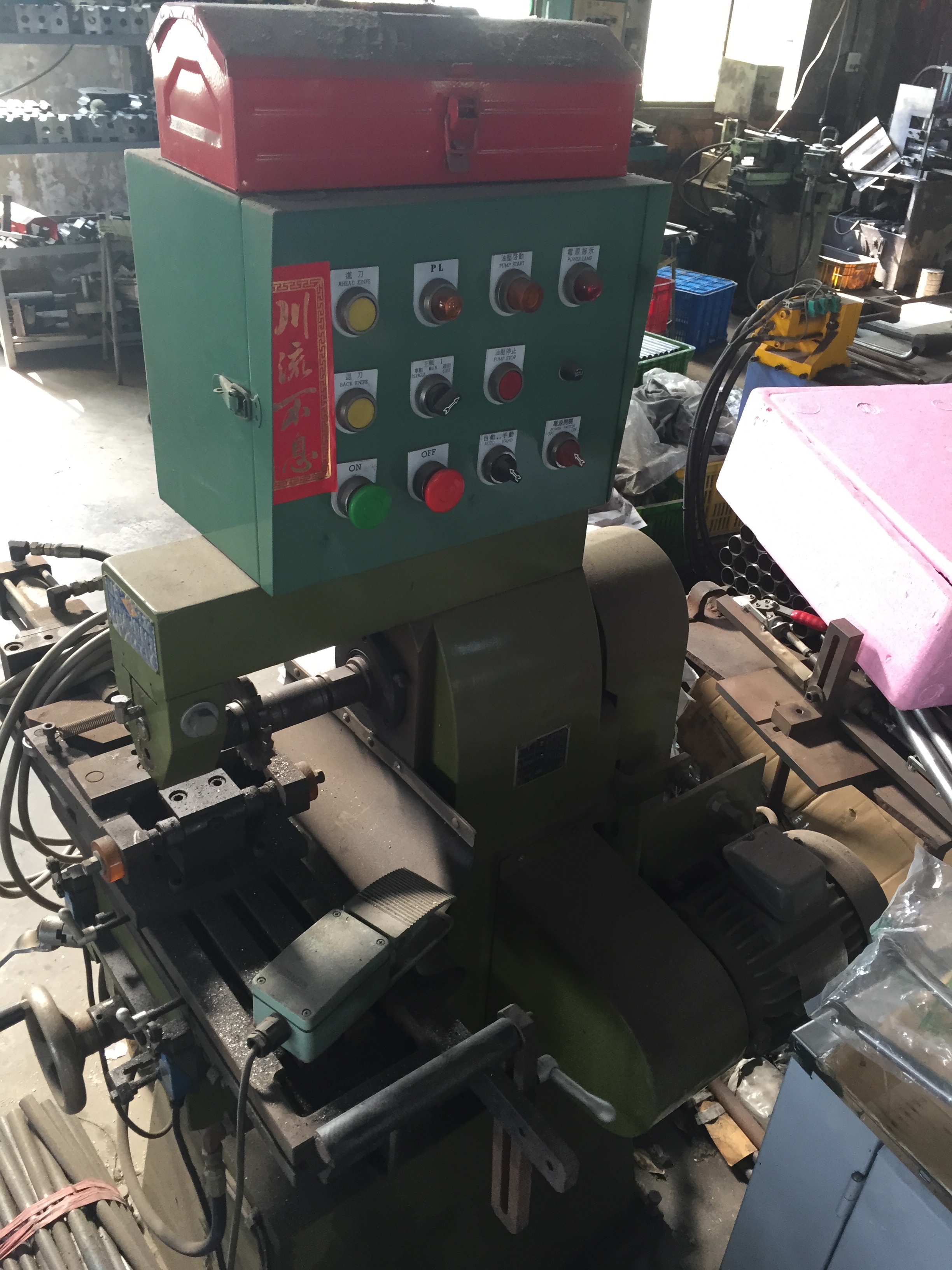
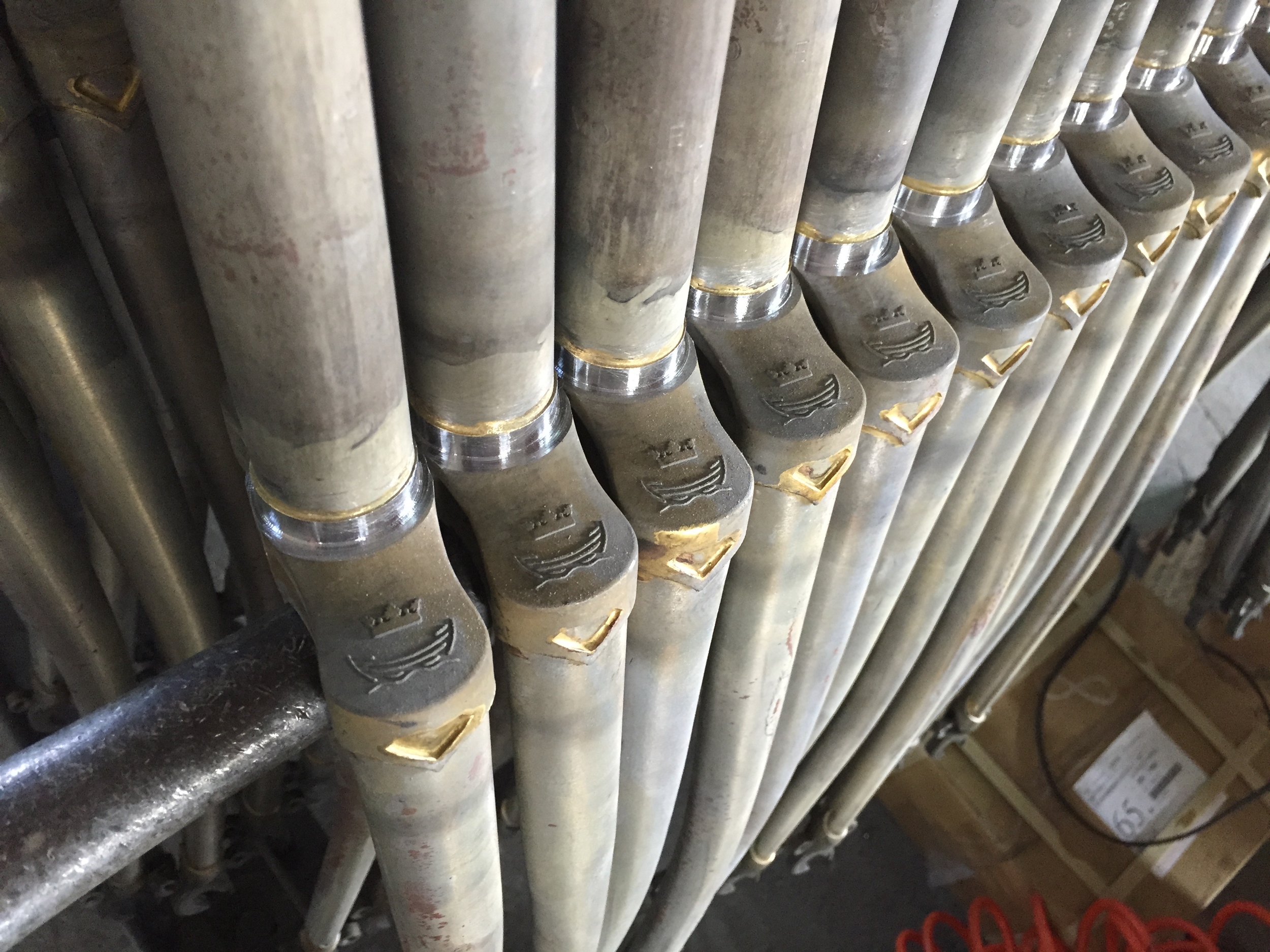
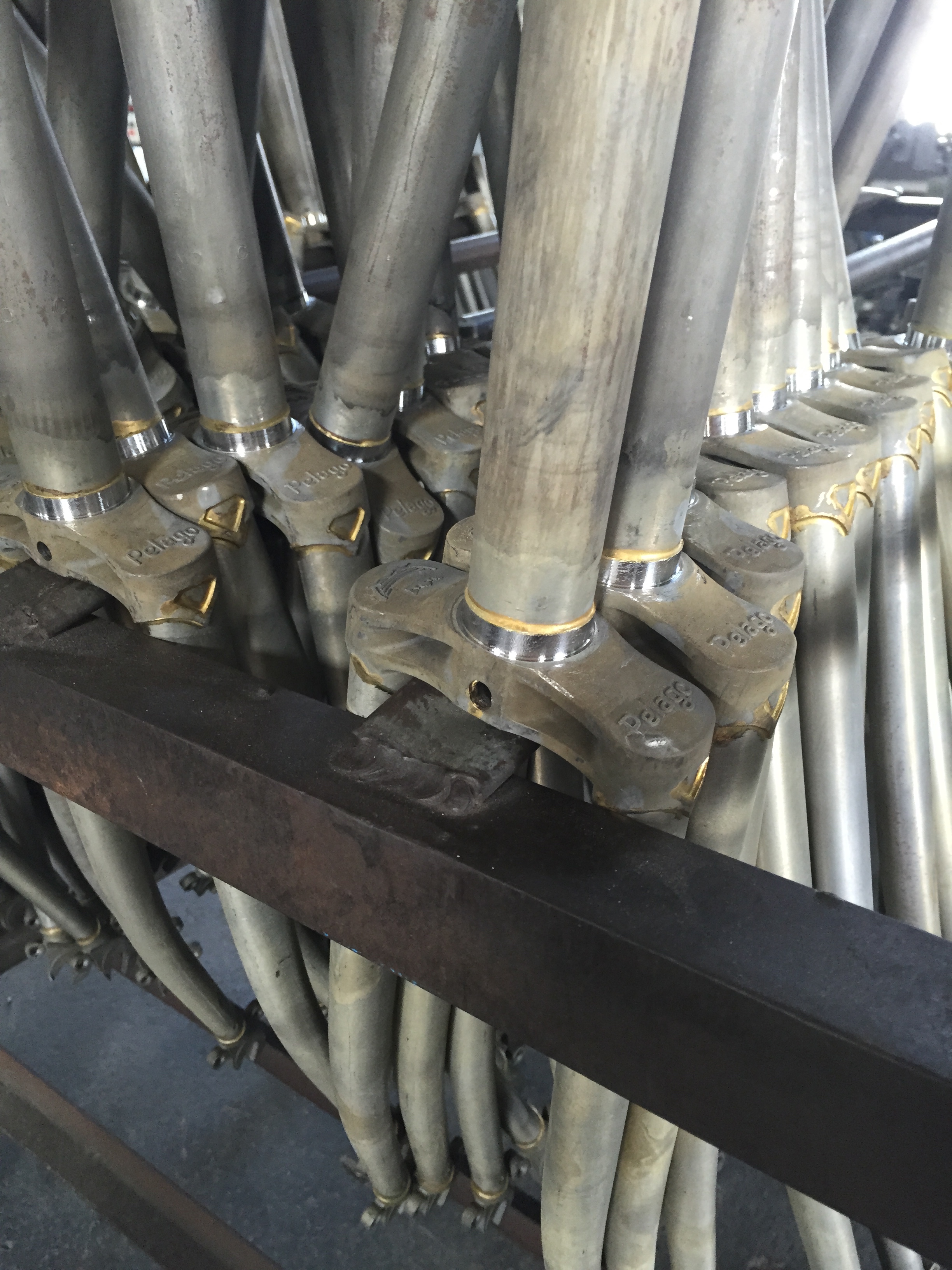
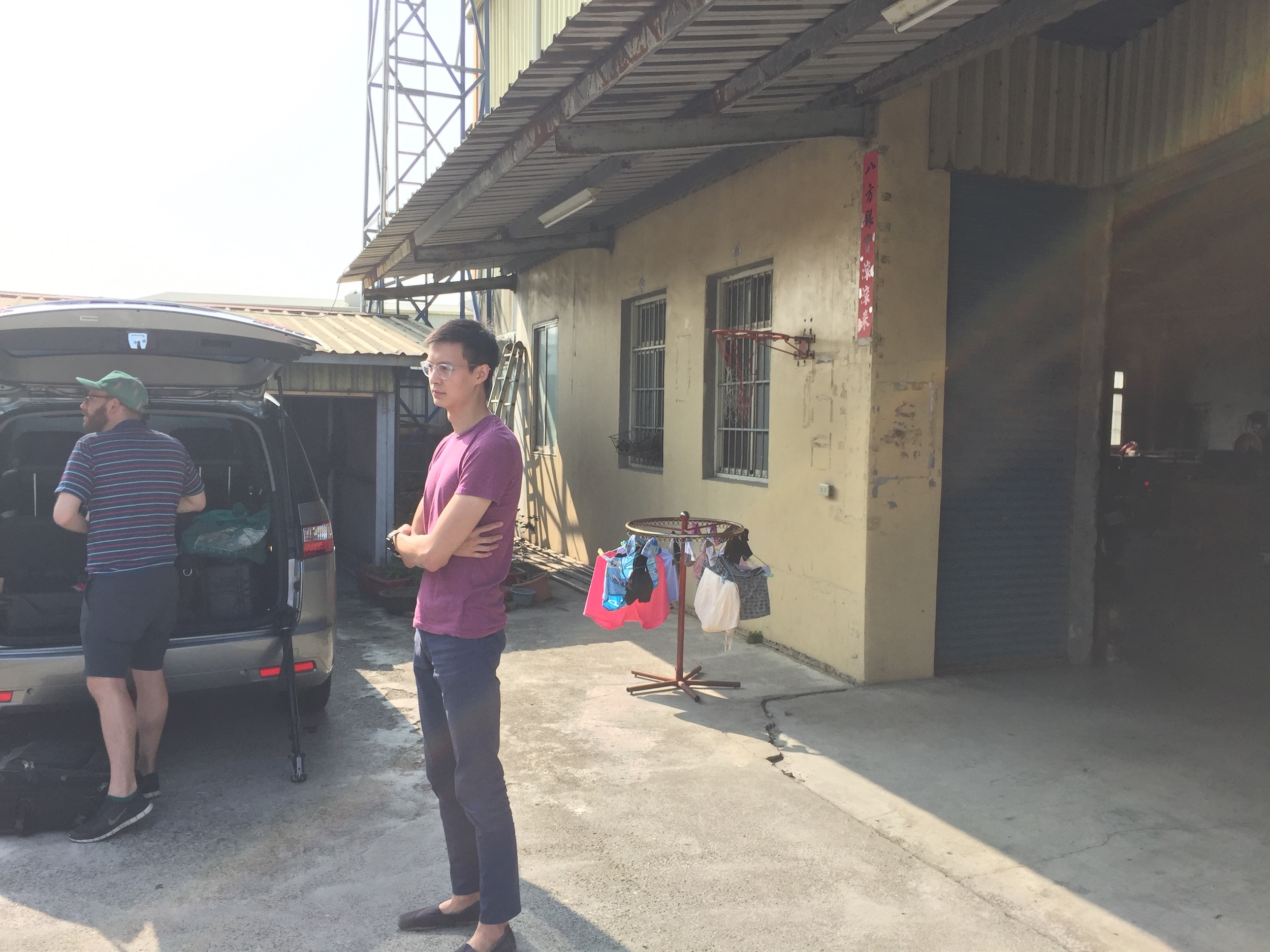
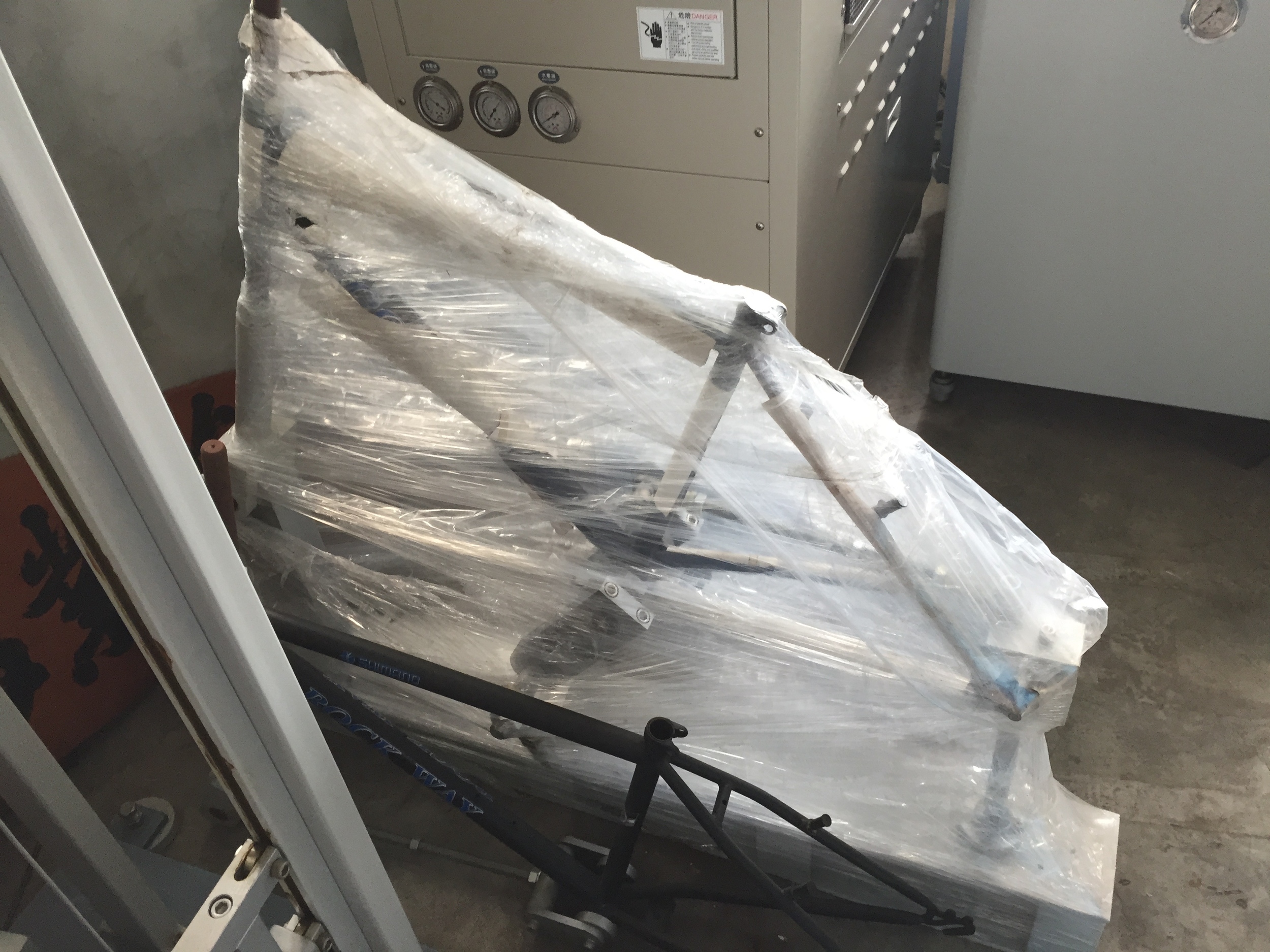
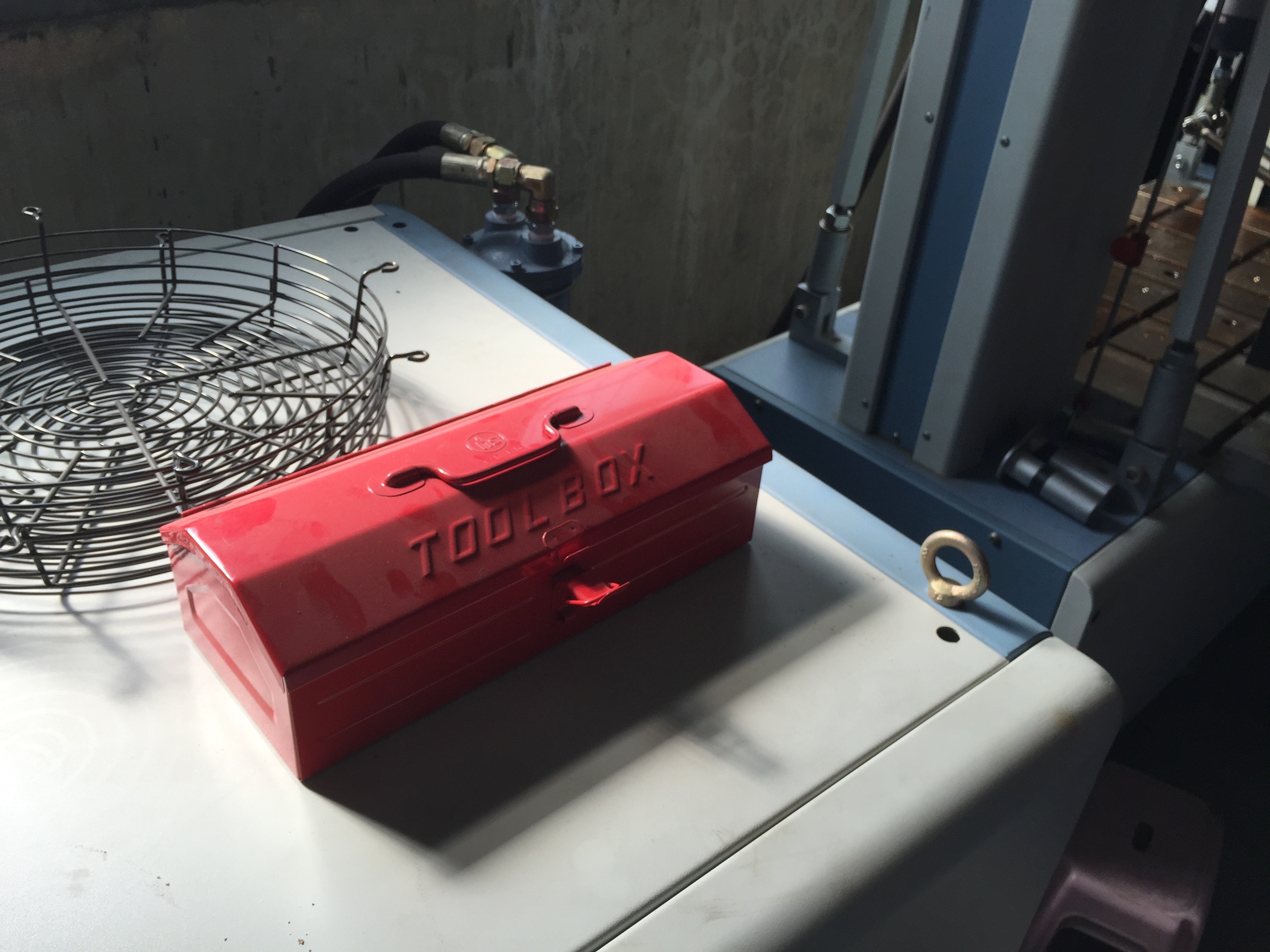
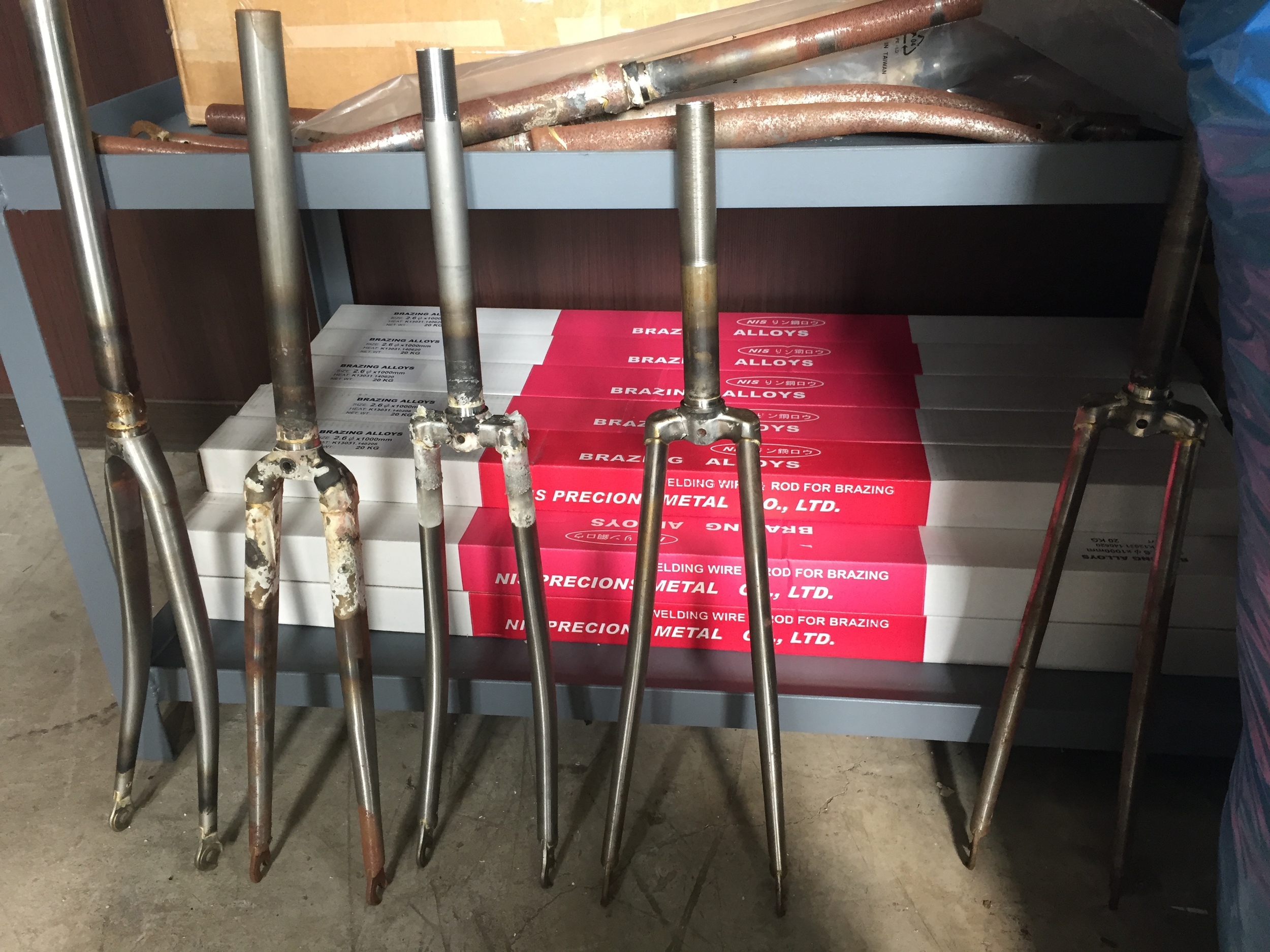
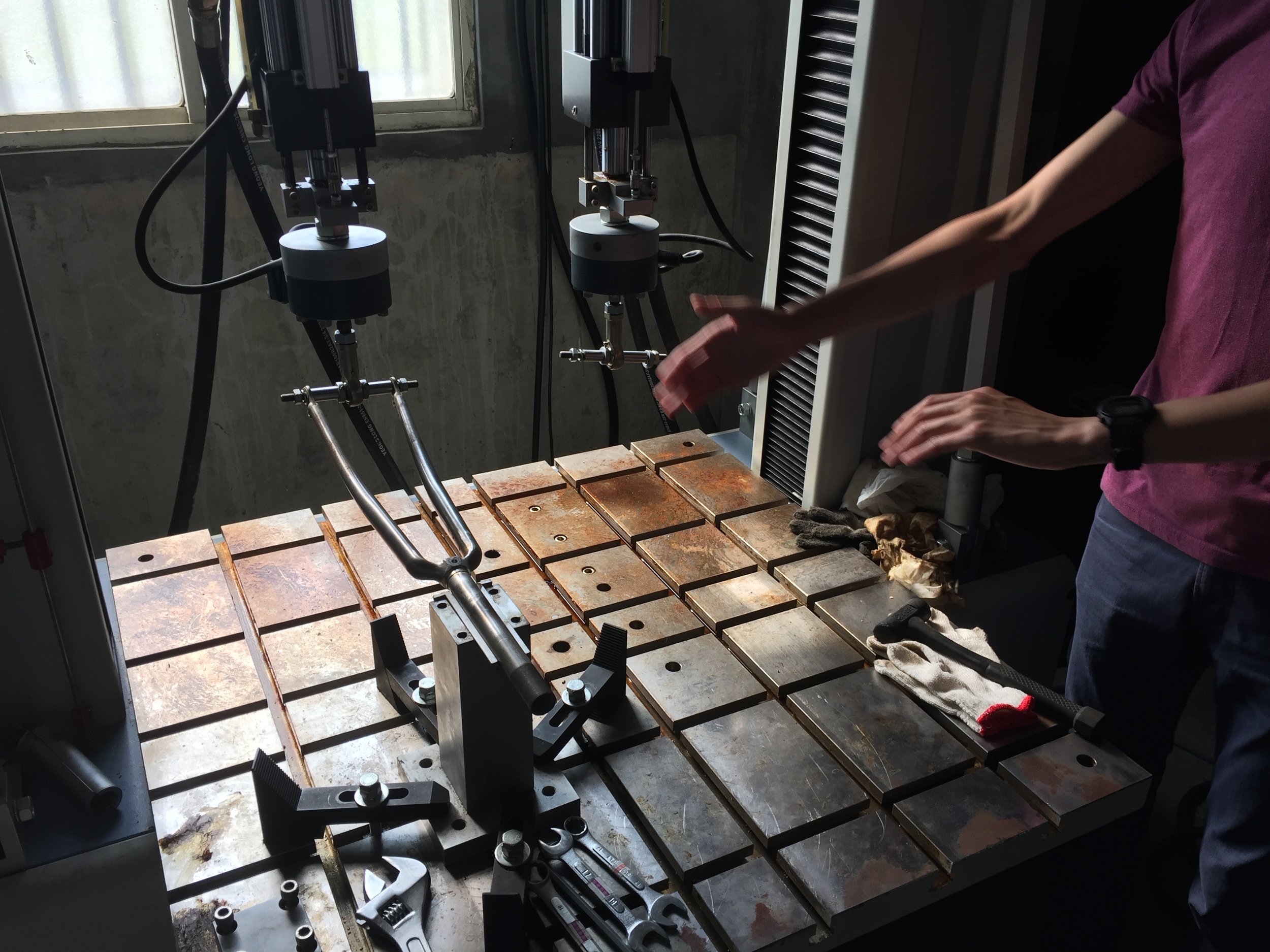
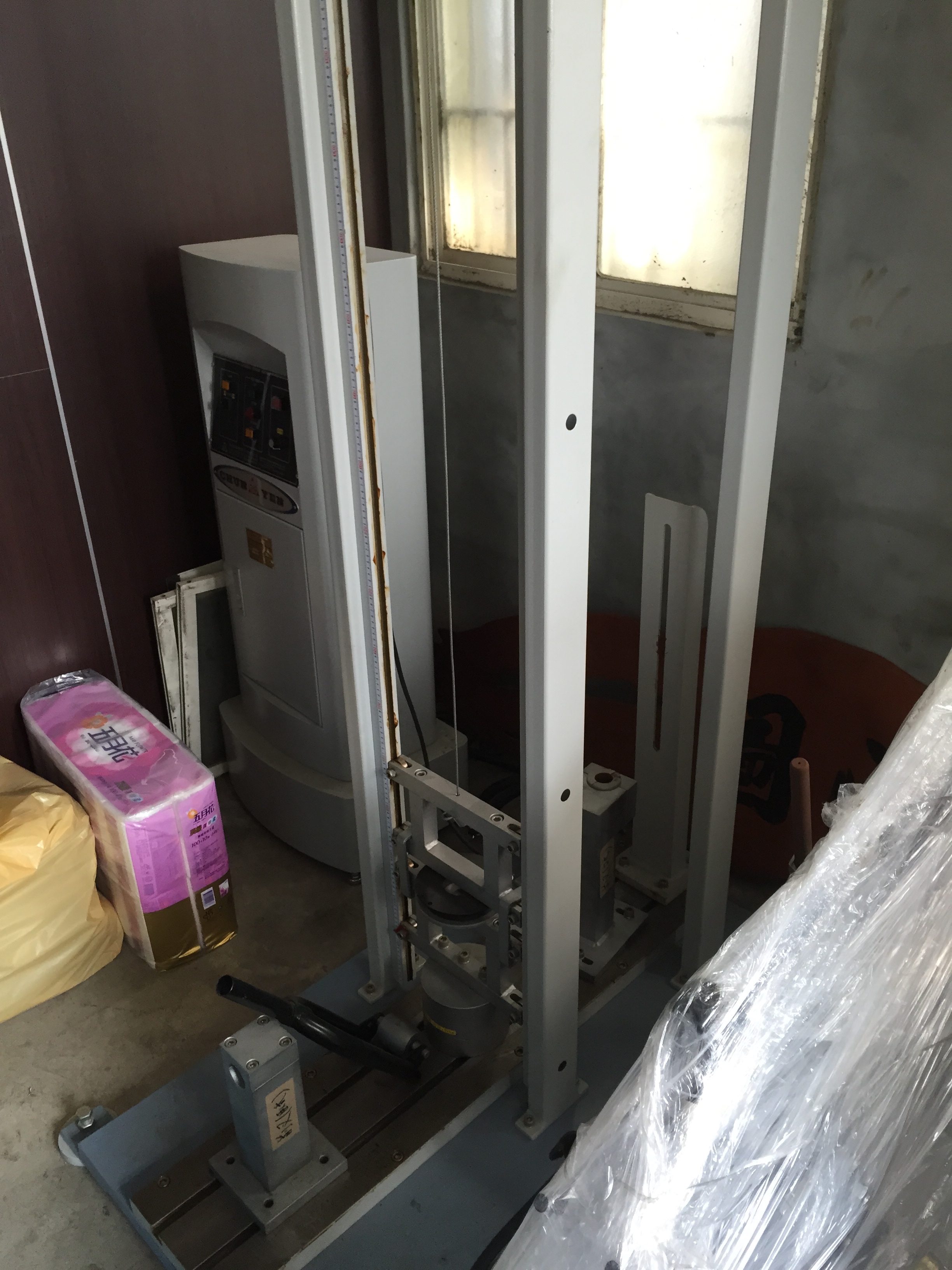
The shop manager was enthusiastic about showing his brazing skills. I was surprised that they brazed them before bending, but the process actually makes a ton of sense in their environment.
The fork alignment process was *awesome.*
Here's a pan of the whole shop:
I liked this shop a *lot.* As we were leaving, the owner commiserated with April that though he had worked there his whole life, he didn't think his children would want to do the same. Building bike forks isn't the dirtiest job in the world, but it isn't the cleanest either. Furthermore, these are good quality but relatively inexpensive steel forks; the product is essentially a commodity, and it isn't exactly prestigious work. I wondered aloud if they could make more money, and have slightly nicer working conditions, if they moved to carbon fiber products. The problem with that is that although the product is a substitute, the skills and equipment needed are quite different. In the end, it might be more fruitful and no less difficult for the next generation to change industries altogether. But anyway the owner was relatively young himself, so it could be decades before it changes at all.